- FMA
- The Fabricator
- FABTECH
- Canadian Metalworking
Categories
- Additive Manufacturing
- Aluminum Welding
- Arc Welding
- Assembly and Joining
- Automation and Robotics
- Bending and Forming
- Consumables
- Cutting and Weld Prep
- Electric Vehicles
- En Español
- Finishing
- Hydroforming
- Laser Cutting
- Laser Welding
- Machining
- Manufacturing Software
- Materials Handling
- Metals/Materials
- Oxyfuel Cutting
- Plasma Cutting
- Power Tools
- Punching and Other Holemaking
- Roll Forming
- Safety
- Sawing
- Shearing
- Shop Management
- Testing and Measuring
- Tube and Pipe Fabrication
- Tube and Pipe Production
- Waterjet Cutting
Industry Directory
Webcasts
Podcasts
FAB 40
Advertise
Subscribe
Account Login
Search
Robotic blast machine automates processing trayloads of components
- May 17, 2010
- Product Release
- Finishing
Guyson Corp. has introduced a robotic blasting system that incorporates a component-manipulating, six-axis robot and a shuttle transfer cart to fully automate processing of trayloads of components.
The model RB-TRR-900 is designed for precise surface preparation, shot peening, and cosmetic finishing operations. The robotic blast machine is provided with a single suction-blast gun or pressure-blast nozzle that is rigidly bracketed in a fixed position inside the 42- by 42- by 42-in. blast chamber.
Guide rails form a track extension into an antechamber on one side of the blast cabinet. Rolling on the track, the transfer cart bearing a tray full of components is moved in and out of the blast enclosure by a precision linear actuator, and a pneumatically actuated vertical sliding door closes to isolate the load/unload station from the blasting zone.
A FANUC M-10iA robot with a pneumatic gripper serves as a component handler in the automated blasting system, grasping and removing a part from the tray, presenting the component to the blast, then replacing the finished workpiece. A tailored skirt seals the cabinet wall and protects the robot from the potentially abrasive environment of the blast chamber.
To blast a production lot of parts, a tray of 6 to 24 oriented components is placed on the transfer cart, the sliding load door is closed, and a part identification number is entered or selected at the touchscreen control panel. Alternatively, component recognition features are available, including a bar code reader, to positively identify the work and prompt the recall of the correct motion program and blasting process recipe, with automatically controlled parameters such as blast pressure, media flow rate, and the duration of the blast and blowoff cycles.
subscribe now
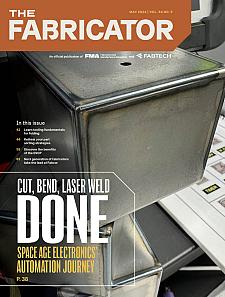
The Fabricator is North America's leading magazine for the metal forming and fabricating industry. The magazine delivers the news, technical articles, and case histories that enable fabricators to do their jobs more efficiently. The Fabricator has served the industry since 1970.
start your free subscription- Stay connected from anywhere
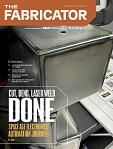
Easily access valuable industry resources now with full access to the digital edition of The Fabricator.
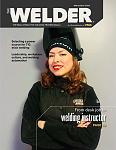
Easily access valuable industry resources now with full access to the digital edition of The Welder.
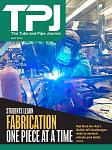
Easily access valuable industry resources now with full access to the digital edition of The Tube and Pipe Journal.
- Podcasting
- Podcast:
- The Fabricator Podcast
- Published:
- 04/16/2024
- Running Time:
- 63:29
In this episode of The Fabricator Podcast, Caleb Chamberlain, co-founder and CEO of OSH Cut, discusses his company’s...
- Trending Articles
Capturing, recording equipment inspection data for FMEA
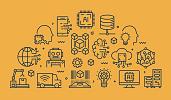
Tips for creating sheet metal tubes with perforations
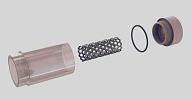
Are two heads better than one in fiber laser cutting?
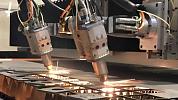
Supporting the metal fabricating industry through FMA
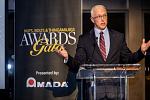
Omco Solar opens second Alabama manufacturing facility
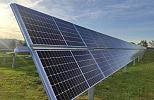
- Industry Events
16th Annual Safety Conference
- April 30 - May 1, 2024
- Elgin,
Pipe and Tube Conference
- May 21 - 22, 2024
- Omaha, NE
World-Class Roll Forming Workshop
- June 5 - 6, 2024
- Louisville, KY
Advanced Laser Application Workshop
- June 25 - 27, 2024
- Novi, MI