- FMA
- The Fabricator
- FABTECH
- Canadian Metalworking
Categories
- Additive Manufacturing
- Aluminum Welding
- Arc Welding
- Assembly and Joining
- Automation and Robotics
- Bending and Forming
- Consumables
- Cutting and Weld Prep
- Electric Vehicles
- En Español
- Finishing
- Hydroforming
- Laser Cutting
- Laser Welding
- Machining
- Manufacturing Software
- Materials Handling
- Metals/Materials
- Oxyfuel Cutting
- Plasma Cutting
- Power Tools
- Punching and Other Holemaking
- Roll Forming
- Safety
- Sawing
- Shearing
- Shop Management
- Testing and Measuring
- Tube and Pipe Fabrication
- Tube and Pipe Production
- Waterjet Cutting
Industry Directory
Webcasts
Podcasts
FAB 40
Advertise
Subscribe
Account Login
Search
EBE Reduced Raw Material and Tightened the Production Belt for Fat-zapping Device
Losing Waste for Smaller Waists
- By Sue Roberts
- May 14, 2015
- Article
- Aluminum Welding
The problem was simple. Too many people prefer relaxing while a medical device cools away fat from their waistlines and curvaceous love handles to passing on ice cream and sweating in the gym. A noninvasive CoolSculpting® process administered by an innovative medical device from ZELTIQ® Aesthetics Inc. uses cold to selectively affect and eliminate fat cells. New, svelte shapes result from fewer—rather than smaller—offending cells. Treated areas simply do not have as many to plump up the profile. The device freezes and kills the affected cells. Then, over time, the body naturally flushes out the dead cells.
The preference for freezing away fat left cosmetic and medical spas clamoring for the equipment. When manufacturing couldn’t keep up with the orders, ZELTIQ approached Electron Beam Engineering Inc. (EBE), in Anaheim, Calif., with the problem.
Welding and More
Specializing in precision electron beam and laser welding services, EBE’s reputation for working with complex components for the aerospace, automotive, defense, electronic, and medical equipment industries made it a good choice to produce the thermoelectric cooling exchangers at the heart of the fat-eliminating equipment. Processes and certifications for quality management, including AS9100C, ISO 9001:2008, and ISO 13485:2003, were already in place. The full machine shop had the equipment and expertise to machine and weld components with tight tolerances.
EBE was also experienced in offering design assistance to simplify complex parts.
Richard Trillwood, CEO, company founder, and designer of electron beam welding machines, and Grant Trillwood, his son and EBE general manager, embraced the challenge.
“The company that was producing this job was unable to keep up with orders because their reject rate was too high,” said Grant. “We produced a small batch of the devices with the old design and it quickly became apparent why production was a struggle. At that point we met with the customer to discuss design changes.”
That troublesome batch of less than 400 pieces produced in 2011 paved the way for the re-engineered design. Since then EBE changes have been implemented, production is running smoothly, and upwards of 3,000 exchangers have been installed in CoolSculpting equipment. The reject rate has dropped to less than 0.5 percent.
“Our aim was not just to weld the parts together, but to re-engineer them and make recommendations to enable a more producible product,” said Richard.
Keeping Cool
The technology behind the procedure is prolonged, controlled cooling applied to the area targeted for reduction. A thermoelectric solid-state heat exchanger, a Peltier cooler, is housed in an enclosure with a curved profile to fit against a human body—typically the waistline. Coolant runs through a labyrinth of grooves within the 6-in. by 3-in. by 0.4-in. exchanger to remove heat absorbed by the heatsink. This allows the cold side of the device, which is in contact with the patient’s skin, to remain cold.
Richard explained, “When you cool something, you have to take the heat somewhere. The pump removes the heat to maintain the electrical heat exchange. When an electrical current is applied to the component, it cools one side and heats the other.”
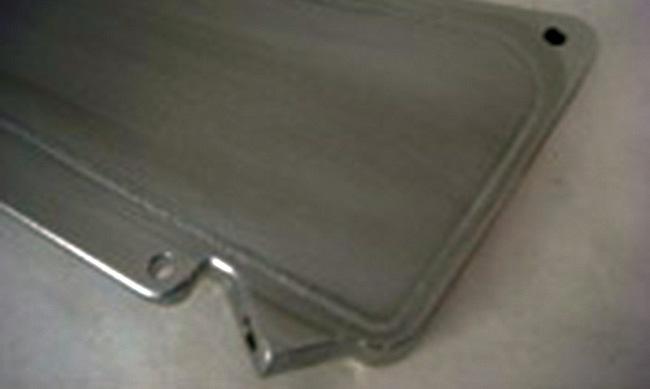
Electron beam welding generates at least 10 times less heat than other welding processes. The lower heat reduces distortion on thin materials.
After EBE welded a small batch of the exchangers according to the initial design, it became apparent that both the dimensions and the design itself were adding to production difficulties. The specifications called for machining compound angular inlet and outlet ports for the coolant, which removes heat from the hot side of the heat exchanger. This necessitated the use of ¾-in. aluminum. The production process was time-consuming, and the high level of complexity in a small part made it difficult to complete within tolerance.
“We made the part thinner,” said Richard. “We got rid of the machined ports and used commercially available quick disconnects. This reduced the amount of machining required, as well as the thickness of the component. We reduced the raw material, 5052 aluminum, from ¾-in. to ½-in. thickness, material that is much easier to find. The change also meant that there was less scrap. So the raw material investment was reduced.”
The second component that benefited from a simplified design was the exchanger cover that is produced from 0.100-in.-thick 5052 aluminum. Each unit requires about 15 in. of electron beam welding.
“Imagine an unusually shaped box that needs a lid,” said Grant. “We talked with the customer about simplifying the external shape of the cover, and that immediately brought the reject rate down. We modified the shape to include more straight lines and gentle radii on the corners.”
An electron beam welding machine, a 318 Beamer manufactured by EBE, is CNC-programmed to follow the housing’s weld profile and automatically control the weld parameters. Narrow, pressure-tight welds are quickly completed and do not require postweld finishing to achieve the 63 RMS finish. The speed of the process added to production time savings.
Grant said that electron beam welding, typically three to six times faster than other welding processes, was the choice for this application because it works well for materials like the 5052 aluminum with high reflectivity and high thermal conductivity.
“The welding could have been done with GMAW [gas metal arc welding],” added Richard, “but the cover is a very thin piece of metal and all of the welding takes place on one side of the part. If we had used conventional welding, it would have gone banana-shaped. By using electron beam welding, the amount of distortion is minimal because it generates at least 10 times less heat than the other processes. The exchanger surface where the heat generation parts are attached has to be flat to 0.001 in.”
Before being shipped to ZELTIQ for assembly in the CoolSculpting units, the exchangers are pressure-tested to ensure that there are no leaks; a final skim cut is made on one surface to keep them within the tight flatness tolerance; and a part number is laser-etched onto the surface. An application of chem-film for corrosion resistance is the final step and the only process that is not completed at EBE.
Slimming Results
Overall, the re-engineering reduced the amount of material needed by about 15 percent, simplified production for a 20 percent time savings, and upped quality for an acceptance rate of over 99 percent. Rejects that led to delayed equipment shipments have all but disappeared.
“The moral of the story,” said Grant, “is that if a designer meets with us before he puts pen to paper, he can save himself a lot of time. In this case, we also saved material. The lid could have been simpler from the get-go, but somebody got carried away on his CAD/CAM program.”
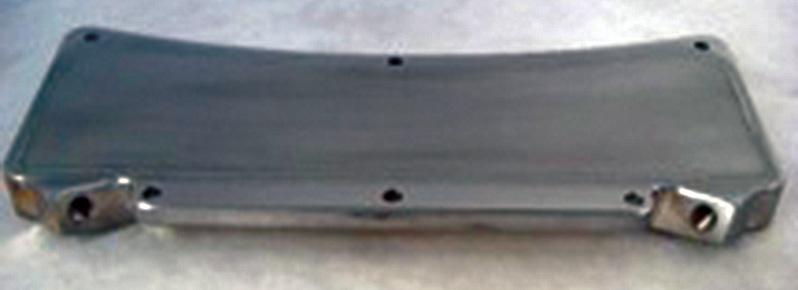
Redesigning the inlet and outlet ports of the heat exchanger, in the angled corners at the front of the 6-in. by 3-in. by 0.4-in. heat exchanger, reduced the complexity and the thickness of the part, saving material and machining time.
Richard said, “The joke in the industry is that if somebody can draw it, surely somebody can build it. We’re problem-solvers, so we don’t turn things away because they look different, are difficult, or perhaps not designed just right, but had the design not changed for this job, we wouldn’t have been able to keep up with demand, and we would have had the extra cost of the rejects.”
Images courtesy of Electron Beam Engineering.
About the Author
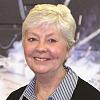
subscribe now
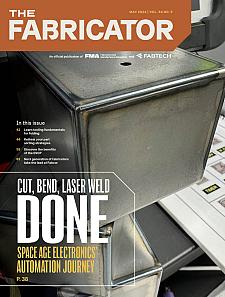
The Fabricator is North America's leading magazine for the metal forming and fabricating industry. The magazine delivers the news, technical articles, and case histories that enable fabricators to do their jobs more efficiently. The Fabricator has served the industry since 1970.
start your free subscription- Stay connected from anywhere
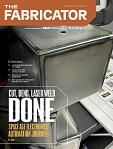
Easily access valuable industry resources now with full access to the digital edition of The Fabricator.
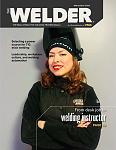
Easily access valuable industry resources now with full access to the digital edition of The Welder.
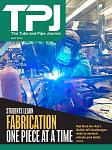
Easily access valuable industry resources now with full access to the digital edition of The Tube and Pipe Journal.
- Podcasting
- Podcast:
- The Fabricator Podcast
- Published:
- 04/16/2024
- Running Time:
- 63:29
In this episode of The Fabricator Podcast, Caleb Chamberlain, co-founder and CEO of OSH Cut, discusses his company’s...
- Trending Articles
Tips for creating sheet metal tubes with perforations
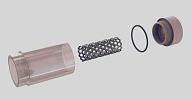
Are two heads better than one in fiber laser cutting?
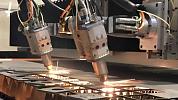
Supporting the metal fabricating industry through FMA
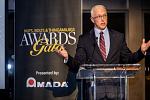
JM Steel triples capacity for solar energy projects at Pennsylvania facility
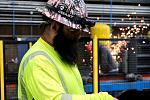
Omco Solar opens second Alabama manufacturing facility
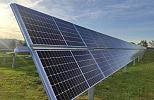
- Industry Events
16th Annual Safety Conference
- April 30 - May 1, 2024
- Elgin,
Pipe and Tube Conference
- May 21 - 22, 2024
- Omaha, NE
World-Class Roll Forming Workshop
- June 5 - 6, 2024
- Louisville, KY
Advanced Laser Application Workshop
- June 25 - 27, 2024
- Novi, MI