Editor-in-Chief
- FMA
- The Fabricator
- FABTECH
- Canadian Metalworking
Categories
- Additive Manufacturing
- Aluminum Welding
- Arc Welding
- Assembly and Joining
- Automation and Robotics
- Bending and Forming
- Consumables
- Cutting and Weld Prep
- Electric Vehicles
- En Español
- Finishing
- Hydroforming
- Laser Cutting
- Laser Welding
- Machining
- Manufacturing Software
- Materials Handling
- Metals/Materials
- Oxyfuel Cutting
- Plasma Cutting
- Power Tools
- Punching and Other Holemaking
- Roll Forming
- Safety
- Sawing
- Shearing
- Shop Management
- Testing and Measuring
- Tube and Pipe Fabrication
- Tube and Pipe Production
- Waterjet Cutting
Industry Directory
Webcasts
Podcasts
FAB 40
Advertise
Subscribe
Account Login
Search
5-step approach to formalizing a feeder system for welding talent
Johnstown, Pa.-based JWF Industries focuses on quality when hiring interns, apprentices
- By Dan Davis
- November 10, 2023
- Article
- Arc Welding
Better vetting of interns and apprentices helps JWF Industries of Johnstown, Pa., find the right welders or machinists for their openings. Todd Berkey/Tribune-Democrat
In 2017, William Polacek, president/CEO of JWF Industries in Johnstown, Pa., saw opportunity—like so many other metal fabricators at the time—and set forth to grow the company. To do that, the company needed welders, so it ramped up the recruitment efforts.
At the time, Polacek stated that he wanted the diversified metal fabricating company (today with locations in four states and with 480 employees) to generate $200 million in annual sales, basically growing the company by 100%. To keep up with all the work, JWF could lean on its in-house welding training program, which had already been around for a couple of years. However, it still needed interested parties to join the cause.
In the ensuing months, business did grow, and more welders were recruited into the fold. But it wasn’t easy. That led to Polacek having what he described as an “epiphany.”
“I was getting beat up every day no matter what was done, and a few of the customers were trying to knock our price down. Then I had some employees who were less than desirable,” he said. “Well, my epiphany was that I had these customers that I really don’t want to do business with and I had employees that I really don’t want to keep employed. So I changed our mission.”
Gone was the focus on a dollar amount. The JWF management team replaced it with a mission to grow with the “right people, right processes, right markets, and right customers,” according to Polacek.
The shift in mission has resulted in JWF focusing on customers with which it can grow profitably. With that growth, the company also has taken on more complex work that has moved it beyond simple fabrications, which almost any other shop can bid on and win. For instance, JWF is building a military vehicle from the ground up. Polacek said that it’s fabricating a very complex frame and a lot of the vehicle’s components, and handling final assembly as well. That type of engineering and turnkey production is hard for other competitors to match.
The Constant Need for Welders
As JWF refocused on its new mission, it also embarked on an effort to make the company a more attractive place to work for area young people entering the job market. Johnstown, Pa., is a town of around 60,000 people, and numerous manufacturing companies are located in the metro Johnstown area. To stand out and capture the attention of those students not necessarily interested in heading to a traditional four-year college, JWF wanted to become “the employer of choice,” Polacek said.
“The best way for us to get employees is through our employees. If they tell you that it’s a great place to work, people are going to come,” he added. (It should be noted that Central Penn Business Journal and Lehigh Valley Business named JWF one of the winners in the “Best Places to Work in PA” competition. “This is a very difficult award to win as a manufacturer,” Polacek said.)
Getting that type of positive promotion from even new employees, particularly welders, which JWF needed, required rethinking who the company welcomed into the fold. Opening the doors to anyone who said they might be interested in welding only led to inconsistent results. Some stuck it out, but others didn’t last long, with one even walking out during lunch on his first day of work.
JWF had to rethink how it reached out to the area’s young population and simultaneously promote manufacturing and the company as a place to explore these interesting career paths. It also needed to rework how its apprenticeship program was set up, making it more flexible for people with differing career interests.
A beginning welder learns the basics of gas tungsten arc welding under the guidance of an instructor at JWF Industries, Johnstown, Pa. JWF Industries
Step 1: Hire the Right Person for the Job
Polacek hired Ed Bowser to be the company’s workforce development coordinator in 2019. Bowser had a great resume for the job, being a former superintendent of the Forest Hills School District, which serves Johnstown and the surrounding Cambria County communities, and a former teacher at a vocational school. He also had a game plan.
Bowser had connections in the education community, and he started to follow up with them. He joined the board of nearby Pennsylvania Highlands Community College, which has satellite locations serving the entire county. He visited other area schools, community colleges, and vocational schools to find out what the instructors were teaching and what students expected in future employers.
“He was able to connect the dots so that a kid can come to work at JWF, and we’ll put him in our co-op program, then follow that up with the apprenticeship program, and then give him $5,250 a year to further the education,” Polacek said.
Step 2: Add Flexibility to the Apprenticeship Program
“When I first started, we looked at what we had, and they were great programs,” Bowser said. “We just needed to modify them a bit.”
The welding apprenticeship program at JWF was a four-year commitment before 2019. The ultimate—and really only—goal was for the individual to complete the studies and training and earn a journeyman’s certificate from the state of Pennsylvania and the U.S. Department of Labor. (JWF has a similar program for those interested in learning to be a machinist.)
Bowser recognized that didn’t leave room for those folks that didn’t have the desire or the time to plow through all of the work on the way to achieving the rank of journeyman and all of the financial benefits that come with that skill level. A tiered system would offer individuals different options to gain skills and also incremental financial increases.
The redesigned apprenticeship program was broken down into three levels:
- A production welder involves 2,000 on-the-job hours and training that would lead to certifications in flux-cored arc welding (FCAW) for steel or gas metal arc welding (GMAW) for aluminum in the 1G position and in material thicknesses from 1/8 in. and up. (As with this level and the other levels, online training accompanies the hands-on work and progression tests. Penn Foster is subcontracted by JWF Industries to provide the apprenticeship modules and a majority of the academic requirement components of the apprenticeship program.) To pass this level, a welder needs to be able to read a drawing, understand the weld specification, set up the welding power source, and produce a weld that meets the job’s specifications.
- A fabrication welder involves 4,000 on-the-job hours and leads to certifications in FCAW in the 3G position in material thicknesses of 1/8 in. and larger; GMAW in 3G in material thicknesses of 1/8 to ¾ in.; gas tungsten arc welding (GTAW) in 3G for steel, aluminum, and stainless steel; and aluminum welding. Before a welder can move on to the next level, he must be able to produce a proper fit-up and weld to critical-to-quality requirements set forth by the welding procedure specification. He also must be able to inspect his own welds. Additionally, the welder must enroll and complete a course called “Critical Thinking” at Pennsylvania Highlands Community College.
- A lead welder requires another 1,000 on-the-job hours and completion of leadership, development, and mentoring classes. The individual also needs to enroll at Pennsylvania Highlands Community College and complete courses on CAD, supply chain management, and emotional intelligence (the ability to perceive, evaluate, express, and control emotions) and take one business elective. Completion of this level leads to certifications in FCAW, GMAW, and GTAW in the 6G position for steel, aluminum, and stainless steel and other certifications as required. The practical test that shows mastery of skills at this level calls for the welder to take an object, create a model for it, produce the print, develop the bill of material for the project, and then create a replica of the object.
With the completion of each of their modules, the apprentices receive a $1.06 per hour raise. This incentivizes them to complete their studies and continue work to improve their welding skills, Bowser said.
“What [Ed Bowser] did was talk to the guys and made them part of the solution,” Polacek said. “Before, they had to go through this over four years. Now, they can go for a year, two years, or four years, whatever they want to do. That got more people enrolled in the program.”
For those that don’t want to go the apprentice route, they can continue to learn how to weld at JWF and work with a mentor until they are skilled enough to work on their own.
A more advanced welding student works on creating a fabrication from a print and work procedure instructions. JWF Industries
“I would say that 100% of them go into the training for the production-level welder because they can see within a year that they can go from $18 per hour to $22.27 per hour, plus quarterly profit-sharing,” Bowser said. “It doesn’t take a lot for a young person to go in and say, ‘Hey! You know what? I can do this. It’s not a lot of work. They’re going to support me. They’re going to pay me to do this.’”
Just as individuals can take their time in the apprenticeship program, apprentice welders also can be aggressive in tackling their studies and passing their tests. Polacek estimated that apprentices could theoretically complete the apprenticeship in two years.
“So you could go from entry-level welder at $18 an hour in two years, and you can make $33 an hour, plus profit-sharing,” Polacek said.
Step 3: Ensure Would-Be Welders Want to Weld
Having someone show up with no welding experience, indicate an interest in the apprenticeship program, start the work, but drop out early on because it turns out that welding is not what they want to do is a drain on an organization’s resources. Time and effort are spent and for little return.
That’s one of the reasons Polacek changed qualifications for who could jump into the welding training program. JWF is now only interested in welders who want to weld.
“If you didn’t at least take this up in high school, we’re not hiring you,” he said. “Or at least go take a 60-hour welding course to show us that you are seriously interested.”
Step 4: Confirm a Possible Pathway
A job is something that’s easy to leave. A career opportunity is something that people are willing to embrace and work hard to make the most of it.
That’s one of the reasons why the welding and machinist apprenticeship program at JWF is now tiered. But it also goes beyond that.
Polacek said that it’s important that employees are informed that they have a growth path at the company should they desire to learn more skills and take on more responsibility. They don’t have to leave for other opportunities because they exist within the JWF organization.
Actually, the first person to progress through the welding apprenticeship program is now a welding instructor at the company. Others have become managers of production areas.
“Most of the time when they go on to become a lead welder, the next step for them is a management role,” Polacek said.
Step 5: Keep Reaching Out to Students
When you are trying to spread the gospel about the upside of a manufacturing career, the job never stops. There’s always a new generation of students, parents, teachers, and administrators to whom to proselytize.
As many in manufacturing can testify, reaching students at a younger age is a good way to hook them on the possibilities associated with embarking on a career right out of high school. If left to their own devices, students with little exposure to the world of manufacturing aren’t likely to plan for a career in that world.
About two years ago, Bowser went to the Indiana County Tech Center (ICTC) to make a presentation and recruit students for co-op slots in JWF’s machining and welding areas (with the hope that those students then join the apprenticeship program), and he was approached by ICTC’s Mike McDermott, administrative director, about possibly creating a welding “pre-apprenticeship” program for juniors. Bowser thought the idea had merit and consulted with JWF’s leadership team, and two years later, the state of Pennsylvania finally gave its blessing to JWF’s new student outreach program. It’s now officially the first U.S. Department of Labor-recognized welding pre-apprenticeship program in western Pennsylvania.
ICTC students can enter the pre-apprenticeship program in the summer after their junior year. If all goes well, they can continue in the program in a co-op role their senior year. Upon graduation and successfully completing the pre-apprenticeship program, which includes classroom learning and paid on-the-job training, the former students are offered full-time employment at JWF and the ability to continue their training in the registered apprenticeship program. Because they have gone through the pre-apprenticeship program, they will be offered advanced placement at the production level of welding. Students who make the transition from the pre-apprenticeship program into full-time employment at JWF receive approximately a $2-per-hour incentive for completing those production-level welding modules and obtaining the two required production-level welding certifications.
“This allows the student the opportunity to participate in a manufacturing setting and understand, ‘OK, this is what it takes to be a welder,’” Bowser said.
By getting to those students coming out of their junior year, Polacek believes the odds are greater that they can pull them into the JWF family.
“The high schools, the teachers, and the students are all starting to buy in to what a manufacturing career can offer,” Polacek said. “But they weren’t the tough part. It was the parents. But even they are starting to see that these kids make $32 an hour and earn $80,000 per year with overtime after four years with no college loans, while other kids finish four years of college and make half of that in their first jobs.”
WHY IT MATTERS
Manufacturers struggle to find the right candidates for their job openings. In the National Association of Manufacturers “2023 Third Quarter Manufacturers’ Outlook Survey,” respondents indicated that the top challenge they face is attracting and retaining a quality workforce (72.1%).
More communities are investing in the vocational training, but will those graduates fit the needs of local manufacturers? That’s why communication channels need to exist between manufacturers and local educators.
Changing the outside world’s perspective on manufacturing means influencing everyone in a community. Back in 2018, a survey sponsored by Kronos Inc. revealed that 58% of parents wanted their child to be knowledgeable about science, technology, engineering, and math (STEM) subjects, but only 20% of parents associated a STEM education with the manufacturing industry. Meanwhile, after being notified about manufacturing’s career opportunities and the availability of jobs, 67% of parents said they would encourage their child to learn more about career opportunities in manufacturing.
Step 6: See the Big Picture
Polacek knows that JWF needs welders, but that’s only one of the reasons he wants to bolster the ranks of manufacturing talent in Cambria County. It’s good for everyone.
Johnstown is like other small cities across the U.S. in that it has lost more residents over the years than gained. Young people go away to college and sometimes stay away in search of big dreams and sometimes big paychecks.
Polacek said that if young people recognize that they can find challenging and rewarding work near their hometowns, they just might stay and perhaps put down roots. That could reverse years of outward migration and build a solid foundation for Johnstown and other nearby communities.
“The way I look at it is from a community aspect. Whether these students work for me or someone else, that’s OK,” Polacek said. “They’re staying here, and we’re building a community.”
The Payoff
The years of outreach to area schools and time spent building a better apprenticeship and training program have paid off for JWF. Polacek said that his company is not only attracting job candidates interested in welding and machining careers, but also painting, assembly, and metal forming. The company also is doing better in retaining those new hires.
This coincides with nearby towns understanding that supporting their neighboring manufacturing companies is an investment in their own communities. One school district is adding another welding instructor to keep up with increased interest in welding classes. Another institution is investing in a new welding training area.
For its next act, JWF is looking to expand its apprenticeship program to groom students for other roles in the company—estimating, modeling, project management, or automation and robotics. These roles don’t require a bachelor’s degree when an associate degree is adequate, but an associate degree in something like engineering is a valuable key when it comes to opening doors that lead to exciting opportunities both inside JWF and maybe outside the company as well. To help develop these programs, the company added Lynn Clement in the role of workforce development coordinator, replacing Bowser who retired last summer.
“There are so many opportunities within a manufacturing organization for a person to get established and then take it to the next level,” Polacek said. “That’s what we want. Those are our next steps.”
About the Author
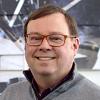
Dan Davis
2135 Point Blvd.
Elgin, IL 60123
815-227-8281
Dan Davis is editor-in-chief of The Fabricator, the industry's most widely circulated metal fabricating magazine, and its sister publications, The Tube & Pipe Journal and The Welder. He has been with the publications since April 2002.
subscribe now
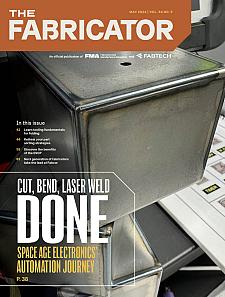
The Fabricator is North America's leading magazine for the metal forming and fabricating industry. The magazine delivers the news, technical articles, and case histories that enable fabricators to do their jobs more efficiently. The Fabricator has served the industry since 1970.
start your free subscription- Stay connected from anywhere
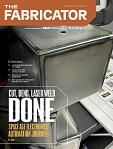
Easily access valuable industry resources now with full access to the digital edition of The Fabricator.
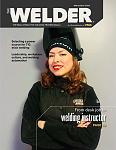
Easily access valuable industry resources now with full access to the digital edition of The Welder.
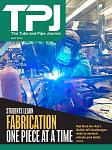
Easily access valuable industry resources now with full access to the digital edition of The Tube and Pipe Journal.
- Podcasting
- Podcast:
- The Fabricator Podcast
- Published:
- 04/16/2024
- Running Time:
- 63:29
In this episode of The Fabricator Podcast, Caleb Chamberlain, co-founder and CEO of OSH Cut, discusses his company’s...
- Trending Articles
Tips for creating sheet metal tubes with perforations
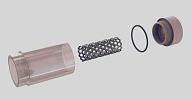
Are two heads better than one in fiber laser cutting?
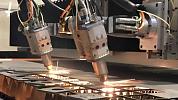
Supporting the metal fabricating industry through FMA
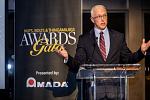
JM Steel triples capacity for solar energy projects at Pennsylvania facility
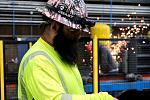
Omco Solar opens second Alabama manufacturing facility
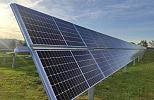
- Industry Events
16th Annual Safety Conference
- April 30 - May 1, 2024
- Elgin,
Pipe and Tube Conference
- May 21 - 22, 2024
- Omaha, NE
World-Class Roll Forming Workshop
- June 5 - 6, 2024
- Louisville, KY
Advanced Laser Application Workshop
- June 25 - 27, 2024
- Novi, MI