Product Manager
- FMA
- The Fabricator
- FABTECH
- Canadian Metalworking
Categories
- Additive Manufacturing
- Aluminum Welding
- Arc Welding
- Assembly and Joining
- Automation and Robotics
- Bending and Forming
- Consumables
- Cutting and Weld Prep
- Electric Vehicles
- En Español
- Finishing
- Hydroforming
- Laser Cutting
- Laser Welding
- Machining
- Manufacturing Software
- Materials Handling
- Metals/Materials
- Oxyfuel Cutting
- Plasma Cutting
- Power Tools
- Punching and Other Holemaking
- Roll Forming
- Safety
- Sawing
- Shearing
- Shop Management
- Testing and Measuring
- Tube and Pipe Fabrication
- Tube and Pipe Production
- Waterjet Cutting
Industry Directory
Webcasts
Podcasts
FAB 40
Advertise
Subscribe
Account Login
Search
Best welding practices start with safety
Safe practices should be the first part of any welder's training
- By Eric Sommers
- February 26, 2024
- Article
- Arc Welding
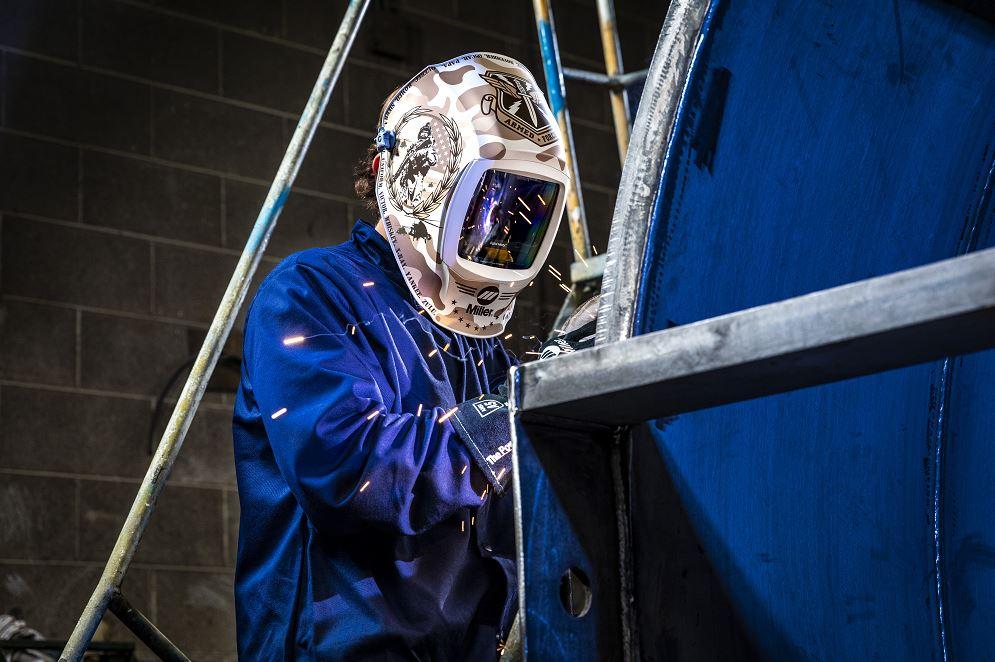
Along with a helmet that offers good visibility, this welder is wearing fire-retardant clothing and gloves that offer full coverage.
Safety is not a one-and-done component to welding—it’s the most important component. Of course, everyone must read and follow all safety precautions on the equipment labels and in the equipment owner’s manual. They aren’t to be taken lightly.
Whether you’re a rookie or a seasoned pro, the importance of safety over your career can’t be understated—and your initial training is a natural, and essential, place to start.
See Clearly
It doesn’t matter if you’re new to welding or an industry veteran, good welding starts with good safety practices. From before you strike the arc through the entire process, you need to be well protected—starting with your eyes and face.
Arc flash is the burning sensation or eye irritation that can occur after even brief exposure to the arc’s radiation. Proper face and eye protection, which includes a welding helmet and safety glasses worn underneath, protects eyes from harmful UV radiation, infrared light, and flying debris. Autodarkening helmets enhance safety by providing the appropriate dark state for the job and eliminating the need to continually flip up your helmet to see between welds.
Dress Safely
Sparks, spatter, and heat make exposed skin vulnerable to burns, so you should never where short sleeves, sandals, and shorts while welding. Flame-resistant pants, long-sleeve shirts, and jackets made from leather or heavy cotton shield skin from direct contact with hot metal or sparks.
High-top leather shoes or steel-toed boots are best for welding. Tennis shoes and other cloth options leave feet susceptible to catching sparks, and left unnoticed, the sparks can smolder and melt through the shoe.
When welding or handling materials, protect your hands against burns, cuts, and electric shock with flame-resistant (and cut-resistant, depending on the application) gloves. Plenty of options not only provide ample protection and comfort but also allow for the dexterity needed to complete welding tasks.
Welding Fume Protection
For certain jobs, various products can ensure your breathing zone is shielded from potentially harmful welding fumes (see Fume Mitigation Strategies sidebar). A half mask typically covers the lower part of the face and uses a filter or cartridge system that purifies the air, removing particles, gases, and vapors.
A powered air-purifying respirator (PAPR) or supplied air respirator (SAR) are more advanced air purification systems. They both consist of a complete facepiece (hood, helmet, or mask) connected to a unit that delivers clean air into the breathing zone. PAPRs are self-contained systems that filter ambient air, whereas SARs deliver clean air from an external source like an air tank.
Starting With Augmented Reality
If you’re just learning the trade today, you might start not with an actual welding gun or torch, but instead with an augmented reality (AR) system. AR has become a beneficial tool in teaching new welders the correct form and techniques, growing their confidence and comfort level before striking an arc.
The blended teaching model simulates multiple welding processes. You wear a special helmet, grasp a training device shaped like a welding gun or torch, and manipulate it against a setup meant to emulate a real welding joint. You won’t strike a real arc, but you’ll see a virtual one through the helmet. Advanced AR training systems simulate gas metal arc welding (GMAW, or MIG), gas tungsten arc welding (GTAW, or TIG), shielded metal arc welding (SMAW, or stick), and fluxed-cored arc welding (FCAW).
With AR, you can get real-time feedback, correct errors, build muscle memory, and safely perfect basic techniques before trying something more advanced. The approach is more forgiving of mistakes, does not waste consumables, and bolsters confidence when the time comes to lay beads on actual workpieces.
FUME MITIGATION STRATEGIES
If you’re supervising or managing a welding operation, you need to understand the airborne contaminants in your welding environment and take the proper steps to ensure a safe and compliant space for operators. Have the air quality in the welding environment assessed by a certified industrial hygienist. Based on those results, you can determine an effective action plan that follows OSHA’s hierarchy of controls for weld fume control:
- Modify the process to reduce airborne contaminants. This can include changing welding operations, using low-manganese consumables, changing to a welding process with less fume generation (for example, shifting from SMAW to GMAW with a solid or metal-cored wire), altering machine parameters, or switching to a specialized shielding gas mix. (You can find more information in the ANSI standards for safety in welding, cutting, and allied processes.)
- Assess engineering controls. If process modifications alone are not feasible or do not reduce exposure levels enough, you might need to physically change the workplace to remove a hazard. This can include implementing process enclosures for robotic welding or ventilation options. Local exhaust ventilation, also referred to as source capture, is the preferred method because of its ability to capture and remove contaminants at their source before they reach a welding operator’s breathing zone. Options include fume extractors, extraction arms, and fume extraction guns.
- Modify work practice controls. Adapt procedures and policies that limit fume exposure. Examples of work practice controls in action are keeping the weld operator’s head out of the weld plume, changing body position so that the airflow moves from back to front, and making sure any air movement in the work area pushes fume away from the breathing zone. Another modification could include removing paint or coating on the base metal before welding to minimize the release of contaminants.
- Require additional PPE. This can include disposable masks, powered air-purifying respirators, or supplied air respirators. Note that whenever a respirator is used on the job, companies must establish and maintain a written respiratory protection program per OSHA.
Good Fundamentals Make Welding Safer
Once you start welding on real workpieces, don’t forget to inspect and clean them. Cleaning the base metal of contaminants will help keep impurities out of the weld.
To set up your equipment properly, you need to establish a great workpiece connection, attaching the clamp as close as possible to the arc so that there’s a proper flow of welding current. Also check the regulators on the gas tanks and set the appropriate gas flow for every job, to ensure the weld has proper gas coverage. To achieve maximum penetration and a good weld, be sure to adjust the voltage and wire feed speed based on the material type, material thickness, and filler metal diameter.
As you start to weld, make sure you have adequate support. The way you hold, move, and position the gun influences not only the quality of the weld but also your chances of incurring work-related injuries. The right techniques will mitigate muscle strain. Whenever possible, use a two-handed grip on the gun and support the hands, wrists, forearms, and elbows in a way that allows the gun to move smoothly while maintaining control.
As part of this, you need to maintain the optimal work angle and travel angle. The work angle relates to the angle of the electrode to the workpiece, while the travel angle relates to whether the operator is pushing the gun in the direction of travel or pulling away from it. How you employ these angles and your overall welding technique comes down to the workpiece, the thickness of the base metal, and the welding position. Without properly taking these variables into account, welds can be too narrow (or wide), distorted, or inconsistent. You might also burn through the material or, conversely, end up with incomplete penetration.
Getting Comfortable With GTAW
GTAW is considered to be one of the more difficult welding processes to learn. If you’re new to GTAW, your trainer should consider having you practice either by tacking small pieces together or creating autogenous welds (without filler metal). Welding autogenously helps familiarize you with controlling heat input, establishing appropriate travel speeds, and reading the weld pool.
As you move away from initial training and settle into day-to-day work with GTAW, safety and good habits should remain top of mind. First, be sure to maintain a proper torch angle. To achieve the best results for most applications, hold the torch at a 70- to 80-degree angle. To avoid contamination, make sure the tungsten never touches the workpiece.
The key to a good gas tungsten arc weld is heat control, and this requires good pedal control. The foot pedal dictates the heat input, so you need to be comfortable with the pedal sensitivity and how resulting pressure and output will impact the weld pool size as it relates to material thickness and amperage.
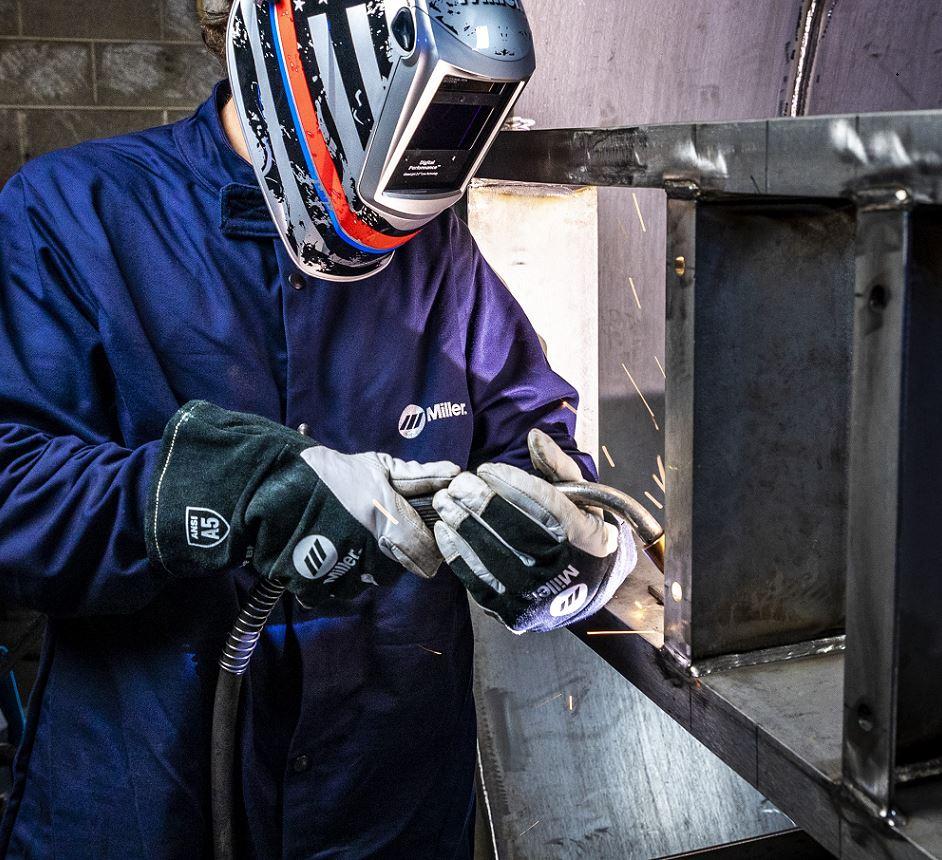
Always look for the best support possible when welding. Supporting the hands and arms provides better control and prevents fatigue.
Also, be sure to have adequate hand and arm support so you can maintain precise control during welding. If you’re in a challenging position, still look for ways to support your hands and arms so you’re as comfortable as possible. Some support is better than no support at all.
Designing a Safe Shop
If possible, organize the workspace into two distinct areas: one for welding and one for cutting and grinding. Cutting and grinding are often dirtier processes than welding, so separating the two is critical for maintaining clean welding conditions. This is especially important when working with aluminum or GTAW, where contaminants can deteriorate weld quality.
Keep flammable materials—including paper, cloth rags, oil, and gasoline—away from welding and welding equipment. Follow the “35-ft. rule” as defined in NFPA 51B, Standard for Fire Prevention During Welding, Cutting, and Other Hot Work.
Keep the work area free of clutter, but make sure any necessary tools are easy to find. Also, double-check that equipment is installed and set up properly. Gas cylinders must be chained securely to a stationary, upright support or cart; only use gas hoses designed for welding. Monitor hoses regularly for leaks, wear, and loose connections. Additionally, store away unused cables and hoses to eliminate trip hazards.
Building a Safe Foundation
Safety means protecting welders under the hood and the environment they’re in, so they can perform their jobs every day without incident. With so many facets, at first pass, best practices for welding safety can seem overwhelming to implement and follow.
That said, when you start with a solid foundation, you’ll find it’s easier to flex that safety muscle for sustained benefits—and major gains.
About the Author
Related Companies
subscribe now
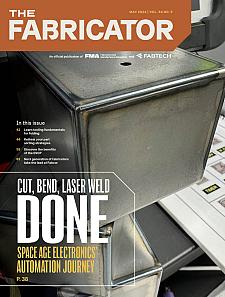
The Fabricator is North America's leading magazine for the metal forming and fabricating industry. The magazine delivers the news, technical articles, and case histories that enable fabricators to do their jobs more efficiently. The Fabricator has served the industry since 1970.
start your free subscription- Stay connected from anywhere
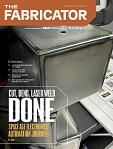
Easily access valuable industry resources now with full access to the digital edition of The Fabricator.
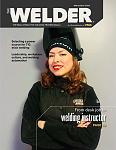
Easily access valuable industry resources now with full access to the digital edition of The Welder.
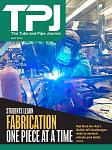
Easily access valuable industry resources now with full access to the digital edition of The Tube and Pipe Journal.
- Podcasting
- Podcast:
- The Fabricator Podcast
- Published:
- 04/16/2024
- Running Time:
- 63:29
In this episode of The Fabricator Podcast, Caleb Chamberlain, co-founder and CEO of OSH Cut, discusses his company’s...
- Trending Articles
Tips for creating sheet metal tubes with perforations
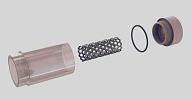
JM Steel triples capacity for solar energy projects at Pennsylvania facility
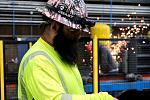
Are two heads better than one in fiber laser cutting?
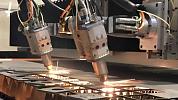
Supporting the metal fabricating industry through FMA
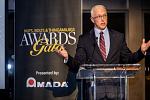
Omco Solar opens second Alabama manufacturing facility
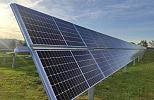
- Industry Events
16th Annual Safety Conference
- April 30 - May 1, 2024
- Elgin,
Pipe and Tube Conference
- May 21 - 22, 2024
- Omaha, NE
World-Class Roll Forming Workshop
- June 5 - 6, 2024
- Louisville, KY
Advanced Laser Application Workshop
- June 25 - 27, 2024
- Novi, MI