Vice President of Sales
- FMA
- The Fabricator
- FABTECH
- Canadian Metalworking
Categories
- Additive Manufacturing
- Aluminum Welding
- Arc Welding
- Assembly and Joining
- Automation and Robotics
- Bending and Forming
- Consumables
- Cutting and Weld Prep
- Electric Vehicles
- En Español
- Finishing
- Hydroforming
- Laser Cutting
- Laser Welding
- Machining
- Manufacturing Software
- Materials Handling
- Metals/Materials
- Oxyfuel Cutting
- Plasma Cutting
- Power Tools
- Punching and Other Holemaking
- Roll Forming
- Safety
- Sawing
- Shearing
- Shop Management
- Testing and Measuring
- Tube and Pipe Fabrication
- Tube and Pipe Production
- Waterjet Cutting
Industry Directory
Webcasts
Podcasts
FAB 40
Advertise
Subscribe
Account Login
Search
Advances in riveting and mechanical fastening
Think riveting hasn’t changed? Think again
- By Bryan Wright
- March 5, 2020
- Article
- Assembly and Joining

An orbital riveting head completes its cycle. Such an application involving mild steel and a peen at a 6-degree angle applies only about 20% of the force impact riveting would require.
When you think of riveting, you might think it’s a mature technology where not much new happens under the sun. You’d be right, but only partly. Yes, riveting is old technology. Place a rivet in a hole, apply pressure to and deform the tenon to create the head, and you create a permanent bond.
Of course, you need the hole to be only slightly larger than the outside diameter of the tenon—that is, the end of the rivet (or wire or ball stud) where the fastening tool makes contact; 6% to 7% is a good rule of thumb. With those basic parameters set, you’re on your way to attaining maximum hole-fill, which is solid, gap-free contact between the rivet and parent materials.
Although you might be on your way, you’re not there yet. That’s because riveting is not an unchanging technology. When you think of the process broadly as just one of many permanent mechanical fastening methods, you’ll find that the innovation abounds. They’re all based on the idea of applying pressure to move material from one form to another, all the while not changing the molecular structure of the material (which sets them apart from other processes like welding).
It could be about forming a solid tenon into a rivet (riveting), a hollow tenon into a flare (flaring), a boss into a hole (staking), or another situation. What works best depends as always on the application, including workpiece thickness, joint strength requirements, part volume, and required flexibility. You have many choices, and each has its pros and cons. But before digging deeper, you first need to know the technology options on the menu, along with the ingredients that can get the best out of each process.
Impact Riveting
The feeding mechanisms, which really define impact riveting, deliver fasteners to the work envelope quickly and in a reliable way. The fastener for the next rivet can be staged and ready within fractions of a second. Take away the feeding mechanism, and you have a conventional riveting press, be it a flywheel press, a pneumatic wedge-head press, an air-over-oil press, or even a hydraulic press. Which press to choose depends on the tonnage it takes to upset a particular fastener in a given workpiece.
With impact riveting, speed is the name of the game. Using a pneumatic or mechanical flywheel press, impact riveting cycle times range from 0.3 to 1 second. Riveting with a hydraulic press might take a little longer. Typical cycles for hydraulic or hydra-pneumatic driven presses are between 1 and 3 seconds, with the tool in place in the work envelope to get maximum “squeeze” and shank swell, cold-forming the tenon to fill the hole diameter.
Impact riveting also helps to meet functional requirements for certain applications, including shear load or torque requirements. A rivet might need to withstand a certain amount of torsional force, and to achieve that, you need to minimize or eliminate gaps in the rivet joint. The high force and direct impact angle behind impact riveting create the shank swell needed to accomplish this.
While impact riveting offers very high speed, it also can require high tonnage, since the rivet is simply being driven straight through the component.
Excessively high tonnage—be it from positioning or other errors—can fault-out and halt the operation. It’s often straightforward to engineer out these issues, but when it’s not, you might want to turn to alternative fastening methods.
Orbital Riveting
Compared to impact riveting, orbital riveting induces considerably less force. The process uses a rotating peen tool offset at a certain angle. Because the rotating peen tool is slightly tilted, it applies the rivet moving in a seemingly wobbly motion—but don’t be deceived. That motion is highly engineered and controlled.
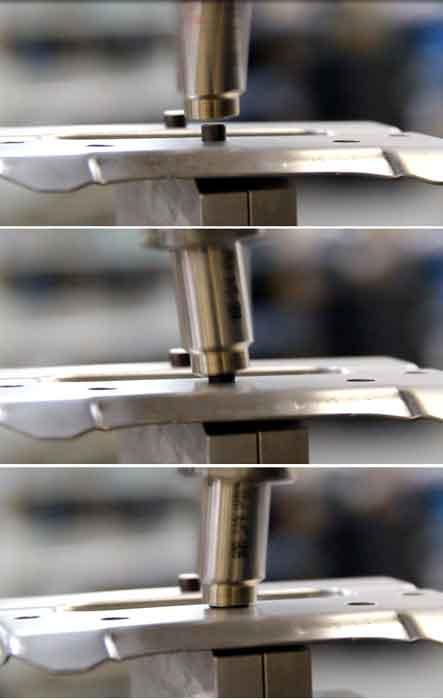
An orbital riveting head applies a sweeping line of pressure 360 degrees around the tenon. The rotation causes the process to move only a percentage of the material per revolution.
The peen tool “massages” or “kneads” the material as the tool advances and forms the head. The rotation causes the process to move only a percentage of the material per revolution. In impact riveting, on the other hand, the entire peen diameter contacts the workpiece and attempts to move it all at once.
An orbital riveting application involving mild steel and a peen at a 6-degree angle applies only about 20% of the force impact riveting would require. Sometimes it’s even less. In impact riveting, a 0.25-in.-diameter solid rivet would normally require an impact press that’s capable of producing 12,000 pounds of force; the same application in an orbital riveting setup might require between only 1,800 and 2,400 lbs. of force.
Orbital riveting is more controllable too. Specifically, you can control the peen tool’s rate of advancement to mitigate work hardening and optimize the overall process. And because orbital riveting uses a lower-capacity machine, it usually requires a lower capital investment and has lower tooling and maintenance costs.
Orbital riveting produces a shank swell concentrated near the top of the rivet body. If you were to cut a cross section, the inserted rivet’s shank body would look like a funnel. When a peen tilted 6 degrees descends toward the work, it forms down as well as out.
Assuming a 6-degree tool angle, orbital riveting produces side load forces that are about 10% of what the downward forming force is. Fixture design is key to ensure the part is secure during the process. Specifically, the fixture design needs to be robust enough to withstand that 10% side load force plus a safety factor.
Orbital riveting does have its downsides, the chief one being cycle time. Most orbital riveting cycle times are between 2 and 4 seconds, much longer than for the fastest impact riveting processes. Also, orbital riveting cannot create the deep shank swell that impact riveting can. If a deep shank swell is an engineering requirement that cannot be changed, impact riveting might be the better choice.
Radial Riveting
Orbital riveting is similar to a process called radial riveting, but there are some key differences, most of which have to do with the toolpath.
In orbital riveting, the peen makes contact at a certain angle of, say, 6 degrees. As the head rotates, the peen tool maintains contact, but due to the orbital head bearing design, the peen massages or kneads the workpiece material, as described previously. (Without the head bearing design, the peen point of contact would make orbital riveting more like a friction weld process.) One revolution of the motor in orbital riveting produces 360 degrees of peen-tool rotation.
The motion in radial riveting, on the other hand, is roughly analogous to the motion you produce using a Spirograph toy, drawing multiple leaflets as you make your way around a circle. It takes radial riveting multiple revolutions of the motor, usually between 11 and 13, to rotate the peen tool 360 degrees. This displaces material from the center outward in a rosette or floret pattern. Spindle rotating speed in radial riveting ranges from 1,140 to 1,780 RPM, where most orbital spindles rotate at 1,140 RPMs.
One big advantage to radial riveting has to do with the forces it exerts—or, more specifically, the lack of certain forces. Radial riveting does not produce side load, so it’s a good option for small-diameter, long-shank rivets or workpieces.
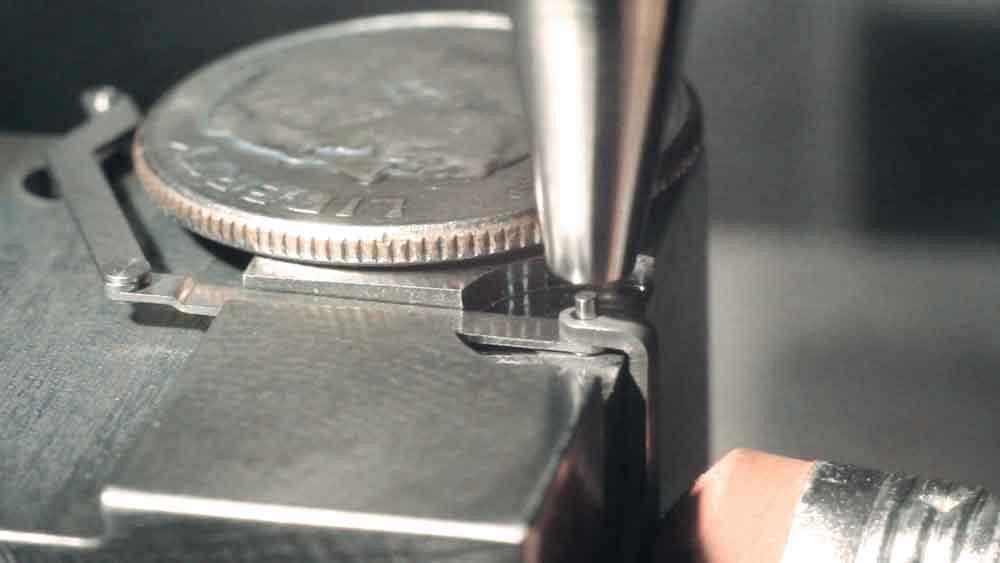
Radial riveting begins its cycle on a tiny workpiece. The process exerts no side loading, which can simplify fixturing.
Orbital Forming
Orbital riveting is part of a broader family of processes called orbital forming, where the peen tool is held at a fixed angle to create a sweeping line of pressure.
This includes orbital staking. In a sheet metal application, the peen tool (which has a different geometry than the one used in orbital riveting) radially expands a boss in one workpiece into a hole of another workpiece, creating an interference fit. It’s similar to a conventional staking operation, but in orbital staking, the peen tool rotates, again applying that sweeping line of pressure 360 degrees around the work area.
Another variation is orbital flaring. Instead of a solid rivet, the process uses a flaring peen-tool geometry that flares semitubular or tubular rivet tenons, which are also used in conventional riveting. But again, instead of a press descending and applying downward force, orbital flaring uses a peen rotating at a fixed angle. The rotating peen descends and applies a precise amount of force to flare the tenon over the parent material.
Hot Upset Forming
Say you’re joining a hard ball stud to a bracket plate, joining a striker wire to a bracket plate, or working with some other material that’s harder than mild steel. When you try to cold-form it, it begins to fracture and crack before achieving your desired finished form.
Here’s where hot upset forming can help. It’s very similar to a projection nut weld or similar resistance welding process. The main difference is that it’s not welding two pieces together. While there is a bond, no fusion occurs.
In hot upset forming, a tool descends and contacts the end of a hardened rivet or tenon. Upon contact, the tool runs current through the rivet and isolates the resistance in a certain area, usually to a point at which the rivet turns cherry red, nearing a molten state. Once the head applies pressure, the resulting heat allows the material to flow down through the joint, maximizing hole-fill, to produce a finished head form.
Heat isolation is key here. The process controller must ensure that it applies significant heat to the tenon, but not the surrounding parent material. The parent material will heat to some degree near the joint interface, but not significantly—otherwise, you risk distorting or even welding the workpieces. If the heat isn’t controlled, neither is the process.
Hot upset forming can also be ideal for applications where the end product is exposed to heavy vibration over long periods. If you expose any joint assembly with even a slight gap to heavy, prolonged vibration, the gap will grow larger over time and eventually weaken the joint. Again, maximizing hole-fill, along with minimal to no material fracture, is the key desired result.
More than other mechanical fastening processes, hot upset forming gives you the greatest opportunity to maximize hole-fill in the joint. You still need to follow basic design guidelines, like a hole diameter being just about 6% to 7% larger than the tenon. But if you’re working with a harder tenon, like one that’s between 28 and 32 Rockwell C, the hot upset process might give you the best chance of filling any gaps between it and the parent material, and minimizing material fracture.
You do need to ensure the tenon has sufficient preform stick-out above the top surface of the sheet metal (or another parent material), as this supports satisfying a minimum retention load in the axial direction of the joint. But once the peen applies electricity to the tenon, the material will flow toward a path of least resistance—including into those gaps. Put another way, the electrical resistance that generates the heat aids formability, while the applied pressure ensures the material flows to the right places.
Move Material Right
The processes discussed here involve fastening flat surfaces like sheet metal, but others involve tubes and a variety of other cylindrical shapes. Regardless, all this is just the tip of the iceberg of permanent mechanical fastening. More options are out there, and the potential for value engineering abounds.
But whatever the exact method, any permanent fastening strategy needs to meet manufacturing throughput demands and a part’s functional and cosmetic requirements. It’s about moving material to the right places and in the right way to make that happen.
Bryan Wright is vice president of sales at Orbitform, 1600 Executive Drive, Jackson, MI 49203, 517-787-9447
About the Author
Related Companies
subscribe now
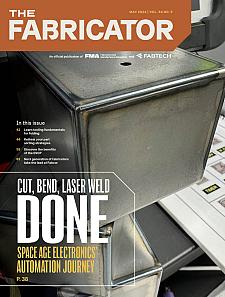
The Fabricator is North America's leading magazine for the metal forming and fabricating industry. The magazine delivers the news, technical articles, and case histories that enable fabricators to do their jobs more efficiently. The Fabricator has served the industry since 1970.
start your free subscription- Stay connected from anywhere
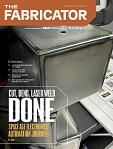
Easily access valuable industry resources now with full access to the digital edition of The Fabricator.
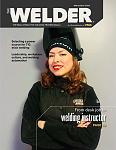
Easily access valuable industry resources now with full access to the digital edition of The Welder.
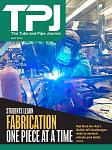
Easily access valuable industry resources now with full access to the digital edition of The Tube and Pipe Journal.
- Podcasting
- Podcast:
- The Fabricator Podcast
- Published:
- 04/16/2024
- Running Time:
- 63:29
In this episode of The Fabricator Podcast, Caleb Chamberlain, co-founder and CEO of OSH Cut, discusses his company’s...
- Trending Articles
Tips for creating sheet metal tubes with perforations
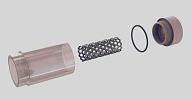
JM Steel triples capacity for solar energy projects at Pennsylvania facility
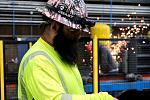
Are two heads better than one in fiber laser cutting?
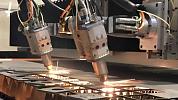
Supporting the metal fabricating industry through FMA
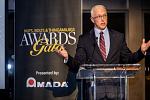
Omco Solar opens second Alabama manufacturing facility
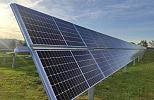
- Industry Events
16th Annual Safety Conference
- April 30 - May 1, 2024
- Elgin,
Pipe and Tube Conference
- May 21 - 22, 2024
- Omaha, NE
World-Class Roll Forming Workshop
- June 5 - 6, 2024
- Louisville, KY
Advanced Laser Application Workshop
- June 25 - 27, 2024
- Novi, MI