Senior Editor
- FMA
- The Fabricator
- FABTECH
- Canadian Metalworking
Categories
- Additive Manufacturing
- Aluminum Welding
- Arc Welding
- Assembly and Joining
- Automation and Robotics
- Bending and Forming
- Consumables
- Cutting and Weld Prep
- Electric Vehicles
- En Español
- Finishing
- Hydroforming
- Laser Cutting
- Laser Welding
- Machining
- Manufacturing Software
- Materials Handling
- Metals/Materials
- Oxyfuel Cutting
- Plasma Cutting
- Power Tools
- Punching and Other Holemaking
- Roll Forming
- Safety
- Sawing
- Shearing
- Shop Management
- Testing and Measuring
- Tube and Pipe Fabrication
- Tube and Pipe Production
- Waterjet Cutting
Industry Directory
Webcasts
Podcasts
FAB 40
Advertise
Subscribe
Account Login
Search
Automotive adhesives get tough
Modern adhesives help make cars lighter and safer
- By Tim Heston
- October 8, 2018
- Article
- Assembly and Joining
If you’ve passed a car accident on the side of the road, particularly one involving newer vehicles, you might see a car body that hasn’t crumpled in the familiar way. It looks less like a torn piece of paper and more like an accordion. The seams between panels haven’t torn open, and that’s because many of those joints aren’t joined exclusively by spot welding or by mechanical means. Instead, new formulations of tough adhesives hold the car together.
Those adhesives aren’t what they used to be either, a point Daniel Sophiea, PhD, R&D leader at Auburn Hills, Mich.-based Dow Automotive Systems, and his team drove home during a Great Designs in Steel conference. The event was held in May and organized by the Automotive Applications Council of the Steel Market Development Institute. After the conference, The FABRICATOR® spoke with Sophiea as well as his colleague Raymond Bis, senior research engineer, about how adhesives are changing the automotive industry and, specifically, what adhesives can do now that they could not do before.
What was their conclusion? To put it in a very unscientific way, adhesives are much tougher than they used to be.
Toughness Matters
Much of Sophiea and Bis’ work focuses not on moisture-cure adhesives—that is, those adhesives that cure at room temperature—but instead on one-part epoxy adhesives that require a curing oven. This includes one-part epoxy hybrids that have enhanced capabilities like improved elongation, peel strength, durability, and corrosion resistance.
As explained in their presentation, these one-part epoxy hybrids can bake through oily substrates. And they’re tough, absorbing energy during impacts, and they don’t become brittle in cold temperatures. They’re designed to endure downstream processes in body-in-white production, including the wash and e-coat cycles.
The adhesive material is mainly used in the automotive industry, but it’s also starting to appear in other industries that require joints with impact toughness, such as truck trailers and all-terrain vehicles.
Regardless, use of epoxy adhesive is increasing, especially in automotive, and the reason for that goes back to toughness. “Under high loads, the adhesives of the past would become very brittle and crack very easily,” Bis said, adding that the brittleness, of course, limited their use. “You basically want to have elongation at high loads, so that under those high loads, when it gets close to failure, it will give some and absorb the energy rather than crack. There’s a lot of chemistry that’s used to do this.”
“There’s an increase in energy management for crashes,” Sophiea added. “This comes from the fact that there’s no weak space between rivets or welds. The whole bond line is coupled, and it forces the metal to do more work. You increase the body stiffness by using a little bit more adhesive, which improves the crash performance and offers the opportunity to reduce the material thickness.”
The adhesive chemistry, combined with refined application techniques (which includes robotics) and the geometry of the applied bead, ultimately helps a crashed car accordion, with bonds intact, rather than tear and crumple. This has increased cars’ crash test safety ratings, even as material becomes thinner and lighter to meet fuel-efficiency standards.
“Adhesives have given automakers much greater weight reduction potential,” Sophiea said. “These materials also give higher static stiffness, which results in better driving, handling, and less noise and vibration.”
When adhesives in automotive began being used several decades ago, they didn’t replace but instead complemented traditional joining techniques. That is, they made the riveted or spot welded joint stronger. Over the years, as automotive engineers became more confident in an adhesive’s performance, and as adhesive technology progressed, joints started having fewer spot welds and mechanical fasteners. They began to rely more on the adhesive for strength.
The geometry of joint overlaps has changed, too. Specifically, as adhesive use has increased, overlaps generally have become narrower. “Overlaps depend on the design and vehicle type,” Sophiea said, “but to give you an idea, a 1-inch-wide overlap could be reduced to, say, 0.5 in. This gives you better design freedom and more mass savings. That smaller overlap is due to the integrity of modern adhesives.”
Traditional spot welders or fasteners are still part of typical adhesive joints in the body-in-white. They still add strength to the joint, but they also serve a practical purpose: to hold the workpieces together as the adhesive cures in the oven.
“These ovens are a major investment,” Bis said, adding that bake cycles aren’t short. Some may take 40 minutes to bake at temperatures between 320 and 400 degrees F. But as sources explained, the long bake cycles still make business sense for automakers, considering the mass savings and design flexibility that come with using adhesives.
New adhesives also have very robust properties, able to withstand exposure to water and humidity and adhere to the surface through different types of oils that may come on materials or composites. Modern adhesives also have more body; as they’re deposited, viscosity allows the adhesive bead to stay where it is rather than run all over. Sources said that this is thanks both to advances in chemistry and better dispensing techniques.
“You now have robotic and other systems that have given us a much more accurate placement of the bead,” Bis said.
Managing Thermal Expansion
Despite their toughness, their ability to help improve driver safety, and the fact they help make vehicles lighter, epoxy adhesives do have their challenges, a chief one being the curing cycle. High heat forces the workpieces to move.
Herein lies the engineering challenge. Work needs to enter the oven having a gap between the material within a certain tolerance, and it needs to exit the oven at a certain gap tolerance. But the gap tolerance while it’s inside the oven needs to be accounted for as well—and, heat having the effect that it does, that gap grows.
Here engineers work to achieve what’s known as hysteresis, or the ability of a material to return to its original shape after cooling. “Unfortunately, when we add adhesive and heat, we have a chemical change, so what you start with isn’t what you end with,” Sophiea explained. “So you have the adhesive developing strength as it goes through the oven, which prevents the two pieces from returning to where they started.”
If not accounted for, thermal expansion can prevent the cured adhesive from having intimate, complete contact between the two workpieces. The workpiece is put into the oven, the workpiece expands and moves, and the adhesive “chases” the other piece of metal during curing. “When it emerges from the oven, you don’t always get intimate contact,” Bis said.
This can be a particular challenge when joining dissimilar materials, like steel to aluminum, each of which have different coefficients of linear thermal expansions (CLTEs).
“Many problems [in curing] relate to managing the thermal expansion of two different materials,” Sophiea said. “If you have steel joined to aluminum, you’ll have this bimetallic strip, but it’s going to separate when it’s in the oven.” And because each material has its own CLTE, accounting for that expansion becomes a challenge. “You run into this problem with joining similar material as well,” Sophiea explained, “but it gets significantly worse when you have material with two different CLTEs, which means they’re expanding at different rates.” This expansion stretches the epoxy adhesive, which can cause issues with the adhesive joint.
How is the adhesive world dealing with this problem? One way relates to the adhesive chemistry. Imagine an adhesive material that, when heated for curing, actually expands to fill gaps. That’s the idea behind expandable epoxy adhesives like Dow Automotive’s BetaMate™ Lightweight Reinforcement (LWR) expandable structural adhesives, which can expand to one and a half times its original size. How, exactly? It’s a system that relies on gas formation during curing, but Sophiea clarified that many of the details are trade secrets, including how the material expands in a controlled fashion.
Regardless, using expandable adhesives can help overcome the challenge of thermal expansion. The base materials are expanding, but now adhesives can expand at an even greater rate, ensuring complete contact and high bond strength.
Adhesive’s Future in Automotive
“We’re still in a mechanical fastening world, and adhesives are designed to meet the needs of traditional body-joining techniques,” Bis said.
Will the industry experience dramatic part redesigns, based around not just welding and fastening but also adhesives? Perhaps not in the immediate future; after all, existing methods of stamping the body-in-white are inexpensive and well-proven.
“Still, there’s a lot that can be done with part design that will help adhesives in the future,” Bis explained. “Regardless, the trend is pretty clear that we’ll see increased use of adhesives in vehicles during the years to come, especially considering the tough adhesives today, which are much more reliable than the brittle adhesives of old.”
Image courtesy of Dow Automotive Systems, www.dow.com/en-us/transportation
About the Author
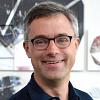
Tim Heston
2135 Point Blvd
Elgin, IL 60123
815-381-1314
Tim Heston, The Fabricator's senior editor, has covered the metal fabrication industry since 1998, starting his career at the American Welding Society's Welding Journal. Since then he has covered the full range of metal fabrication processes, from stamping, bending, and cutting to grinding and polishing. He joined The Fabricator's staff in October 2007.
subscribe now
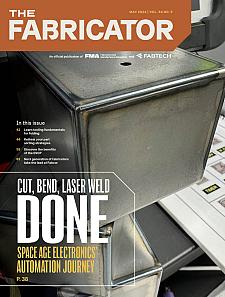
The Fabricator is North America's leading magazine for the metal forming and fabricating industry. The magazine delivers the news, technical articles, and case histories that enable fabricators to do their jobs more efficiently. The Fabricator has served the industry since 1970.
start your free subscription- Stay connected from anywhere
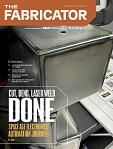
Easily access valuable industry resources now with full access to the digital edition of The Fabricator.
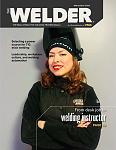
Easily access valuable industry resources now with full access to the digital edition of The Welder.
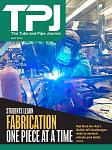
Easily access valuable industry resources now with full access to the digital edition of The Tube and Pipe Journal.
- Podcasting
- Podcast:
- The Fabricator Podcast
- Published:
- 04/16/2024
- Running Time:
- 63:29
In this episode of The Fabricator Podcast, Caleb Chamberlain, co-founder and CEO of OSH Cut, discusses his company’s...
- Trending Articles
Tips for creating sheet metal tubes with perforations
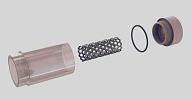
JM Steel triples capacity for solar energy projects at Pennsylvania facility
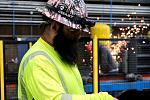
Are two heads better than one in fiber laser cutting?
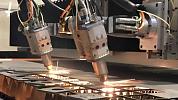
Supporting the metal fabricating industry through FMA
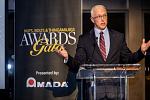
Omco Solar opens second Alabama manufacturing facility
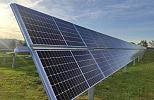
- Industry Events
16th Annual Safety Conference
- April 30 - May 1, 2024
- Elgin,
Pipe and Tube Conference
- May 21 - 22, 2024
- Omaha, NE
World-Class Roll Forming Workshop
- June 5 - 6, 2024
- Louisville, KY
Advanced Laser Application Workshop
- June 25 - 27, 2024
- Novi, MI