Senior Editor
- FMA
- The Fabricator
- FABTECH
- Canadian Metalworking
Categories
- Additive Manufacturing
- Aluminum Welding
- Arc Welding
- Assembly and Joining
- Automation and Robotics
- Bending and Forming
- Consumables
- Cutting and Weld Prep
- Electric Vehicles
- En Español
- Finishing
- Hydroforming
- Laser Cutting
- Laser Welding
- Machining
- Manufacturing Software
- Materials Handling
- Metals/Materials
- Oxyfuel Cutting
- Plasma Cutting
- Power Tools
- Punching and Other Holemaking
- Roll Forming
- Safety
- Sawing
- Shearing
- Shop Management
- Testing and Measuring
- Tube and Pipe Fabrication
- Tube and Pipe Production
- Waterjet Cutting
Industry Directory
Webcasts
Podcasts
FAB 40
Advertise
Subscribe
Account Login
Search
Building improvement at JCB: A case study in lean manufacturing
How the construction equipment-maker designs for lean manufacturing
- By Tim Heston
- January 6, 2016
- Article
- Assembly and Joining
The JCB facility near Savannah, plainly visible from I-95, has a lake in front with a small island where a skid steer, a telescopic handler, and other construction machines sit, mysteriously (see Figures 1 and 2). Countless bored children, riding down to Florida with mom and dad, undoubtedly have asked just how those machines got out there. (In the middle of the night, the lake can be drained to reveal a road to the island.)
The plant is in an ideal location for a global enterprise. The Port of Savannah, currently undergoing an expansion, is a few miles away, as are rail lines and interstate highways.
Plants in Europe, South America, Asia, and JCB’s home base in the U.K., in rural Rocester just north of Birmingham, share the same general layout, from the lobby to the stairs that lead up to the plant mezzanine to the open office adjacent to the factory floor, with fabrication in back feeding coating and assembly toward the front (see Figure 3).
But that open office plan, along with the open layout on the floor, does promote good communication, which in one sense makes each JCB plant unique. They all abide by the general principles of the JCB Production System, which adapts lean manufacturing to JCB’s products. But that communication has led to some significant changes during the past five years.
Although the factory itself looks the same as it did when it opened in 2000—500,000 square feet with 75 percent of that space used for manufacturing—the part flow has changed dramatically. The result has been what everyone everywhere in manufacturing wants. The people at JCB’s Savannah plant now produce more quality products in less time and with fewer resources.
A Changing Market
In late October 2015 the JCB Savannah plant hosted a tour organized by the Georgia Manufacturing Alliance. During the tour, Tim Witter, vice president of manufacturing, shed some light on the challenging conditions in the construction equipment market. In 2014 China was the world’s largest construction market. “But in 2015, of course, the Chinese market has taken a beating; [that] construction equipment market is down 63 percent. Russia has slid 69 percent. Brazil is down 45 percent.”
For decades JCB has had a presence in India, where it’s a construction equipment market leader. “We see 2 percent growth [in India for 2015],” Witter said, “which is a good thing for JCB, but it’s not the rapid growth that we’ve seen historically.”
JCB has 22 manufacturing facilities throughout the world; 17 parts depots; about 10,000 employees; and a portfolio of more than 300 products, including telescopic handlers (what the company is best known for stateside) and skid steers. The Savannah plant, which also serves as JCB’s North American headquarters, employs a little more than 500 people, 300 of whom work on the manufacturing floor.
“We’re currently running a production rate of about 13 machines a day over a single shift,” said Aaron Traywick, JCB Savannah’s manufacturing engineering manager. “Though during peak times in 2011 and 2012, we produced as many as 24 machines a day.”
When it opened 15 years ago, the company produced a mix of backhoes and telescopic handlers for North American sale and distribution, and each product had myriad options. The same conveyor-driven assembly line used today to build skid steers was the same line used to build backhoes and telescopic handlers in 2000.

Figure 2
A lake in front of the JCB plant near Savannah has an island where several machines sit (shown here just behind the fountain). In the middle of the night, the lake can be drained to reveal a road to the island.
Back then all parts for all the different variations of backhoes and telescopic handlers were stored “line-side”—that is, along the main assembly line. Managers determined the sequencing of the machines—this backhoe will follow that telescopic handler, which will follow another backhoe—at the beginning of the final assembly line.
As Daryl Berryman, new product introduction manager, explained, “Back in 2000 we produced all backhoes and telescopic handlers on the same moving assembly line. These products had very different part content and very different cycle times. The backhoes alone came with hundreds and hundreds of options. We would have a basic machine followed by a complex machine, which gave us a big shift in the cycle time.”
Moreover, the sequence in final assembly dictated the build schedule in fabrication and other upstream processes, and there were few if any inventory buffers between those processes.
As Berryman recalled, “Essentially, the assembly line was susceptible to any type of downtime all the way back through the fab shop. There were no buffers in place to manage ups and downs in fabrication or assembly. So that became quite complex to manage.”
Today the plant in Savannah produces skid steers and compact track loaders for the global market, the HMEE (high-mobility engineer excavator) for the military, and backhoes. It also may be adding to its product portfolio. At this writing, there’s a good chance the Savannah plant will again be producing telescopic handlers, but in a very different way, thanks to changes that began to take place about six years ago.
When the construction market hit a low in 2008 and 2009, the people at JCB took a step back and basically started to redesign the factory, starting with the skid steer production. “That was going to become the JCB machine built exclusively in North America for the world,” Berryman said.
They reconsidered how parts were fabricated and sequenced through the operation. And, most important, they reconsidered the design of the skid steers themselves.
The Modular Skid Steer
Touring the plant, you wouldn’t think workers were processing so many product variants. You instead see seemingly standardized products: the same or similar cabs, chassis, and other components (see Figure 4). That’s mainly thanks to the skid steer product redesign six years ago. It was a collaborative effort among sales, design, and manufacturing. Everyone asked if the skid steer line could maintain all the options that made the product competitive in the market, yet still simplify the manufacturing.
“The skid steer was designed in modules to allow us to build it in modules as well,” Berryman said. “Because we were able to work alongside the designers and design the machine in modules, our subassembly areas essentially become the assembly area for each of those modules independently.
“The main line conveyor handles the big stuff; the subassembly areas handle all the complexity,” he continued. “On the moving main line, you want the cycle time from machine to machine to be exactly the same. We then manage all the option content in our subassembly areas, where we’re not tied to a moving conveyor, and we have the flexibility to move people around to manage those more complex builds. Because of the way the product was designed, it really set us up for an assembly process that captures the ability to manage complexity, the ability to have quality inspection points in those lines, and then to manage a steady flow down the moving conveyor of the main line.”
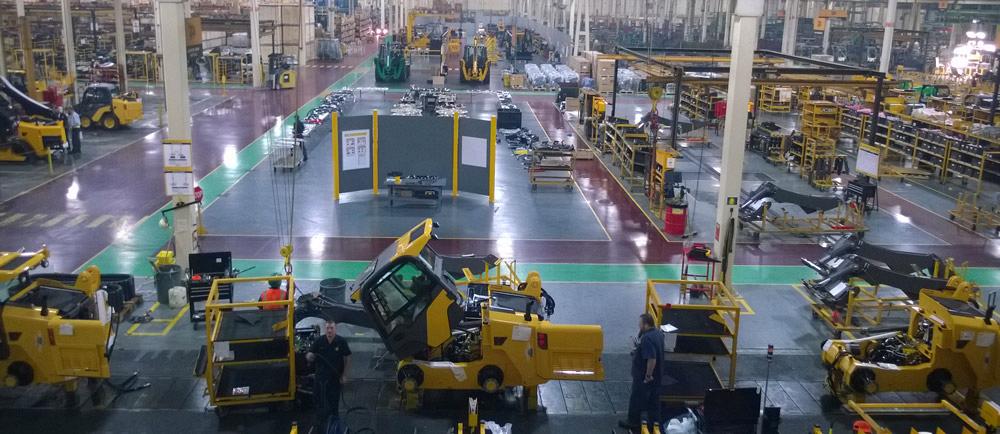
Figure 3
The general layout of the JCB factory floor resembles other JCB facilities’ across the globe, but the details—and the product mix—differ significantly.
The factory produces 17 different models of skid steers. You can immediately identify the JCB skid steers by the fact that they have one rigid lifting arm, allowing operators to enter the cab from the side instead of clambering inside from the front.
“From one machine to the next could be an entirely different build, because of the wide variety of options we offer people,” Traywick said.
The company staffs up assuming that the entire line is for fully loaded machines, which provides the capacity buffer needed to handle the variability. But again, all that variability is handled in the subassembly area. The final moving skid steer line moves at a set pace, and products flow off at a steady rate.
Upstream processes essentially produce common puzzle pieces. To build all the various skid steers the market demands, assemblers put together those puzzle pieces in different ways.
Some unique puzzle pieces are unavoidable, though. For instance, the skid steer line produces equipment for customers around the globe. It would be great to put the same diesel engine in every machine, but not everyone is willing to pay for the Tier 4 engines required by emissions regulations in Europe and North America. So the line needs both Tier 3 and Tier 4 diesels fed into it.
Overall, though, the product’s modular design has simplified manufacturing, a fact that becomes immensely clear in the fabrication area.
Sequencing Starts in Fabrication
“Today we’ve moved to a kitting style of machine build,” Berryman said. “The sequencing of the machines used to start at the assembly line. Now it starts all the way back in fabrication. And the flow of material has moved away from line-side storage toward kitting.”
Walk back in the fabrication area and you wouldn’t know the department was fabricating parts for so many different machines in sequence. This again is thanks to the machines’ modular design. Many different machines use the same fabricated components (see Figures 5 and 6).
“Our metal fabrication strategy has been to be as vanilla as possible,” Berryman said. “We would prefer not to have to define what the machine needs to be until it hits the subassembly area. The last thing we want is the fabrication department trying to manage hundreds of different part numbers. If they can make 10 different part numbers that then can become part of 400 different part numbers once they hit the assembly line, that’s the ideal. And in our cab and chassis fabrication areas, we were able to do that.
“We make only three different cabs and eight different chassis,” Berryman continued.
“And we don’t have to decide what they need to be as far as all the features and options of a particular product until they hit the assembly line.”
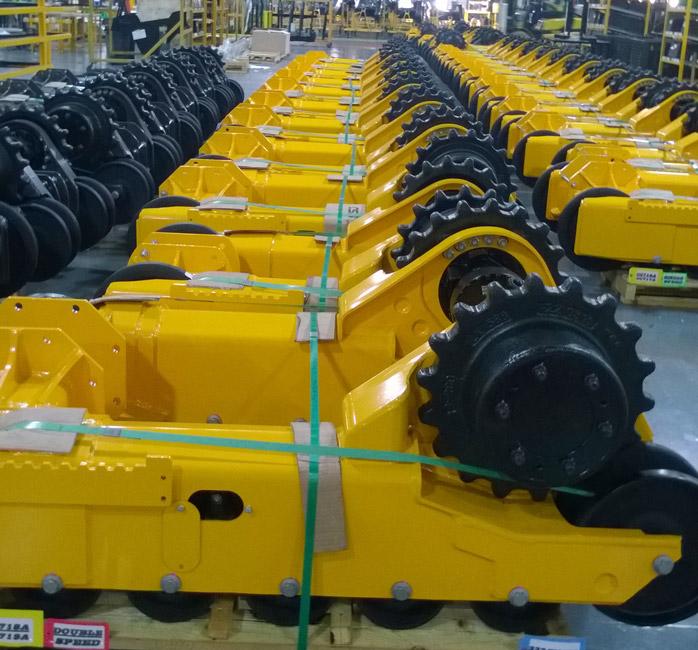
Figure 4
Track pods for compact track loaders (the tracked cousin of the wheeled skid steer) are staged for final assembly.
Moreover, the fabrication department now builds to a carefully managed work-in-process buffer. “They run to a buffer and are not affected by the assembly line being unexpectedly down. And the assembly line can pull from that buffer and not be affected by something in fabrication being down. It really has helped us put more stability in the operation.”
Managing the Constraint
What hasn’t changed since 2000 is the operation constraint: parts coating. JCB’s coating operation involves paint prep via shotblasting, multistage cleaning in alkaline baths, then powder coating or electrocoating. To prepare, coat, and fully cure all the components for one machine takes between eight and 10 hours.
Like in any manufacturing operation, the constraint governs the throughput. To increase throughput—today the maximum is enough sheet metal parts for 13 machines a shift—an improvement team integrated a quick-color-change system inside the paint booths and added different carriers that could handle more parts. The team also replaced a convection oven baking operation with an infrared oven.
When changing colors, operators previously left a gap between different colored parts, because the draft from the convection oven could blow the paint from one batch onto another, contaminating those parts. “With an infrared oven, the coating congeals quickly,” Traywick said. “We can run strictly to demand without risk of contamination.”
Everyone Talking
The Savannah operation tends to outsource simple fabrications to other facilities around the world, including the JCB plant in India; in these situations, a long supply chain remains cost-effective. In recent years, though, the company has been reshoring or near-shoring a number of components, especially the complex ones that require close supplier collaboration. For instance, it outsources armored plate fabrication for the HMEE line to custom fabricators in the Southeast.
On the tour, Traywick pointed to a large area of parts on the floor, including sheet metal subassemblies, metal tubes, and hoses (see Figure 7). About every year or two, JCB employees gather all the contracted parts.
“We lay them out by commodity type,” Traywick said, “and we label each with the supplier and the price. We then give everyone in the office and on the floor a chance to walk through and write down potential cost-savings ideas. So say you see two hoses are almost identical for different products, but one costs twice as much. Could we just use the less expensive one for all products?
“We realize the best ideas come from either the people who are on the floor or people in the front office who don’t have jobs related to machine design or production,” he continued. “In fact, we get some of the best ideas from people who have the least amount of knowledge about the machines. The last time we did this exercise, we took about $1,000 out of the machine cost, which is pretty significant.”
JCB is all about standardization. Everyone on the assembly line gets trained the same way, and the torque they apply to bolts and other joints is continually monitored. Metrics are updated per the procedures outlined by the JCB Production System. The offices and lobby look the same as every JCB facility. Even the lake and its mysterious island mirrors the landscape in front of every JCB plant.
The structure seems rigid, yet according to sources, instead of stifling idea generation, it in fact promotes it. The open office plan encourages purchasing personnel to talk with manufacturing and design engineers, who talk with front-line personnel.
Traywick and others conceded that it’s not always perfect; no company structure really is. But for the most part, the structure allows a global corporation to act small and agile. Such a structure, predictable yet flexible, may be a valuable thing in an increasingly volatile global construction market.
JCB Savannah, 2000 Bamford Blvd., Pooler, GA 31322, 912-447-2000, www.jcbna.com
Georgia Manufacturing Alliance, 750 Longleaf Blvd., Suite C, Lawrence-ville, GA 30046, 678-896-9312, www.georgiamanufacturing.com
About the Author
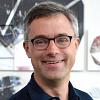
Tim Heston
2135 Point Blvd
Elgin, IL 60123
815-381-1314
Tim Heston, The Fabricator's senior editor, has covered the metal fabrication industry since 1998, starting his career at the American Welding Society's Welding Journal. Since then he has covered the full range of metal fabrication processes, from stamping, bending, and cutting to grinding and polishing. He joined The Fabricator's staff in October 2007.
subscribe now
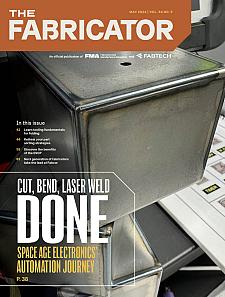
The Fabricator is North America's leading magazine for the metal forming and fabricating industry. The magazine delivers the news, technical articles, and case histories that enable fabricators to do their jobs more efficiently. The Fabricator has served the industry since 1970.
start your free subscription- Stay connected from anywhere
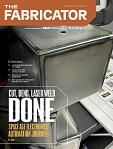
Easily access valuable industry resources now with full access to the digital edition of The Fabricator.
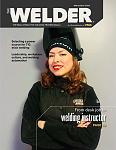
Easily access valuable industry resources now with full access to the digital edition of The Welder.
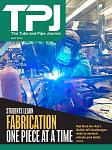
Easily access valuable industry resources now with full access to the digital edition of The Tube and Pipe Journal.
- Podcasting
- Podcast:
- The Fabricator Podcast
- Published:
- 04/16/2024
- Running Time:
- 63:29
In this episode of The Fabricator Podcast, Caleb Chamberlain, co-founder and CEO of OSH Cut, discusses his company’s...
- Trending Articles
Tips for creating sheet metal tubes with perforations
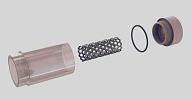
JM Steel triples capacity for solar energy projects at Pennsylvania facility
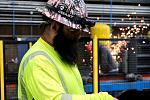
Are two heads better than one in fiber laser cutting?
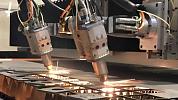
Supporting the metal fabricating industry through FMA
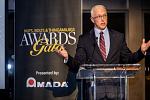
Omco Solar opens second Alabama manufacturing facility
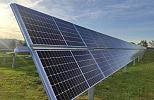
- Industry Events
16th Annual Safety Conference
- April 30 - May 1, 2024
- Elgin,
Pipe and Tube Conference
- May 21 - 22, 2024
- Omaha, NE
World-Class Roll Forming Workshop
- June 5 - 6, 2024
- Louisville, KY
Advanced Laser Application Workshop
- June 25 - 27, 2024
- Novi, MI