- FMA
- The Fabricator
- FABTECH
- Canadian Metalworking
Categories
- Additive Manufacturing
- Aluminum Welding
- Arc Welding
- Assembly and Joining
- Automation and Robotics
- Bending and Forming
- Consumables
- Cutting and Weld Prep
- Electric Vehicles
- En Español
- Finishing
- Hydroforming
- Laser Cutting
- Laser Welding
- Machining
- Manufacturing Software
- Materials Handling
- Metals/Materials
- Oxyfuel Cutting
- Plasma Cutting
- Power Tools
- Punching and Other Holemaking
- Roll Forming
- Safety
- Sawing
- Shearing
- Shop Management
- Testing and Measuring
- Tube and Pipe Fabrication
- Tube and Pipe Production
- Waterjet Cutting
Industry Directory
Webcasts
Podcasts
FAB 40
Advertise
Subscribe
Account Login
Search
Overview of techniques for joining dissimilar materials
How metals and polymers come together harmoniously
- By Paul Kah
- September 12, 2017
- Article
- Assembly and Joining
Editor’s Note: This article has been adapted from the white paper “Techniques for joining dissimilar materials: metals and polymers,” Lappeenranta University of Technology, Lappeenranta, Finland, 2013.
The growing prevalence of polymer materials in structural and automotive applications because of their low weight, high specific strength, elasticity, and low cost has spurred research into the combination of polymers and metals in manufacturing. Parts made with metal-to-polymer joints now are in high demand in the automotive and aerospace industries.
One of the goals for the use of dissimilar joints is to enhance product design flexibility so that differing materials can be used in an efficient and functional manner based on their specific properties. Metal-to-polymer assemblies combine the strength and ductility of metal with the physical-chemical resistance and light weight of polymers. Metal is used in sections where high stiffness and strength are needed, whereas plastic provides unique chemical properties.
Therefore, it is important to maximize the joint contribution of each material to ensure optimal operational performance while still maintaining a weight- and cost-effective approach.
However, joining dissimilar materials often is difficult to achieve. The behavior of such joints is rarely fully understood, particularly when using bonding and heating techniques.
Current Metal-to-Plastic Joining Methods
Several joining techniques are commonly used for hybrid joints between metal and polymer workpieces. They are adhesive bonding, mechanical fastening, and welding.
Each joining technique has advantages and disadvantages. The most appropriate method will depend on application and service.
Mechanical Fastening. Originally used for metal-to-metal joining, mechanical fastening is now used for metal-to-plastic joining too. It comprises using clamping components such as screws and rivets for joint formation without fusing the joint surfaces. It requires mechanical operations such as drilling holes and making screw threads.
Different types of mechanical joining techniques exist for metal-to-plastic joints, but the emphasis currently is on riveting, because it establishes a reliable joint. Some types of riveting need a heating cycle during which the rivets are heated before the fastening so that the rivets shrink upon cooling, clamping the component tightly.
Test results showed that in rivet joining between a metallic and polymeric material, the process depends on sheet thickness and the geometric parameters of the rivet, such as tool design and the riveting force (see Figure 1). Because the bottom material undergoes the greatest deformation, it is important that the polymeric material be placed under the metallic sheet.
Joint configuration often depends solely on service conditions, such as whether it must be leakproof. In some cases, the joint may be designed to tolerate a mismatch in the coefficient of thermal expansion during assembly. A joint also can be made to allow freedom of movement in the plane perpendicular to the clamping member.
Mechanical fastening remains the most often used joining method because of its simplicity. However, it has limitations, such as increased component weight and stress concentration around fastener holes, which degrade strength and eventually create corrosion.
Adhesive Bonding. Adhesive bonding is a solid-state joining technique that relies on the formation of intermolecular forces between the workpieces and the polymeric adhesive itself for joint formation (see Figure 2). It involves the use of a polymeric adhesive, which undergoes a chemical or physical reaction, for joint formation.
The use of adhesive-metal joining has grown substantially in recent years because of the development of very strong and tough adhesives that can withstand both static and alternating loads. Also, they generally weigh less than mechanical fasteners, affording considerable weight reduction. In addition, stress distribution during loading is homogeneous.
However, adhesive bond joints can prove to be problematic, because the bonded joints cannot be disassembled without damage and can emit harmful environmental emissions. In addition, the joints are prone to degradation from moisture, humidity, and temperature and have low resistance in a chemically reactive environment.
Furthermore, bonding demands extensive surface preparation. The workpiece surface properties in an adhesive bond play a vital role in the bonding process, and bond strength and joint durability can be significantly improved by surface treating the workpieces before the bonding. During surface pretreatment, the workpiece’s surface tension increases, but the contact angle of water decreases. Typical surface pretreatment techniques include solvent cleaning, surface chemistry alteration, and abrasion and other topographical changes.
An additional limitation is that bonded joints often fail instantaneously instead of progressively. The most important limiting factor for bonding is uncertainty in forecasting the long-term durability of this kind of joint because of difficulties in carrying out reliable nondestructive testing.
Both mechanical fastening and adhesive bonding require an overlapping joint configuration to achieve the necessary joint strength, which then increases the weight, thickness, and stress concentration of the structure. This limitation restricts the use of these joining techniques.
This has led to the pursuit of a joining technique for dissimilar materials that has greater design flexibility and fabrication rates than adhesive joining and mechanical fastening—and to the development of welding approaches.
Welding. Conventional welding processes such as shielded metal arc welding (SMAW), gas tungsten arc welding (GTAW), gas metal arc welding (GMAW), and submerged arc welding (SAW) have been used to weld dissimilar materials in metal-to-metal joints. However, the high energy inputs of these fusion welding processes result in material metallurgical distortion that hinders this application as well as metal-to-polymer joints.
The melting temperature of metals is extremely high compared to the melting temperature of polymers. Hence, polymers tend to degrade before metals melt.
Polymer welding can be done only on thermoplastics. This limitation exists because the processing of thermosets and chemically cross-linked elastomers is characterized by an irreversible cross-linking reaction that results in degradation; therefore, they cannot be reshaped by heating. Thermoplastics and thermoplastic elastomers can be melted and softened by heat because of the weakening of the secondary Van der Waals and hydrogen bonding forces among interlocking polymer chains. This makes it possible for thermoplastics and thermoplastic elastomers to be remolded upon application of heat, and they can, consequently, be fusion welded.
Emerging Welding Techniques or Joining Dissimilar Materials
Promising welding techniques and new applications for existing welding approaches for joining dissimilar materials have been developed—ultrasonic welding, laser welding, friction stir welding, and friction spot welding—as a way to solve problems related to traditional joining techniques. The effective application of these welding processes necessitates an understanding of their capabilities and limitations and the behavior of metals and polymers.
1. Ultrasonic Welding. Ultrasonic welding is a solid-state joining technique that initiates coalescence via the simultaneous application of localized high-frequency vibration energy with a moderate clamping force (see Figure 3).
This welding technique is characterized by low energy input and requires the clamping and positioning of the workpieces between the welding tool (sonotrode) and an anvil by static force. No microstructural changes occur in the metal.
The workpieces can be two thin sheets or a thick and a thin sheet in a simple lap joint or a butt joint, depending on the direction of the energy supply of elastic oscillations to the welding zone.
Ultrasonic vibration can be applied to welding both metals and plastics, but the welding process differs for each. The actual weld achieved depends on how the ultrasonic energy (vibration) is delivered to the weld.
In ultrasonic metal welding, the direction of ultrasonic oscillation is parallel to the weld area. When the ultrasonic metal welding is realized, the frictional action of the workpiece surfaces initiates a solid-state bond without any melting action of the workpiece. In plastic welding, the case is reversed. For ultrasonic plastic welding, the direction of ultrasonic oscillation is perpendicular to the weld area (see Figure 4).
Researchers experimented with ultrasonic welding of aluminum sheets to carbon fiber-reinforced thermoplastic composites. Their experiment studied the weldability of aluminum alloy 5754 to carbon fiber-reinforced polymer with thicknesses of 1 mm and 2 mm, respectively. They observed that a sound weld occurred at amplitudes around 40 µm as a result of displacement of the carbon fiber-reinforced thermoplastic matrix, thus leading to a better contact between the sheet metal and the fiber.
They also observed that intermolecular reactions in the weld zone formed when oxide layers on the sheet metal peeled off during the welding process. The polymer matrix was actually displaced from the welding zone, which allowed the ductile aluminum to adapt the carbon fibers. This enabled mechanical interlocking between the joining layers and consequently increased the joint strength.
Finally, it was observed that the carbon fibers surrounded the aluminum alloy as a result of the plastic deformation of the aluminum sheet, thus creating a successful weld between the metal and the polymer.
2. Laser Welding. Laser welding offers unique manufacturing opportunities. It complements the fabrication and processing of joints that previously had been difficult or impossible to achieve by other welding methods. Laser welding of metals to polymers can be used to achieve stable metallic, chemical, and covalent bonds between metal and polymer hybrid components (see Figure 5).
Laser direct joining methods between metals and polymers, typically known as laser-assisted metal and plastic joining, have been proposed. The metal-to-polymer joint interface is heated up by the incident laser beam, and melting temperature is attained in the plastic material in a narrow region adjacent to the interface. The resulting high temperature initiates the formation of bubbles in the melted plastic close to the interface, which spread and diffuse into the molten phase and consequently increase seam dimension between the plastic and the metal (see Figure 6).
The bonding mechanism occurs as a result of the combined influences of chemical bonding between the metal oxide film and the carbon atoms of polymers, and the physical bonding phenomenon resulting from the Van der Waals force and mechanical bonding.
The advantages are very fast welding times, small heat input, and the process’s high adaptability. High joint strength can be achieved in laser direct metal-to-polymer joining, and this method is applicable to several metals, such as steel, titanium, aluminum, and iron.
It should be noted, however, that the metal does not melt in this joining process. The limitations are the many parameters, such as travel speed and welding power, that influence the quality and reliability of the eventual joint. Laser welding also has limited design flexibility and is suitable mainly for lap joints because of the need for effective absorption of the laser beam.
Due to the low thermal conductivity of plastics, this means that heat remains concentrated in the material interaction zone. Furthermore, the behavior of the heat depends on the optical properties of the plastics, which are a function of its molecular composition, such as the plastic’s color and the incident beam’s wavelength.
3. Friction Stir Welding. This welding process incorporates three distinct phases: plunging, stirring, and retracting. During welding, a high-speed rotating tool with a probe pin is plunged at a specific rate into the overlapping weld spot until the shoulder of the tool contacts the upper workpiece. This causes plastic deformation around the pin.
Conventional friction stir welding encounters problems when welding plastics. These problems are related to the poor thermal conductivity and diffusion from the macromolecular structure of thermoplastics.
4. Friction Spot Joining. Friction spot joining is a variant of linear friction stir welding except that there is no linear movement of the tool during joining.
During friction spot joining, the friction between the pin and the workpiece generates most of the heat energy for the joint. Friction spot joining of metals to polymers incorporates two distinct processes: the sleeve plunge and the pin plunge.
In sleeve plunging, the workpieces are initially overlapped and clamped between a backing plate and a clamping ring with the metal part on top of the polymer workpiece (see Figure 7). The sleeve and pin rotational motion is then initiated, with both pieces rotating in the same direction.
At some point, the sleeve touches down on the upper metal workpiece, bringing about frictional heating. Simultaneously, the sleeve is inserted into the metal workpiece, thus plasticizing the metal, and the pin is retracted, which consequently results in the formation of an annular space, or reservoir. The plasticized metal is then squeezed into the created reservoir as a result of the sleeve plunging effect.
Upon completion of the joining process, the sleeve is retracted from the metallic workpiece surface and the pin extrudes the entrapped plasticized material back into the weld. The keyhole is consequently refilled.
Tool plunging is set in such a way that plunging takes place only in the metallic workpiece. This is done to avoid damage to the fiber reinforcement of the polymeric workpiece, which can reduce joint strength. The plasticized metallic workpiece is further deformed by the sleeve plunging, resulting in the formation of a metallic nub on the surface of the polymeric workpiece.
Friction spot welding has been feasible in welding dissimilar metals such as aluminum alloy and magnesium alloy.
The feasibility of friction stir welding with metal-to-polymer joints is not fully understood, mainly because of differences between friction stir welding for metals and friction stir welding of plastics. The low thermal conductivity of polymers, along with their complex molecular structure, requires changes in welding tools and tool design. More studies still need to be conducted to understand how the welding method can be controlled.
Conclusion
Of the welding approaches thus far researched, ultrasonic metal-to-polymer welding seems to be a most promising method for hybrid structures when joining metals to polymers. There is uniform mixing between the metallic and polymeric part, which promotes intermolecular contact and mechanical interlocking in the weld zone. High joint strength can be achieved with relatively low energy input and very short welding times. It has been successfully employed to join metal and fiber-reinforced polymers.
Friction spot joining presents similar results as ultrasonic metal welding. However, this joining method has been successfully applied only to low-melting-point metals such as magnesium and aluminum and is not applicable to very thick metals.
Laser welding of metals to polymers can be used to achieve stable metallic, chemical, and covalent bonds between metal and polymer hybrid components. However, bonding occurs in the molten-solid interphase between the plastic and metal; the metal does not melt.
Metal-to-polymer welding processes are promising, but still in the developmental stages; more studies need to be done to effectively understand their feasibility and durability.
Note: References are well-documented and numerous. To view them in the original white paper and to read the in-depth research, refer to “Techniques for joining dissimilar materials: Metals and polymers” (http://www.ipme.ru/e-journals/RAMS/no_23614/05_23614_kah.pdf), 2013.
Images are courtesy of the authors except where noted.
About the Author
Paul Kah
Lappeenranta University of Technology, Lappeenranta, Finland
subscribe now
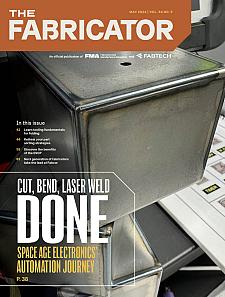
The Fabricator is North America's leading magazine for the metal forming and fabricating industry. The magazine delivers the news, technical articles, and case histories that enable fabricators to do their jobs more efficiently. The Fabricator has served the industry since 1970.
start your free subscription- Stay connected from anywhere
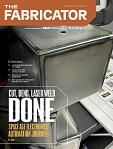
Easily access valuable industry resources now with full access to the digital edition of The Fabricator.
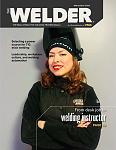
Easily access valuable industry resources now with full access to the digital edition of The Welder.
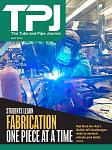
Easily access valuable industry resources now with full access to the digital edition of The Tube and Pipe Journal.
- Podcasting
- Podcast:
- The Fabricator Podcast
- Published:
- 04/16/2024
- Running Time:
- 63:29
In this episode of The Fabricator Podcast, Caleb Chamberlain, co-founder and CEO of OSH Cut, discusses his company’s...
- Trending Articles
Tips for creating sheet metal tubes with perforations
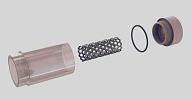
Are two heads better than one in fiber laser cutting?
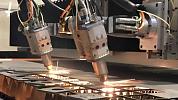
Supporting the metal fabricating industry through FMA
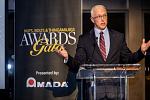
JM Steel triples capacity for solar energy projects at Pennsylvania facility
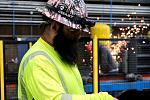
Omco Solar opens second Alabama manufacturing facility
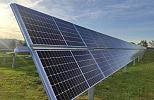
- Industry Events
16th Annual Safety Conference
- April 30 - May 1, 2024
- Elgin,
Pipe and Tube Conference
- May 21 - 22, 2024
- Omaha, NE
World-Class Roll Forming Workshop
- June 5 - 6, 2024
- Louisville, KY
Advanced Laser Application Workshop
- June 25 - 27, 2024
- Novi, MI