Automation Division Manager, North America,
- FMA
- The Fabricator
- FABTECH
- Canadian Metalworking
Categories
- Additive Manufacturing
- Aluminum Welding
- Arc Welding
- Assembly and Joining
- Automation and Robotics
- Bending and Forming
- Consumables
- Cutting and Weld Prep
- Electric Vehicles
- En Español
- Finishing
- Hydroforming
- Laser Cutting
- Laser Welding
- Machining
- Manufacturing Software
- Materials Handling
- Metals/Materials
- Oxyfuel Cutting
- Plasma Cutting
- Power Tools
- Punching and Other Holemaking
- Roll Forming
- Safety
- Sawing
- Shearing
- Shop Management
- Testing and Measuring
- Tube and Pipe Fabrication
- Tube and Pipe Production
- Waterjet Cutting
Industry Directory
Webcasts
Podcasts
FAB 40
Advertise
Subscribe
Account Login
Search
5 steps toward more productive transfer press operations
Automated material handling upgrades boost uptime
- By Mike Brotz
- June 23, 2017
- Article
- Automation and Robotics
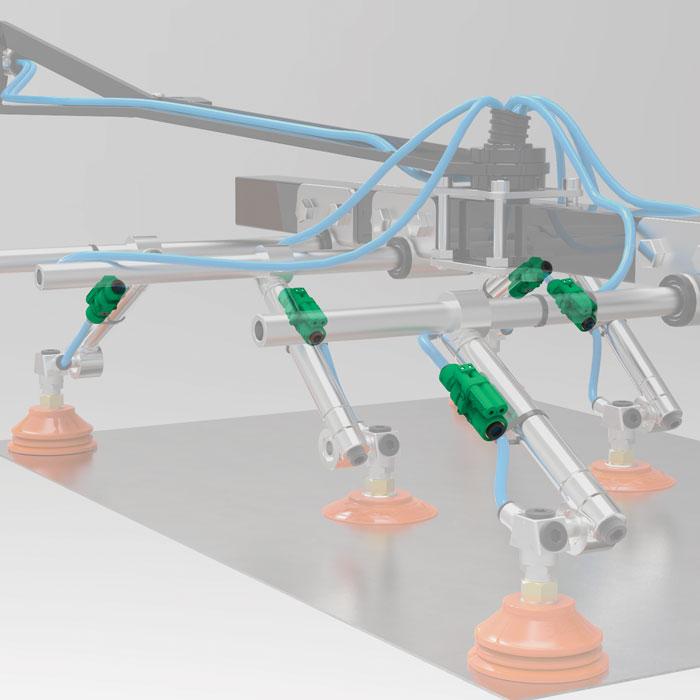
Decentralized vacuum systems, such as one cup per one vacuum generator (in green), generally are more flexible than centralized vacuum systems.
Stamping plants are continuing to seek ways to increase throughput, and automation has been key in helping to achieve productivity goals. An increase of just 1 stroke per minute (SPM) can greatly affect production. A plant running 24 hours a day can produce 1,440 more parts per day. That volume multiplied by 364 days a year equals 524,160 more parts annually. Every SPM counts!
Currently, crossbar presses are capable of speeds in excess of 20 SPM, and robotic tandem presses are pushing traditional rates of 8 SPM up to 12 SPM.
However, challenges can occur at high speeds. Attention must be paid to ensure that blanks do not slide when handled, when the press must be stopped abruptly because of an emergency, and so forth. It is essential that each subsequent blank is positioned into the die properly and consistently (see Figure 1).
Following are five ways to increase productivity at high speeds without costly downtime and increased errors.
1. Feed Single Blanks
At the start of the stamping process, you need to make sure that you are able to pick up blank metal sheets singly. This may sound elementary, but in a fast-flowing process, it can be quite a challenge.
For standard steel sheet metal, you can use fanner magnets and similar products to assist separation; aluminum, however, presents a whole new set of separation challenges in automated feeding at high speeds. Various surface treatments have been used to prevent aluminum sheets from sticking together, but waxy surfaces can leave a lasting residue on cups, ejectors, and other automation equipment, resulting in part slippage and failed automation. Also, blanks may be oily, too dry, or both, making consistent picking of these parts a challenge. This ultimately causes downtime, slowing press speeds.
One widely used solution to the problem is to “float” sheets by blowing compressed air between them. The tricky part is getting the sheets to separate so the air can do its work. New multibellow friction cups aid separation by slightly bending the sheets’ outer edges so less air is needed to float the sheets (see Figure 2). This makes the picking more reliable, again helping to minimize downtime and increase SPM.
Other problems occur when automation equipment comes down too hard on stacks of parts. This tends to wear or damage vacuum cups and causes blanks to stick together. The best approach is to adjust the speed and distance of the equipment to the parts and let the cups do the work. When the cups engage a sheet, they create a peeling effect by curling and separating it from other sheets. As the robot or automation equipment lifts the sheet, a shot of air can be used as an “air knife” to complete the separation. On larger sheets, brushes also can be used to assist the separation.
Also, blowoff can be used to release parts quickly. Vacuum and compressed air tend to take the path of least resistance, so it is important that the circuit is designed and plumbed in such a way that flow paths are equalized. This will allow for speedy picking and releasing of parts.
2. Use a Flexible Design
Flexibility will help customize your production so you can match automation components to your specific needs. Decentralized vacuum systems, such as one cup per one vacuum generator (see lead photo), generally are more flexible than centralized vacuum systems with multiple cups per one vacuum generator.
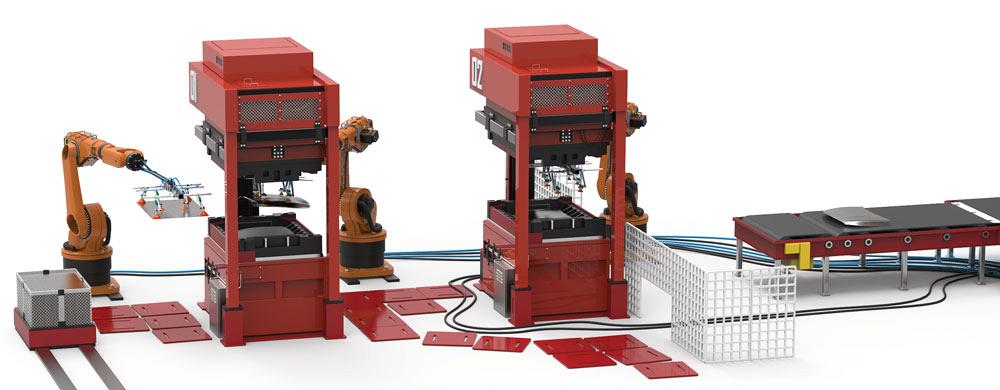
Figure 1
Automation has been key in helping stamping manufacturers achieve productivity goals. An increase of just 1 SPM can raise output by 1,440 more parts a day in a 24-hour-a-day operation. However, challenges can occur at high speeds.
Both centralized and decentralized systems have their own set of advantages and challenges, depending on the application.
Quicker response and release times are the main benefits of a decentralized system. Also, each vacuum cup is independent, which means that if one cup doesn’t make full contact with the part, the other cups will be unaffected. This ensures good, reliable, and consistent parts picking. Tubing lines can be smaller and more flexible. On the rare occasion that the vacuum and blowoff release at the same time, fewer problems occur in a decentralized system. This is very important for accurately releasing parts so that they are in the proper location for the next die.
A challenge of decentralized systems is that having several ejectors on each gripper arm typically makes them more expensive. Also, traditional ejectors are built into the cup tooling, which means that if there are any problems with the ejector, the operator has to replace it and also reset the cup’s position. Newer technology provides lightweight, flexible decentralized ejectors that allow for lighter cup tooling and easy ejector replacement without the downtime associated with resetting cup positions.
Centralized systems, or all-in-one ejectors, usually are located on the robot, upstream of the end-of-arm tooling (EOAT), and they typically are set up as multiple vacuum zones. Usually there are two pumps per EOAT. Each centralized ejector controls a set of vacuum cups. These ejectors have control valves for turning on the vacuum and blowoff. They also incorporate a vacuum switch, giving a go/no-go signal to the robot. This signals that the desired vacuum level has been achieved and that the robot or automation can move the part. The main advantages of this type of system are lower cost and weight.
The challenges of the centralized approach are related to the distance from the vacuum source to the cups. The vacuum flow determines the speed and recovery rate of the ejector, so it is absolutely crucial that this is optimized for speed. Unlike compressed air, vacuum pressure is lower than the atmospheric pressure. Hence, restriction and frictional losses within the vacuum tubing can cause huge delays in both vac-uum and blowoff.
The system and plumbing design is critical. A few rules of thumb apply: The main vacuum line coming from the ejector should have the same inner diameter as the vacuum port of the ejector. This line should then run to a vacuum manifold. Another rule is that the vacuum lines to each cup should be the same length. Again, compressed air and vacuum will take the path of least resistance, so if the lines are unequal or daisy-chained, an unbalanced flow to the vacuum cups will result. This is a common problem in automation. If the flows to vacuum cups are unequal, the overall system will not be optimized.
Another challenge in centralized systems is the troubleshooting time. If the vacuum signal is not activated because there is an air leak, it can take a press operator a long time to find the leak. It could be in any vacuum cup, so the operator needs to inspect them all. Busy operators often change all the cups when a fault occurs to save the time of inspecting each cup individually. Obviously, this practice consumes more cups. It is worth remembering that leaks also can occur at any fitting or connection point running all the way back to the centralized ejector.
New technologies built into ejectors offer a centralized system that is designed to simplify setup and maximize press uptime (see Figure 3). Also, having a vacuum manifold built into the housing allows multiple smaller vacuum lines for the cup automation and amplifies blowoff to ensure quick part release.
3. Avoid Bottlenecks
Configurable equipment on centralized systems that offer optional integrated release functions—amplified blowoff or intelligent blowoff, for example—provides for quick part release. These functions help you avoid production bottlenecks while ensuring that the process runs smoothly at the fastest possible speed. Automatic release functions for decentralized systems play a vital role in reducing plumbing and simplifying controls. In general, such functions work by forcing a massive amount of air to enter suction cups, either by opening a membrane or by blocking the exhaust air with a membrane controlled by pilot compressed air.
Systems that are easy to assemble and disassemble are easier to clean and maintain, helping you to avoid unnecessary or prolonged stoppages. Equipment that allows for individual parts to be replaced quickly or retrofitted will also help to minimize downtime and improve plant throughput.
Quick-fit, push-in connectors are worth using because they speed up the assembly process. They come in varying diameters. Usually this type of connector is mounted directly onto the hose, close to the point of suction, to optimize efficiency. Make sure all parts, including those with integrated functions such as membrane-based release mechanisms or sensors, can be opened for cleaning.
Generic fittings or holders usually are compatible with standard press shop tooling systems, facilitating retrofits and upgrades.
4. Focus on Friction
Suction cups are the workhorses of the system and should be chosen wisely. Make sure they are of the right design and material for top performance. Friction is key. The real cost of suction cups is based on their ability to limit downtime. Here are a few things worth considering when choosing cups:
- How does the cup react to oil? Rubber, nitrile butadiene rubber (NBR), and other materials tend to soak up oil. This causes cups to get spongy and lose memory. It also leads to dry rot and cracking of cups, resulting in premature wear. Polyurethane friction cups are impervious to oil penetration, so they last longer.
- How is the EOAT stored when not in use? Many materials, like thermoplastic elastomers (TPE), set when they lean against other surfaces. This impairs the cups’ ability to return to their original state and they need to be replaced frequently. Conversely, polyurethane friction cups have excellent memory.
- Which is the best friction pattern for cups that handle oily surfaces and high speeds? Many cups have just a surface treatment on their cleat patterns that wears off over time. The cup becomes smooth and shiny as the surface wears, causing slippage and frequent replacement. Like the tread on tires, deep, machined grooves dissipate oil and provide a sharp edge and more friction to keep parts from slipping (see Figure 4).
5. Ensure Safety
Staff safety is vital, but how do you ensure a safe working environment without compromising productivity? The good news is that several of the steps described previously also will help to ensure the safety of the operating staff.
The idea is to design a system that has minimal downtime, minimizing the need for staff to enter into the dangerous press area. Oily conditions make for slippery surfaces for workers entering the cells, so a well-thought-out system is crucial. Incorporate simple and easy-to-understand troubleshooting designs and components.
High-quality friction cups help prevent industrial accidents by gripping objects.
Configurable equipment can help you meet safety regulations by enabling you to assemble handling tools and systems that are ergonomically fit for your purpose. In addition, systems that are easy to disassemble and clean will help your workplace stay clean and safe.
About the Author
subscribe now
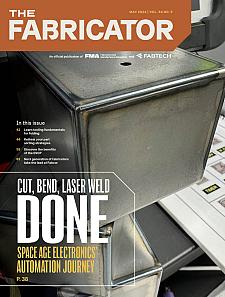
The Fabricator is North America's leading magazine for the metal forming and fabricating industry. The magazine delivers the news, technical articles, and case histories that enable fabricators to do their jobs more efficiently. The Fabricator has served the industry since 1970.
start your free subscription- Stay connected from anywhere
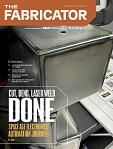
Easily access valuable industry resources now with full access to the digital edition of The Fabricator.
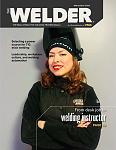
Easily access valuable industry resources now with full access to the digital edition of The Welder.
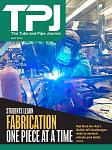
Easily access valuable industry resources now with full access to the digital edition of The Tube and Pipe Journal.
- Podcasting
- Podcast:
- The Fabricator Podcast
- Published:
- 04/16/2024
- Running Time:
- 63:29
In this episode of The Fabricator Podcast, Caleb Chamberlain, co-founder and CEO of OSH Cut, discusses his company’s...
- Trending Articles
Tips for creating sheet metal tubes with perforations
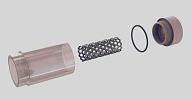
Supporting the metal fabricating industry through FMA
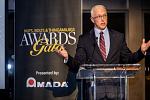
JM Steel triples capacity for solar energy projects at Pennsylvania facility
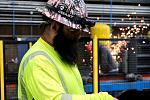
Are two heads better than one in fiber laser cutting?
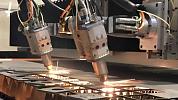
Fabricating favorite childhood memories
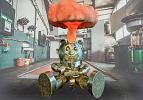
- Industry Events
16th Annual Safety Conference
- April 30 - May 1, 2024
- Elgin,
Pipe and Tube Conference
- May 21 - 22, 2024
- Omaha, NE
World-Class Roll Forming Workshop
- June 5 - 6, 2024
- Louisville, KY
Advanced Laser Application Workshop
- June 25 - 27, 2024
- Novi, MI