Editor-in-Chief
- FMA
- The Fabricator
- FABTECH
- Canadian Metalworking
Categories
- Additive Manufacturing
- Aluminum Welding
- Arc Welding
- Assembly and Joining
- Automation and Robotics
- Bending and Forming
- Consumables
- Cutting and Weld Prep
- Electric Vehicles
- En Español
- Finishing
- Hydroforming
- Laser Cutting
- Laser Welding
- Machining
- Manufacturing Software
- Materials Handling
- Metals/Materials
- Oxyfuel Cutting
- Plasma Cutting
- Power Tools
- Punching and Other Holemaking
- Roll Forming
- Safety
- Sawing
- Shearing
- Shop Management
- Testing and Measuring
- Tube and Pipe Fabrication
- Tube and Pipe Production
- Waterjet Cutting
Industry Directory
Webcasts
Podcasts
FAB 40
Advertise
Subscribe
Account Login
Search
Is automated grinding of 3D parts happening in most fab shops?
It’s happening, just not in most fab shops—but that could be changing
- By Dan Davis
- Updated May 9, 2023
- March 17, 2021
- Article
- Automation and Robotics
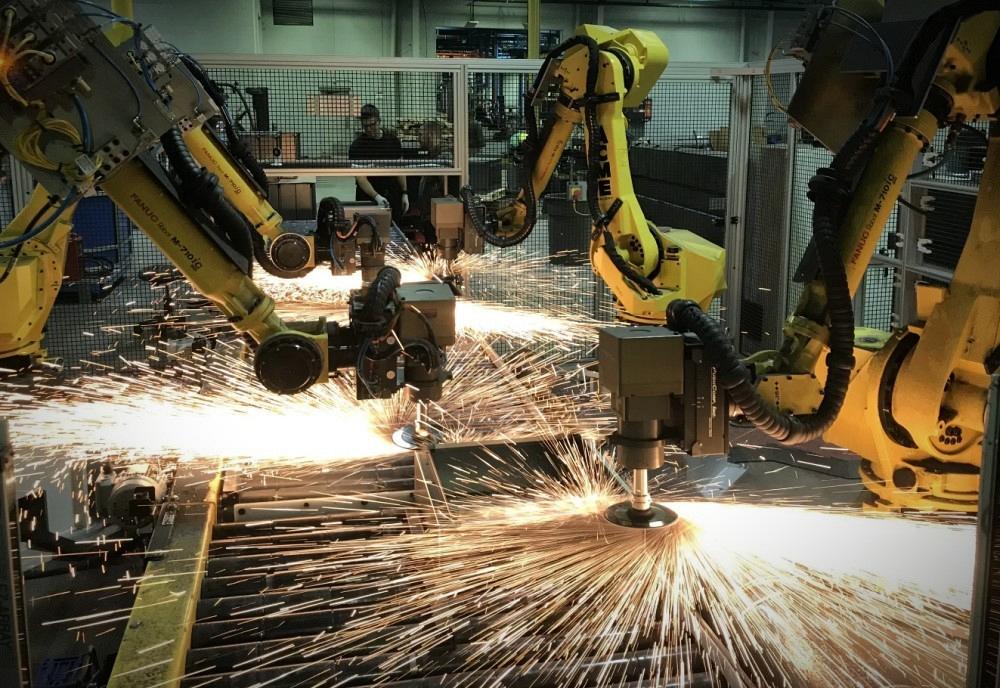
Acme Manufacturing Co. recently installed a four-robot cell dedicated to grinding down and polishing corner welds on box fabrications. Acme Manufacturing Co.
Grinding metal is a grind. There’s no getting around it.
Thermal cutting processes can leave edges that need to be cleaned up. Welding results in spatter on the weldment surface that must be removed. Surfaces and edges need to be prepped to accept paint or a powder coating. Grinding makes all of this possible.
But grinding takes a lot of effort if it’s a manual operation. The operator has to apply some sort of pressure to that grinding tool so that the abrasive belt, disc, or pad can do its job, and he has to repeat that same task for several hours. The manual grinder is likely on his feet, hunkered over the workpiece, and holding that vibrating hand tool for an extended period of time. It’s exhausting.
But that’s just the physical toll. The same operator has to be engaged enough not to remove too much material and apply just the right amount of pressure with the hand tool to avoid burning through too many consumables. He’s also likely wearing protective glasses to keep those metal shavings and sparks out of his eyes and a respirator to avoid breathing in the metal-filled dust.
“With grinding, there’s the three Ds: It’s dirty, dangerous, and demeaning,” said G.A. “Fritz” Carlson III, president/CEO, Acme Manufacturing Co., a robotic technology integrator that’s totally focused on deburring and polishing automation. “When implementing robotic automation, you’re eliminating those three Ds because the robot clearly doesn’t care about all of that.”
That reality is running up against a society that appears ready to embrace all that robots have to offer, particularly as the current pandemic has forced many companies to cut back on employees and do what they can to minimize human-to-human contact. In fact, the Robotics Industries Association reported in January that yearly orders of robots from nonautomotive sectors surpassed automotive robot orders for the first time ever. Sales of robotic units in North America increased 3.5% in 2020 from 2019. Key to that growth was the second-best quarter ever for North American robotic sales, with a 63.6% increase over Q4 2019.
With all that in mind, why don’t you see more robotic grinding cells in fab shops? Welding robots are a more common sight in metal fabricating operations now than they were 10 to 15 years ago, as robotic prices have decreased and skilled welders have been harder to find for the benefits being offered. Conventional wisdom might suggest that robotic grinding cells would be more widely adopted in the sheet and plate fabricating industries as well. But while automated grinding technology is becoming more widely adopted, most of the metal fabricating world just isn’t aware that.
Where Can You Find Robotic Grinding?
As with most things in a capitalist society, companies recognize opportunities where businesses have the biggest needs. The segments of the manufacturing world that had the biggest needs for automated grinding technology were the ones that needed them for a majority of their products.
James Ward, director of sales and marketing, MESH Automation Inc., has developed numerous robotic grinding systems for manufacturing customers over the years. He pointed out that foundries and die casters have always looked for help from finishing robots because the products are never made perfectly. They have parting lines and witness marks that need to be removed so that they have a more finished appearance.
“That’s kind of where we started,” Ward said, “but then we got into machined parts.”
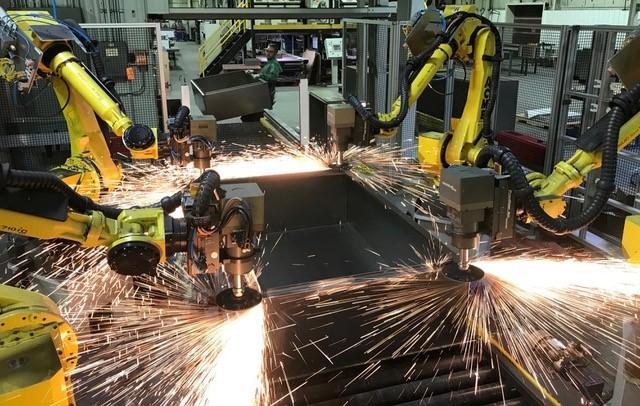
The system recognizes the size of the product coming into the cell and automatically generates a polishing program from the reading. The cell can accommodate boxes from 8 by 8 in. to 48 by 76 in.
Milling machines are wonderful pieces of manufacturing equipment, but they rely on cutting tools. Those tools do not wear out at predictable rates. Newer tools cut more precisely, and older tools can have a dull cutting edge, leaving more burrs. When a shop is machining something like an impeller that is going to be rotating inside of a pump, that impeller has to be burr-free. Robotic grinders are the insurance policy that makes that happen.
In these instances, a robot using abrasives can remove these burrs and other unwanted features quickly. These are not the type of things that a manufacturer wants to put on a CNC grinder to remove.
Carlson said that if a part is considered to have “high value,” determined by the amount of manufacturing time needed to create it or simply because it’s made of something such as titanium, it becomes a lot easier to make the case to use automation for surface and edge finishing. In other words, a blade impeller made of an austenitic nickel-chromium-based superalloy that needs some postprocess finishing is much more of a candidate for a robotic grinding cell than a simple die-cast part.
“So you know the value of that component is going to drive whether the return on investment is really good or just crazy bad,” Carlson said.
Ward said that some manufacturing environments are simply harsh enough that the trend has been to remove humans from the scene. Such “no man on the floor” scenarios, such as those where airborne particulate is deemed dangerous if inhaled directly by humans, require automation to complete the tasks once done by workers.
Ward added that other companies are just looking for parts that don’t show signs of any processing, which means no weld beads or inconsistencies on the surface. Such defects might be noticeable as the part comes off the welding fixture, but they become especially obvious when painted. The farmer wants the same paint quality on his combine as the wealth fund manager wants on his BMW.
“Consumers are very picky these days, and the paint job is the first thing you see,” Ward said.
Manufacturers that have adopted robotic grinding technology have done so to boost productivity, remove the human element from process, and deliver consistent finishes for a better cosmetic appearance. So it’s no surprise that this type of automation has found a home in certain manufacturing settings that might prove awfully familiar to metal fabricators.
Fabricating Examples Using Robotic Grinding
Ward described one cell that was dedicated to the postprocessing of a large weldment. More specifically, the cell was designed to remove slag, arc gas contaminants, and weld spatter.
The weldments were produced in large quantities and in different configurations. A robotic grinding cell was going to help to reduce the time spent to clean up the weldments and introduce a level of consistency that wasn’t going to be possible with the manual grinders using power tools with wire wheels and buffing pads.
MESH Automation designed a cell with a customized operator interface, buffing spindle, and automated fixture. Pressure on the spindle’s wire sheet was programmable and consistently monitored so that it could be changed during finishing. The cell also came with a tooling drawer for replacement of used wire wheels with fresh wire wheels.
The fixture that MESH Automation designed could accommodate the various weldments. A vision camera mounted above the fixture provided verification to the machine that the right part was loaded and that it matched the selected job.
Ward said that the customer was pleased that the cell could finish the cleanup work on these parts in less than 80 seconds. The cell also delivered a cosmetically pleasing surface finish.
“We can get tremendous accuracy and repeatability with these robots,” Ward said.
Electrical enclosures are a familiar sight in some job shops, and Ward said that his company’s robotic grinding cells have found homes in these manufacturing environments as well. One installation in particular accommodated boxes that ranged in size from 12 by 12 in. to 38 by 60 in.
“It could be anything coming down the line at any time,” Ward recalled. “We developed a way to recognize what the size of the part was and established different variables for them to tell the robots what to do.”
In this instance, the robots in the cell were equipped with brushes to grind down the weld seams. They then would switch out tooling to blend in the area of he weld joint with the rest of the surface metal. Ward said someone would struggle to really know where the weld joint was.
“It has gotten to the point where this can be adopted for more varied products, as opposed to just being different kind of variations of a product family,” Ward said. “We refer to that as sequential batches of one.”
A Robotic Grinding Future?
Carlson said that since the pandemic forced manufacturers to take a step back and re-evaluate investments during 2020, companies now are ready to engage plans for future production. Given that manufacturers, even in the face of high unemployment rates, still have trouble finding the right employees to join their companies, they are thirsty for automation technologies that allow them to take advantage of opportunities that don’t necessarily require them to add operators.
Carlson pointed to the firearms industry as an example. Describing it as a “growth area” for Acme, Carlson said that the departure of craftsmen that used to spend entire shifts manually polishing pistol and rifle barrels is causing firearms manufacturers to seek out robots that can step in to do these jobs. Millennials and Generation Zers aren’t interested in making a career out of hand polishing.
Now the firearms industry isn’t exactly what one thinks of when talking about metal fabricating, but making electrical enclosures and large weldments for agricultural and industrial applications is. An automated future with automated grinding is near.
Carlson advised any metal fabricating company thinking about an automated alternative to manual grinding to reach out to a systems integrator to see what might make sense. However, it helps if the integrator has experience with metal finishing.
“When you’re looking for a system for material removal, we understand how abrasives need to be utilized, what horsepower is necessary, and the proper speeds and feeds,” Carlson said.
Ward added a robotic grinding system can cost about as much as a robotic welding cell. Of course, that’s a huge generality, but robot prices are much more affordable than they were 10 years ago. Also, programming these robots is a lot more user-friendly.
An automated grinding cell will not be the right fit for every part, but it might make sense under the right circumstances. Fabricators have to determine how much of a grind the process is for their companies.
Acme Manufacturing Co., www.acmemfg.com
MESH Automation, meshautomationinc.com
Robotics Industries Association. www.robotics.org
About the Author
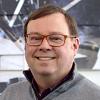
Dan Davis
2135 Point Blvd.
Elgin, IL 60123
815-227-8281
Dan Davis is editor-in-chief of The Fabricator, the industry's most widely circulated metal fabricating magazine, and its sister publications, The Tube & Pipe Journal and The Welder. He has been with the publications since April 2002.
subscribe now
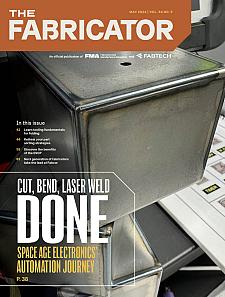
The Fabricator is North America's leading magazine for the metal forming and fabricating industry. The magazine delivers the news, technical articles, and case histories that enable fabricators to do their jobs more efficiently. The Fabricator has served the industry since 1970.
start your free subscription- Stay connected from anywhere
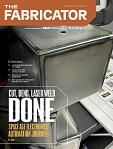
Easily access valuable industry resources now with full access to the digital edition of The Fabricator.
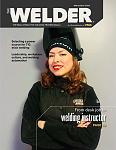
Easily access valuable industry resources now with full access to the digital edition of The Welder.
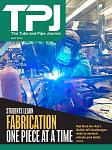
Easily access valuable industry resources now with full access to the digital edition of The Tube and Pipe Journal.
- Podcasting
- Podcast:
- The Fabricator Podcast
- Published:
- 04/16/2024
- Running Time:
- 63:29
In this episode of The Fabricator Podcast, Caleb Chamberlain, co-founder and CEO of OSH Cut, discusses his company’s...
- Trending Articles
Tips for creating sheet metal tubes with perforations
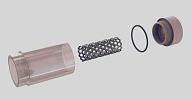
Are two heads better than one in fiber laser cutting?
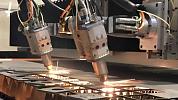
Supporting the metal fabricating industry through FMA
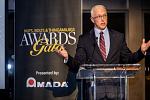
JM Steel triples capacity for solar energy projects at Pennsylvania facility
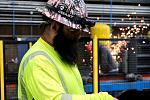
Omco Solar opens second Alabama manufacturing facility
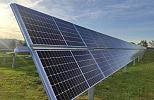
- Industry Events
16th Annual Safety Conference
- April 30 - May 1, 2024
- Elgin,
Pipe and Tube Conference
- May 21 - 22, 2024
- Omaha, NE
World-Class Roll Forming Workshop
- June 5 - 6, 2024
- Louisville, KY
Advanced Laser Application Workshop
- June 25 - 27, 2024
- Novi, MI