Editor-in-Chief
- FMA
- The Fabricator
- FABTECH
- Canadian Metalworking
Categories
- Additive Manufacturing
- Aluminum Welding
- Arc Welding
- Assembly and Joining
- Automation and Robotics
- Bending and Forming
- Consumables
- Cutting and Weld Prep
- Electric Vehicles
- En Español
- Finishing
- Hydroforming
- Laser Cutting
- Laser Welding
- Machining
- Manufacturing Software
- Materials Handling
- Metals/Materials
- Oxyfuel Cutting
- Plasma Cutting
- Power Tools
- Punching and Other Holemaking
- Roll Forming
- Safety
- Sawing
- Shearing
- Shop Management
- Testing and Measuring
- Tube and Pipe Fabrication
- Tube and Pipe Production
- Waterjet Cutting
Industry Directory
Webcasts
Podcasts
FAB 40
Advertise
Subscribe
Account Login
Search
Metal fabricator finds flexibility in its bending department with cobots
Wisconsin manufacturing company finds success with its first collaborative robot installation
- By Dan Davis
- Updated June 20, 2023
- June 19, 2023
- Article
- Automation and Robotics
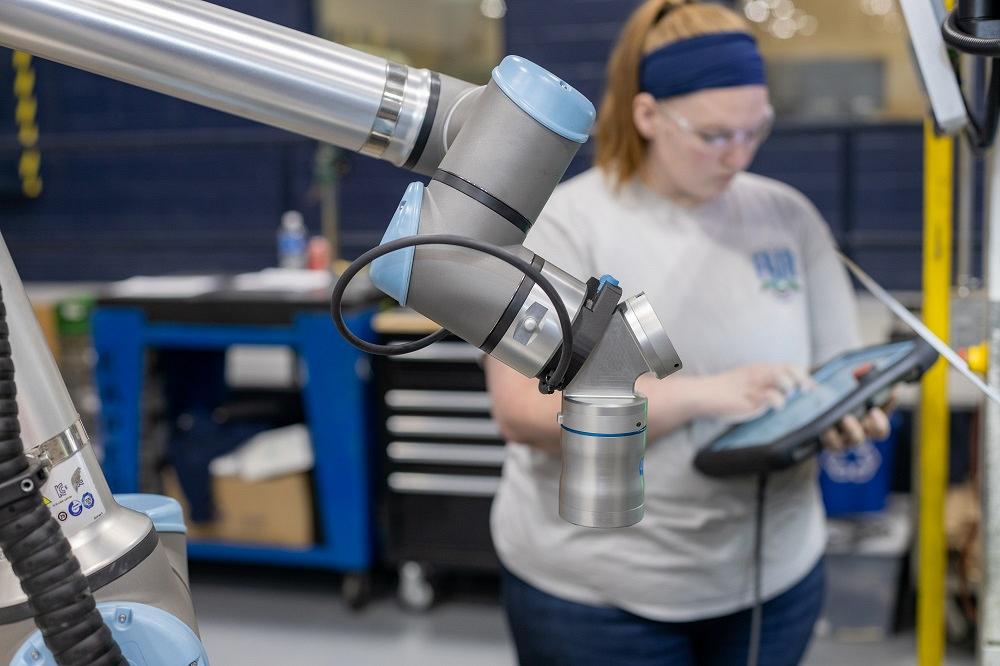
Kapco Metal Stamping relies on former press brake setup specialists and operators who are interested in learning about new technology to program its cobots in the bending department. Images: Kapco Metal Stamping
Any metal fabricator with a large percentage of high-mix, low-volume work looked at bending automation in the 2010s with a little bit of skepticism. Robot programming took time, and excessive downtime associated with programming new jobs was a red flag for some shops. Also, investing in a fixed automation system, complete with cages, was not cheap.
Those hesitations didn’t keep Kapco Metal Stamping, a metal forming and fabrication company in Grafton, Wis., from investigating bending automation three years ago. It found that the technology worked for some jobs but wasn’t as flexible as the company needed it to be.
The system had offline programming, so that wasn’t the issue. The problem was that the cell couldn’t accommodate as much bending work as the manufacturing team would have liked. The software limited complex jobs with multiple bends. Some parts didn’t fit within the confines of the guarding that surrounded the bending robot. When new parts were loaded into the cell for bending, the robot would stop because a human was present within the work area; because part loading was a manual process and took some time, the robot was not running as much as Kapco’s production team would have liked.
The recent emergence of collaborative robots, also known as cobots, gives metal fabricators a new perspective on automation. Kapco’s Advanced Engineering Team, who are responsible for implementing automation at the company’s facilities, saw these first-generation cobots at a recent FABTECH and recognized that they represented a new way to automate shop floor tasks. Even though the cobots were part of a cell, the team saw the potential of being able to move the cobots from one part of the factory to the other.
“With an industrial robot, you’re taking that whole asset offline when it’s not being used. So, in contract manufacturing, for example, when a job ends after two or three years, the robot that was used to do that job is now not being used, unless something else has been lined up,” said Joe Bassindale, Kapco’s director of manufacturing engineering. “We wanted to use cobots to allow ourselves to still run those assets [such as press brakes] manually if we needed to, but then as we ramped up, we can fully utilize them to give us the full benefits of automation.”
A New Approach to Automated Bending
Bassindale said the cobot’s flexibility made it much easier for the Advanced Engineering Team to make its case for investment in this automation. Not only could the cobot be used in front of a press brake, but it could be deployed in a welding cell or in front of a stamping press or machining center.
In 2022, the target for automation was the bending department. Kapco has 17 press brakes that range in size from 40 to 250 tons.
According to Stuart Swanson, Kapco’s advanced manufacturing engineering manager, two of the company’s five 40-ton press brakes had the volume and variety of parts typically formed on those machines that made them the perfect candidates for the automation upgrade.
Kapco selected two cobots from Universal Robots for the new automation cell. The end effectors (the MG10 magnetic gripper and the 2FG7 finger gripper from OnRobot) and pin table were customized internally. The Advanced Engineering Team worked with manufacturing engineers to write standard work, conduct training, program part numbers into the cell, and perform production readiness trials.
After signing the purchase order for the cobots in April last year, Kapco started laying the groundwork required before the cobots could be put into use. The first steps were capability studies to see what parts made the most sense to dedicate to the cobot-focused bending cells. From there, Kapco submitted production part approval process forms to key customers to inform them about technology change in their forming processes. Training of operators followed.
By the time the cobots hit the shop floor in August, Kapco was ready to go.
“It was really a very swiftly implemented project,” Swanson said.
Not Like Your Other Automated Cells
The cobot brake cell includes two press brakes, each equipped with a cobot and a pin table for parts. Each cobot picks flat parts off the pin table, brings them to the press brake to be formed, and then drops them into the designated packaging. This process continues until all parts are consumed on the pin table. Operators can restack flat parts on the pin table while the process is running. The program cycle is all contained within the cobot.
The cobots are adept at even the most challenging bend sequences, some of which reach five or six bends. Each has a force sensor that allows it to get the part right up against the backgauge before the bending process initiates. A regrip station also can be found near the press brake in case certain parts require a change in the way the cobot presents it to the press brake.
“We can load the pin tables as the cobots are running, and we can also remove and replace the part bins. So they never really stop,” Swanson added.
Kapco has leveraged its current press brake setup people and technology-curious operators as cobot programmers. When programming, they literally grab the cobot’s wrist and drag it through the bending process, with each movement being logged as a “teach point,” according to Swanson. Because the folks that used to set up and operate manual brakes know how to do the jobs, they require only minutes to teach the cobots how to perform similar jobs.
As for scheduling, Bassindale said the two cobot cells are treated like any other press brake. Certain jobs are assigned to the cobots, and changeovers are scheduled when they are necessary.
“The only thing really different is, before the cobots, we had a person on each one of these brakes running jobs, but now we don’t have the two people there. We have someone who is dedicated to monitoring the cells while operating another asset, which has been helpful in keeping both cells running to maximize efficiency and uptime,” Bassindale said.
The Outcome
In a typical industrial robot cell, a cage can partially obscure a person’s line of sight into the production area, but these two cobots operate in a wide-open space. Safety scanners are set up around each of the press brake areas, so if someone walks in, the cobots’ speed is greatly reduced. In fact, if a cobot does make contact, built-in force sensors will stop it.
“We’ve been running these for a year,” Bassindale said. “We haven’t had any safety issues or injuries.”
Over that year, Kapco employees also have had the chance to see what the new bending automation is capable of. They recognize that the cobots can do the job, but they also notice that they aren’t necessarily as fast as human operators. While that observation is accurate, that is not the full story either.
Bassindale said the cobots help to maximize bending capacity by forming parts throughout the week, both during the shift and between shifts. For example, a pin table that is fully loaded at the end of the shift can form parts for the next several hours. That’s why when everyone goes home on a Friday afternoon, the cobots are still bending parts.
Bassindale added that the cobots, even at a slower speed, offer repeatability that is hard for a human operator to match. Even the most experienced brake operators are prone to putting a part against the backgauge backwards every now and then, especially if they are having to work their way through several different jobs during a shift. On the other hand, a robot is going to make that part the same way every time, even if those parts are made seven days apart.
Swanson said the press brake is helping to improve safety in the bending department as well. Parts that are deemed “safety critical,” he said, are sent to the automated press brakes. They might be parts with obvious pinch points, for example.
“We keep the people out of those safety-critical jobs,” Swanson said.
With this successful implementation under its belt, the Advanced Engineering Team is now focusing on rolling out cobots and automation to other areas of the company. Swanson said the next application could be stamping, and the team is looking at part-scanning technology that will eliminate the need for a specific table arrangement for part presentation to the cobot. A cobot should be able to scan a bin full of parts, pick it up, no matter what the orientation, and feed it into the stamping press.
Bassindale said cobots represent a huge advantage for any business looking to automate processes because they can be repurposed and used in many areas of the business. A company might start out using a cobot in a pick-and-place application and then place that same cobot in a press brake application.
“If it doesn’t work here, you can always put it somewhere else,” he said. “It raises the confidence level for a shop like us [to invest in automation]. There are just a lot of applications where cobots can be deployed.”
About the Author
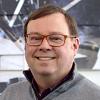
Dan Davis
2135 Point Blvd.
Elgin, IL 60123
815-227-8281
Dan Davis is editor-in-chief of The Fabricator, the industry's most widely circulated metal fabricating magazine, and its sister publications, The Tube & Pipe Journal and The Welder. He has been with the publications since April 2002.
subscribe now
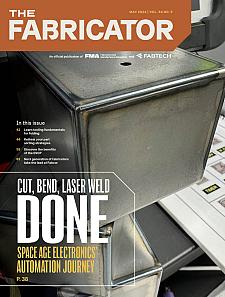
The Fabricator is North America's leading magazine for the metal forming and fabricating industry. The magazine delivers the news, technical articles, and case histories that enable fabricators to do their jobs more efficiently. The Fabricator has served the industry since 1970.
start your free subscription- Stay connected from anywhere
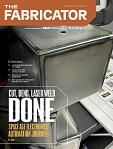
Easily access valuable industry resources now with full access to the digital edition of The Fabricator.
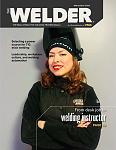
Easily access valuable industry resources now with full access to the digital edition of The Welder.
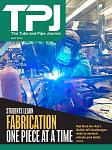
Easily access valuable industry resources now with full access to the digital edition of The Tube and Pipe Journal.
- Podcasting
- Podcast:
- The Fabricator Podcast
- Published:
- 04/16/2024
- Running Time:
- 63:29
In this episode of The Fabricator Podcast, Caleb Chamberlain, co-founder and CEO of OSH Cut, discusses his company’s...
- Trending Articles
Tips for creating sheet metal tubes with perforations
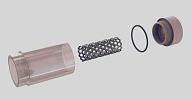
Are two heads better than one in fiber laser cutting?
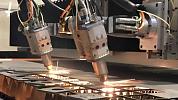
Supporting the metal fabricating industry through FMA
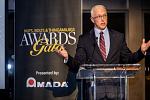
JM Steel triples capacity for solar energy projects at Pennsylvania facility
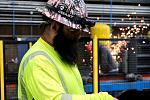
Omco Solar opens second Alabama manufacturing facility
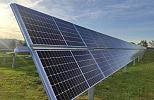
- Industry Events
16th Annual Safety Conference
- April 30 - May 1, 2024
- Elgin,
Pipe and Tube Conference
- May 21 - 22, 2024
- Omaha, NE
World-Class Roll Forming Workshop
- June 5 - 6, 2024
- Louisville, KY
Advanced Laser Application Workshop
- June 25 - 27, 2024
- Novi, MI