Vice President of Marketing
- FMA
- The Fabricator
- FABTECH
- Canadian Metalworking
Categories
- Additive Manufacturing
- Aluminum Welding
- Arc Welding
- Assembly and Joining
- Automation and Robotics
- Bending and Forming
- Consumables
- Cutting and Weld Prep
- Electric Vehicles
- En Español
- Finishing
- Hydroforming
- Laser Cutting
- Laser Welding
- Machining
- Manufacturing Software
- Materials Handling
- Metals/Materials
- Oxyfuel Cutting
- Plasma Cutting
- Power Tools
- Punching and Other Holemaking
- Roll Forming
- Safety
- Sawing
- Shearing
- Shop Management
- Testing and Measuring
- Tube and Pipe Fabrication
- Tube and Pipe Production
- Waterjet Cutting
Industry Directory
Webcasts
Podcasts
FAB 40
Advertise
Subscribe
Account Login
Search
Smart equipment choices in structural fabrication
Managing a world of equipment options in structural fabrication
- By Nick Hajewski
- Updated May 8, 2023
- December 18, 2014
- Article
- Automation and Robotics
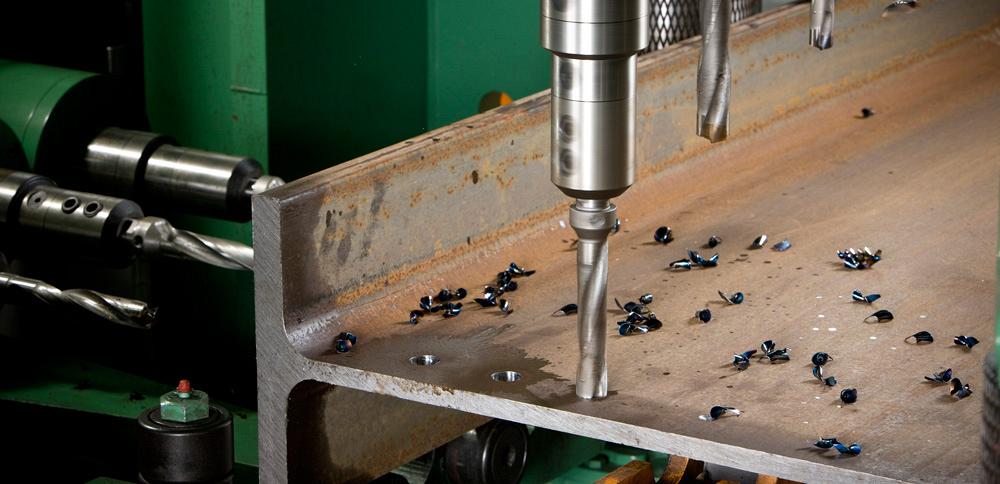
Figure 1
Beam lines range from single-spindle units to advanced multispindle machines, such as this nine-spindle drill line system.
From smartphones to smart watches, the digital world evolves so quickly that it’s hard to keep track of the latest offerings that can affect our day-to-day lives. The structural steel industry isn’t much different.
Today’s equipment options can be a bit overwhelming. Most machine tool providers now offer several models for a given machine category, and many are now developing new types of systems that until recently didn’t even exist.
From the smallest shops to the largest national players, no one fabricator is exactly like the next, and there is no one-size-fits-all machine. But taking a closer look at the equipment offered today, fabricators can make an educated decision when upgrading their production.
Structural Steel Fabrication Equipment Beam Lines
Part-producing machines make individual pieces that a structural fabricator will either weld to other parts or provide to the erector for the final bolted assembly. Sounds simple, right? The reality is far more subtle and complex, of course. The equipment decision includes not only the beam processing machines themselves, but also the options, such as part marking and material handling. Ultimately, the fastest machine for your production depends on the type of production you are doing.
The beam drill line marketplace is a lot different than it was in the early 2000s. They no longer just drill. They can mark, tap, countersink, and mill slots. Some machines have tool changers, others have nine spindles, and some have only a single spindle (see Figures 1-3). Most are designed specifically for carbide tooling, while others make use of high-speed-steel or Morse-taper styles of tooling.
Why such a disparity in technology? It’s all about the fabricator’s unique production requirements. It’s useful to categorize the different types of fabricators as small, medium, and large. During a 40-hour workweek, small fabricators can process 30 to 50 tons, medium fabricators 50 to 125 tons, and large fabricators more than 125 tons. Tonnage is not as cut-and-dry as it sounds; some industries may have lower piece counts yet heavier section weights, and vice versa. Regardless, these benchmarks provide a broad guideline.
Single-spindle drill lines are designed specifically for small to midsized fabricators but can serve many purposes. Single-spindle machines can drill a variety of workpieces, from columns to base plates to clip angles. These machines take up little floor space and can yield substantial capacity gains for those just getting into automation. Still, because they generally lack automation for material handling, single-spindle machines tend to be more effective for small to midsized shops.
These machines aren’t the only option for small fabricators. Shops that want to add more automation may step into the pass-through technology that a multispindle drill line may offer. Pass-through systems streamline material handling by moving material to the machine’s processing area, as opposed to moving the machine to a stationary piece of material. These drilling machines are modular; they grow with the shop. You can place them in tandem with a saw for automatic cutting and drilling of structural profiles. If production needs to increase, you can split two machines apart with a modest investment in material handling, yielding a 30 to 35 percent increase in productivity. Further into the future, you can integrate coping machines into the same line and virtually eliminate crane handling within the system.
For fabricators in the small to midsized production range, basic multispindle drilling machines work with standard high-speed-steel tooling. Medium-sized fabricators can step into either nine-spindle drilling or three-spindle carbide drilling machines with automatic tool changers. These machines are 30 to 50 percent faster than their high-speed-steel counterparts and are typically capable of more advanced processes such as tapping, countersinking, 4-axis layout marking, and slot milling.
For the largest fabricators, equipment that specializes in a given function comes into play, and shop layout becomes crucial (see Figure 4). When it comes to structural equipment, production and versatility correlate directly. As a rule, the more operations a machine performs, the lower the level of production. This becomes evident when introducing 4-axis layout marking options to a drilling system. Fabricators need to take this into account when calculating system capacity.
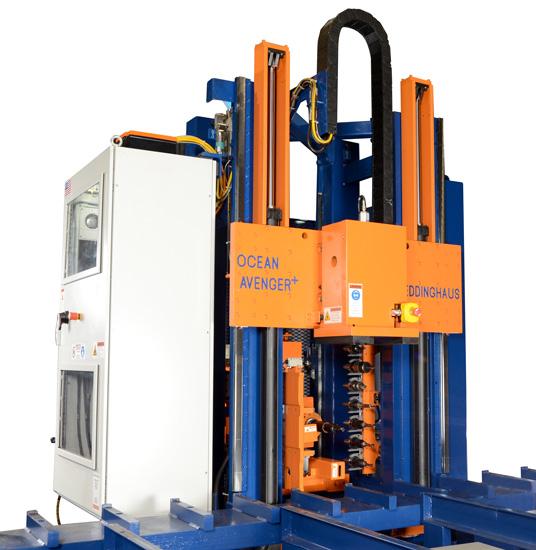
Figure 2
Single-spindle machines take up little floor space yet can yield substantial capacity gains for those just getting into automation.
Coping With Speed
When it comes to coping systems, the speed debate has become all the rage. Which is faster: The traditional oxyfuel or newer plasma technology? A plasma coping machine with a single torch or an oxyfuel coping machine with three torches? The answer is a fairly ambiguous “it depends.”
Plasma coping systems can also create holes and lay out locations for welding and assembly. Although the plasma coper can make holes in addition to cutouts and length cuts while reducing material handling, it overloads a machine with multiple operations and thus reduces its overall productivity.
When it comes to coping by itself, fabricators using both plasma and multitorch oxyfuel machines report the technologies to be equal in speed, and in some scenarios, the oxyfuel is actually faster because of its multiple cutting heads and limited need to probe material to calculate proper torch standoff distances. Oxyfuel can cut heavy sections (jumbo beams) and very close to a beam’s K-section. The technology requires a relatively low initial investment, needs no dust collection system, and uses inexpensive consumables. All this proves that oxyfuel still is at the forefront of structural coping.
So which fabricators can make use of a coping system? For those in seismic areas or working on projects with many welded connections, coping machines are extremely useful. Overall, they work great for midsized to large fabricators, but small fabricators have adopted coping systems as well—especially plasma machines, which fabricators report having similar production capacity to single-spindle drilling systems, in regards to the tonnage and number of pieces produced within a given period. Although the plasma system is costlier, it’s far more versatile.
Automating Fit-up and Welding
As labor continues to be difficult to locate and costly to fund, automation becomes increasingly desirable. But unlike the repetitive nature of industries such as automotive manufacturing, structural steel has unique programming scenarios and unpredictable workpieces due to mill tolerance deviations.
After years of development work, machine builders have overcome these challenges. Structural welding machines now can offer two functions: complete welding of a structural profile and tack welding of parts. Complete welding eliminates the need for manual labor, whereas tack welding increases the overall productivity of the system by eliminating the fitting and layout of sections. In this scenario, shop welders need not spend time fitting and tacking but instead simply finish the welding.
Fully automatic welding machines typically have a part handling robot and a dedicated welding robot (see Figure 5). The operator loads the main structural member into the fixture, and the machine takes over from there. As the part handling robot places detail components at the required location on the main member, the master robot welds the part to the main section.
Because of the large initial investment required, these advanced systems find their home in the facilities of midsized to large fabricators. Production volume can vary based on the number of robots, fixtures, parts scanning stations, and other factors.
As an alternative to automated welding systems, marking systems lay out weld locations directly on the main member of a fabricated section. These stand-alone systems use marking methods ranging from plasma to carbide scribing. They also can lay out copes or hole locations for fabricators that do not have coping or drilling machines. Furthermore, the systems can be placed directly in tandem with a saw for cutting sections to length (see Figures 6 and 7).
Such marking systems, which are relatively inexpensive compared to larger automated systems, have become increasingly popular among the world’s largest fabricators. They have reported that a marking system with multiple plasma torches can lay out more than 160 profiles in one 10-hour shift.
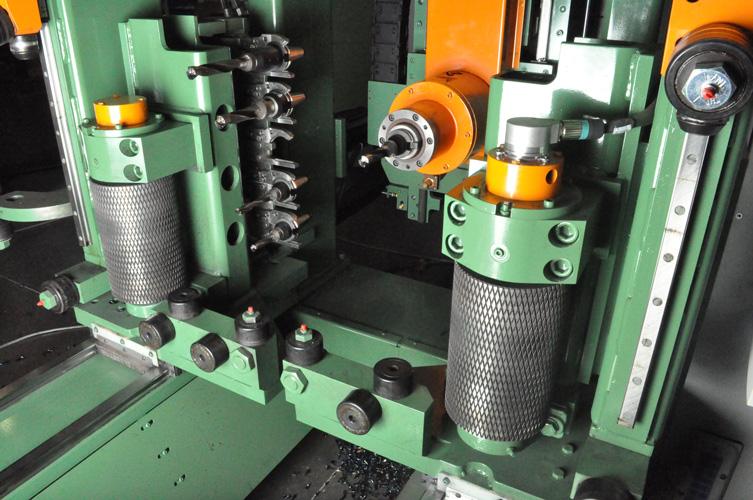
Figure 3
Beam lines, like this three-spindle drilling system with automatic tool changers, can process up to 125 tons of structural steel in a 40-hour workweek.
Translating the Details
Software’s connection to the original design of a structure has become more important than ever. The programming software for each of these types of machines communicates in a unique way with the original building modeling software (commonly referred to as BIM, or building information modeling).
Equipment manufacturers must find a way to tap into the information contained within the original design of a structure; otherwise, a lot more programming will be demanded on the front end of the production process. When researching equipment, make sure that the information you need to run the machine is getting into the program with as little manual intervention as possible.
Also note that simply producing more pieces, or operating more efficiently on a physical level, does not necessarily yield the highest returns possible. You need to know where parts are in the shop, and this is where parts tracking enters the picture. To round out your production, be sure that production management controls are streamlined. This doesn’t always mean an investment in software, but this area does require investigation.
Many have the ability to link programming and control software with modern MRP platforms to make production management easier—important for midsized and large fabricators dealing with high volumes.
Just Scratching the Surface
There’s more to a structural fab shop than structural members, of course. Advances for smaller detail components, like plates and
angles, have greatly increased the capacity of many structural fabricators. Although these parts typically comprise between 10 and 15 percent of a fabricator’s overall tonnage, they tend to be the most labor-intensive—and, therefore, dollar per pound, much more expensive.
Like equipment for structural members, angle line and plate processing machines offer different levels of productivity and versatility, and the same is true for surface cleaning and coating systems.
The Right Choice for Structural Steel Fabrication Equipment
The options abound, but at the end of the day, what matters most is that the firm operates better from a business perspective: Do more and spend less.
Say you need to produce more beams per hour, and you purchase a multiprocess system that drills, taps, mills, cuts, and perhaps even applies layout. It sounds about as efficient as you can get. But when you place the system in operation, you find that your cycle time isn’t what it needs to be. That’s because, again, when you add another operation to the machine work envelope, your cycle time gets longer. In this case, a series of dedicated machines, with automated material handling in between (see Figure 3), may be the better choice. On the other hand, smaller structural fabricators may need the efficiency that a multiprocess system provides.
Granted, this is an obvious example, but there are plenty of subtler choices to make. Each investment offers benefits. As a researcher and a buyer, it is up to you to pick the option that gives you the greatest advantage to stay ahead of your competition in today’s structural steel marketplace.
About the Author
Nick Hajewski
300 N. Washington Ave.
Bradley, IL 60915
815-937-3800
Related Companies
subscribe now
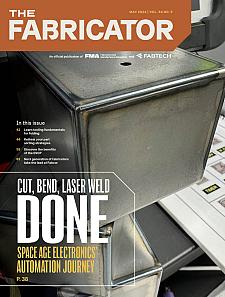
The Fabricator is North America's leading magazine for the metal forming and fabricating industry. The magazine delivers the news, technical articles, and case histories that enable fabricators to do their jobs more efficiently. The Fabricator has served the industry since 1970.
start your free subscription- Stay connected from anywhere
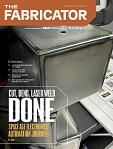
Easily access valuable industry resources now with full access to the digital edition of The Fabricator.
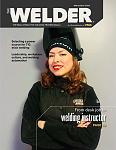
Easily access valuable industry resources now with full access to the digital edition of The Welder.
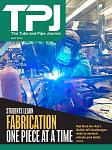
Easily access valuable industry resources now with full access to the digital edition of The Tube and Pipe Journal.
- Podcasting
- Podcast:
- The Fabricator Podcast
- Published:
- 04/16/2024
- Running Time:
- 63:29
In this episode of The Fabricator Podcast, Caleb Chamberlain, co-founder and CEO of OSH Cut, discusses his company’s...
- Trending Articles
Tips for creating sheet metal tubes with perforations
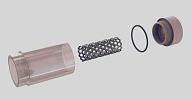
JM Steel triples capacity for solar energy projects at Pennsylvania facility
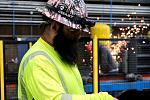
Are two heads better than one in fiber laser cutting?
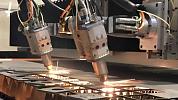
Supporting the metal fabricating industry through FMA
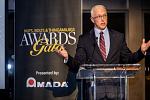
Omco Solar opens second Alabama manufacturing facility
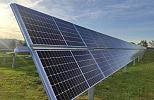
- Industry Events
16th Annual Safety Conference
- April 30 - May 1, 2024
- Elgin,
Pipe and Tube Conference
- May 21 - 22, 2024
- Omaha, NE
World-Class Roll Forming Workshop
- June 5 - 6, 2024
- Louisville, KY
Advanced Laser Application Workshop
- June 25 - 27, 2024
- Novi, MI