Senior Editor
- FMA
- The Fabricator
- FABTECH
- Canadian Metalworking
Categories
- Additive Manufacturing
- Aluminum Welding
- Arc Welding
- Assembly and Joining
- Automation and Robotics
- Bending and Forming
- Consumables
- Cutting and Weld Prep
- Electric Vehicles
- En Español
- Finishing
- Hydroforming
- Laser Cutting
- Laser Welding
- Machining
- Manufacturing Software
- Materials Handling
- Metals/Materials
- Oxyfuel Cutting
- Plasma Cutting
- Power Tools
- Punching and Other Holemaking
- Roll Forming
- Safety
- Sawing
- Shearing
- Shop Management
- Testing and Measuring
- Tube and Pipe Fabrication
- Tube and Pipe Production
- Waterjet Cutting
Industry Directory
Webcasts
Podcasts
FAB 40
Advertise
Subscribe
Account Login
Search
The many roads toward automated metal processing
Technology strategies vary greatly throughout the industry, hinge on market demand, shop culture
- By Tim Heston
- Updated May 9, 2023
- July 20, 2020
- Article
- Automation and Robotics
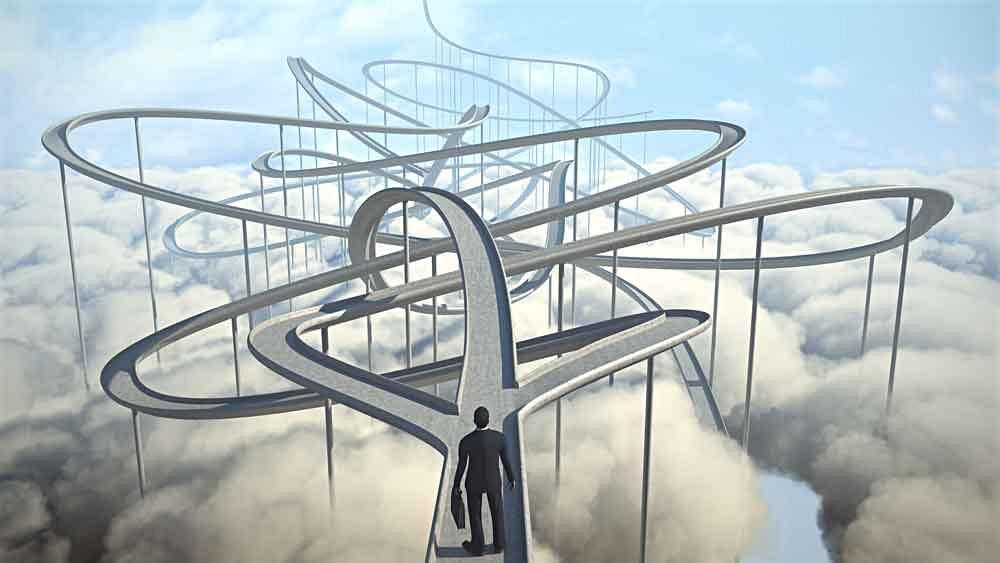
Different metal fabrication shops have different cultures and different customer bases with different demands. No wonder the industry’s automation and technology strategies vary so greatly. Getty Images
Years ago a reader asked why fabricators invested in automation. Was it because they couldn’t find a skilled person to do the job, or was automation just inevitable regardless of available talent? At the time I thought automation was just inevitable simply because of the raw time savings. For instance, an incredibly skilled press brake operator might set up a complicated job in as little as 15 minutes, but an automatic tool change (ATC) press brake might do it in five.
Then in 2019 I visited Food Warming Equipment Inc.’s plant in Tennessee and saw workers swapping out dies and punches within a few minutes—so fast that, though they might not have kept up with an ATC brake, they gave it a run for its money. Because of the nature of the product mix and job flow, bending wasn’t the constraint. Operators kept pace. The company did have several robotic press brake cells for certain part families, but the manual press brake operator’s job didn’t go away. Rewind the tape about 20 years. At the FABTECH show that year I chatted with a weld shop owner who was looking at the robot welding cells on the floor but told me he wouldn’t dare buy one. His welders, extremely skilled individuals tough to find even then, thought the robots were out for their job. His small shop was doing just fine, so why rock the boat?
Fast-forward to FABTECH 2019. I recall chatting with executives at Boca Raton, Fla.-based AOC Metal Works who told me they had no choice but to invest in automation. With record-low unemployment (and yes, this was only last November), shops simply had no choice but to automate.
Fast-forward a few months to January 2020. Jeff Cupples, vice president at Jackson, Tenn.-based Cupples’ J&J Co. Inc., described how a team of sorting personnel and operators successfully offloaded parts manually within the shop’s extensive laser cutting operation, with almost 20 machines ranging up to 15 kW in power. The offload process took coordination, but the approach worked.
On the other hand, fabricators like Nu-Way Industries in Des Plaines, Ill., and Ometek Inc. in Columbus, Ohio, continued their robust growth with a full suite of automation, including advanced sheet storage and retrieval systems. The same could be said for U-Haul’s sheet metal fabrication plant in Glendale, Ariz., and various other shops across the country.
All this says that no one size fits all when it comes to an automation strategy, and the proof comes from The FABRICATOR’s 50 years of coverage.
No Generalizations
The FABRICATOR’s editors have visited literally hundreds of fabricators over the past 20 years. You’d be hard-pressed to find such extensive on-the-ground coverage elsewhere. A local newspaper reporter might call a shop owner for a few comments, and business analysts might conduct research mainly through the internet, email, and phone calls, but not actual visits to the shop floor.
The FABRICATOR editors play a unique role in this industry. We visit shops with no intent to sell a product or service. We just listen, observe, and report. And we see the gamut when it comes to automation. A structural rolling and bending operation might have a few advanced plate and angle rolls next to some dinosaurs that have been rolling metal since the Hoover administration. Old iron dies hard. We see on-machine programming as well as offline programming with 3D simulations, often on the same shop floor.
Some incredibly advanced operations have graced these pages too. A notable one is 247TailorSteel, a fabricator in the Netherlands that uses automated guided vehicles (AGVs) to transport raw stock to and cut parts from more than 50 laser cutting machines across several plants. Those AGVs then make their way to an army of ATC press brakes.
No One Way to Automated Metal Processing
All this makes for a complex reality. Some shops are gleaming showrooms of high-tech software and machinery, a shining example of what Industry 4.0 can be. Others use age-old equipment and still rely solely on paper prints. What’s driving these differences?
Market demand for one. We’re told that U.S. manufacturing thrives on serving customers with ever-changing demands, and that’s true in most cases—but not all. I recall visiting a shop in Detroit with steel-rule dies on the shelf. They were still used to stamp blanks for products that hadn’t seen a design change in more than 50 years.
Another custom fabricator in Mississippi found a niche fabricating replacement parts for boilers. The boilers in power generation and other sectors have been in use for decades and weren’t about to be retired anytime soon. Like old machine tools, the demand for replacement parts in certain aftermarkets takes a long time to die completely.
Another driver behind such differences in automation strategies comes from the various shop cultures in this industry, created by owners, managers, and the talent on the floor. A shop with a few talented press brake operators might opt to stay with equipment they are most comfortable with. But what if the shop hires new brake operators and perhaps tackles a new customer base with different expectations? If it has the funds, the shop might decide to upgrade.
It boils down to the nature of the markets a fabricator serves and the people involved. As The FABRICATOR’s coverage has shown through the years—outside of some business fundamentals like ensuring customer satisfaction, adequate cash flow, and, yes, even a little profit—there is no one “right way” to run a shop.
In aggregate, all the fab shop profiles the magazine has run over the years show how the industry is changing, not with grand statements about the direction of manufacturing, but with stories of what fabricators are actually doing to make their operations better. The quest for improvement ties this incredibly diverse industry together.
Sometimes improvement calls for a deep dive into automation. It’s not a cure-all, and if implemented badly it can even make problems worse. But if a shop implements automation in a smart way, it can grow revenue and eventually dominate its market—if, that is, the company cultivates and grows a mix of customers that appreciates and rewards those efforts.
One Shop, Hypothetically
Picture a sheet metal fab shop of the 1970s, punching templates and all. Operators mark a hole location with a vertical and horizontal line; center the tool on those crosshairs and drill; then repeat until the part template is made, ready to be used on a duplicator punch press.
The shop has some NC equipment too. Programmers take paper drawings and plot the X and Y coordinates for each hole they need to punch. As they get into complex geometries, such as nibbling an arc, they use trigonometry to determine the coordinates for the starting point, the intermediate path, and the end point.
And with no CAD/CAM, draftsmen nest parts manually, piecing components together like a puzzle, with blank sizes for formed parts calculated with the right bend deductions. They input code into a teletype to create a roll of paper or Mylar tape to be fed into the machine control, which of course has no memory at all. Blanks make their way to the forming department full of mechanical press brakes that perform bottoming and coining—no air bending, of course. Then it’s on to welding, finishing, and assembly, areas with no automation to speak of.
Then come the changes: CAD/CAM, user-friendly machine controls, more process automation to ease machine setup and operation, controls that can download programs directly from a network, offline bend programming and simulation, and robotic welding cells simulated and programmed offline. All of it is designed to handle a high product mix. Then come fiber lasers and the associated material handling automation. Immense towers make for a robust live inventory, constantly tracked and able to be retrieved at a moment’s notice.
That’s one path of automation, though again, which path a shop takes depends on the circumstance. Even so, what makes this automation scenario so exciting is its potential future. Considering how rapidly technologies like additive manufacturing, artificial intelligence, and machine learning are changing, technological advancement is taking on not a linear curve but a logarithmic one, with greater leaps being made year after year. The difference between the fabrication tech of 1970 and 2020—a span of 50 years—might actually be less than the difference between the shop of today and 30 or even just 20 years from now.
Consider again that hypothetical shop but with a laser cutting operation that’s even more automated. Blanks move from offloading and automated part stacking to AGVs that transport jobs downstream. Every job is tracked, with a transmitter placed into the job traveler jacket itself, so everyone knows what path those parts traveled from the laser to the shipping dock—and, most importantly, how long the journey took. The schedule sees what’s happening constantly and adjusts to suit.
The shop also augments their welding capacity by adapting automated laser welding. One fiber laser welding cell does the work of two or three robotic arc welding cells. The shop has a range of cobots welding simpler joints (though with simplified programming suited for high-mix production), plus a core of highly skilled manual welders working on the most challenging jobs.
But it doesn’t stop there. Shop engineers work with new so-called “cloud-based manufacturing automation platforms”—a company called Vention (vention.io) is an early example—where they can configure machine tending and conveyance automation. AI maps part flow and then helps shop personnel design the right conveyance system that brings parts to bending, welding, and finishing.
Finding good people remains the greatest challenge, of course, but it’s no longer called a skilled labor crisis. Labor implies a unit of measure around a specialized task. But the shop of the future can’t survive like this. It needs talented, engaged people who know how to wield a welding torch and grind a weld, but also how to give input on how automation can present work to the welding cell. The shop of the future doesn’t need labor; it needs cross-trained, curious, energized talent.
The Reality of Automated Metal Processing
That’s the pie-in-the-sky potential. Of course, all this doesn’t give any consideration to what people want and are willing to pay for. The availability of financial capital in metal fabrication might be on the rise. The private equity players involved with some of the companies in the 2020 FAB 40 might be a harbinger. And financial capital available to U.S. manufacturing in general might be ramping up as supply chains adapt to a postpandemic world.
Still, the people in metal fabrication are in the drivers’ seat. They see many roads ahead of them, and which one they take will depend on the shop culture and the markets they serve. That said, because technology’s potential continues to grow, the roads fabricators choose will become ever more divergent, and The FABRICATOR will be there to cover them all.
About the Author
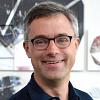
Tim Heston
2135 Point Blvd
Elgin, IL 60123
815-381-1314
Tim Heston, The Fabricator's senior editor, has covered the metal fabrication industry since 1998, starting his career at the American Welding Society's Welding Journal. Since then he has covered the full range of metal fabrication processes, from stamping, bending, and cutting to grinding and polishing. He joined The Fabricator's staff in October 2007.
subscribe now
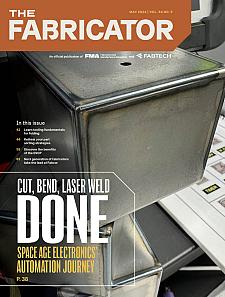
The Fabricator is North America's leading magazine for the metal forming and fabricating industry. The magazine delivers the news, technical articles, and case histories that enable fabricators to do their jobs more efficiently. The Fabricator has served the industry since 1970.
start your free subscription- Stay connected from anywhere
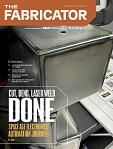
Easily access valuable industry resources now with full access to the digital edition of The Fabricator.
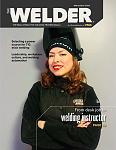
Easily access valuable industry resources now with full access to the digital edition of The Welder.
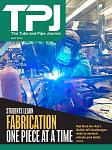
Easily access valuable industry resources now with full access to the digital edition of The Tube and Pipe Journal.
- Podcasting
- Podcast:
- The Fabricator Podcast
- Published:
- 04/16/2024
- Running Time:
- 63:29
In this episode of The Fabricator Podcast, Caleb Chamberlain, co-founder and CEO of OSH Cut, discusses his company’s...
- Trending Articles
Tips for creating sheet metal tubes with perforations
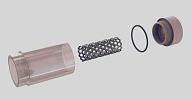
Are two heads better than one in fiber laser cutting?
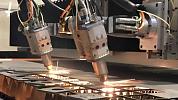
Supporting the metal fabricating industry through FMA
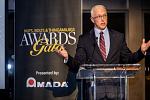
JM Steel triples capacity for solar energy projects at Pennsylvania facility
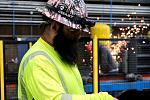
Omco Solar opens second Alabama manufacturing facility
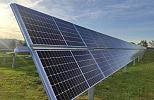
- Industry Events
16th Annual Safety Conference
- April 30 - May 1, 2024
- Elgin,
Pipe and Tube Conference
- May 21 - 22, 2024
- Omaha, NE
World-Class Roll Forming Workshop
- June 5 - 6, 2024
- Louisville, KY
Advanced Laser Application Workshop
- June 25 - 27, 2024
- Novi, MI