Editor-in-Chief
- FMA
- The Fabricator
- FABTECH
- Canadian Metalworking
Categories
- Additive Manufacturing
- Aluminum Welding
- Arc Welding
- Assembly and Joining
- Automation and Robotics
- Bending and Forming
- Consumables
- Cutting and Weld Prep
- Electric Vehicles
- En Español
- Finishing
- Hydroforming
- Laser Cutting
- Laser Welding
- Machining
- Manufacturing Software
- Materials Handling
- Metals/Materials
- Oxyfuel Cutting
- Plasma Cutting
- Power Tools
- Punching and Other Holemaking
- Roll Forming
- Safety
- Sawing
- Shearing
- Shop Management
- Testing and Measuring
- Tube and Pipe Fabrication
- Tube and Pipe Production
- Waterjet Cutting
Industry Directory
Webcasts
Podcasts
FAB 40
Advertise
Subscribe
Account Login
Search
A guide to tandem press brakes
When does it make sense for a metal fabricator to invest in this special bending combination?
- By Dan Davis
- September 5, 2023
- Article
- Bending and Forming
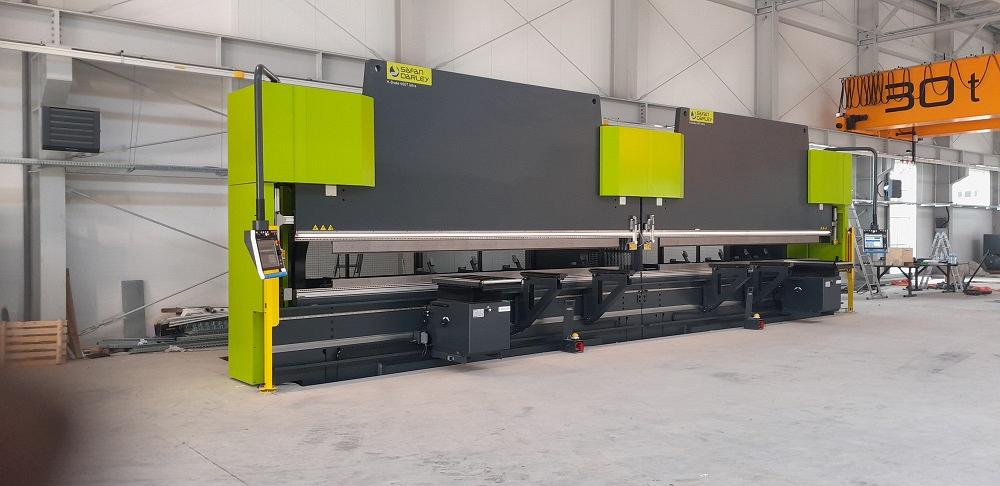
FIGURE 1. Tandem brakes might not be the best fit for all long-form bending, but when that type of forming activity represents at least 20% of a shop’s bending activity, tandem press brakes might make sense. Images: SafanDarley
In the spirit of talking about tandem press brakes, let’s provide two examples of why a metal fabricator chose to go that route.
But before we start, if you aren’t aware of what a tandem press brake is, you just need to picture two press brakes, typically the same size, placed right next to each other, but configured so that they can be used as one bending machine (see Figure 1). When not needed to bend long workpieces, the press brakes then can be used individually.
Who might want this type of press brake setup? A trailer manufacturer is a good example. Kyle Zellmann, vice president of sales, SafanDarley North America, described how a shop that produces a lot of long workpieces for especially long trailers required tandem press brakes for its mix of fabricated products. While long trailers don’t make up a majority of the fabricator’s sales, they do account for about 20%, which represents production volumes where a tandem press brake makes sense.
That’s why the company purchased two 230-metric ton brakes that can be combined to offer one 8.5-m-long bed, just under 28 ft., for the bending of 20-ft.-long channels. For the other 80% of the products formed by the company that aren’t as long, the press brake technicians can use the two brakes as individual bending machines with 4-m bending lengths, which is just over 13 ft.
“When someone wants a specialty trailer with the long channels, they can now use the capacity of the tandem press brake,” Zellmann said.
In another example, a European fabricator of building components needed something to form long channels for structural support applications. It needed a bed of at least 12 m, which is just over 39 ft., and forming capacity of at least 400 tons.
Ronald Mille, sales manager, SafanDarley B.V., said that a single machine with a bed that long and capable of delivering 400 tons in forming pressure probably made the most sense—if someone wasn’t familiar with the actual facility in which the equipment was needed. In this case, the fabricator of building components was operating in a building with low ceilings (see Figure 2), and a 400-ton brake with a 12-m bed would have been too large to fit the space. The tandem brake setup, however, had a much lower profile and fit just under the company’s overhead crane.
Mille added that tandem press brakes come with the added benefit of not having to build a special foundation that normally is required to support single high-tonnage brakes with wide beds. That is a cost savings that might be easy to overlook when it comes time to decide between a large press brake or a tandem brake setup.
Tandem press brakes also offer up a couple of other benefits for metal fabricators:
- The tandem setup always offers redundancy for bending smaller parts, which can come in handy if one of the brakes is down for maintenance.
- These smaller-sized brakes have bending cycles that are much faster than those associated with large machines. As a result, these larger single-unit press brakes don’t produce parts as efficiently as the tandem arrangements.
Tandem Press Brake Complexity
In today’s modern fab shop, a lot of bending programming is done offline in the name of efficiency. With jobs being created in the front office away from the press brakes, technicians can focus on forming parts, not spending time working the control.
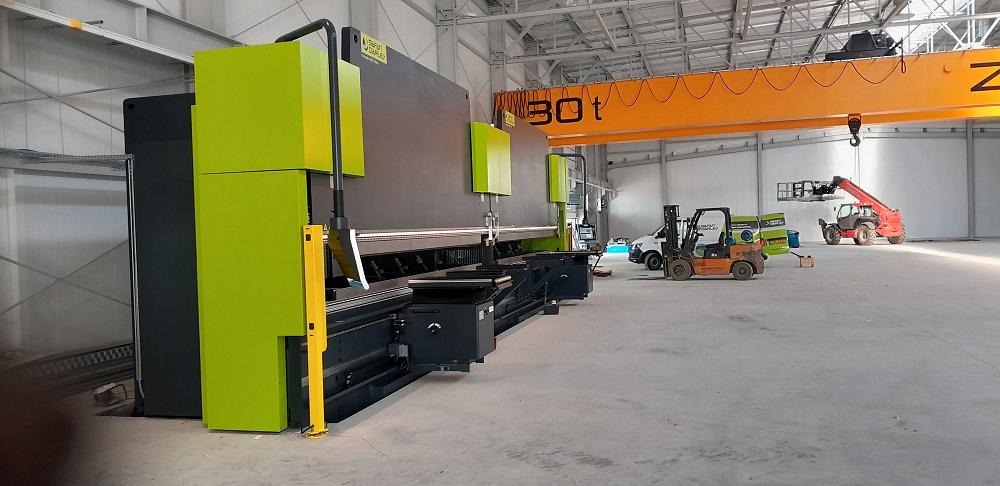
FIGURE 2. Flexibility in bending equipment isn’t the only reason that a fab shop might invest in a tandem press brake setup. Sometimes a tandem press brake is literally just the right fit. In this installation, two 400-ton, 6-m press brakes are joined in tandem mode to form long C-channel forms for a building application. A single 12-m machine would not have worked in this space because it would have been too tall, potentially colliding with the building’s crane.
In tandem press brakes, however, you need to be at the press bake control because you are no longer working with just one press brake. Things get a little more complicated.
“You don’t have a continuous bed or continuous crowning, and that’s very difficult. You are trying to sync four cylinders, not just two, and trying to get the ram to act as one unit coming down, all while calculating the proper CNC crowning. That’s a hard thing to do,” Zellmann said.
In tandem mode, you have to look at the part and think of it as two halves. You create a program for one press brake and one half of the part and then duplicate that program over on the other press brake.
“Normally with a press brake, you have the two cylinders and you bend the part in the middle. If you go into tandem mode, the focus shifts out of the middle [of the individual brakes],” Mille said.
The program has to ensure that the press brake cylinders aren’t driving the calculated force in the middle of the brake but distribute that bending power across the entire length of the workpiece, which sits across the two brakes. Any deviation in bending power on one press brake in a tandem setup adversely affects the other press brake, leading to potential performance issues and poorly formed parts.
Mille said that if precision bending is the goal, a single press brake probably is the best call because these units have automated crowning systems that help to compensate for the deflection that inherently occurs in the ram as it drives into the workpiece to create the form. Without deflection compensation, it’s likely that a workpiece demonstrates some sort of deformation at its center. This is especially true when forming long parts.
In a tandem press brake, the control system synchronizes the machine cylinders in regular split-second intervals to ensure that the ram is delivering straight-line movement as the tooling drives into the workpiece. To produce the same high-precision parts as on a stand-alone brake, more adjustments and corrections must be made with a tandem setup.
When discussing tandem press brakes, a lot of focus is naturally on part length. However, the width has to be taken into consideration because tandem press brakes have to cope with the presence of two uprights in the middle of bending window. After all, we’re still talking about two press brakes with two uprights smack dab in the way.
With that in mind, the width of the final formed part has to fit within the depth provided by the two C-frame uprights. Most press brake OEMs can offer some custom dimensions, but metal fabricators need to have a really good idea of what types of parts are destined for the tandem press brake before making such a large investment.
The Need for Some Bending Expertise
“It’s not your everyday fab shop that’s buying a tandem press brake, because it’s very application-based, but generally when this happens, you’re working with somebody who understands what they’re trying to fabricate,” Zellmann said.
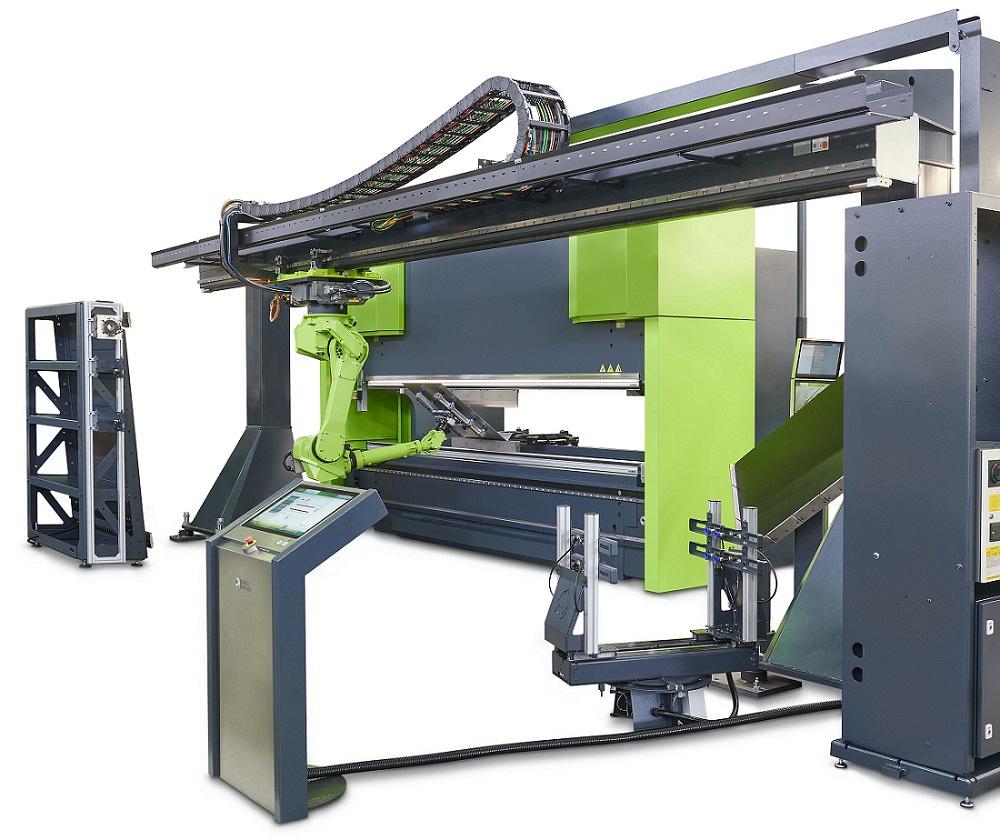
FIGURE 3. Robotic arms in tandem press brake scenarios are a possibility. With an overhead gantry design, the robot could move quickly down the length of a tandem setup.
So the control software does help, but a shop obviously wants someone with some press brake experience to stay on top of the entire bending sequence. That not only avoids the risk of poor part quality, but also damage to the brakes, tooling, and possibly the workpiece.
From a safety perspective, tandem brakes can be looked upon as being as safe as single units, according to Mille. Laser-based light guards are typically found on both press brakes, and if the fingers are in the way as the tooling is about to engage the workpiece, the light guards are tripped, shutting the press brake down and stopping the downward progression of the ram.
“Each machine also comes with its own foot pedals,” Mille said. “You have one for the left machine and one for the right machine. When one operator pushes the foot pedal, the other operator also has to push the pedal within one or two seconds for the press to come down.”
If a metal fabricator wants to automate tandem press brake operation, that’s also a possibility, given advances in robotics and control software (see Figure 3). It’s not frequently done, Zellmann said, but it’s possible. If the gantry that allowed for robotic movement between press brakes remained independent of the machines, the robot then could move between the brakes and could be used also as a single robot-and-brake combination as well.
“It really could be almost any size,” Zellmann said.
One Final Note
While tandem press brakes are designed to operate as one press brake, they still remain two distinct machines. That’s important to remember because you don’t get double the tonnage when you get two similarly sized brakes operating in unison.
Those slightly familiar with the concept of tandem press brakes might think that two machines in tandem doubles the tonnage regardless of where the bend takes place. That’s not the case. A press brake can deliver the tonnage that it was designed to deliver, not more, even in a tandem setup. So, for example, that 230-ton press brake working in tandem with another 230-ton press brake is only going to deliver a maximum of 230 tons of forming force.
Tandem press brakes aren’t widely found in shops, but they serve vital roles for those metal fabricators with special applications. Perhaps they might one day fit a job for you.
About the Author
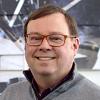
Dan Davis
2135 Point Blvd.
Elgin, IL 60123
815-227-8281
Dan Davis is editor-in-chief of The Fabricator, the industry's most widely circulated metal fabricating magazine, and its sister publications, The Tube & Pipe Journal and The Welder. He has been with the publications since April 2002.
Related Companies
subscribe now
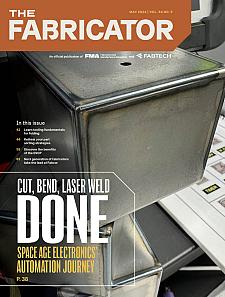
The Fabricator is North America's leading magazine for the metal forming and fabricating industry. The magazine delivers the news, technical articles, and case histories that enable fabricators to do their jobs more efficiently. The Fabricator has served the industry since 1970.
start your free subscription- Stay connected from anywhere
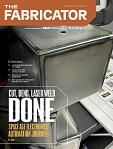
Easily access valuable industry resources now with full access to the digital edition of The Fabricator.
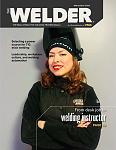
Easily access valuable industry resources now with full access to the digital edition of The Welder.
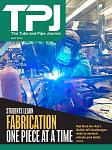
Easily access valuable industry resources now with full access to the digital edition of The Tube and Pipe Journal.
- Podcasting
- Podcast:
- The Fabricator Podcast
- Published:
- 04/16/2024
- Running Time:
- 63:29
In this episode of The Fabricator Podcast, Caleb Chamberlain, co-founder and CEO of OSH Cut, discusses his company’s...
- Industry Events
16th Annual Safety Conference
- April 30 - May 1, 2024
- Elgin,
Pipe and Tube Conference
- May 21 - 22, 2024
- Omaha, NE
World-Class Roll Forming Workshop
- June 5 - 6, 2024
- Louisville, KY
Advanced Laser Application Workshop
- June 25 - 27, 2024
- Novi, MI