Sales and Product Manager
- FMA
- The Fabricator
- FABTECH
- Canadian Metalworking
Categories
- Additive Manufacturing
- Aluminum Welding
- Arc Welding
- Assembly and Joining
- Automation and Robotics
- Bending and Forming
- Consumables
- Cutting and Weld Prep
- Electric Vehicles
- En Español
- Finishing
- Hydroforming
- Laser Cutting
- Laser Welding
- Machining
- Manufacturing Software
- Materials Handling
- Metals/Materials
- Oxyfuel Cutting
- Plasma Cutting
- Power Tools
- Punching and Other Holemaking
- Roll Forming
- Safety
- Sawing
- Shearing
- Shop Management
- Testing and Measuring
- Tube and Pipe Fabrication
- Tube and Pipe Production
- Waterjet Cutting
Industry Directory
Webcasts
Podcasts
FAB 40
Advertise
Subscribe
Account Login
Search
At WITS end with wrinkles, tears, springback in AHSS?
Servo’s position, velocity, force control can ease forming challenges
- By Darrell Quander Jr., George Schreck, and Jim Landowski
- January 26, 2016
- Article
- Bending and Forming

As pressure to reduce vehicular weight increases, the inclusion of high-strength metals also increases, along with forming challenges. Image courtesy of the Steel Market Development Institute, sponsor of the Great Designs in Steel conference, and Honda Motor Co.
Editor’s Note: This article was extracted from the authors’ co-presentation during a stamping educational track at FABTECH® 2015, Chicago, and the Great Designs in Steel conference, 2015, Livonia, Mich.
Today’s emphasis on manufacturing lighter yet safer vehicles has led to the use of new advanced high-strength steels (AHSS) to meet both emissions and safety regulations. Doing so has created forming challenges, however. Problems exist in the entire spectrum of the supply chain, including steel mills, tool and die shops, and stamping plants.
Typically, forming problems occur during new material tryouts or stem from incorrect tonnage or lack of force control throughout the stroke of a draw. These problems typically cause inconsistent part quality and longer production and setup times. Particularly frustrating are the wrinkling, tearing, and ruthless springback that occur during AHSS forming and increased maintenance costs caused by press wear.
Servo technology—both in the press and cushion—brings controllability to meet all these challenges head-on. Its ability to control position, velocity, and force independently of both the press slide and the cushion pressure pad—working as “partners”—can help stampers overcome those forming challenges and allow for the most controllability possible in the process.
With servo technology, a press is no longer a hammer beating a piece of iron; with the addition of a servo cushion, it’s part of an integrated forming system.
Forming Control Tames Wrinkles, Tears, Springback
The programmable resistive force capabilities of servo technology allow stampers to program multiple points of control, or zones, within the cushion stroke path as many times needed.
By varying the cushion pressure pad’s resistive capabilities—aggressive resistive force in some areas with passive resistive force in others—formability can be improved (see Figure 1).
At a certain cushion stroke position, an operator might set the resistive cushion force at 100 tons,
then at 80 tons, then back up to 120 tons during the course of one stroke—whatever combination is needed to produce optimal results to fend off tearing and wrinkling. A stamper can stop the slide motion at the point of material contact, then go slowly through the forming portion of the press stroke without the loss of system energy, allowing the material to flow. The operator can adjust the force of the servo cushion in strategic positions, such as high cushion force at the top of the stroke and lower force at bottom dead center (BDC).
With servo technology, an operator can dwell the press slide motion. What if he or she could then dwell at tonnage for a quarter of a second at BDC to let the material lose its memory before pulling back? This dwell capability is key for countering springback.
In addition, a progressive stroke really helps improve formability in draw work. For example, the ram can go down a little, let the material flow, go down a little more, let the material flow, repeatedly. The servo press can slow down throughout the draw and then speed back up. This capability enables a stamper to minimize or eliminate tears and reduce springback without running the part in three separate stations, as might be required in a flywheel mechanical press.
Servo press technology’s controllable ram velocity enables stampers to reduce frictional heat—the result of lost energy. A part gets hot primarily when the press runs too fast or has too much tonnage in the cushion. Because a flywheel mechanical press cannot change speeds and its cushion cannot change force, in certain areas of the part profile where the speed was too high or force was excessive, that excess energy converts into heat.
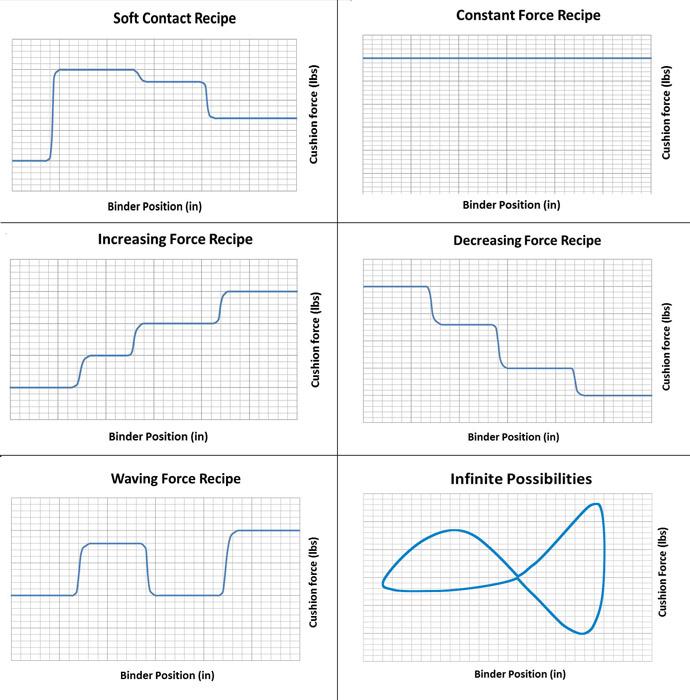
Figure 1
Servo technology allows stampers to change force profiles on-the-fly, which enhances the
ability to apply more or less pressure at different stages of the part formation. This can ease
problems with wrinkling, tearing, and springback.
Programming varying slide velocity in different regions of the part and slowing velocity at key spots can dissipate heat, helping to prevent wrinkling and tearing. Reducing heat reduces the rippling, bubbling, and thickness variations as well. Often, parts can exit cool to the touch with a less expensive water-based lubricant, or even without the use of any die lubricant at all.
A stamper can use the servo press’s ability to reverse the stroke motion direction by stopping at or going through BDC, then reversing and returning to BDC multiple times—pendulum mode—to perform rehits in the same stroke. Therefore, the part does not need to run through a secondary operation.
In addition, programmable slide velocity can reduce the reverse shock at fracture during blanking operations. Stampers can program the force based on the slide’s position so that the cushion “catches” the load at the point of snap-through. Because they can slow the slide velocity without losing energy, they can slow down the ram higher in the motion path than with eccentric motion. As a result, the material is severed more by shear than fracture, which is better.
Servo Cushion
So what does a servo cushion do? Just like a servo press, it has an adjustable and programmable force profile (see Figure 2). The servo cushion can deliver exactly the right amount of force needed at any point throughout the stroke.
The key is to have an integrated system that allows the force in the cushion to react to the progressive stroke. Integrating the servo cushion with a press provides the most overall control, including how the cushion interacts with the press.
A servo cushion and press work together so one isn’t slowing the other down. A servo cushion can work with the press, reducing press and tooling wear.
For example, a servo cushion allows stampers to control the cushion force, effectively creating a “soft hit.” Using the pre-acceleration function, the operator can program the cushion to start to descend before the ram descends, effectively giving it a head start to soften the blow of the initial contact and draw a better part. The press also can slow down or dwell to make contact with the cushion, countering the reverse shock inherent with a flywheel press. The cushion return stroke can be delayed at BDC, like a cushion lock option, and then the servo cushion can be programmed to smoothly return to the top of its stroke.
Programmable force is the key with the servo cushion—being able to make a change on-the-fly and having the force that can aso change on-the-fly throughout the stroke.
Yet to Be Discovered
Although servo technology is not new, it is still in its early stages, and a lot of cool ideas, approaches, and uses are being uncovered as it matures.
Stampers now can integrate secondary operations such as welding, drilling, machining, fastener insertions, laminations, and bonding into servo machines—operations that formerly could not be done.
The full book has not yet been written for this technology. A person can’t go into the archives of history like he or she can with flywheel machines. As new materials are developed—alloy steels, new aluminums, heated materials—it’s unknown how else servo technology can be applied to resolve new forming problems and to make process improvements.
About the Authors
Darrell Quander Jr.
10367 Brecksville Road
Brecksville, OH 44141
George Schreck
Product Manager
1701 Golf Rd.
Rolling Meadows, IL 60008
630-842-8189
Jim Landowski
Vice President
1701 Golf Road
Rolling Meadows, IL 60008
847-437-3750
subscribe now
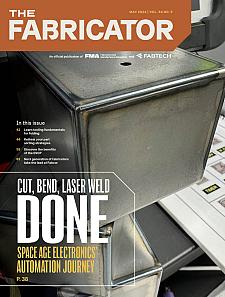
The Fabricator is North America's leading magazine for the metal forming and fabricating industry. The magazine delivers the news, technical articles, and case histories that enable fabricators to do their jobs more efficiently. The Fabricator has served the industry since 1970.
start your free subscription- Stay connected from anywhere
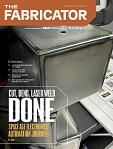
Easily access valuable industry resources now with full access to the digital edition of The Fabricator.
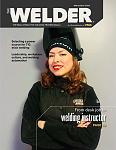
Easily access valuable industry resources now with full access to the digital edition of The Welder.
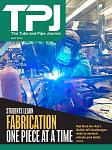
Easily access valuable industry resources now with full access to the digital edition of The Tube and Pipe Journal.
- Podcasting
- Podcast:
- The Fabricator Podcast
- Published:
- 04/16/2024
- Running Time:
- 63:29
In this episode of The Fabricator Podcast, Caleb Chamberlain, co-founder and CEO of OSH Cut, discusses his company’s...
- Trending Articles
Tips for creating sheet metal tubes with perforations
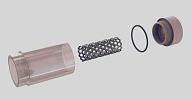
JM Steel triples capacity for solar energy projects at Pennsylvania facility
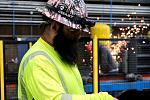
Are two heads better than one in fiber laser cutting?
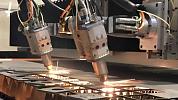
Supporting the metal fabricating industry through FMA
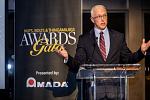
Omco Solar opens second Alabama manufacturing facility
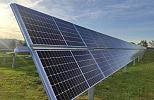
- Industry Events
16th Annual Safety Conference
- April 30 - May 1, 2024
- Elgin,
Pipe and Tube Conference
- May 21 - 22, 2024
- Omaha, NE
World-Class Roll Forming Workshop
- June 5 - 6, 2024
- Louisville, KY
Advanced Laser Application Workshop
- June 25 - 27, 2024
- Novi, MI