Contributing Writer
- FMA
- The Fabricator
- FABTECH
- Canadian Metalworking
Categories
- Additive Manufacturing
- Aluminum Welding
- Arc Welding
- Assembly and Joining
- Automation and Robotics
- Bending and Forming
- Consumables
- Cutting and Weld Prep
- Electric Vehicles
- En Español
- Finishing
- Hydroforming
- Laser Cutting
- Laser Welding
- Machining
- Manufacturing Software
- Materials Handling
- Metals/Materials
- Oxyfuel Cutting
- Plasma Cutting
- Power Tools
- Punching and Other Holemaking
- Roll Forming
- Safety
- Sawing
- Shearing
- Shop Management
- Testing and Measuring
- Tube and Pipe Fabrication
- Tube and Pipe Production
- Waterjet Cutting
Industry Directory
Webcasts
Podcasts
FAB 40
Advertise
Subscribe
Account Login
Search
Die Science: 6 questions to answer to achieve successful deep drawing
Part I: Material behavior, press selection
- By Art Hedrick
- July 4, 2017
- Article
- Bending and Forming
1. What Is Deep Drawing? How is it Different From Stretching?
Drawing is a process in which a metal product is shaped by controlled inward flow of the metal over a punch an into a cavity. In deep drawing, the total height of the part exceeds its minimum part width. Long, tubular parts often are made using this process.Frequently deep drawing requires more than one operation. The secondary operation are referred to as draw reductions or redraws (see Figure 1 ).
In deep drawing, the original blank must change its perimeter dimensions. As metal flows during drawing, it may get thicker.
Note that stretching and drawing are not the same. While drawing displaces surface area through plastic flow, stretching increases the surface area via tension. Although some stretching occurs during the drawing process, the process should be engineered so that the amount of stretching is limited. Metal is at greater risk of failing during stretching than during drawing.2. How Well Do I Know My Material?
Thousands of different types of ferrous an nonferrous metals are available in sheet form today. Although not all are suitable, many of them can be deep drawn (see Figure 2 ).
Each type of metal has its own special behavior characteristics, and to form a material successfully, you need to take the time to determine its tensile and yield strength, elongation percentage, and average n and r values. Find out if the metal is coated or pre-painted. If it is a nonferrous metal, find out if it is full hard, dead soft, or half hard. What is it drawing quality? Is it a speciality advanced high-strength steel such as dual-or trip-phase?
Knowing the material type will help you choose a suitable tool steel to cut and form it. Knowing you metal’s characteristics also will help you to determine if you need to anneal the parts between forming operations.
Annealing is a heat-treating process that returns the metal to it original properties after being cold-worked. Superalloys often require annealing between drawing operations, which explains why aircraft and medical parts typically are so expensive: They often are designed wit tight geometric tolerances and require more steps, including annealing, to manufacture. In contrast, materials such as low-carbon extra-deep-drawn-quality steel can be drawn up to 12 times before annealing becomes necessary.
If your material is high strength, you might need to add extra stations to compensate for springback. The material strength also affects your lubricant choice. Drawing high-strength steel into a given geometry usually requires a different lubricant than drawing the same geometry out of low-strength steel, because higher-strength steels require more force and energy to form. Higher forming forces result in more friction between the tool steel and the metal being formed, which generates more heat.
Most lubricants contain additives that react to heat and reduce the friction. If the heat being generated is insufficient or excessive, the additive will likely fail to reduce the friction sufficiently.
Avoid building common tools that are designed to form a variety of different metals without changing the die.
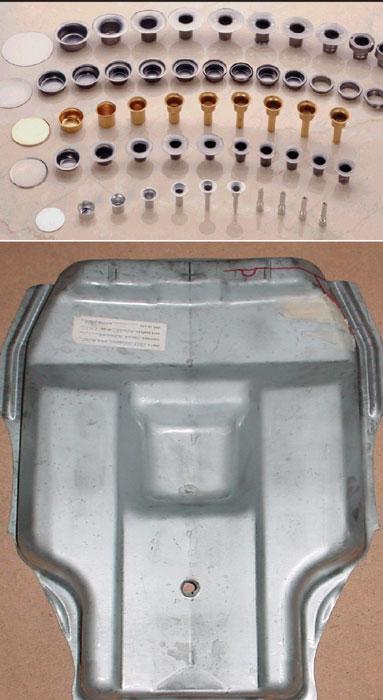
Figure 1
Deep-drawn parts require several draw
reductions (top) as opposed to a single
drawing die (bottom). Top photo courtesy
of Prospect Machine Products Inc.,
Prospect, Conn. Bottom photo courtesy of
Greenville Tool & Die, Greenville, Mich.
Also pay close attention to the material’s thickness. Thicker metal because there is more metal to stretch. Nothing is more difficult to stretch or draw than thin, high-strength metal because of buckling and wrinkling.
Whenever possible, avoid trying to draw materials that are extremely hard with poor stretchability. They might require additional heat to be formed.
3. Am I Using the Right Press?
Keep in mind that the press you select for deep drawing not only use have the force necessary to deform it too but it must not try to deform it too quickly. Think of your metal as being like Silly Putty®— if you pull it apart very quickly, it will snap and break, but if you stretch it slowly, you can stretch it a great deal without breaking it.
Hydraulic and servo-drive presses are suitable for deep drawing because they can be adjusted not to exceed the maximum forming speed for the metal. In addition, hydraulic presses have their full rated tonnage throughout the entire press stoke, whereas crank-drive presses often lose tonnage off the bottom of the press stroke. Eyelet presses or special cam/shaft drive transfer presses also are good for deep drawing.
Part II, which will discuss the limiting draw ratio, metal flow patterns, and draw radii.
Until next time… Best of Luck!
About the Author
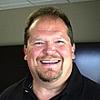
Art Hedrick
10855 Simpson Drive West Private
Greenville, MI 48838
616-894-6855
Related Companies
subscribe now
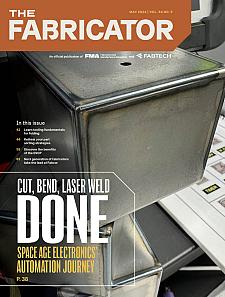
The Fabricator is North America's leading magazine for the metal forming and fabricating industry. The magazine delivers the news, technical articles, and case histories that enable fabricators to do their jobs more efficiently. The Fabricator has served the industry since 1970.
start your free subscription- Stay connected from anywhere
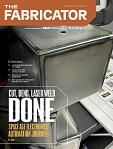
Easily access valuable industry resources now with full access to the digital edition of The Fabricator.
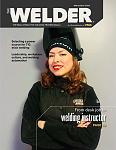
Easily access valuable industry resources now with full access to the digital edition of The Welder.
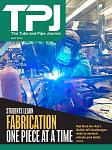
Easily access valuable industry resources now with full access to the digital edition of The Tube and Pipe Journal.
- Podcasting
- Podcast:
- The Fabricator Podcast
- Published:
- 04/16/2024
- Running Time:
- 63:29
In this episode of The Fabricator Podcast, Caleb Chamberlain, co-founder and CEO of OSH Cut, discusses his company’s...
- Trending Articles
Tips for creating sheet metal tubes with perforations
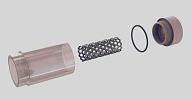
Supporting the metal fabricating industry through FMA
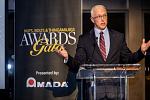
JM Steel triples capacity for solar energy projects at Pennsylvania facility
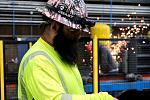
Fabricating favorite childhood memories
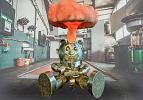
Omco Solar opens second Alabama manufacturing facility
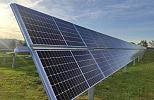
- Industry Events
16th Annual Safety Conference
- April 30 - May 1, 2024
- Elgin,
Pipe and Tube Conference
- May 21 - 22, 2024
- Omaha, NE
World-Class Roll Forming Workshop
- June 5 - 6, 2024
- Louisville, KY
Advanced Laser Application Workshop
- June 25 - 27, 2024
- Novi, MI