Contributing Writer
- FMA
- The Fabricator
- FABTECH
- Canadian Metalworking
Categories
- Additive Manufacturing
- Aluminum Welding
- Arc Welding
- Assembly and Joining
- Automation and Robotics
- Bending and Forming
- Consumables
- Cutting and Weld Prep
- Electric Vehicles
- En Español
- Finishing
- Hydroforming
- Laser Cutting
- Laser Welding
- Machining
- Manufacturing Software
- Materials Handling
- Metals/Materials
- Oxyfuel Cutting
- Plasma Cutting
- Power Tools
- Punching and Other Holemaking
- Roll Forming
- Safety
- Sawing
- Shearing
- Shop Management
- Testing and Measuring
- Tube and Pipe Fabrication
- Tube and Pipe Production
- Waterjet Cutting
Industry Directory
Webcasts
Podcasts
FAB 40
Advertise
Subscribe
Account Login
Search
Die Science: 7 ways that part material affects die design and the forming process
- By Art Hedrick
- March 16, 2017
- Article
- Bending and Forming
I recently had an opportunity to train some young product designers. During this training session, one of the product designers brought me a print of a project he was working on. It was a contoured, deep-drawn part with many intricate features, and he had a lot of questions about the manufacturability of the design.
The title block of the print listed a long number. It was a typical automotive specification that indicated 1.5-millimeter, DP600 material was to be used to make the part. I asked the designer to tell me what the material was. He said, “Some kind of steel.” When I asked if he could give me more detail about the material, he admitted that he knew very little about it—just that his supervisor wanted him to use it for the part.
It’s All About the Material
I explained that he was inadvertently and unknowingly making all sorts of decisions about his part forming process, because material choice determines multiple aspects of part production:
1. Part manufacturability. All metals have a certain amount of ductility, stretchability, and malleability that makes them more or less suitable for deep forming. For example, designing a multiple-step, deep-drawn part to be made out of DP980 would defy the metal’s physical capabilities and likely cause part failure. Designing the same part out of a low-carbon, deep-drawing steel would be a much better choice.
2. Tool steel type
. Parts made out of abrasive materials—such as high-strength steel; spring steel; stronger-grade high-strength, low-alloy steel; or superalloys such as INCONEL®will require tools made of premium grades of tool steel or solid carbide. Of course, this affects the tooling cost significantly.3. Die coating type.
Depending on the metal being formed, the die might have to be coated with special antifriction, high-wear surface coatings such as titanium carbide or specialized duplex coatings.4. Press capacity.
High-strength steel takes more tonnage to form and cut than lower-strength steel. Although the product designer might not select the actual press the part will be run on, his or her decisions certainly are going to affect the amount of tonnage and type of drive needed. In addition, some materials are very strain rate-sensitive or sensitive to forming speeds, so they lend themselves to a slower-speed press.5. Die component thickness and geometry.
High-strength materials require greater forces to cut and form. Therefore, the tool steel sections must be thicker and more rigid than the sections used for forming low-strength mild steel.6. Lubricant chemistry.
High-strength materials generate a lot of heat when being formed and cut. For this reason, additives such as chlorine, sulfur, fats, waxes, and oils often are added to the lubricant to help reduce friction and reduce the amount of heat. Some of these additives must be removed from the formed part before painting, which adds expense to the manufacturing process.7. Number of stations.
High-strength materials most likely will require more stations to make the part geometry than their low-strength counterparts. Higher-strength metal bottles, for instance, probably will require secondary restrike or requalifying stations to compensate for the material’s extensive amount of springback.A Few Final Tips
Every feature and every tolerance that a product designer assigns to a part has a certain cost associated with it. Sometimes, reducing the geometric dimensioning and tolerancing on a part can double or even triple the tooling and manufacturing cost. Choosing to make a part out of high-strength material can have a similar effect.
Make sure you fully understand how the material from which you are designing a part will affect the entire process. Avoid overdesigning your part with features and tolerances the aren’t absolutely necessary. Choose a metal that suits the fit and function of your part.
Take the time to learn about the metals you’re using in your product designs. It will pay off in the long run.
About the Author
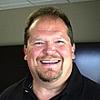
Art Hedrick
10855 Simpson Drive West Private
Greenville, MI 48838
616-894-6855
Related Companies
subscribe now
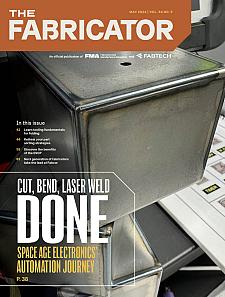
The Fabricator is North America's leading magazine for the metal forming and fabricating industry. The magazine delivers the news, technical articles, and case histories that enable fabricators to do their jobs more efficiently. The Fabricator has served the industry since 1970.
start your free subscription- Stay connected from anywhere
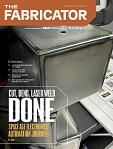
Easily access valuable industry resources now with full access to the digital edition of The Fabricator.
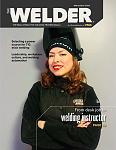
Easily access valuable industry resources now with full access to the digital edition of The Welder.
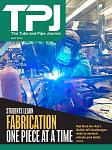
Easily access valuable industry resources now with full access to the digital edition of The Tube and Pipe Journal.
- Podcasting
- Podcast:
- The Fabricator Podcast
- Published:
- 04/30/2024
- Running Time:
- 53:00
Seth Feldman of Iowa-based Wertzbaugher Services joins The Fabricator Podcast to offer his take as a Gen Zer...
- Industry Events
Pipe and Tube Conference
- May 21 - 22, 2024
- Omaha, NE
World-Class Roll Forming Workshop
- June 5 - 6, 2024
- Louisville, KY
Advanced Laser Application Workshop
- June 25 - 27, 2024
- Novi, MI
Precision Press Brake Certificate Course
- July 31 - August 1, 2024
- Elgin,