Contributing Writer
- FMA
- The Fabricator
- FABTECH
- Canadian Metalworking
Categories
- Additive Manufacturing
- Aluminum Welding
- Arc Welding
- Assembly and Joining
- Automation and Robotics
- Bending and Forming
- Consumables
- Cutting and Weld Prep
- Electric Vehicles
- En Español
- Finishing
- Hydroforming
- Laser Cutting
- Laser Welding
- Machining
- Manufacturing Software
- Materials Handling
- Metals/Materials
- Oxyfuel Cutting
- Plasma Cutting
- Power Tools
- Punching and Other Holemaking
- Roll Forming
- Safety
- Sawing
- Shearing
- Shop Management
- Testing and Measuring
- Tube and Pipe Fabrication
- Tube and Pipe Production
- Waterjet Cutting
Industry Directory
Webcasts
Podcasts
FAB 40
Advertise
Subscribe
Account Login
Search
Die Science: Drawing under pressure
How the draw pad affects results
- By Art Hedrick
- July 11, 2017
- Article
- Bending and Forming
On my list of pet peeves are die shops and stampers that use only draw pad pressure—also known as blank holder pressure —to control metal flow. If the part wrinkles, they increase the draw pad pressure; if the part splits, they reduce the draw pad pressure. They find themselves changing the pressure form shift to shift and day to day. While this method can offer limited success, problems with inconsistent parts may result.
The key to any successful metal drawing or stretching operation is the ability to control metal flow consistently .
Numerous factors determine how much stretch and flow take place during a metal forming process; the mechanical properties of the metal being formed, the geometry of the part being produced, and friction are just a few. However, in this article I will focus on controlling metal flow through the use of the forming die’s draw pad.
Many studies have been published about the depth of draw that can be achieved with respect to the draw pad pressure. But no all-drawing operation should use draw pad pressure to control the metal’s flow. In fact, whenever feasible or practical, draw pad pressure should not be used.
Draw Pad Basics
The draw pad typically is a thick, hardened tool steel ring, either flat or contoured, that surrounds the draw punch and controls the inward flow of metal. It usually is pressure-loaded, meaning that it sits on top of a pressure system such as coil, urethane, or gas springs.
The draw pad also can get its necessary force from an external source, such as a press cushion. This plate is mounted underneath the bolster of the press and moves vertically, typically activated by air or hydraulics.
On some newer presses, the press cushion is servo-driven and can be programmed to apply different points during the stroke of the press. These types of cushions are effective, especially when you are attempting to make a part geometry that requires a great deal of holding pressure followed by a big reduction in draw pad force.
Most press cushions use cushion pins to transfer the force to the bottom side of the blank holder. Special units, such as electronic shimming systems, use individual hydraulic cylinders to provide the necessary force (see Figure 1 ). They allow the force to be changed in different areas around the punch during the forming process.
Control and Consistency
If your goal i stop obtain extreme consistency, avoid using draw pad pressure to control metal flow. Despite very popular misconceptions, the true function of a draw pad is not to squeeze or pinch the metal and create a resistance to flow. The function of a draw pad is to keep the metal from wrinkling during the inward flow of the metal.
If you find yourself constantly changing the pressure in your system to try to combat splits and wrinkles, you’re most likely trying to control metal flow through pinching or not pinching the material. This method can result in great inconsistency in your parts.

Figure 1
Electronic shimming systems, often used in kitchen sink manufacturing, allow force to be
changed in different areas around the punch during the forming process. Courtesy of
Hydraulico Press Technologies and Kovinoplastika.
I am in no way saying that draw pad pressure cannot be used to create a restrictive force. I am saying that achieving consistency will be more difficult.
Unless you have a special system, such as electronic shimming or a programmable servo-drive cushion, the draw pad pressure normally increases during the drawing and stretching process.
For example, the pressure exerted on the blank when using a stand-alone gas spring can double during the downstroke. This is a problem because the more pressure that is applied to the blank, the greater the friction. The greater the friction, the higher the temperature at the interface. As forming temperature increases in the die, the coefficient of friction also changes with respect to the additives in the lubricant.
The more you squeeze the metal, the more it affects friction. This means that when using draw pad pressure alone, you are relying solely on the frictional value created by an inconsistent pressure and the coefficient of friction created by the lubricant. Such factors as die temperature, lubricant viscosity, press deflection, forming speeds, metal surface topography, and lubricant application will likely have a significant impact on the success of your drawing process.
Also, keep in mind that as the metal flows inward, the draw ratio is changing. In simple terms, the amount of metal that is trapped between the die face and the draw pad is decreasing as metal flows inward. This essentially results in more pressure being concentrated on a smaller area of the blank during the drawing process.
Creating a Restrictive Force
Consider using draw or step beads to restrict and control metal flow. Think of draw beads as speed bumps for metal (see Figure 3 ). They create a restrictive force by bending and unbending the metal. The draw beads’ height and geometry control the restrictive force.
When to Use Draw Pad Pressure
There are certainly times when draw pad pressure must be used. For instance, with very large dies, because of their deflection rates, it is nearly impossible to prevent draw pad pressure and standoffs are used to control the metal flow.
The key is to try to avoid using draw pads as much as possible to control metal.
Until next time…Best of luck!
About the Author
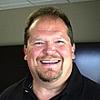
Art Hedrick
10855 Simpson Drive West Private
Greenville, MI 48838
616-894-6855
Related Companies
subscribe now
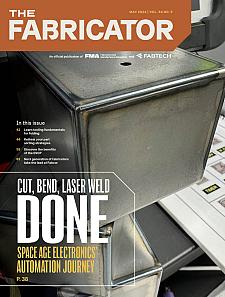
The Fabricator is North America's leading magazine for the metal forming and fabricating industry. The magazine delivers the news, technical articles, and case histories that enable fabricators to do their jobs more efficiently. The Fabricator has served the industry since 1970.
start your free subscription- Stay connected from anywhere
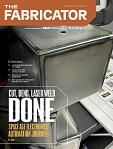
Easily access valuable industry resources now with full access to the digital edition of The Fabricator.
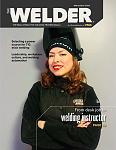
Easily access valuable industry resources now with full access to the digital edition of The Welder.
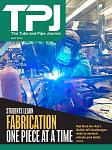
Easily access valuable industry resources now with full access to the digital edition of The Tube and Pipe Journal.
- Podcasting
- Podcast:
- The Fabricator Podcast
- Published:
- 04/30/2024
- Running Time:
- 53:00
Seth Feldman of Iowa-based Wertzbaugher Services joins The Fabricator Podcast to offer his take as a Gen Zer...
- Industry Events
16th Annual Safety Conference
- April 30 - May 1, 2024
- Elgin,
Pipe and Tube Conference
- May 21 - 22, 2024
- Omaha, NE
World-Class Roll Forming Workshop
- June 5 - 6, 2024
- Louisville, KY
Advanced Laser Application Workshop
- June 25 - 27, 2024
- Novi, MI