Contributing Writer
- FMA
- The Fabricator
- FABTECH
- Canadian Metalworking
Categories
- Additive Manufacturing
- Aluminum Welding
- Arc Welding
- Assembly and Joining
- Automation and Robotics
- Bending and Forming
- Consumables
- Cutting and Weld Prep
- Electric Vehicles
- En Español
- Finishing
- Hydroforming
- Laser Cutting
- Laser Welding
- Machining
- Manufacturing Software
- Materials Handling
- Metals/Materials
- Oxyfuel Cutting
- Plasma Cutting
- Power Tools
- Punching and Other Holemaking
- Roll Forming
- Safety
- Sawing
- Shearing
- Shop Management
- Testing and Measuring
- Tube and Pipe Fabrication
- Tube and Pipe Production
- Waterjet Cutting
Industry Directory
Webcasts
Podcasts
FAB 40
Advertise
Subscribe
Account Login
Search
Die Science: Forming simulation software
Almost perfect
- By Art Hedrick
- June 29, 2017
- Article
- Bending and Forming
Of all the advancements in stamping over the last 20 years, the invention and use of forming simulation undoubtedly has had one of the greatest impacts on the way we design and engineer stamped parts and dies.
When it was first introduced, you needed a computer that mimicked something from NASA—and a Ph.D. computer scientist to run it. Today’s software is far more advanced, can be run on laptop, and can be operated by almost any person with experience in processing and forming sheet metal. With its ability to aid product design and feasibility, reduce die tryout time, reduce lead-times, and make the entire building process less frustrating, forming simulation has helped to revolutionize the stamping industry.
I am a very strong advocate for the use of forming simulation. For the most part, it does almost everything it says it can do, and I strongly believe that the results of performing a formability study can lead you to forming success.
Notice that I said lead you to a success. Just because the part was formed successfully in a virtual world doesn’t guarantee that you will get those exact results when you build the tool. Sometimes the end result might not exactly match the forming simulation results.
Why does’t the part coming out of the tool always match those results? Th problem isn’t with the forming simulation. The simulation is perfect: Based on the data that has been input into the computer and the mathematical data that the computer is using, the results will be accurate. Computers don’t make mistakes.
Press Ram and Bolster Parallelism
During a forming simulation, the virtual ram and bolster plate of the press are perfectly parallel. During the forming process, they never go out of perfect parallelism, either—but your process does.
Ram and Bolster Deflection Rates
During virtual forming, the ram and the bolster of the press do not deflect; the virtual press does not bend twist, bow, or compress. But again, the press does.Press Speed
Virtual forming typically uses a constant forming speed. The speed of the actual metal forming process affects the amount of friction between the sheet metal and the die. That friction determines the amount of metal flow into the forming cavity and the amount of strain in the stamping. Strain levels and distribution parameters affect springbuck severity.To make a long story short, if you are using a crank or draw-link-drive press, your ram velocity is not a constant value and cannot replicate the simulation exactly.
Die Deflection
In forming simulation, the die does not deflect. The binder or blank holder doe not bend more in one area than another.In reality, draw pads, especially those that have a great deal of shape to them, will deflect during actual forming process. Deflection as small as 0.001 inch can make a substantial difference in the amount that metal flows and stretches.
Thermal Changes
The virtual forming process generates no heat. The virtual punch, binder, and captivity never change their temperature or size as a result of thermal expansion, and the die sections never gall.An actual metal forming process does generate heat, and that causes die sections to expand thermally, changing the clearances between the working components. In addition, different temperatures in the die affect the behavior of the metal.
Consider what happens to the ductility of a steel bar when you heat it to red-hot: It becomes much more malleable. While you might not think that red-hot temperatures happen in a drawing operation, I assure you they sometimes do. As evidence, consider adhesive galling, the welding of sheet metal to the die. Enough said. You get the idea.
Frictional Values
Success in a drawing or stretching operation relies heavily on the control of friction. Forming simulation doe account for friction, but not for the changes in friction during the forming process.Most lubricants used in stamping operations recta to heat. For example, when the forming temperature gets to about 250 degrees F, the coefficient of friction with a straight, chlorinated lubricant drops from 0.3 to 0.08. This is a triple reduction in friction (see Figure 1 ). Since the friction never changes in virtual forming, most people just use the default friction of 0.15 for all forming operations being simulated.
Not only is temperature a factor in friction, but so is the die surface quality. Those of you with a great deal of experience in drawing and stretching know the importance accurately completed, polished radius. And, unfortunately, forming simulation doesn’t know whether “Mach the Hack” or “Fine-finish Fred” will be working on the forming radii. It makes a big difference in the actual tool.
Die Fit
In a virtual simulation, all of the die surfaces fit perfectly, with nothing warped or twisted during the heating process. However, during the actual building process, the fit might be so-so. The die might also be draw spotted with respect to ever-changing metal thickness.How do your die sections fit? Not as well as they do in a simulation.
Sheet Material Specs
Was the virtual tryout performed using the average mechanical values of the materials? Were they at the high or low end of the spec? Although these differences may seem subtle, they can make a big difference in the outcome of the part.Know the Limitations, Understand the Variables
The key when using forming simulations is to know its limitations. I have no doubt that in the future, software might be able to account for many real-world variables. Until that happens, I strongly suggest you continue to use forming simulation, because the benefits outweigh the problems exponentially.The key to success, though, is to understand all of the variables in your process and make the best judgment you can with the knowledge base you have.
Until next time… Best of luck!About the Author
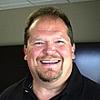
Art Hedrick
10855 Simpson Drive West Private
Greenville, MI 48838
616-894-6855
Related Companies
subscribe now
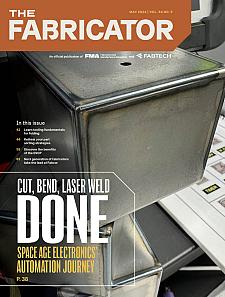
The Fabricator is North America's leading magazine for the metal forming and fabricating industry. The magazine delivers the news, technical articles, and case histories that enable fabricators to do their jobs more efficiently. The Fabricator has served the industry since 1970.
start your free subscription- Stay connected from anywhere
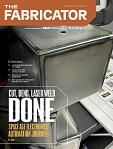
Easily access valuable industry resources now with full access to the digital edition of The Fabricator.
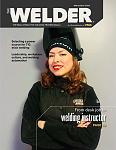
Easily access valuable industry resources now with full access to the digital edition of The Welder.
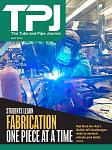
Easily access valuable industry resources now with full access to the digital edition of The Tube and Pipe Journal.
- Podcasting
- Podcast:
- The Fabricator Podcast
- Published:
- 04/30/2024
- Running Time:
- 53:00
Seth Feldman of Iowa-based Wertzbaugher Services joins The Fabricator Podcast to offer his take as a Gen Zer...
- Industry Events
Pipe and Tube Conference
- May 21 - 22, 2024
- Omaha, NE
World-Class Roll Forming Workshop
- June 5 - 6, 2024
- Louisville, KY
Advanced Laser Application Workshop
- June 25 - 27, 2024
- Novi, MI
Precision Press Brake Certificate Course
- July 31 - August 1, 2024
- Elgin,