Contributing Writer
- FMA
- The Fabricator
- FABTECH
- Canadian Metalworking
Categories
- Additive Manufacturing
- Aluminum Welding
- Arc Welding
- Assembly and Joining
- Automation and Robotics
- Bending and Forming
- Consumables
- Cutting and Weld Prep
- Electric Vehicles
- En Español
- Finishing
- Hydroforming
- Laser Cutting
- Laser Welding
- Machining
- Manufacturing Software
- Materials Handling
- Metals/Materials
- Oxyfuel Cutting
- Plasma Cutting
- Power Tools
- Punching and Other Holemaking
- Roll Forming
- Safety
- Sawing
- Shearing
- Shop Management
- Testing and Measuring
- Tube and Pipe Fabrication
- Tube and Pipe Production
- Waterjet Cutting
Industry Directory
Webcasts
Podcasts
FAB 40
Advertise
Subscribe
Account Login
Search
Die Science: Fundamentals of drawing
- By Art Hedrick
- June 8, 2016
- Article
- Bending and Forming
Once a week, it seems, I receive a print in my e-mail containing the following question: Can this part be made? In general, if the part has a great deal of contour or shape to it, a drawing operation will be required to make it.
Even though the term draw also can mean a method of deformation in which metal is both compressed and stretched simultaneously, draIwing is a loosely used term referring to an operation containing many different forms of metal deformation. In fact, certain types of draw dies produce parts that don’t have any draw deformation in them.
Drawing is advantageous compared to other forming operations in that it can form very tall, wrinkle-free, highly sculptured parts out of a large variety of both ferrous and nonferrous metals while maintaining a quality surface finish. Some typical parts made in draw dies are car doors; hoods; oil pans; oil cans; filters; and numerous components used in the automotive, appliance, construction, hardware, and medical fields.
Drawing Versus Casting
Drawing a part, as opposed to casting it, typically reduces part cost, improves production rates and part quality, and lowers overall production cost. As a result, a large percentage of parts previously made as castings have been converted to drawn stamped parts, and many product designers consider drawing to be an economically sound, viable option. In fact, part design is the main limiting factor that determines whether a part can be drawn or if it needs to be made in an alternative process.
Quite simply, if the design for a sheet metal stamped part dictates that the metal undergo stretch or compression or that it maintain a high-quality surface finish, drawing usually is the best process for the job.
Flow and Control
In drawing, not to be confused with stretching, the flow of flat sheet metal into a specific shape is controlled. In other words, the basic purpose of drawing is to create as much of the part shape as possible through the displacement of surface area.
The key words in the definition of drawing are flow and control.
Flow, in its simplest form, describes what the metal must do so it can restructure into a specific shape. Picture in your mind a large sheet of rubbery plastic being formed over a given shape, liquefying not under heat but under pressure. Steel and other ferrous and nonferrous metals react to forming in much the same manner.
Control of that flow—making it go where you want it to and not where you don’t—is one of the key principles of drawing operations. Control of the metal flow is what differentiates a drawing die from any other stamping die. The flow of the metal is controlled by a pressure-loaded plate called the drawing pad or binder, along with the pressure system underneath the pad, which comprises a series of gas springs, a manifold, or an alternate pressure system.
Deep Drawing
When drawing is used to form a part that is deeper than its minimum part width, the process is called deep drawing. An example of a typical deep-drawn part is an oil filter.
Successful deep drawing depends on many factors:
- Material type, thickness, and mechanical properties
- Blank size and shape
- Part geometry
- Press speed (ram speed)
- Draw radii
- Draw ratio
- Die surface finish
- Die temperature
- Lubricant
- Draw bead height and shape
- Binder pressure
- Binder deflection
- Standoff height
The material used in deep drawing must have the mechanical ability to take the part shape without rupturing. For this reason, you need to pay strict attention to the material type and thickness. Press speeds must allow time for materials to flow.
Die surface finishes and lubricants are important because they can reduce the coefficient of friction, allowing materials to slide through tools more easily. In most cases, the dies are polished to a mirror-like finish.
A draw bead is like a speed bump for the metal—it forces the metal to bend and unbend prior to flowing into the cavities and over the punch. Increasing binder or draw pad pressure will exert more force on the material, creating a restriction to flow. This helps reduce wrinkling and increase the amount of stretch occurring in the part.
The draw ratio—the relationship between the size of the draw punch and the blank—is among the most important elements to consider when attempting to deep draw a part. In fact, it is one of the main reasons that so many stations are required to make tall, small-diameter parts. If the blank is too far from the punch, the metal most likely will stretch and could fail. Reducing the blank size will cause the metal to flow.
About the Author
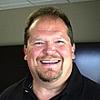
Art Hedrick
10855 Simpson Drive West Private
Greenville, MI 48838
616-894-6855
Related Companies
subscribe now
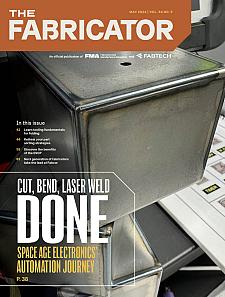
The Fabricator is North America's leading magazine for the metal forming and fabricating industry. The magazine delivers the news, technical articles, and case histories that enable fabricators to do their jobs more efficiently. The Fabricator has served the industry since 1970.
start your free subscription- Stay connected from anywhere
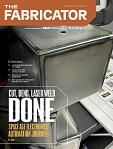
Easily access valuable industry resources now with full access to the digital edition of The Fabricator.
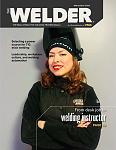
Easily access valuable industry resources now with full access to the digital edition of The Welder.
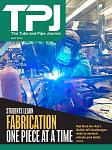
Easily access valuable industry resources now with full access to the digital edition of The Tube and Pipe Journal.
- Podcasting
- Podcast:
- The Fabricator Podcast
- Published:
- 04/30/2024
- Running Time:
- 53:00
Seth Feldman of Iowa-based Wertzbaugher Services joins The Fabricator Podcast to offer his take as a Gen Zer...
- Industry Events
Pipe and Tube Conference
- May 21 - 22, 2024
- Omaha, NE
World-Class Roll Forming Workshop
- June 5 - 6, 2024
- Louisville, KY
Advanced Laser Application Workshop
- June 25 - 27, 2024
- Novi, MI
Precision Press Brake Certificate Course
- July 31 - August 1, 2024
- Elgin,