Contributing Writer
- FMA
- The Fabricator
- FABTECH
- Canadian Metalworking
Categories
- Additive Manufacturing
- Aluminum Welding
- Arc Welding
- Assembly and Joining
- Automation and Robotics
- Bending and Forming
- Consumables
- Cutting and Weld Prep
- Electric Vehicles
- En Español
- Finishing
- Hydroforming
- Laser Cutting
- Laser Welding
- Machining
- Manufacturing Software
- Materials Handling
- Metals/Materials
- Oxyfuel Cutting
- Plasma Cutting
- Power Tools
- Punching and Other Holemaking
- Roll Forming
- Safety
- Sawing
- Shearing
- Shop Management
- Testing and Measuring
- Tube and Pipe Fabrication
- Tube and Pipe Production
- Waterjet Cutting
Industry Directory
Webcasts
Podcasts
FAB 40
Advertise
Subscribe
Account Login
Search
Die Science: Keys for drawing rectangular or square shells
- By Art Hedrick
- August 23, 2017
- Article
- Bending and Forming
First Things First
Before any processing takes place, you have to determine what the material is. Different materials have distinctly different behaviors that affect formability:
- Thickness—thicker metals stretch farther than thin metals of the same type.
- Tensile, yield, and elongation—These are the basic forming, rupture, and stretching abilities.
- Hardness— Many steel and nonferrous metals come in different hardness levels, such as quarter-hard, half-hard, three-quarter hard, and full-hard.
- Grade— Advanced high-strength steels (AHSS), such as dual-phrase, have unique behaviors that you must compensate for.
Metal Flow Basics
To understand the metal flow patterns in a square drawn shell, consider how a cylinder cup is drawn.
A cylinder starts out as a simple round blank. For the larger-diameter round blank to transform into the smaller cylinder shape, it must compress radially. In other words, the metal must flow inward toward the centerline of the cup simultaneously as it compresses together (see Figure 1 ).
Controlled compression results in a part with a flat flange. Uncontrolled compression causes a severely wrinkled flange (see Figure 2 ). The key point to remember is that metal in compression has a great resistance to flow.
Radial Compression in Square Draws
The corners of the square draw are essentially one-quarter of a round draw (see Figure 3 ). The radial compression that produces a round draw causes a resistance to flow in the corners of a square draw. This type of deformation is known as draw deformation, or compressing the metal as it flows inward intension.
If too much metal surface area is forced into radial compression, it will cause a great resistance to flow, resulting in excessive metal stretching and possible splitting. However, if the blank is close enough to the radial profile of the punch, the metal will compress and flow inward, resulting in less metal thinning. This basic relationship between the blank edge and the draw punch is called the limiting draw ratio (LDR).
Shell Side Walls
The side walls of a drawn box are in bend-and-straighten deformation. With little or no compression during this deformation mode, the metal flows inward with very little resistance. You can increase resistance by applying more blank holder force in this area or adding draw beads.
This type of deformation is known as plain strain, or simply stretching the metal in one direction. If too much metal flow in this area, it may cause the side walls of your part to be bowed outward.
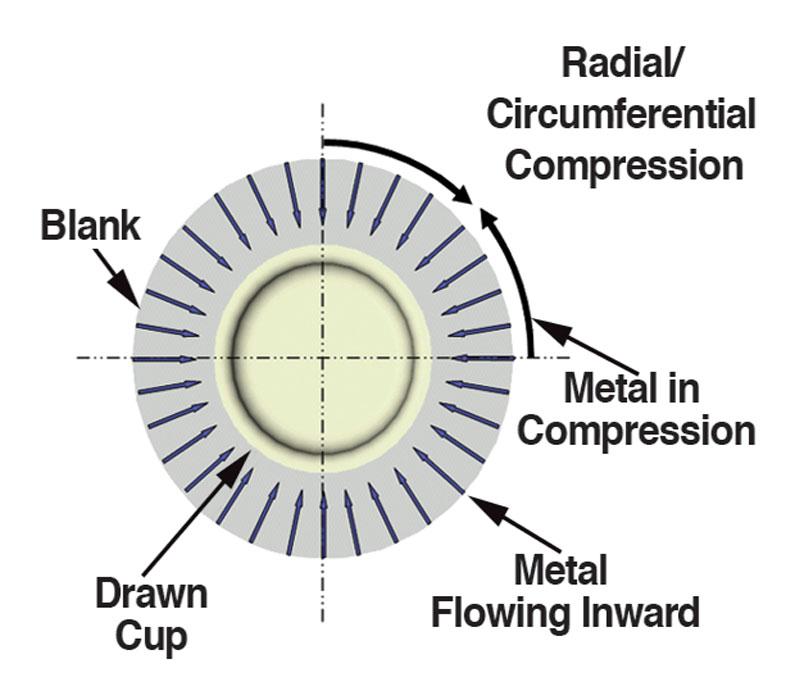
Figure 1
For a larger-diameter round blank to transform
into a smaller cylinder shape, it must
compress radially. The metal must flow
inward toward the centerline of the cup
simultaneously as it compresses together.
Surface Area Displacement for Compressive Deformation
During compressive deformation, the flat sheet metal’s surface area is displaced into a radial shape that must consume nearly equal amounts of surface area. In other words, if the metal flows inward in the corners of the draw 1 linear inch, the shell will get taller than 1 inch.
Consider that when producing a round drawn cup, the outer blank edge is a much larger diameter than the drawn cup. For the blank edge to become the edge of the finished cup, the surface area contained in the flat blank must be displaced into a smaller profile corner. The only way the smaller diameter can consume the surface area is to get taller (see Figure 4 ).
Blank Size and Shape
Whenever feasible, use the smallest blank possible to make the part.
The closer the blank is to the draw punch, the more the metal will flow. When using a square blank to make a square shell, consider nesting it 45 degrees in reference to blank. This puts greater resistance to flow in the side of the shell, where more tension is desired, and less material in the corners to help maximize flow in the radial profile.
Square Draw, Round Blank?
Yes.
In the side walls, there is very little resistance to flow; in the corners, resistance to flow is greater. Combining this factor with the draw-in-to-height ratio differences from the side wall to the corners results in a “roundish” blank (see Figure 5 ).
Draw Spotting
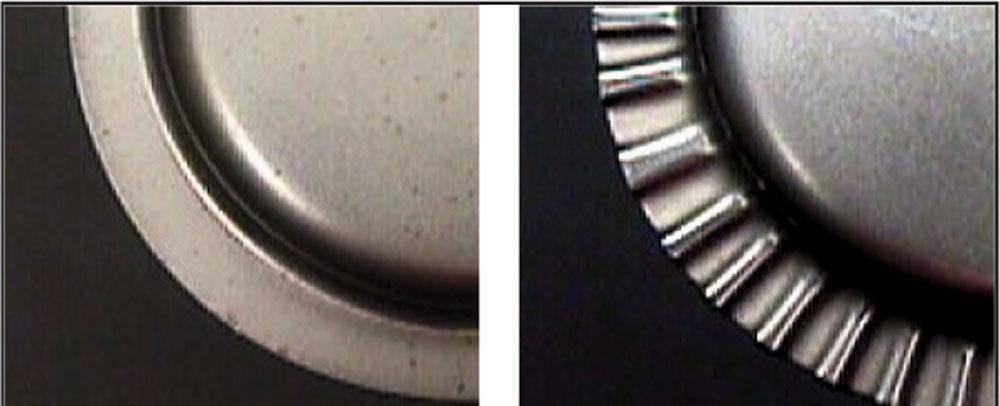
Figure 2
Controlled compression results in a part
with a flat flange. Uncontrolled compression
causes a severely wrinkled flange.
Often referred to as a running spot, the draw holder or die face with respect to the compressive thickening and tensile thinning that occurs during the drawing process.
In the corners of a draw, the metal will be in compression. Compressed metal trapped between the die face and a blank holder will thicken during the drawing process. Grinding the die face or blank holder with respect to compressive thickening and tensile thinning that occurs during the drawing process.
In the corners of a draw, the metal will be in compression. Compressed metal trapped between the die face and a blank holder will thicken during the drawing process. Grinding the die face or blank holder with respect to compressive thickening will help reproduce the resistance in the corners of the drawn shell.
The typical thought is that if a part is flat, a perfectly flat blank holder can be used. Flat blank holders are fine as long as they are draw spotted to metal flow conditions in a process known as tuning the blank holder.Figure 6 shows a hard mark, resulting from compressive thickening in the corners, that must be ground away by draw spotting.
These are just a few concepts and ideas that will help you to successfully draw a shell. Until next time… Best of luck!
About the Author
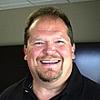
Art Hedrick
10855 Simpson Drive West Private
Greenville, MI 48838
616-894-6855
Related Companies
subscribe now
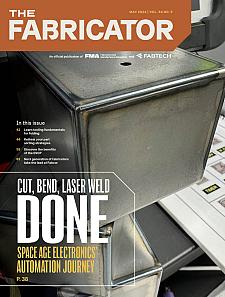
The Fabricator is North America's leading magazine for the metal forming and fabricating industry. The magazine delivers the news, technical articles, and case histories that enable fabricators to do their jobs more efficiently. The Fabricator has served the industry since 1970.
start your free subscription- Stay connected from anywhere
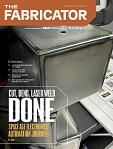
Easily access valuable industry resources now with full access to the digital edition of The Fabricator.
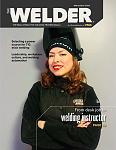
Easily access valuable industry resources now with full access to the digital edition of The Welder.
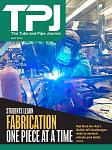
Easily access valuable industry resources now with full access to the digital edition of The Tube and Pipe Journal.
- Podcasting
- Podcast:
- The Fabricator Podcast
- Published:
- 04/30/2024
- Running Time:
- 53:00
Seth Feldman of Iowa-based Wertzbaugher Services joins The Fabricator Podcast to offer his take as a Gen Zer...
- Trending Articles
JM Steel triples capacity for solar energy projects at Pennsylvania facility
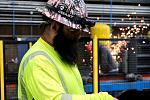
Fabricating favorite childhood memories
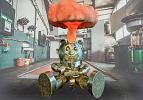
How laser and TIG welding coexist in the modern job shop
Robotic welding sets up small-batch manufacturer for future growth
Ultra Tool and Manufacturing adds 2D laser system
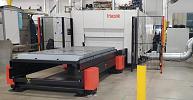
- Industry Events
Pipe and Tube Conference
- May 21 - 22, 2024
- Omaha, NE
World-Class Roll Forming Workshop
- June 5 - 6, 2024
- Louisville, KY
Advanced Laser Application Workshop
- June 25 - 27, 2024
- Novi, MI
Precision Press Brake Certificate Course
- July 31 - August 1, 2024
- Elgin,