Contributing Writer
- FMA
- The Fabricator
- FABTECH
- Canadian Metalworking
Categories
- Additive Manufacturing
- Aluminum Welding
- Arc Welding
- Assembly and Joining
- Automation and Robotics
- Bending and Forming
- Consumables
- Cutting and Weld Prep
- Electric Vehicles
- En Español
- Finishing
- Hydroforming
- Laser Cutting
- Laser Welding
- Machining
- Manufacturing Software
- Materials Handling
- Metals/Materials
- Oxyfuel Cutting
- Plasma Cutting
- Power Tools
- Punching and Other Holemaking
- Roll Forming
- Safety
- Sawing
- Shearing
- Shop Management
- Testing and Measuring
- Tube and Pipe Fabrication
- Tube and Pipe Production
- Waterjet Cutting
Industry Directory
Webcasts
Podcasts
FAB 40
Advertise
Subscribe
Account Login
Search
Die Science: Splitting in a stretch flange?
Forming factors to consider
- By Art Hedrick
- July 18, 2017
- Article
- Bending and Forming
Splitting in the proximity of a stretch flange is one of the most common forming failures that occur in sheet metal stamping.
What is Stretch Flange?
Also known as a tension flange , a stretch flange is a part feature in which the metal is bent along a concave or convex axis. This curvature forces the material to stretch from a short length of line to a longer length of line. Because the metal is being stretched, it has a tendency to crack or split along the curved surface (see Figure 1 ) .
Stretch flanges are common design features in stamped parts. They typically are added to increase a part’s stiffness and rigidity.
Part features such as the length of flange, the radial profile, and the metal type and thickness determine the difficulty of the flange. Long flanges formed in an area with a small radial profile are the most difficult, especially if they are made of high-strength metals (see Figure 2 ). The smaller the profile radius, the more difficult it will be to keep the flange from splitting.
Stretch Distribution
Of all the factors controlling the success of the stretch flanging operation, the type of material being flanged, its thickness, and its mechanical properties are the most influential. Materials exhibiting good stretchability and stretch distribution characteristics are best-suited for stretch flanging operations.
In the case of ferrous metals, such as plain carbon steels, the metal’s stretching characteristics are best expressed by evaluating the material’s n value. Also known as the material’s work-or strain hardening exponent, this numeric value represents the metal’s ability to distribute stretch though the process of strain hardening.
The higher the number, the more evenly and uniformly the material will stretch. For carbon steel, the n value is from 0.1 to 0.3. Low-carbon steel typically has an n value of about 0.22 or higher, whereas high strength carbon steel might have values near 0.11 or lower.
This ability to stretch is known as stretch or strain distribution . The metal’s stretch distribution characteristics do not stretch over a large surface area but rather stretch in a very confined, isolated area. This is commonly called localized straining .
Performing
To make a long stretch flange out of a material with a lower n value, a perform operation might be needed before the flanging operation.
The basic purpose of performing the blank is to gain the same surface area that is contained in the stretch flange geometry by stretching the metal first. This gives the process engineer a chance to force stretch distribution by altering the punch shape of the preforming operation. In other words, preforming the material stretches more surface area of the metal needed in the flange.
Many tooling engineers elect to use a “roller coaster” perform shape to prevent severe localized stretching. As long as the surface area increase is equal to or greater than the surface area of the flange, the likelihood of splitting is reduced.
Blank and Hole Edge Quality
Cutting metal before the flanging process can affect the results. The normal metal cutting process, with the exception of speciality operations such as GRIP flow ® or fine blanking, involves exceeding the metal’s shear involves exceeding the metal’s shear strength, which results in the metal fracturing or breaking free. However, before the metal can fracture, the punch must cut or extrude the metal.
The basic process results in a cut metal edge that combines a portion of shear and a portion of fracture. This shear/ fracture relationship, often referred to as the metal’s cut band , can be seen on the edge of any conventionally cut part (see Figures 3 ).
Oftentimes grinding or sanding the edge of the blank before forming results in a more successful stretch flanging operation. There are two basic reasons for this result:
- The smooth portions of the cut has more edge-stretching capability than the fracture portion of the cut. Smoothing out this fracture zone of the metal results in more edge-stretching ability for the material
- During the metal cutting process, the metal often is deformed in compression around the punch or cutting section. This metal deformation usually results in work hardening at the cut edge. This cold worked material has less stretching ability than unworked material. Grinding the edge of the blank often removes the cold-worked material and smooths the cut edge.
Shaving the Blank Edge
Cut edges in areas that will be exposed to tension must be kept sharp and free of chips or severely damaged edges. Even a small chip in the cutting edge can create a weak spot or stress riser in the cut edge. When this edge is exposed to tension, it typically begins to split at the stress riser location.
Many stampers shave the cut edge to keep it smooth and remove the work-hardened edge. Shaving is more of a machining or broaching process than a metal cutting process. Unlike a conventional piercing or trimming punch, a shaving punch is ground to a sharp point resembling a lathe or sharper tool bit. It removes a small portion of the cut edge using a positive rake angle. This leaves the cut edge smooth and also helps to remove some of the cold-worked material on the edge.
One drawback of shaving in a die is that it often leaves small shaving slivers in the tool, which can cause problems. Most companies use commercial vacuum units to keep the die free from slivers.
Data-based Forming
The notorious stretch flange always has been—and probably always will be—somewhat of a forming problem. Success begins with a realistic product design followed by a good, data-based forming process. Understanding all of the factors that affect the metal’s edge-stretching ability is the key.
Until next time… Best of luck!
About the Author
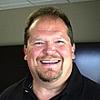
Art Hedrick
10855 Simpson Drive West Private
Greenville, MI 48838
616-894-6855
Related Companies
subscribe now
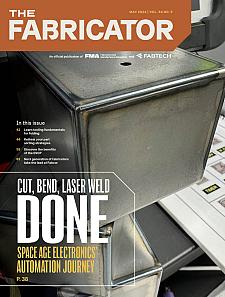
The Fabricator is North America's leading magazine for the metal forming and fabricating industry. The magazine delivers the news, technical articles, and case histories that enable fabricators to do their jobs more efficiently. The Fabricator has served the industry since 1970.
start your free subscription- Stay connected from anywhere
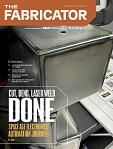
Easily access valuable industry resources now with full access to the digital edition of The Fabricator.
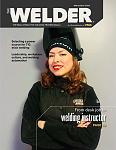
Easily access valuable industry resources now with full access to the digital edition of The Welder.
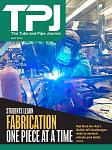
Easily access valuable industry resources now with full access to the digital edition of The Tube and Pipe Journal.
- Podcasting
- Podcast:
- The Fabricator Podcast
- Published:
- 04/30/2024
- Running Time:
- 53:00
Seth Feldman of Iowa-based Wertzbaugher Services joins The Fabricator Podcast to offer his take as a Gen Zer...
- Industry Events
16th Annual Safety Conference
- April 30 - May 1, 2024
- Elgin,
Pipe and Tube Conference
- May 21 - 22, 2024
- Omaha, NE
World-Class Roll Forming Workshop
- June 5 - 6, 2024
- Louisville, KY
Advanced Laser Application Workshop
- June 25 - 27, 2024
- Novi, MI