Contributing Writer
- FMA
- The Fabricator
- FABTECH
- Canadian Metalworking
Categories
- Additive Manufacturing
- Aluminum Welding
- Arc Welding
- Assembly and Joining
- Automation and Robotics
- Bending and Forming
- Consumables
- Cutting and Weld Prep
- Electric Vehicles
- En Español
- Finishing
- Hydroforming
- Laser Cutting
- Laser Welding
- Machining
- Manufacturing Software
- Materials Handling
- Metals/Materials
- Oxyfuel Cutting
- Plasma Cutting
- Power Tools
- Punching and Other Holemaking
- Roll Forming
- Safety
- Sawing
- Shearing
- Shop Management
- Testing and Measuring
- Tube and Pipe Fabrication
- Tube and Pipe Production
- Waterjet Cutting
Industry Directory
Webcasts
Podcasts
FAB 40
Advertise
Subscribe
Account Login
Search
Die Science: Steel made simple, Part I
- By Art Hedrick
- August 9, 2017
- Article
- Bending and Forming
Sound confusing? It is.
Have you ever attempted to get a better gaps of sheet steel properties but instead became overwhelmed and frustrated with hard-to-understand technical jargon? Believe me, you’re not alone. Even after more than 20 years in the stamping, training, and die building business, I still get confused.
Most stampers and die builders are concerned primarily with the end result of the steel. We are concerned with its formability, weldability, and strength. In-depth metallurgical mathematical calculations may be useful for steel researchers and producers, but they rarely help stampers solve splitting issues.
Let’s take a look at some basic steel terms defined first in metallurgical terminology and then translated into plain English.
Stress
Technical : The intensity at a point in a body of the internal forces or components of force that acts on a given plane through the point.
Translation: A measurement of the force being applied to the steel. Higher strength steels require higher stress to deform the same amount as a lower strength steel.
Strain
Technical : The unit change in size or shape of a body caused by force, referred to as its original size or shape.
Translation : A measurement of deformation. For a stamped part to hold its shape, it must be strained. Metal straining can occurring in tension (pulling or stretching the metal) or in compression (pushing the metal together). Strain distribution is the metal’s ability to stretch evenly over a large surface area. Good drawing-quality low-strength steels typically have a good strain distribution, while high-strength steels have poor strain distribution characteristics.
Stress-Strain Curve
Technical : A diagram in which corresponding values of stress and strain are plotted against each other.
Translation : A chart that shows how the steel is deforming, as well as how much force is needed to deform the steel permanently. Figure 1 shows a typical stress-strain curve.
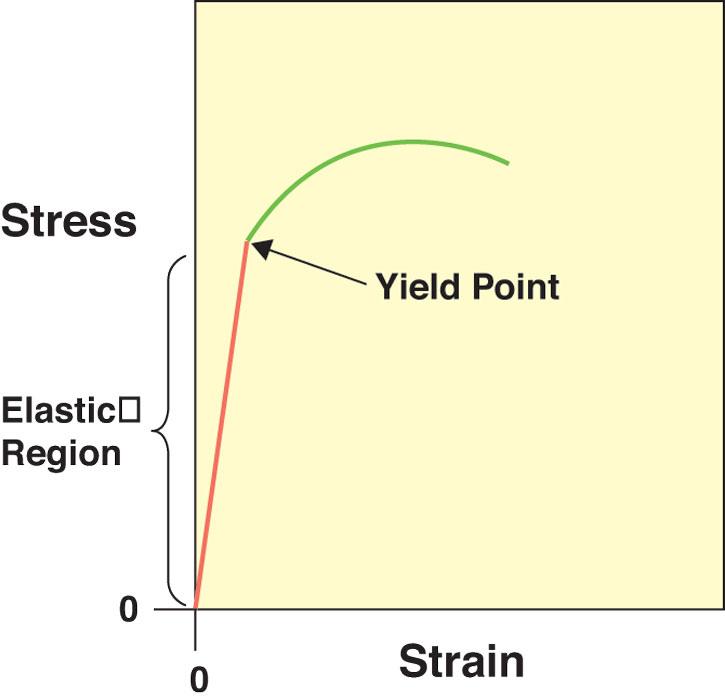
Figure 1
The yield point on a simple stress-strain diagram shows how much force is needed to deform the steel permanently.
Elastic Recovery
Technical : The ratio of stress to corresponding strain below the proportional limit.
Translation : Springback and the metal’s tendency for springback. Any time a sheet of steel is deformed, it tries to return to its original flat shape. All metal exhibit a certain amount of elastic recovery. High-strength steels exhibit more elastic recovery than do low strength steels.
Elastic Deformation
Technical : The value on a stress-strain diagram at which the metal exhibits a proportional ratio of stress to strain.
Translation : Deformation that results in 100 percent elastic recovery. The elastic zone of deformation is shown in Figure 2 .
Plastic, or Permanent, Deformation
Technical: The point at which the metal begins to undergo permanent strain.
Translation: For a stamping to hold its shape, it must be permanently, or plastically, strained. Once the metal has bene plastically stained, its mechanical properties change. In other words, if I bowed severely the same sheet of steel mentioned previously, it would begin to take the bowed shape. A certain amount of springback still would occur, but the sheet would retain a slight bow.
Yield Strength
Technical: The point at which a material exhibits a determined deviation from the proportion of stress to strain as shown on a strew-strain diagram.
Translation : A measurement of the force needed to deform a steel permanently, or plastically. In other words, it is the point at which the metal gives up, or yields, to the forces being applied (stress). The yield point is shown on the stress-strain diagram in Figure 3 . A material’s yield strength usually is expressed as a numerical value in pounds per square inch, kilo pounds per square inch, or megapascals.
Hard steels containing more carbon have high yield strengths. Typically, as yield strength increases, stretchability decreases. Use of steel with high yield strength is becoming more popular in the automotive industry because it produces lighter, stronger, and more fuel efficient vehicles.
These are just a few of the basic terms and definitions used to described steel’s mechanical properties and forming behaviors. If you are a metallurgist, you may find my descriptions and definitions a bit broad and not as well-refined as you would like. Please keep in mind that this information is intended for end users.
Part II will cover more specific formability characteristics of steel. Until then, good luck!
About the Author
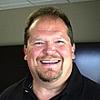
Art Hedrick
10855 Simpson Drive West Private
Greenville, MI 48838
616-894-6855
Related Companies
subscribe now
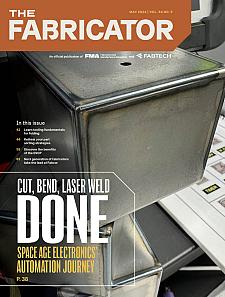
The Fabricator is North America's leading magazine for the metal forming and fabricating industry. The magazine delivers the news, technical articles, and case histories that enable fabricators to do their jobs more efficiently. The Fabricator has served the industry since 1970.
start your free subscription- Stay connected from anywhere
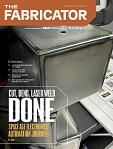
Easily access valuable industry resources now with full access to the digital edition of The Fabricator.
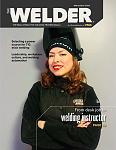
Easily access valuable industry resources now with full access to the digital edition of The Welder.
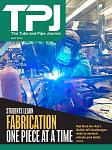
Easily access valuable industry resources now with full access to the digital edition of The Tube and Pipe Journal.
- Podcasting
- Podcast:
- The Fabricator Podcast
- Published:
- 04/30/2024
- Running Time:
- 53:00
Seth Feldman of Iowa-based Wertzbaugher Services joins The Fabricator Podcast to offer his take as a Gen Zer...
- Industry Events
Pipe and Tube Conference
- May 21 - 22, 2024
- Omaha, NE
World-Class Roll Forming Workshop
- June 5 - 6, 2024
- Louisville, KY
Advanced Laser Application Workshop
- June 25 - 27, 2024
- Novi, MI
Precision Press Brake Certificate Course
- July 31 - August 1, 2024
- Elgin,