Contributing Writer
- FMA
- The Fabricator
- FABTECH
- Canadian Metalworking
Categories
- Additive Manufacturing
- Aluminum Welding
- Arc Welding
- Assembly and Joining
- Automation and Robotics
- Bending and Forming
- Consumables
- Cutting and Weld Prep
- Electric Vehicles
- En Español
- Finishing
- Hydroforming
- Laser Cutting
- Laser Welding
- Machining
- Manufacturing Software
- Materials Handling
- Metals/Materials
- Oxyfuel Cutting
- Plasma Cutting
- Power Tools
- Punching and Other Holemaking
- Roll Forming
- Safety
- Sawing
- Shearing
- Shop Management
- Testing and Measuring
- Tube and Pipe Fabrication
- Tube and Pipe Production
- Waterjet Cutting
Industry Directory
Webcasts
Podcasts
FAB 40
Advertise
Subscribe
Account Login
Search
Die Science: Tooling and die training
Part II: Begin with a course outline
- By Art Hedrick
- August 9, 2017
- Article
- Bending and Forming
Human Engineering
Human engineering is the single most important class a company can offer its employees. Having a tool roomful of die geniuses who don’t know how to communicate effectively is like having a Ferrari without gas. The potential is great, but you can’t realize it.The success of an organization does not rely solely on it technical ability; it also relies on its working culture. It is important to train your employees to communicate effectively and to teach them what leadership really is. The principles of this course are learned behaviors, not instinctual.
Course outline:A. Leadership principles
B. Conflict resolution
C. Listening
D. Effective communication
E. Team building
F. Basic human psychology
G. Creative thinking
H. Problem solving
Stamping Die and Press Fundamentals
We all have to start somewhere. Don’t assume that this basic information is unnecessary
Course outline:A. Stamping die fundamentals
Line dies- Progressive dies
- Transfer dies
- Speciality dies
B. Cutting fundamentals
- Blanking
- Piercing/perforating
- Lancing
- Trimming
- Notching
C. Forming fundamentals
- Bending
- Flanging
- Coining
- Ironing
- Cold heading
- Drawing
- Solid forming/restriking
- Embossing
- Hemming
- Curling
D. Die terminology
- Cams
- Dowels
- Guide pin types
- Buttons
- Pierce punch types
- Die shoes
- Heels
- Parallels
E. Press fundamentals
- Press types
- Counterbalance
- Ram
- Bolster
- Cushion
- Stroke
- Tonnage
F. Basic precision instrument reading
- Micrometers
- Height gauges
- Indicators
Sheet Material
Before you process, build, and try out a die, you need to understand the material you are dealing with to make a good, data-based decision. The objective is not to get side-tracked by the details of manufacturing the material, but rather to focus on how to select the material an dot understand how it behaves when it is cut and formed. Remember that you are the end user of the product, not the producer.
Course outline :A. Ferrous and nonferrous metals
B. Yield strength
C. Stretch distribution
D. n value
E. r value
F. High-strength materials
G.Aluminium
H. Coil defects
Tool Steel Selection and Treatment
Make sure the diemakers indresadtand how to select the proper tool steel for the job. Make sure they also understand how to mill, drill, weld, and grind it properly.
A. Tool steel selectioN
B. Hardness measurement
C. Toughness
D. Wear resistance
E. Interface
F. Carbide
G. Welding
H. Grinding
I. Drilling
J. Milling
K. Stress relieving
L. Tempering
Safety
A small 250-ton press can exert 5000,000 pounds of pressure, and presses and equipment used in diemaking are completely unforgiving, so saftey is a very imprint issue.
Course outline:A. Crane safety
B. Press safety
C.Basic first aid
D.HiLo reach and fork truck operation
Die setup
Many problems can be traced back to an improper die setup
Course outline: Shut height Press cleanness Pitch progression Press feeders and straightnessGas pressuresDie location and alignment Counterbalance Tonnage monitorsLubrication methodsProgressive Die Design
Most companies have or design progressive dies. A good die begins with a good process and design method.
Course outline:A. Strip carrier designs
- Solid
- Stretch/flex
B. Strip starting and piloting
- Pitch stops
- First hit line
- Smooth feeding techniques
- Bar lifters/round lifters
C. Metal cutting
Cutting clearance selection- Wrap removal
- Bypass burrs
- Pinch trimming
D. Part flatness
- Pressure blanking
- Strippling
E. Flanging, bending, curling, and extruding
- Stretch flanges/compression flanges
- Holding bend tolerances
- Hole flanging techniques
F. Pressure and stripper pads
G. Drawing in progressive dies
- Draw ratios
- Radii
- Timing
H. Web carrier development techniques Forming problems are the most prevalent in stamping shops. Splitting in draws, inability to maintain or achieve been angles, and fracturing in stretch flanges and extrusions are common problems. A. Bending B. Stretch compression flanging C. Embossing D. Metal stretching E. Drawing These are just a few of the most commonly needed classes. You may find it necessary to add classes on statistical process control, math, heatreating, metallurgy, and other topics. Find out what training your company really needs, and don't be satisfied with a "canned" course from the local tech center that doesn't fit your requirements. Don't forget that your own employees can be a great resource for leading the training. You might be surprised at the training talent in your own company. Until next time... Best of luck! Sheet Metal Forming Techniques
Make it Your Own
About the Author
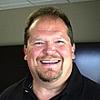
Art Hedrick
10855 Simpson Drive West Private
Greenville, MI 48838
616-894-6855
Related Companies
subscribe now
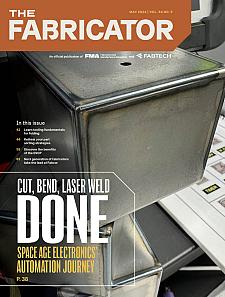
The Fabricator is North America's leading magazine for the metal forming and fabricating industry. The magazine delivers the news, technical articles, and case histories that enable fabricators to do their jobs more efficiently. The Fabricator has served the industry since 1970.
start your free subscription- Stay connected from anywhere
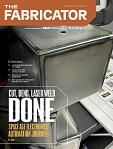
Easily access valuable industry resources now with full access to the digital edition of The Fabricator.
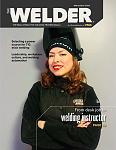
Easily access valuable industry resources now with full access to the digital edition of The Welder.
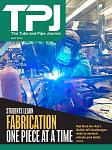
Easily access valuable industry resources now with full access to the digital edition of The Tube and Pipe Journal.
- Podcasting
- Podcast:
- The Fabricator Podcast
- Published:
- 04/30/2024
- Running Time:
- 53:00
Seth Feldman of Iowa-based Wertzbaugher Services joins The Fabricator Podcast to offer his take as a Gen Zer...
- Industry Events
Pipe and Tube Conference
- May 21 - 22, 2024
- Omaha, NE
World-Class Roll Forming Workshop
- June 5 - 6, 2024
- Louisville, KY
Advanced Laser Application Workshop
- June 25 - 27, 2024
- Novi, MI
Precision Press Brake Certificate Course
- July 31 - August 1, 2024
- Elgin,