Contributing Writer
- FMA
- The Fabricator
- FABTECH
- Canadian Metalworking
Categories
- Additive Manufacturing
- Aluminum Welding
- Arc Welding
- Assembly and Joining
- Automation and Robotics
- Bending and Forming
- Consumables
- Cutting and Weld Prep
- Electric Vehicles
- En Español
- Finishing
- Hydroforming
- Laser Cutting
- Laser Welding
- Machining
- Manufacturing Software
- Materials Handling
- Metals/Materials
- Oxyfuel Cutting
- Plasma Cutting
- Power Tools
- Punching and Other Holemaking
- Roll Forming
- Safety
- Sawing
- Shearing
- Shop Management
- Testing and Measuring
- Tube and Pipe Fabrication
- Tube and Pipe Production
- Waterjet Cutting
Industry Directory
Webcasts
Podcasts
FAB 40
Advertise
Subscribe
Account Login
Search
Die Science: Using urethane in dies
- By Art Hedrick
- August 4, 2017
- Article
- Bending and Forming
Meeting that challenge often requires us to think about tooling from a completely different perspective. Urethane, which has bene used in dies for many years in various applications, can present a whole new approach.
Shrinking Tool Life Requirements
Despite the enormous challenges that we stampers are faced with, there is a little good news. Unlike 20 years ago, certain stamped automotive parts are not required in large volumes. Consumers today are looking of new car styles every year. This increases the number of tools required, but also decrease the number of part that each tool must produce.
Many dies produce, say, 20,000 parts and then later are used for very short-run service parts only. This is good news for urethane, since most urethane tools do not last as long as dies made from tool steel. Take time to collect data with respect to the expected life of the tool. If you expect your die stop produce millions of parts a year, urethane may not be your best choice. However, if your production needs are few, and yu budget is lean, welcome to urethane.
Urethane types and Grades
Urethane is available in many types, shapes, hardness levels, and compression rates (see Figure 1 ). Most are color-coded to indicate hardness and type. Generally speaking, softer grades can be compressed much more than harder grades. However, softer grades of urethane often do not have the necessary force needed to perform adequately.
The hardness of urethane is measured using a durometer. The higher the durometer reading, the harder the urethane, and the harder the urethane, the more abrasion-resistant it is and the less it can compress. For example, a urethane measuring 70 on a durometer can safely compress about 35 percent and offer an average force of about 110 pounds when compressed 10 percent. However, urethane measuring 95 on a durometer can safely compress about 15 percent, offering a force of 450 lbs. when compressed 10 percent.
Cutting Applications
Consider using urethane as a cost-saving measure in cutting dies. Urethane can be used as an alternative to a spring-or pressure-loaded stripper pad.
Many tool designers and process engineers avoid using urethane strippers because they claim the urethane doesn’t last long. While urethane will not outlast a steel stripper pad, most premature failure is the result of too much pierce punch entry.
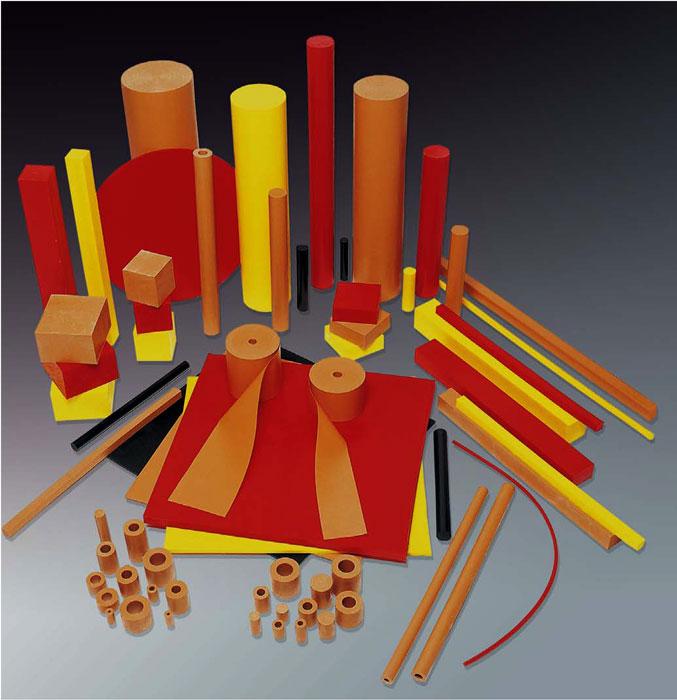
Figure 1
Urethane is available in many types,
shapes, hardness levels, and compression
rates. Image courtesy of Danly IEM,
Bellaire, Mich.
Overentering your piece punch compresses the urethane to a much greater extent, dramatically reducing its life. Try to enter your piece punches no more than necessary. A good rule of thumb is no more than 1x the metal’s thickness (see Figure 2 ).
When piercing metal that is very thick, such as 0.500 inch, use a softer grade of urethane, and make sure that you are using engineered cutting clearance to help reduce the stripping force. Using insufficient cutting clearance will increase the required stripping force (see Figure 3 ), and you’ll have to use a much higher-strength, harder grade of urethane. Hard grades of urethane cannot be compressed as much as softer grades, and over-compressing them results in shorter urethane life.
Urethane Pressure Pads
Urethane often can be used as a substitute coil and gas springs. The key is to avoid using it when a great deal of compression is required. For example, urethane springs are fine to use under a draw pad when the depth of form is limited. However, using them in severe deep-drawing operations most likely will result in complete failure or, at best, a very short urethane spring life.
When using urethane springs for drawing dies, be sure to use spacer blocks between the die face and draw pad. This will allow you to control the space between these two components. Adding spacer blocks also will help to prevent the tremendous pressure rise that can result in squeezing the blank tighter and tighter as the pad moves downward (see Figure 4 ).
Urethane Forming Punches
I have always thought that using a urethane punch is sort of “poor man’s hydroforming.” Believe it or not, urethane offers some of the same advantages as water. First of all, unlike a steel punch, urethane can change its shape during the forming process. Second, it forces the metal to distribute the stretching more evenly. This results in less springback and reduces the probability of splitting.
Unlike a steel punch, a urethane punch can be engineered to contact the entire surface of the blank. This can offer a much better draw ratio than a conventional steel punch. Using urethane also typically allows a part to be made in fewer steps (see Figure 5 ).
Keep in Mind
Certainly urethane is not the definitive material to use in all applications. Keep in mind that you should pay careful attention to solvents and certain lubricants, as they may quickly deteriorate the urethane.
Also, trying to achieve features in a stamped part such as sharp radii or corners is very difficult. A good compromise is to obtain the basic shape of the part using urethane and then switch to a secondary steel die to sharpen up the part features.
Until next time… Best of luck!
About the Author
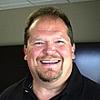
Art Hedrick
10855 Simpson Drive West Private
Greenville, MI 48838
616-894-6855
Related Companies
subscribe now
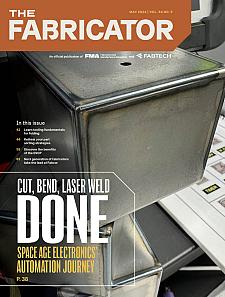
The Fabricator is North America's leading magazine for the metal forming and fabricating industry. The magazine delivers the news, technical articles, and case histories that enable fabricators to do their jobs more efficiently. The Fabricator has served the industry since 1970.
start your free subscription- Stay connected from anywhere
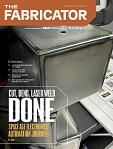
Easily access valuable industry resources now with full access to the digital edition of The Fabricator.
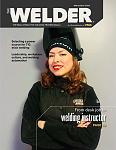
Easily access valuable industry resources now with full access to the digital edition of The Welder.
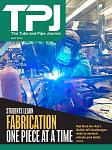
Easily access valuable industry resources now with full access to the digital edition of The Tube and Pipe Journal.
- Podcasting
- Podcast:
- The Fabricator Podcast
- Published:
- 04/30/2024
- Running Time:
- 53:00
Seth Feldman of Iowa-based Wertzbaugher Services joins The Fabricator Podcast to offer his take as a Gen Zer...
- Industry Events
Pipe and Tube Conference
- May 21 - 22, 2024
- Omaha, NE
World-Class Roll Forming Workshop
- June 5 - 6, 2024
- Louisville, KY
Advanced Laser Application Workshop
- June 25 - 27, 2024
- Novi, MI
Precision Press Brake Certificate Course
- July 31 - August 1, 2024
- Elgin,