- FMA
- The Fabricator
- FABTECH
- Canadian Metalworking
Categories
- Additive Manufacturing
- Aluminum Welding
- Arc Welding
- Assembly and Joining
- Automation and Robotics
- Bending and Forming
- Consumables
- Cutting and Weld Prep
- Electric Vehicles
- En Español
- Finishing
- Hydroforming
- Laser Cutting
- Laser Welding
- Machining
- Manufacturing Software
- Materials Handling
- Metals/Materials
- Oxyfuel Cutting
- Plasma Cutting
- Power Tools
- Punching and Other Holemaking
- Roll Forming
- Safety
- Sawing
- Shearing
- Shop Management
- Testing and Measuring
- Tube and Pipe Fabrication
- Tube and Pipe Production
- Waterjet Cutting
Industry Directory
Webcasts
Podcasts
FAB 40
Advertise
Subscribe
Account Login
Search
R&D Update: Warm-forming magnesium sheet, Part I
- November 10, 2017
- Article
- Bending and Forming
Mg has a lower density (1.7 g/cm³) than Al (2.7 g/cm³) and a higher strength-to-weight ratio. Mg alloys are used mostly in die casting, but the automotive industry’s goal to reduce vehicle weight is resulting in its increased use in sheet and tube forming applications.
The formability of Mg sheet at room temperature is limited, so several research groups, including the ERC/NSM, are exploring forming the alloy at elevated temperatures. This method, called warm forming, involves temperatures up to 300 degrees C (572 degrees F).
Physical Properties of Magnesium
According to www.magnesium.com, 1 cubic kilometer (km) of seawater contains 1.5 million tons of Mg, and there is 1,375 million cubic km of seawater in the world. General Motors currently uses 28,000 metric tons (mt) of Mg casting in its cars; Ford Motor Co. uses 19,000 mt; and Daimlerchrysler AG’s Chrysler Group uses 10,000 mt.
The International Standards Organization has designated 16 Mg alloys and heat treatment conditions.
The main group of Mg alloys that can be formed are the MgAlZn alloys (AZ alloys) with a concentration of Al and Zn. The most common AZ alloys are AZ31(3 percent Al, 1 percent Zn), AZ61 (6 percent Al, 1 percent Zn), and AZ80 (8 percent Al, 0.5 percent Zn). Figure 1 shows the composition of the AZ31B alloy.
Figures 2 and 3 compare the physical properties of the AZ31B alloy with 1006 and ASTM A572, a low- and a high-carbon alloy steel, respectively, and Al5086 alloy.
AZ31B has the lowest Young’s modulus (48 GPa/6,960 KSI) and a yield stress of 170 MPa (24,656 PSI) at room temperature. Mg has the highest specific strength (strength/density) among all other metals. Figure 3 illustrates that Mg is suitable fro structural part design and that all four metals have approximately the same specific stiffness (elastic modulus/ density).
More information about the mechanical and physical properties of Mg is available at the International Magnesium Association’s Web site, www. intlmag.org.
Magnesium’s Forming Limitations
The main disadvantages of using Mg-alloy sheet for automotive body panels are in its high cost and limited formability at room temperature. The cost may decrease as its use increases and suppliers find ways to cut prices to compete. It is almost impossible to draw a complex automotive body panel using Mg-alloy sheet at room temperature because forming needs to take place at elevated temperatures.
Figure 4 shows the flow stress curves for AZ31B sheet at elevated temperatures between 25 degrees C and 235 degrees C (77 degrees F and 455 degrees F). At a constant strain rate (Ɛ= 0.002s-1), strain values up to 0.35 at 235 degrees C (455 degrees F) were obtained. It is interesting to note that at 235 degrees C, with a strain value of 0.2, flow stress decreases (that is , work-softening behavior begins).
Part II will cover current tool design strategies and applications of deep-drawn hydroformed Mg sheet and tubular parts.
subscribe now
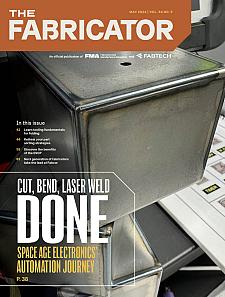
The Fabricator is North America's leading magazine for the metal forming and fabricating industry. The magazine delivers the news, technical articles, and case histories that enable fabricators to do their jobs more efficiently. The Fabricator has served the industry since 1970.
start your free subscription- Stay connected from anywhere
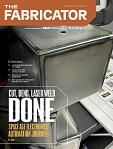
Easily access valuable industry resources now with full access to the digital edition of The Fabricator.
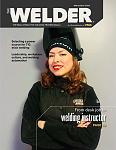
Easily access valuable industry resources now with full access to the digital edition of The Welder.
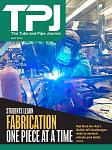
Easily access valuable industry resources now with full access to the digital edition of The Tube and Pipe Journal.
- Podcasting
- Podcast:
- The Fabricator Podcast
- Published:
- 04/16/2024
- Running Time:
- 63:29
In this episode of The Fabricator Podcast, Caleb Chamberlain, co-founder and CEO of OSH Cut, discusses his company’s...
- Trending Articles
Tips for creating sheet metal tubes with perforations
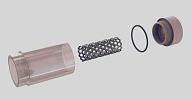
JM Steel triples capacity for solar energy projects at Pennsylvania facility
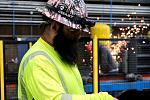
Are two heads better than one in fiber laser cutting?
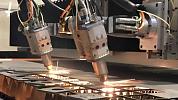
Supporting the metal fabricating industry through FMA
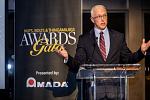
Omco Solar opens second Alabama manufacturing facility
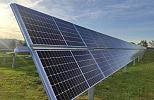
- Industry Events
16th Annual Safety Conference
- April 30 - May 1, 2024
- Elgin,
Pipe and Tube Conference
- May 21 - 22, 2024
- Omaha, NE
World-Class Roll Forming Workshop
- June 5 - 6, 2024
- Louisville, KY
Advanced Laser Application Workshop
- June 25 - 27, 2024
- Novi, MI