Contributing Writer
- FMA
- The Fabricator
- FABTECH
- Canadian Metalworking
Categories
- Additive Manufacturing
- Aluminum Welding
- Arc Welding
- Assembly and Joining
- Automation and Robotics
- Bending and Forming
- Consumables
- Cutting and Weld Prep
- Electric Vehicles
- En Español
- Finishing
- Hydroforming
- Laser Cutting
- Laser Welding
- Machining
- Manufacturing Software
- Materials Handling
- Metals/Materials
- Oxyfuel Cutting
- Plasma Cutting
- Power Tools
- Punching and Other Holemaking
- Roll Forming
- Safety
- Sawing
- Shearing
- Shop Management
- Testing and Measuring
- Tube and Pipe Fabrication
- Tube and Pipe Production
- Waterjet Cutting
Industry Directory
Webcasts
Podcasts
FAB 40
Advertise
Subscribe
Account Login
Search
Die Science: Driving change in metal forming methods
- By Art Hedrick
- August 1, 2017
- Article
- Bending and Forming
In addition to seeking alternative fuel sources, the U.S. is making a great effort to develop more fuel-efficient vehicles. Reducing the size of an automobile certainly helps reduce fuel consumption, but this alone will not solve the fuel crisis. Changes have to be made in the use of new materials and methods that will contribute to fuel efficiency.
New Steel
The aircraft industry has been using ultrahigh-strength materials, both ferous and nonferrous, for years. The latest material being used is carbon graphite, a strong, light material often used in the bodies of race cars. In some newer jets, the entire fuselage is made from this material. Other materials, commonly referred to as superalloys, also are not uncommon. INCONEL® alloy and titanium are popular choices.All of these materials are used in the interest of obtaining extreme strength and reducing weight in aircraft. Rarely are these materials used in the production and manufacturing of consumer vehicles, however, because they are expensive. Although they would help to reduce vehicle weight and fuel consumption, they would also double the cost of producing an automobile.
Instead of using these expensive materials, the automobile industry has started using more advanced high strength steel (AHSS). The high strength of these steels results from the process of strain hardening. Strain, or work hardening, is the same thing that happens when you bend a coat hanger back and forth in an attempt to break it. As the metal is bent, it gets more and more difficult to deform it in the same localized area. The metal becomes cold-worked and hard.
AHSS work-hardens a great deal, resulting in as much as a 40 percent increase in strength. This allows automobile manufactures to reduce the metal’s thickness while still retaining the necessary product strength.
One of the most commonly used types of AHSS is dual-phase. Martensitic grades are used for application requiring extreme strength or heat treating. These special grades are available in strengths ranging from 250 MPa (36,250 PSI) to 1,300 MPa (188,500 PSI).
Steel Problems
One of the problems with using AHSS is that it does not increase in strength unless it is permanently deformed. Many products are designed and processed so that only small areas of the product are strained, which means only those isolated areas will have an increase in strength. In addition, to reduce the amount of springbuck that occurs, the entire stamping must be strained as evenly as possible.
Compared to conventional low-carbon steel, AHSS has very poor stretch or strain distribution characteristics. In other words, when it is subjected to a stretching operation, it has a tendency to stretch in a very small, localized area and does not distribute the stretch over a larger surface area. A great deal of strain and work hardening in an area of a part right next to an area that has not been strained may result in severe twisting of the formed part.
Lower-carbon steels, especially those with high elongation and n values, distribute the stretch more evenly over a large surface area.
The Hydroforming Option
Using nonconventional methods such as hydroforming can help distribute strain more evenly in an AHSS part. Unlike a conventional metal drawing or stretching operation, which uses a steel punch and cavity to stretch the metal where the punch contacts the sheet (see Figure 1a ), hydroforming uses water to form the metal. The water pushes the metal into the cavity or over the punch (see Figure 1b ). In either case, water replaces one die half.
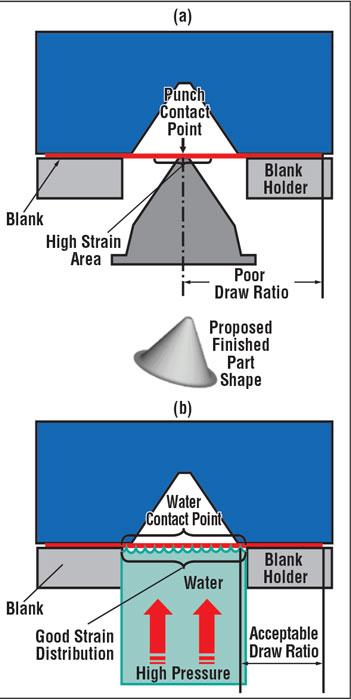
Figure 1
The same conical part shape can be produced
through conventional stamping and
drawing methods or by hydroforming.
Other methods, such as explosive and electromagnetic forming, use the same basic concept but replace the water with an alternative means of force.
Other methods, such as explosive and electromagnetic forming, use the same basic concept but replace the water with an alternative means of force.
Using AHSS and hydroforming or other nonconventional methods in automobile manufacture allows the use of more stretchable materials, which reduces the weight of the vehicle while improving strength. Improved stretch distribution reduces springback and allow for stronger part with no “dead’ metal. Material and freight cost decrease.
With these methods and materials, more difficult geometries can be formed. Smaller blanks often can be used to make parts because more surface area can be stretched. In addition, stamping lubricant usage, forming temperatures, and tool steel wear all are reduced.
Hydroforming typically is slower than conventional metal forming temperatures, and tool steel wear all are reduced.
The hyrdoforming process is nothing new. It has been used in the aircraft industry for years. As the automobile industry for years. As the automobile industry begins to use more aircraft-like materials, it must consider a major change in the methods needed to form these materials.
I don’t have a crystal ball, but I do believe that someday the process of forming with a metal punch and die will become obsolete. Change drives change. Embrace change, and understand why it is necessary.
Until next time… Best of luck!
About the Author
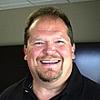
Art Hedrick
10855 Simpson Drive West Private
Greenville, MI 48838
616-894-6855
Related Companies
subscribe now
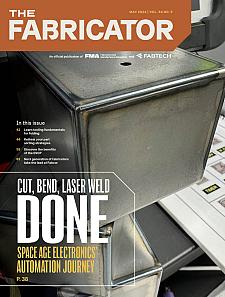
The Fabricator is North America's leading magazine for the metal forming and fabricating industry. The magazine delivers the news, technical articles, and case histories that enable fabricators to do their jobs more efficiently. The Fabricator has served the industry since 1970.
start your free subscription- Stay connected from anywhere
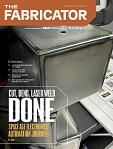
Easily access valuable industry resources now with full access to the digital edition of The Fabricator.
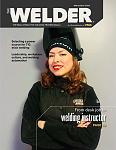
Easily access valuable industry resources now with full access to the digital edition of The Welder.
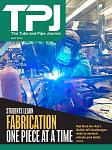
Easily access valuable industry resources now with full access to the digital edition of The Tube and Pipe Journal.
- Podcasting
- Podcast:
- The Fabricator Podcast
- Published:
- 04/30/2024
- Running Time:
- 53:00
Seth Feldman of Iowa-based Wertzbaugher Services joins The Fabricator Podcast to offer his take as a Gen Zer...
- Industry Events
16th Annual Safety Conference
- April 30 - May 1, 2024
- Elgin,
Pipe and Tube Conference
- May 21 - 22, 2024
- Omaha, NE
World-Class Roll Forming Workshop
- June 5 - 6, 2024
- Louisville, KY
Advanced Laser Application Workshop
- June 25 - 27, 2024
- Novi, MI