Sales and Applications Consultant
- FMA
- The Fabricator
- FABTECH
- Canadian Metalworking
Categories
- Additive Manufacturing
- Aluminum Welding
- Arc Welding
- Assembly and Joining
- Automation and Robotics
- Bending and Forming
- Consumables
- Cutting and Weld Prep
- Electric Vehicles
- En Español
- Finishing
- Hydroforming
- Laser Cutting
- Laser Welding
- Machining
- Manufacturing Software
- Materials Handling
- Metals/Materials
- Oxyfuel Cutting
- Plasma Cutting
- Power Tools
- Punching and Other Holemaking
- Roll Forming
- Safety
- Sawing
- Shearing
- Shop Management
- Testing and Measuring
- Tube and Pipe Fabrication
- Tube and Pipe Production
- Waterjet Cutting
Industry Directory
Webcasts
Podcasts
FAB 40
Advertise
Subscribe
Account Login
Search
Efficient die handling saves space, time, cost
Controlled movement, storage is path to maximum uptime
- By Bill Rogner and Ron Demonet
- October 3, 2018
- Article
- Bending and Forming
Most stampers concentrate on making parts efficiently to stay competitive in today’s marketplace. As one would expect, the focus is on the stamping process itself and how to make quality parts at high rates. Because of this, the dies, presses, and automation get the most attention and most of the investment capital.
Handling and storing dies is not seen as a value-added part of the process, so stamping manufacturers often pay little attention to this function. They may store dies on the floor, in inexpensive racks on a remote wall, or—worse—outside in the elements and then move them around the plant with universal material handling systems such as fork trucks and cranes.
This approach costs more than stampers realize when hidden expenses just get rolled into everyday operating costs. Inefficient die handling and storage costs include additional die repair, additional equipment maintenance, lost production time, safety-related problems, and additional labor requirements. Because these expenses are not considered direct labor expenses associated with stamping production, most companies don’t attach them to the costs of stamping a job.
They may overlook the benefits of streamlined die storage and handling when using their standard cost justification methods.
Carts for Controlled Die Movement
Efficient die handling can be defined as the safe, controlled management of dies throughout the plant, which minimizes labor requirements and production downtime.
First, random die locations make finding dies hard and can create much more searching and handling than is necessary.
- Floor-level stacked dies create blind spots or broken fields of vision. These blind spots obstruct fork truck and crane operators from seeing and avoiding unwanted contact.
- Overhead cranes often use cable slings to connect the die to the crane for transport. The slings often remain on the crane hook as the cranes traverse over the stored dies. These slings can get caught on dies or other objects while the crane is moving and cause the objects to slide or tumble.
Using material handling equipment that is designed specifically for heavy loads is the best way to minimize problems.
Heavy-duty carts with a sufficiently large, flat upper surface are optimal for moving dies from point A to point B in a stamping operation.
Track-mounted carts capable of handling large loads usually are the lowest-cost options when the conditions are amenable to this approach. If more flexibility is needed, then mobile nontrack-mounted carts are an option (see Figure 1).
Cart payload capacities are designed for a stamper’s specific needs. Payloads in excess of 50 tons are typical. The cart’s deck can be a simple flat surface or it can be fixtured to handle dies, steel coils, stacks of blanks, and maintenance parts.
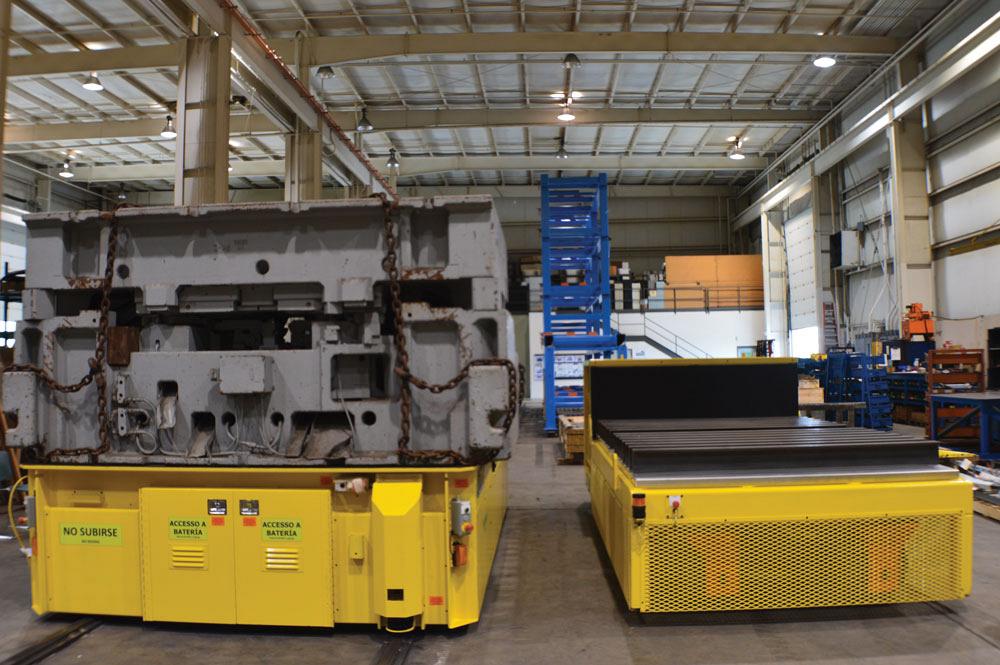
Figure 1
A track-mounted cart (left) and mobile nontrack-mounted cart (right) move dies safely and efficiently.
Controlled acceleration and deceleration make for a safer operation. Safety equipment such as bumpers, scanners, horns, and lights can be employed to enhance safety. The carts can be controlled manually via a pendant or are programmable for automatic operation.
Another positive aspect of having a heavy-duty cart dedicated to moving dies is that stampers never have to wait for a crane or fork truck that is being used for other purposes—and that means less production downtime.
High-rise Systems for Controlled Die Storage
Die storage and retrieval can be a major waste of time and resources. Stamping dies can monopolize floor space. In some facilities, just-in-time requirements have necessitated that a large number of die sets be kept waiting and ready in the pressroom. For some contract stampers, a growing customer list means more stacks of active dies that need to be managed and stored.
The number of dies that a successful stamper needs to have within ready access to the press line increases when a part job launches. While these new programs require additional work space for die storage and work-in-process inventory, the size of the building usually remains fixed.
Not only does it consume valuable floor space, but it also leads to the typical die handling problems, including die damage, high maintenance costs, part quality problems, lost production, and safety problems.
High-rise die storage and retrieval systems can help solve problems in many applications. New systems not only fix the storage space dilemma but also increase press use by providing expanded production capability without adding presses. The systems accomplish this by stacking dies close to the pressroom vertically, enabling fast, controlled access to them (see Lead Image).
Slow die changeover and floor space restrictions can create a vicious cycle for stampers running shorter production runs on a wide variety of parts, setting up a self-defeating scenario: The longer it takes to handle and change over dies for short-run production, the greater the temptation to increase each batch run, resulting in more inventory that worsens the floor space and die access problems, resulting in additional downtime.
Die storage and retrieval systems can be designed to fit a plant’s specific requirements and use plant space effectively. They can even be nestled into column lines that ordinarily are difficult-to-access dead zones (see Figure 2).
In these systems, a dedicated die retriever moves dies into and out of the storage racks in a safe, controlled manner. The retriever can interface directly with a handling cart or even directly with the quick die change system on the press line.
Implications
The controlled movement aspect of die handling has many implications. When dies are handled properly and safely, there is less chance of damage to dies, presses, and other ancillary equipment. Any damage results in repair costs, which add to overall manufacturing costs. Damage to dies and equipment also results in production downtime.
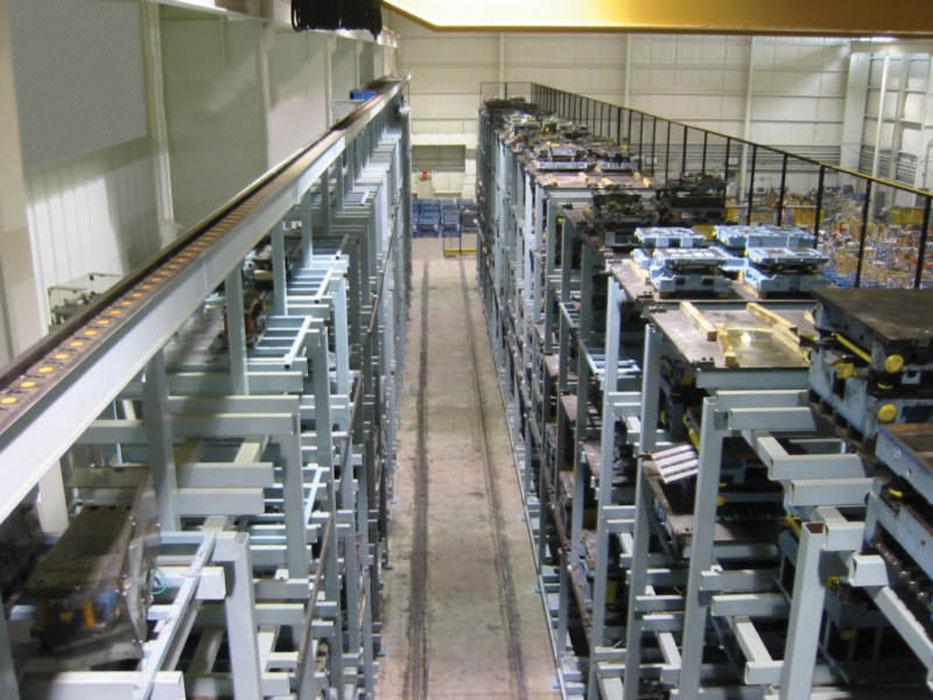
Figure 2
This automated storage and retrieval system is designed into a plant’s “dead zone.” This five-level system for a Tier 1 stamper houses 206 storage cells.
Dies last longer and wear better when they are handled in a controlled manner. This translates into more predictable, consistent part quality, which again reduces maintenance costs and production downtime.
A downed press doesn’t produce. Conversely reductions in production downtime increase equipment use and productivity. This increased productivity combined with lower overall manufacturing costs enables stampers to be more profitable in a very competitive marketplace.
Bill Rogner is sales and applications consultant and Ron Demonet is account manager for Atlas Technologies Inc., 3100 Copper Ave., Fenton, MI 48430, rognerb@atlastechnologies.com, demonetr@atlastechnologies.com, www.atlastechnologies.com.
About the Authors
Ron Demonet
3100 Copper Ave.
Fenton, MI 48430
810-629-6663
subscribe now
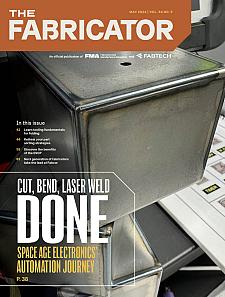
The Fabricator is North America's leading magazine for the metal forming and fabricating industry. The magazine delivers the news, technical articles, and case histories that enable fabricators to do their jobs more efficiently. The Fabricator has served the industry since 1970.
start your free subscription- Stay connected from anywhere
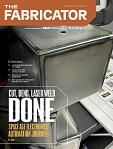
Easily access valuable industry resources now with full access to the digital edition of The Fabricator.
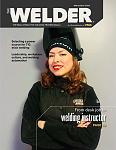
Easily access valuable industry resources now with full access to the digital edition of The Welder.
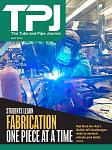
Easily access valuable industry resources now with full access to the digital edition of The Tube and Pipe Journal.
- Podcasting
- Podcast:
- The Fabricator Podcast
- Published:
- 04/16/2024
- Running Time:
- 63:29
In this episode of The Fabricator Podcast, Caleb Chamberlain, co-founder and CEO of OSH Cut, discusses his company’s...
- Trending Articles
Tips for creating sheet metal tubes with perforations
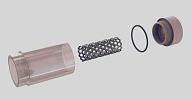
JM Steel triples capacity for solar energy projects at Pennsylvania facility
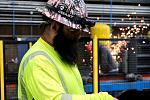
Are two heads better than one in fiber laser cutting?
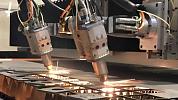
Supporting the metal fabricating industry through FMA
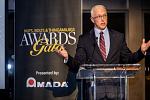
Omco Solar opens second Alabama manufacturing facility
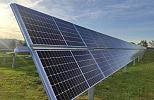
- Industry Events
16th Annual Safety Conference
- April 30 - May 1, 2024
- Elgin,
Pipe and Tube Conference
- May 21 - 22, 2024
- Omaha, NE
World-Class Roll Forming Workshop
- June 5 - 6, 2024
- Louisville, KY
Advanced Laser Application Workshop
- June 25 - 27, 2024
- Novi, MI