Press Brake Tooling Product Specialist
- FMA
- The Fabricator
- FABTECH
- Canadian Metalworking
Categories
- Additive Manufacturing
- Aluminum Welding
- Arc Welding
- Assembly and Joining
- Automation and Robotics
- Bending and Forming
- Consumables
- Cutting and Weld Prep
- Electric Vehicles
- En Español
- Finishing
- Hydroforming
- Laser Cutting
- Laser Welding
- Machining
- Manufacturing Software
- Materials Handling
- Metals/Materials
- Oxyfuel Cutting
- Plasma Cutting
- Power Tools
- Punching and Other Holemaking
- Roll Forming
- Safety
- Sawing
- Shearing
- Shop Management
- Testing and Measuring
- Tube and Pipe Fabrication
- Tube and Pipe Production
- Waterjet Cutting
Industry Directory
Webcasts
Podcasts
FAB 40
Advertise
Subscribe
Account Login
Search
Eliminating information waste at the press brake
Better communication and better visibility means better bending
- By Larry Boden
- June 20, 2019
- Article
- Bending and Forming
A well-organized press brake department can be a thing of beauty. You might see clearly labeled punches and dies on rolling carts, job sheets with well-documented setup procedures—the works. But then you see a brake operator looking intently at the CNC. He’s changing the program, including the bend sequence and perhaps even the tooling. What’s going on?
Bending is the most complex operation in metal fabrication, and good communication is absolutely key. In this case, as in many others, engineers and operators probably didn’t discuss as much as they could have before the job launched into production.
In many ways, lean manufacturing is all about flow. This includes fabricated parts as well as the information about those parts. With bending in particular, efficient part flow can’t happen without the efficient flow of information.
Fundamentals First
Having a cheat sheet can do a world of good in the press brake department, programming, and, especially, engineering. If an engineer knows what the shop’s tooling library can and cannot produce, he or she can prevent a tremendous number of headaches down the road.
What should be on this cheat sheet depends on the shop and the product mix. Generally speaking, it should describe the basics of forming tonnages to ensure the job can be bent safely with the shop’s available tools and equipment.
It also should describe the basics of bend allowances, bend deductions, and blank sizes, and how changing the inside bend radius affects all three. It should note whether the brakes are bottoming or air bending. Most modern operations air-bend, so if the shop is still relying on old charts developed around bottoming, operators in the brake department will continue to struggle, often just “making it work” the best they can.
In air bending (or air forming), the die width determines the inside bend radius, not the punch tip. In 60-KSI carbon steel, the radius air-forms at approximately 16 percent of the die opening. That percentage gets larger or smaller depending on the material and its tensile strength.
In most situations the most stable inside bend radius should equal or be very close to the material thickness. Ideally, the punch tip radius should be close to, but not greater than, the naturally floated inside radius. If the punch tip is larger than the inside bend radius, then the bend will assume the new, larger radius of the punch tip, which in turn will change your bend calculations.
For accurate bend calculations, an air-bent radius cannot be smaller than a certain percentage of the material thickness—usually around 63 percent (though there are more exact ways to calculate this). Less than that, and the bend creases and turns sharp. If you have a drawing that calls for an inside radius less than sharp, and if you use that tiny radius in your bend calculations, you’ll create inaccuracies in bending that operators will have to muddle through.
The cheat sheet also should include minimum flange lengths, which usually can’t be less than 70 percent of the standard die width. Ideally, an engineer should look at a flange on a drawing, refer to the tooling library, and know whether it will work with the machines and tools the fabricator has on the floor.
If the operator is forced to change the die to accommodate a short flange, the bend deduction will change and there will be extra setup time or, worse yet, an additional setup.
Holes and cutouts need to be factored in as well. Bends near holes or other cutouts cause distortion, so if a design has a bend line at or very near a hole, you could run into problems. Here, special tooling, like rotational wing dies that support the workpiece throughout the bend, can help. Again, the engineer would know if the shop had a rotational die, because he’d have a list of available tools on hand.
He’d also know the tooling shut heights and how they affect bend line access, such as deep box bends with return flanges. The engineer might have to talk with the programmer or others to discuss forming options, be it using gooseneck punches, window punches, a punch with horns, or anything else. But a cheat sheet could at least spell out general guidelines; if the part has flange dimensions outside these limits, the engineer can talk to the programmer to discuss options.
Finally, you have the tolerance guidelines. A cheat sheet should include what the shop deems to be reasonable linear and angular tolerances—that is, those that can be met on any properly set up machine in the shop. Material thickness can vary from lot to lot, and for efficient operation the tolerances specified should take that thickness variation into account.
For precision work, a seemingly small variation in thickness can snowball into major headaches in front of the press brake. But does the work need to be that precise? Do the tolerances need to be that tight? Ideally, engineers should ask these questions from the get-go.
True, a new press brake with modern punches and dies can hold some impressively tight tolerances, but you still need to take that material variability into account. Dealing with that adds costs and makes life in the press brake department more difficult. If a part doesn’t need to be toleranced so tightly, why specify it?
Prototyping Versus Production
From a throughput standpoint, the last thing a press brake lead or supervisor wants is for the operator to receive a new job, scrap the written program, and start puzzling together a complex setup from scratch. Brakes take time to program; setting up a complex staged-bend sequence (a series of punches and dies next to each other) can take even longer.
Moreover, it’s very difficult for one person to start developing such a setup and then have another person finish it. Developing a complex setup requires complex thought processes, and each operator thinks differently. If an operator can’t finish developing a new setup, the next person (say, on the next shift) will probably just start over.
Even offline bend simulations aren’t perfect. They can create some incredibly complex stage-bending sequences in short order, which is fantastic for an operator who wants to get it all done in one setup. But because these sequences have so many moving parts, adjustments still need to happen.
In a lean press brake operation, those adjustments should happen in prototyping (technically more of a “challenging job tryout” or “preproduction” area than a true prototyping operation, but you get the idea). Sure, many small shops probably can’t afford to dedicate machinery to new jobs, but if a fabricator grows large enough, creating a separate department for prototyping, one-off, and nonrepeat low-volume work can make a world of sense.If a preproduction department isn’t feasible, try fitting new, challenging jobs into your capacity planning. Dedicate time that doesn’t cut into your regular production. This way, these challenging jobs won’t be a bump-on-a-log, stealing your bending capacity away from simpler bending work that could flow right through to the next operation.
Such a structure ideally would foster good communication among the company’s operators, programmers, and engineers. Simple part programs probably don’t need to be discussed and debated, of course. But when a programmer develops a difficult program offline, he or she can talk with the operators who will be running the part and listen to their feedback. This way, everyone is driving toward a common destination: for the first bent part to be a good part. Sure, it’s not always possible, but it’s certainly a worthy goal.
Pride and Workmanship
It’s no secret that operators tweak programs. Sometimes it’s absolutely necessary; the setup sheet might specify an incorrect tool, a radius that’s impossible to produce, or a bend sequence and tool setup that causes collisions.
Catching such problems in production is a bit like reactive maintenance. Just as machines break unexpectedly, badly specified jobs sometimes slip through. Again, these jobs shouldn’t tie up production but instead be pulled out of the schedule and moved to a more convenient time (like after or between shifts)—or, ideally, just moved to the preproduction department.
Sometimes an operator makes changes for other reasons. It could be to suit personal preferences, and this brings up a murky area. If you’re a highly skilled operator, you might feel that your preferences are truly best practices, and your changes are allowing parts to be formed faster and more consistently for everyone in the shop.
If you’re a supervisor or press brake lead person, you see the situation quite differently. If everyone is tweaking programs, the operation isn’t efficient. Too often the brakes sit idle as operators debate programs and tooling setups with their supervisors. Program changes during production add yet another variable in an already highly variable situation. An operator on one shift might feel his way is best and change a program, while an operator on another shift might not feel the same way and change it back.
Brake operators in job shops might run hundreds of different parts, which makes program changes even more chaotic. Consider an operator who wants to change a program for a certain job. The supervisor approves, documents the change, and creates the new work standard for that job. When the job comes up again six months later, the same operator wants to change the program again. The supervisor looks at his records and discovers that the operator now has changed the program to exactly the way it was before.
For parts in production, an operator really should never change a program. After all, changing programs at the machine negates the whole point of preparing programs ahead of time.
Still, why do operators want to make these changes? To find the answer, put yourself in the operators’ shoes. Think about why your best operators got interested in the press brake in the first place. It’s one of the most complex operations in metal fabrication, and good operators thrive on that complexity. Some might see a blank fold up in their head, and they’ll jump at the chance to change a bending sequence or tooling setup to an arrangement that, in their opinion at least, is better.
They enjoy puzzling together a good setup. In truth, it’s the best part of their day. They didn’t become press brake operators to pull up a program, load tools, and run part after part after part, all day every day.
Pride in their work comes from solving problems at the press brake. A skilled operator’s best day happens when he or she tackles what the boss says is an impossible job and, against all odds, makes it possible. (And let’s be honest, proving the boss wrong is an added benefit.) That’s a feather in the operator’s cap. He’s proud, and his boss is proud. Every time the operator solves a difficult problem, he becomes a better press brake operator.
But up in production management, the headaches ensue. Sure, an operator made the impossible possible, but in doing so, he just made four or five other jobs late.
Skilled operators thrive on variety, and most custom fabricators have plenty to give them. But that variety needs structure. Customers don’t pay for the time operators spend piecing together the perfect brake setup; they pay for quality parts delivered on time.
Fabricators absolutely need those technical experts who can look at a sheet metal part or setup sheet and develop a better way. This is where designating a preproduction area can help. And even if a preproduction department isn’t practical, a fabricator can still schedule time to allow operators to work on challenging jobs.
Of course, some weeks might be full of higher-volume production work or large rush orders, which could mean all-hands-on-deck, requiring everyone available to churn out part after part after part. Most people don’t enjoy every aspect of their job all the time, and press brake operation is no different.
But most of the time, if they have the skill and desire, operators could spend some of the week working on new or difficult jobs—again, outside of production. They also could suggest better practices for current production jobs. Again, this would be outside of production and in communication with all operators on every shift who run that job, so everyone is on the same page. If everyone agrees a new brake setup would be better, the supervisor could make the change. But it’s all done using a defined process, not on-the-fly during production.About Time
Finally, a disclaimer: There is no one-size-fits-all solution in metal fabrication. A shop’s best practices depend on a host of factors, so please use these suggestions as thought-starters for your own operation.
One constant, though, is time. If a job takes more time, it costs more. The less time it takes for an order of quality products to appear on the customer’s receiving dock, the better.
To that end, lean tools like 5S and standard work instructions can help. But controlling the flow and quality of information—between engineering, programming, and the shop floor—is just as critical.
Larry Boden is press brake tooling specialist for Mate Precision Tooling, 1295 Lund Blvd., Anoka, MN 55303, 763-421-0230, www.mate.com.
Engineering Cheat Sheet
What follows is a hypothetical cheat sheet an engineering department might use for bending. In reality, what exactly to include depends on shop practices, bending technology, material, and the product mix. In this shop, for instance, we’re assuming that the bending department performs air bending only, not bottoming or coining.
Engineers probably won’t use all these formulas. For example, these days software takes care of most bend calculations using time-tested k-factor values. But the formulas show how the inside bend radius (Ir) fits into the larger picture. Change the Ir, and you change everything.
The document is not set in stone, either. For instance, engineers might update percentages to predict the Ir based on the material the shop uses.
About the Author
Related Companies
subscribe now
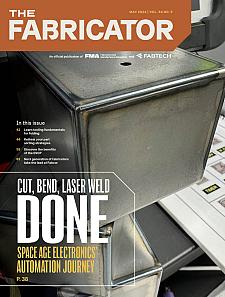
The Fabricator is North America's leading magazine for the metal forming and fabricating industry. The magazine delivers the news, technical articles, and case histories that enable fabricators to do their jobs more efficiently. The Fabricator has served the industry since 1970.
start your free subscription- Stay connected from anywhere
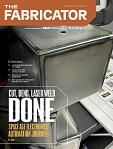
Easily access valuable industry resources now with full access to the digital edition of The Fabricator.
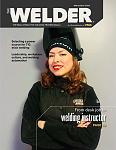
Easily access valuable industry resources now with full access to the digital edition of The Welder.
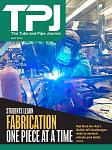
Easily access valuable industry resources now with full access to the digital edition of The Tube and Pipe Journal.
- Podcasting
- Podcast:
- The Fabricator Podcast
- Published:
- 04/16/2024
- Running Time:
- 63:29
In this episode of The Fabricator Podcast, Caleb Chamberlain, co-founder and CEO of OSH Cut, discusses his company’s...
- Trending Articles
Tips for creating sheet metal tubes with perforations
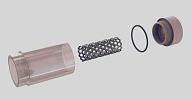
Are two heads better than one in fiber laser cutting?
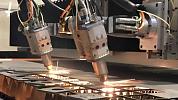
Supporting the metal fabricating industry through FMA
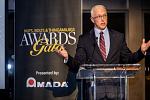
JM Steel triples capacity for solar energy projects at Pennsylvania facility
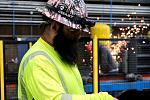
Omco Solar opens second Alabama manufacturing facility
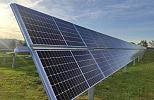
- Industry Events
16th Annual Safety Conference
- April 30 - May 1, 2024
- Elgin,
Pipe and Tube Conference
- May 21 - 22, 2024
- Omaha, NE
World-Class Roll Forming Workshop
- June 5 - 6, 2024
- Louisville, KY
Advanced Laser Application Workshop
- June 25 - 27, 2024
- Novi, MI