Contributing editor
- FMA
- The Fabricator
- FABTECH
- Canadian Metalworking
Categories
- Additive Manufacturing
- Aluminum Welding
- Arc Welding
- Assembly and Joining
- Automation and Robotics
- Bending and Forming
- Consumables
- Cutting and Weld Prep
- Electric Vehicles
- En Español
- Finishing
- Hydroforming
- Laser Cutting
- Laser Welding
- Machining
- Manufacturing Software
- Materials Handling
- Metals/Materials
- Oxyfuel Cutting
- Plasma Cutting
- Power Tools
- Punching and Other Holemaking
- Roll Forming
- Safety
- Sawing
- Shearing
- Shop Management
- Testing and Measuring
- Tube and Pipe Fabrication
- Tube and Pipe Production
- Waterjet Cutting
Industry Directory
Webcasts
Podcasts
FAB 40
Advertise
Subscribe
Account Login
Search
Growing solar market rife with stamping opportunities
- By Kate Bachman
- May 24, 2017
- Article
- Bending and Forming
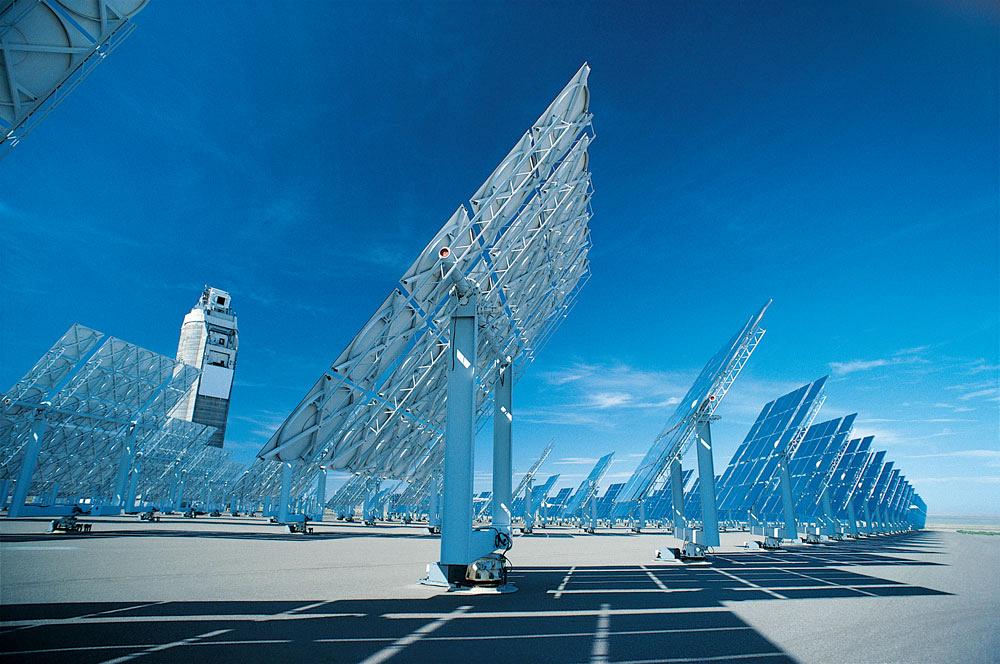
Often perceptions of solar energy manufacturing focus on the silicon materials but neglect to consider all of the metal—and metal fabrications—that frame and support them. Photo courtesy of Getty images.
The solar energy market offers sunny opportunities for stamping manufacturers, despite dissipated support from the new administration.
Corporate demand, rather than state mandates, has become the top driving force behind solar and wind energy growth in the U.S., reported Moody’s Investors Service. Corporations agreed to buy nearly 3 gigawatts (GW) of power generated by clean energy projects in 2015, and another 2.5 GW in 2016, according to Bloomberg New Energy Finance (see Figure 1).
Solar Metal Fabrications
Types of stamped and metal fabricated parts needed for solar power systems include:
Solar Photovoltaic (electric):
- Aluminum frames
- Posts
- Trackers
- Bracketry
- Standard electric components, connectors
- Inverter, controller enclosures
Stamper Prospers Under Solar
Stamping manufacturer Talan Products, Cleveland, has doubled its solar energy components business every year since 2014, according to CEO Steve Peplin. “Last year it was half of what it was this year, and that was half of what it was the year before. That rate of growth is holding.” He added, “The solar industry is growing very fast.”
One reason the stamper has realized so much business activity stamping solar power components is that it is helping to lower the cost of solar power—in turn, increasing its demand and accelerating its growth.
Peplin said that the stamping process is inherently one of the best ways to reduce part costs for high volumes. “Stamping using progressive die tooling is the most common way that we take cost out of high-volume production.” He said that because stamping is suited for high production volumes, it helps realize economies of scale.
Another reason stamping can wring costs out of solar energy components is that it produces parts less expensively, per piece in high volumes, than other methods such as casting, forging, laser cutting or turret punching, and press brake bending.
“Usually if you can take a part that was a casting or a forging and re-engineer it into a stamping, you can take costs out,” Peplin said. Many solar power parts are aluminum components. Often they are extrusions. “We converted a simple bracket that had machined holes and slots into a stamping. Huge savings. We saved 50 percent for our customer on that part.”
Peplin cited the practice of design for manufacturability as “another arrow in our quiver to help our customer lower the cost of solar power parts.” By doing concurrent engineering, by collaborating with the customer, stampers can pull costs out without compromising performance. “It might involve some other methods. It might involve removing some welding or doing automated assembly.”
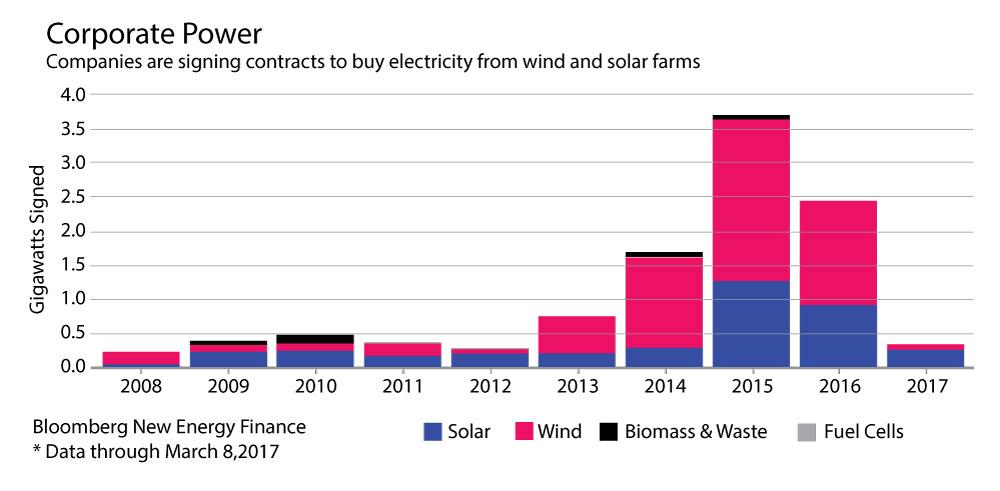
Figure 1
Corporations, rather than utilities, will drive solar growth, according to Bloomberg New Energy Finance. Graph courtesy of Bloomberg.
Some approaches to reducing costs have seemed counterintuitive, Peplin said. “Usually if you can get rid of welding, you can take cost out. But in one recent case, we took the opposite approach to save costs.”
The part was for a large tracker assembly for a utility-scale installation. A solar tracking assembly allows the solar modules to tilt to “follow” the sun from east to west to capture more solar radiation and generate more electricity.
“Solar fields are rough. They’re an outdoor environment and the ground is uneven, so the bracket assembly has to accommodate variations in terrain. We worked really closely with our customer as they were designing a complicated bracket assembly. By actually breaking down this complex system into three simple parts and welding them together, we were able to save enough material to offset the cost of the welding. It is kind of unusual. But these were big, heavy ¼-inch-thick structural brackets, so when you save a little material, you save a lot. We’re talking dollars of savings on a $40 assembly, not pennies,” he added.
Peplin said that as the costs of solar power drop, demand rises—which is good news for his bottom line. “There’s a huge cost pressure down. Solar is doubling in size because costs are lowering.
“Economies of scale is a huge driver. So is the methodology—going from machining or casting to stamping; design for manufacturability; and economies of scale derived from progressive die stamping vesus fabricated … all of those are driving the cost of solar down.
Peplin said that because the solar industry still is relatively new, some risk is expected. “There are a lot of startups, so there’s some risk. Initially, with some of them, we thought, ‘Are these guys going to make it?’ Well, now they’re really successful companies. One of our biggest solar customers is just south of $1 billion and they’re only 8 years old.”
Solar Business, Jobs
In 2016, 260,077 Americans were employed by the solar industry—a 25 percent increase over 2015—including 38,121 in the manufacturing segment, according to The Solar Foundation, solarjobscensus.org (see Figure 2). In fact, solar industry jobs have increased more than 20 percent per year for the past four years, the organization said.
China to Increase Solar Manufacture, Use
U.S. manufacturers might lose out on opportunities in the industry in the face of global competition, however. China intends to spend more than $360 billion through 2020 on renewable power sources like solar and wind, the government’s energy agency said, according to a New York Times Jan. 5, 2017, article by Michael Forsythe.
“The country’s [China’s] National Energy Administration laid out a plan to dominate one of the world’s fastest-growing industries, just at a time when the U.S. [under President Trump] is set to take the opposite tack,” Forsythe wrote.
The agency said in a statement that China would create more than 13 million jobs in the renewable energy sector by 2020.
Talan Products, 216-458-0170, www.talanproducts.com
About the Author
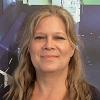
Kate Bachman
815-381-1302
Kate Bachman is a contributing editor for The FABRICATOR editor. Bachman has more than 20 years of experience as a writer and editor in the manufacturing and other industries.
subscribe now
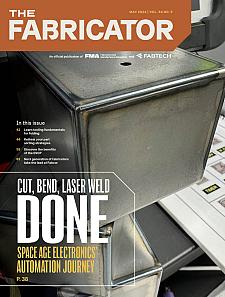
The Fabricator is North America's leading magazine for the metal forming and fabricating industry. The magazine delivers the news, technical articles, and case histories that enable fabricators to do their jobs more efficiently. The Fabricator has served the industry since 1970.
start your free subscription- Stay connected from anywhere
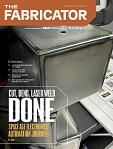
Easily access valuable industry resources now with full access to the digital edition of The Fabricator.
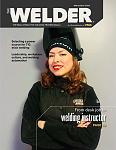
Easily access valuable industry resources now with full access to the digital edition of The Welder.
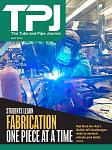
Easily access valuable industry resources now with full access to the digital edition of The Tube and Pipe Journal.
- Podcasting
- Podcast:
- The Fabricator Podcast
- Published:
- 04/16/2024
- Running Time:
- 63:29
In this episode of The Fabricator Podcast, Caleb Chamberlain, co-founder and CEO of OSH Cut, discusses his company’s...
- Trending Articles
Tips for creating sheet metal tubes with perforations
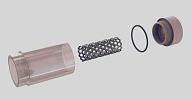
Supporting the metal fabricating industry through FMA
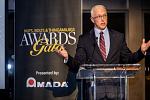
JM Steel triples capacity for solar energy projects at Pennsylvania facility
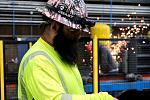
Fabricating favorite childhood memories
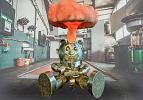
Omco Solar opens second Alabama manufacturing facility
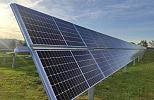
- Industry Events
16th Annual Safety Conference
- April 30 - May 1, 2024
- Elgin,
Pipe and Tube Conference
- May 21 - 22, 2024
- Omaha, NE
World-Class Roll Forming Workshop
- June 5 - 6, 2024
- Louisville, KY
Advanced Laser Application Workshop
- June 25 - 27, 2024
- Novi, MI