Contributing editor
- FMA
- The Fabricator
- FABTECH
- Canadian Metalworking
Our Publications
Categories
- Additive Manufacturing
- Aluminum Welding
- Arc Welding
- Assembly and Joining
- Automation and Robotics
- Bending and Forming
- Consumables
- Cutting and Weld Prep
- Electric Vehicles
- En Español
- Finishing
- Hydroforming
- Laser Cutting
- Laser Welding
- Machining
- Manufacturing Software
- Materials Handling
- Metals/Materials
- Oxyfuel Cutting
- Plasma Cutting
- Power Tools
- Punching and Other Holemaking
- Roll Forming
- Safety
- Sawing
- Shearing
- Shop Management
- Testing and Measuring
- Tube and Pipe Fabrication
- Tube and Pipe Production
- Waterjet Cutting
Industry Directory
Webcasts
Podcasts
FAB 40
Advertise
Subscribe
Account Login
Search

Kate Bachman
815-381-1302
Kate Bachman is a contributing editor for The FABRICATOR editor. Bachman has more than 20 years of experience as a writer and editor in the manufacturing and other industries.
-
- From The Fabricator
Engineering and fabricating a one-of-a-kind bridge to span the Mississippi River
- By Kate Bachman
- Aug 10, 2023
- Plasma Cutting
- Article
Industrial Steel Construction fabricated the steel components and assemblies for a new arched bridge between Iowa and Illinois.
-
- From The Fabricator
Industry insights to efficient holemaking in metal plate: laser, plasma, or drilling
- By Kate Bachman
- May 11, 2023
- Punching and Other Holemaking
- Article
Three metal fabricators—SCW Contracting Corp., H&H Metals, and Ultratech Tool and Design—share their go-to holemaking approaches and why those methods are the best for their applications.
-
- From The Fabricator
Hear from experts at Manufacturing in an EV World Conference
- By Kate Bachman
- May 3, 2023
- Electric Vehicles
- Blog Post
The 2023 Manufacturing in an EV World Conference features experts and panel discussions on how electric vehicle production is shaping the future of metal forming.
Mejoras en el doblado de paneles ayudan a los fabricantes con la escasez de mano de obra
- By Kate Bachman
- Apr 3, 2023
- Bending and Forming
- Article
Las actualizaciones en la tecnología de doblado de paneles amplían los tipos de perfiles, tamaños y rangos de componentes que se pueden doblar, automatizar los aspectos de manejo de materiales, aumentar el número de herramientas que se pueden almacenar en la máquina, y mejorar la consistencia de la primera pieza buena.
-
- From The Fabricator
Tier 1 masters massive stampings with 3,000-tonne press
- By Kate Bachman
- Mar 30, 2023
- Bending and Forming
- Article
Martinrea’s fast-growing plant in Hopkinsville, Ky., needed to expand press capacity, so it installed two large mechanical transfer presses and built a new building to house them.
-
- From The Fabricator
Achieving sharp bends in aluminum with the right tooling
- By Kate Bachman
- Mar 10, 2023
- Bending and Forming
- Article
Fabricating aluminum brings with it a few challenges unique to bending and forming—getting sharp bends without cracking, reducing or eliminating galling, and preventing marking. Three press brake bending experts offer their assistance.
-
- From The Fabricator
Prototyper proves to be missing link for tooling manufacturer
- By Kate Bachman
- Feb 16, 2023
- Bending and Forming
- Article
Tooling Systems Group, Grand Rapids, Mich., was encountering situations where it lost out on some projects because it did not have prototyping expertise and capabilities in-house, so it acquired Auto Metal Craft, Oak Park, Mich.
-
- From The Fabricator
Small California metal fabrication shop provides props for Hollywood
- By Kate Bachman
- Feb 12, 2023
- Waterjet Cutting
- Article
A small metal fab shop in North Hollywood that usually supplies the aerospace industry occasionally gets the chance to supply props and parts to the motion picture industry.
-
- From The Fabricator
Panel bending upgrades aid metal fabricators with labor shortages
- By Kate Bachman
- Jan 12, 2023
- Bending and Forming
- Article
Panel benders were developed to reduce labor requirements by simplifying bending. Upgrades in the technology expand the types of components that can be bent, automate material handling, and improve consistency.
-
- From The Fabricator
Things that come not back and squaring the ones that can in metal stamping
- By Kate Bachman
- Jan 5, 2023
- Bending and Forming
- Blog Post
STAMPING Journal Editor Kate Bachman dwells on the need for restraint, and also for taking action in the metal stamping sector, based on the Arabian proverb, "Four things come not back—the spoken word, the sped arrow, the past life, and the neglected opportunity.”
-
- From The Fabricator
Smart inspection planning boosts quality without slowdown
- By Kate Bachman
- Dec 3, 2022
- Manufacturing Software
- Article
Smart inspection planning allows metal stamping operations to boost quality without slowing down the process. Using deep learning, 3D imaging, novel algorithms, and intelligent robotic planning technologies for single-part inspection, vision systems can ensure that only defect-free parts make it off the line.
-
- From The Fabricator
Workforce training and automation, recurrent interwoven themes at FABTECH 2022
- By Kate Bachman
- Nov 30, 2022
- Automation and Robotics
- Blog Post
Workforce training and automation in manufacturing were recurrent and interwoven themes at FABTECH 2022 in Atlanta. In the stamping and metalforming area, several of the technological advancements exhibited there are intended to either support a human workforce or reduce the reliance on it.
-
- From The Fabricator
Notable quotes via CAR MBS 2022, Part II
- By Kate Bachman
- Nov 16, 2022
- Electric Vehicles
- Blog Post
With automakers selling out their electric vehicles on reserve in a matter of hours, and the data showing battery-electric vehicles reaching 10% of the worldwide auto market in July, clearly the auto industry is at the tipping point for the move to vehicle electrification. The transition’s effect on suppliers was dissected at this year’s CAR MBS. Here are the GM, BorgWarner, and ABS panelists’ quotes, verbatim:
-
- From The Fabricator
Privately held Ohio metal fabrication shop goes employee-owned
- By Kate Bachman
- Nov 14, 2022
- Shop Management
- Article
When Valco Industries owner Ed Leventhal was mapping his exit plan, he took the road less traveled to ensure that his valued manufacturing employees would continue to have jobs by transferring ownership to them.
-
- From The Fabricator
Horseshoes proving to be good luck for British metal artist
- By Kate Bachman
- Nov 3, 2022
- Arc Welding
- Article
When British artist William Moulton-Day sees a horseshoe, he sees a part for a welded sculpture to grace an English country-style garden. His work is progressing at “an alarming rate.”
- Podcasting
- Podcast:
- The Fabricator Podcast
- Published:
- 04/16/2024
- Running Time:
- 63:29
In this episode of The Fabricator Podcast, Caleb Chamberlain, co-founder and CEO of OSH Cut, discusses his company’s...
- Trending Articles
Tips for creating sheet metal tubes with perforations
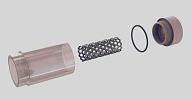
Are two heads better than one in fiber laser cutting?
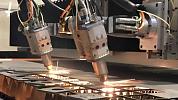
Supporting the metal fabricating industry through FMA
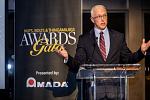
JM Steel triples capacity for solar energy projects at Pennsylvania facility
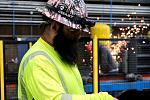
Zekelman Industries to invest $120 million in Arkansas expansion
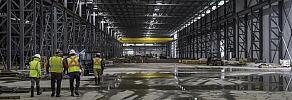
- Industry Events
16th Annual Safety Conference
- April 30 - May 1, 2024
- Elgin,
Pipe and Tube Conference
- May 21 - 22, 2024
- Omaha, NE
World-Class Roll Forming Workshop
- June 5 - 6, 2024
- Louisville, KY
Advanced Laser Application Workshop
- June 25 - 27, 2024
- Novi, MI
- Upcoming Webcasts
Navigating Change: The Manufacturer’s Guide to Change Management with ERP Implementation
- May 16, 2024
- Sponsored
- Presented By: ECI Software Solutions, M1