- FMA
- The Fabricator
- FABTECH
- Canadian Metalworking
Categories
- Additive Manufacturing
- Aluminum Welding
- Arc Welding
- Assembly and Joining
- Automation and Robotics
- Bending and Forming
- Consumables
- Cutting and Weld Prep
- Electric Vehicles
- En Español
- Finishing
- Hydroforming
- Laser Cutting
- Laser Welding
- Machining
- Manufacturing Software
- Materials Handling
- Metals/Materials
- Oxyfuel Cutting
- Plasma Cutting
- Power Tools
- Punching and Other Holemaking
- Roll Forming
- Safety
- Sawing
- Shearing
- Shop Management
- Testing and Measuring
- Tube and Pipe Fabrication
- Tube and Pipe Production
- Waterjet Cutting
Industry Directory
Webcasts
Podcasts
FAB 40
Advertise
Subscribe
Account Login
Search
How servo presses work with advanced high-strength steel (AHSS)
By supporting lightweighting, servos allow operator to work with material
- By Masa Sakoda
- August 26, 2021
- Article
- Bending and Forming
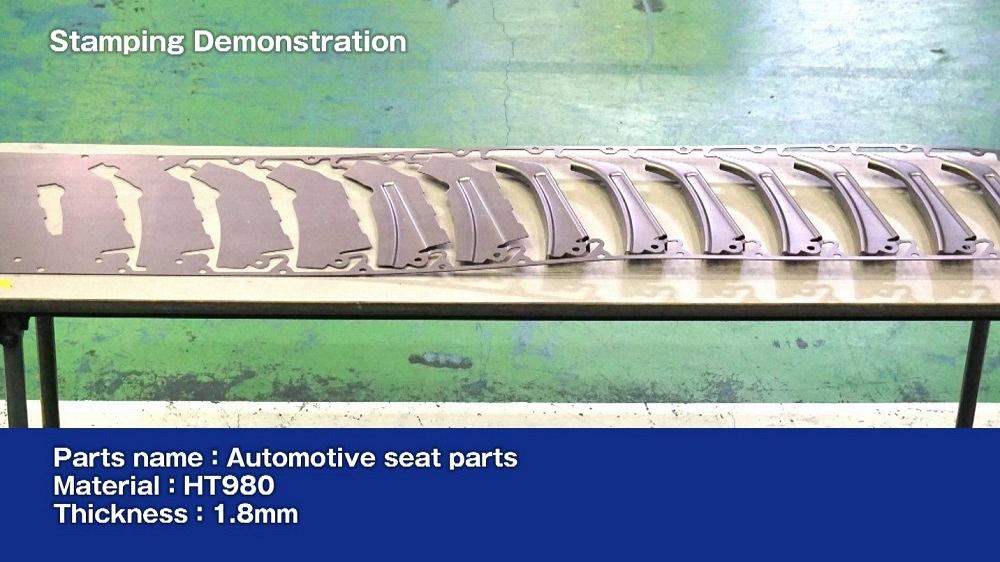
An automotive seat part is formed from a progressive die strip constructed of 1.8- mm-thick HT980 AHSS material.
The term lightweighting seems to be the new buzzword in manufacturing for most industries today. The goal to reduce product weight accomplishes two key objectives. First, less energy is needed to move the resulting lighter product, usually a vehicle, and, second, it requires fewer resources to manufacture the product.
However, though lighter and perhaps thinner than it was originally designed to be, the material cannot compromise the product’s strength specified for the application. In the stamping world, this has resulted in new generations of high-strength materials such as advanced high-strength steel (AHSS), high-strength aluminum alloys, and new specialty metals that handle more heat and shock.
The demand for better fuel economy and the advent of electric vehicles in the auto industry may have started the lightweighting trend, but most industries are following suit to take advantage of the benefits. Stampers should prepare for broad use of high-strength materials.
Tougher Materials Need Gentler Forming
The first variable is the energy and force (tonnage) needed to deform the material. The next is the application for how the part is to be produced. This includes how the part will move through the press (progressive, transfer, or manual) and the corresponding tooling design itself. Different methods exist to make the same part, and the tooling design and application method are key factors.
Third, the machine specifications to run the application must be determined. The machine—whether it is a stamping press, coil line, or other automated system—needs to summon not just the energy needed to produce the part, it must also be designed to handle the higher stresses that these high-strength materials place on the machine’s components.
Unfortunately, many people only consider the energy/tonnage needed and assume that since the material is lighter or thinner, stress loads on the equipment will be less; in fact, the reverse is true.
Servo Presses Work With Materials
Servo press technology offers many benefits for working with these new materials. In short, servo presses allow the operator to work with the material rather than work the material.
Working with the material means having the ability to program and control slide velocity and dwell anywhere in the working part of the stroke. This can provide higher part quality and longer die life. Both speed and dwell depend on the application, tooling design, and material’s chemistry.
Being able to control velocity right at the point where the punch begins to work the material minimizes friction (heat buildup), reduces snap-through (reverse loading), and is key to minimizing the lateral movement of the punch—which can extend die life.
Furthermore, controlling velocity in a shallow draw or form operation allows some of these materials to flow more evenly. The velocity can be slowed to a constant speed or progressively slower through the form, based on the material characteristics. The available energy output of the press needs to meet the application requirements at this reduced velocity.
Most servo presses are equipped with a pendulum mode. As the name implies, the slide moves in a back-and-forth continuous motion like a clock pendulum, rather than a full 360-degree rotation. Because the starting and stopping positions of the stroke are programmable, much higher speeds can be attained than with a full rotation—and at the same motor speed. However, the faster the production speed, the quicker the energy is consumed by the motor. Increasing the start/stop/reverse operation of the servomotor results in heat buildup.
Cooling Systems Counter Detrimental Effects of Heat
The Achilles’ heel of any servomotor is heat; heat is energy that cannot be used in the production of the part and is wasted. Because heat is a common byproduct of higher pendulum speeds, it needs to be addressed.
Some servo presses are equipped with a multitude of fans surrounding the motor engineered to dissipate the heat. Alternatively, they simply have ambient cooling of the motor and capacitor banks. This heat is wasted energy that is transferred to the surrounding environment.
Other servo presses use forced liquid cooling to manage the heat of the motor and capacitor banks in the control cabinets. Forced liquid cooling to manage the heat provides more usable energy in the die space for that work.
The ambient or air-cooled servo designs have lower rating points and less available energy at the higher pendulum speed compared to the liquid-cooled designs. This is especially important with the newer materials that require more energy to form the part profiles needed.
Flexibility Prepares the Way Forward
The chemistries of these new ultrahard materials require more flexibility in stamping applications. If the press design allows for the higher stresses produced working with these new materials rather than the conventional materials, servo press technology can offer all the benefits of programmable velocity, including dwell if needed, throughout the stroke and high pendulum speeds with more energy available to work at these speeds. And these features can be combined in any application, allowing high pendulum speeds along with programmed reduced velocity in the working part of the stroke.
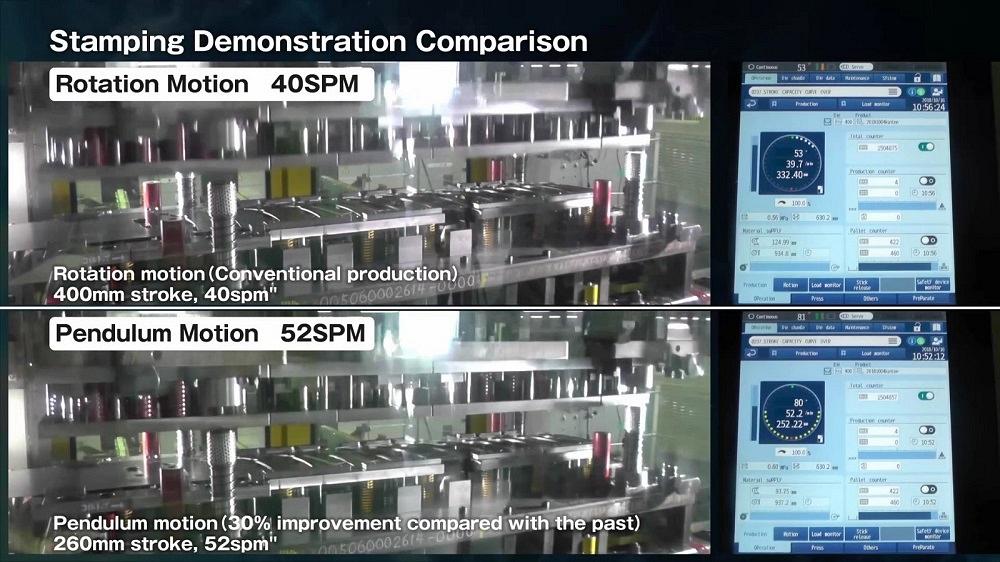
Running a part in pendulum mode, in which the slide travels only slightly before and beyond the BDC rather than completing a full 360-degree rotation, can save time, increasing the strokes per minute by 30%.
If the application requires an emboss or other defined profile, sometimes a momentary dwell of less than a second can set that profile. It may even eliminate a restrike station or secondary operation.
As materials change, manufacturing processes must change with them. This includes not only the tooling and application methods, but the stamping press itself. It needs to be engineered to handle the increasing energy demands and increasing loads that ultrahigh-strength materials create.
Investing in flexible equipment today is the best guarantee for longevity in the future.
About the Author
Masa Sakoda
8770 W. Bryn Mawr Ave., Ste. 100
Chicago, IL 60631
(847) 437-5800
Related Companies
subscribe now
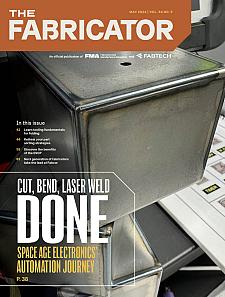
The Fabricator is North America's leading magazine for the metal forming and fabricating industry. The magazine delivers the news, technical articles, and case histories that enable fabricators to do their jobs more efficiently. The Fabricator has served the industry since 1970.
start your free subscription- Stay connected from anywhere
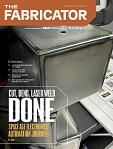
Easily access valuable industry resources now with full access to the digital edition of The Fabricator.
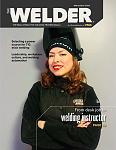
Easily access valuable industry resources now with full access to the digital edition of The Welder.
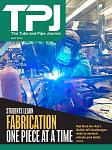
Easily access valuable industry resources now with full access to the digital edition of The Tube and Pipe Journal.
- Podcasting
- Podcast:
- The Fabricator Podcast
- Published:
- 04/16/2024
- Running Time:
- 63:29
In this episode of The Fabricator Podcast, Caleb Chamberlain, co-founder and CEO of OSH Cut, discusses his company’s...
- Industry Events
16th Annual Safety Conference
- April 30 - May 1, 2024
- Elgin,
Pipe and Tube Conference
- May 21 - 22, 2024
- Omaha, NE
World-Class Roll Forming Workshop
- June 5 - 6, 2024
- Louisville, KY
Advanced Laser Application Workshop
- June 25 - 27, 2024
- Novi, MI