Contributing editor
- FMA
- The Fabricator
- FABTECH
- Canadian Metalworking
Categories
- Additive Manufacturing
- Aluminum Welding
- Arc Welding
- Assembly and Joining
- Automation and Robotics
- Bending and Forming
- Consumables
- Cutting and Weld Prep
- Electric Vehicles
- En Español
- Finishing
- Hydroforming
- Laser Cutting
- Laser Welding
- Machining
- Manufacturing Software
- Materials Handling
- Metals/Materials
- Oxyfuel Cutting
- Plasma Cutting
- Power Tools
- Punching and Other Holemaking
- Roll Forming
- Safety
- Sawing
- Shearing
- Shop Management
- Testing and Measuring
- Tube and Pipe Fabrication
- Tube and Pipe Production
- Waterjet Cutting
Industry Directory
Webcasts
Podcasts
FAB 40
Advertise
Subscribe
Account Login
Search
Hydraulic presses progress with 100-year-old stamper
Attleboro, Mass.-based company draws fire extinguishers as deep as its century-long evolution
- By Kate Bachman
- February 4, 2021
- Article
- Bending and Forming
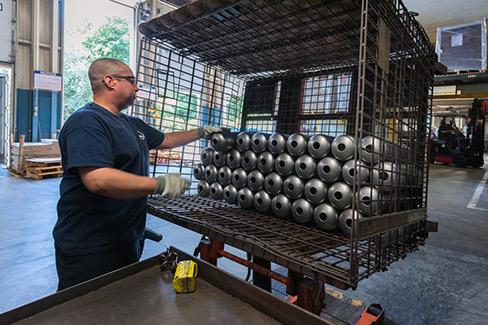
The deep drawn shells for fire extinguisher canisters must meet strict UL requirements for wall thicknesses in pressure vessels. Images provided by Larson Tool & Stamping
Centenarian Larson Tool & Stamping, Attleboro, Mass., has been deep drawing cylindrical canisters for a fire extinguisher manufacturer for more than 50 years, as well as producing many other stampings.
The manufacturer has been using hydraulic presses to draw the canisters since the early 1980s and has upgraded its hydraulic transfer press lines four times since. With each successive press system installation, the company has marked hydraulic press technology’s evolution over the years—and improved the company’s process and products.
Vice President and Director of Engineering Ray Niquette said that when he started working at Larson Tool & Stamping, the fire extinguisher cylinders were deep drawn in mechanical presses to perform the blanking, drawing, and redrawing. But deep drawing on mechanical presses required very high press tonnages. “That’s because the load at which you’re applying the forces on the material are so high in the stroke, you have to dramatically oversize the pressure size and capacity just to have that tonnage and energy needed for the extreme drawing process.”
The other problem the company had with using mechanical presses for deep drawing is that the ram velocity is highest at bottom dead center. “That’s backward of what you need for deep draw work. You really want to approach the material slowly, get it to start flowing, then drive through and finish the part,” Niquette said.
The press feeds and press-to-press transfers were being done manually.
Five Generations of Hydraulic Press Systems
Each time the company purchased a new hydraulic press system, it capitalized on updated technology.
First Gen. In the mid-‘80s, the stamper installed hydraulic presses to perform the deep draws because of their ability to apply consistent load throughout the linear stroke of the press. “So then we could optimize pressure and speed,” said Niquette. “Forming with hydraulics was so much smoother and neater.” The company incorporated a transfer system and retrained its operators so that two could run the press line instead of five. “Basically it’s multiple presses on one platen,” he commented.
“In the beginning, we looked at the hydraulic presses as single-action presses. We had to create the hold-down pressure externally using air cushions.” The draw punch’s shaft came down through an outer and inner seal, a large donut air cylinder that sealed around the shaft to generate the hold-down pressure. “You can imagine, using just regular shop air at 100 PSI, the diameter of the cylinder we had to have to generate the tonnage we needed to hold down that material and keep it from wrinkling. They were pretty good-sized air cylinders. And then of course the seals would wear, so they were problematic,” Niquette said.
A press-to-press transfer system was incorporated into the first hydraulic press line, but it was more of a mechanical transfer system. “It was the type commonly used in the ‘80s,” he said.
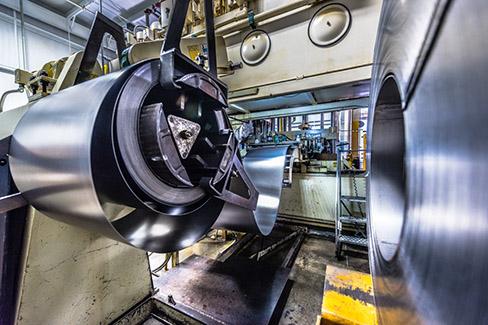
Larson Tool & Stamping has been using hydraulic presses to deep draw fire extinguisher canisters since the early 1980s and has upgraded its hydraulic transfer press lines four times since.
“Basically it’s multiple presses on one platen, if you will,” Niquette explained. “There’s one big slab of steel where all the tools and transfer system are mounted so it’s a stable platform, and then the individual four-post presses doing redraws are mounted to that one main plate.”
The system has a PLC but it is a push-button type control, he relayed. “The control console for that was very big, with multiple push-buttons with idiot lights to show what was running and what was not.”
Second Gen. Larson Tool & Stamping holds several patents and has invented numerous products, including the Ing shovel, a single-serve freon tank, a furnace brazing process, and the widely used spin-on oil filters.
It was while helping a customer improve its fire extinguisher from a two-piece to a one-piece design that Larson upgraded its hydraulic presses. The canister’s original two-piece design had a seam that caused water to collect at the bottom, rusting it out.
“Going from the two-piece to the one-piece shell really pushed us to upgrade. It required a whole other level of control,” Niquette said.
“So when we specified the next generation of hydraulic presses, we said, ‘Well why can’t we have a second ram with another set of hydraulic cylinders so that the first one comes down to hold that material and the second one does the drawing?’ That is what drove us to get into the double-action machines.”
The next generation of hydraulic presses in 1992 were all custom built, with double-action slides, a more sophisticated control, and automated transfer systems.
The double-action ram doubled the complexity of the press system, Niquette said. “So now, the light bulb starts brightening, and we started really looking closely at how to use our hydraulic system better.”
The second generation of presses were equipped with a servo motor to drive the transfer using pneumatic grippers. “It allowed us much more flexibility,” he said.
The line was not optimized for the smaller canisters, however. The press line was equipped to draw a couple of different sizes of cylinders, but its speed was limited because it had to be slow enough and powerful enough to draw the largest shell.
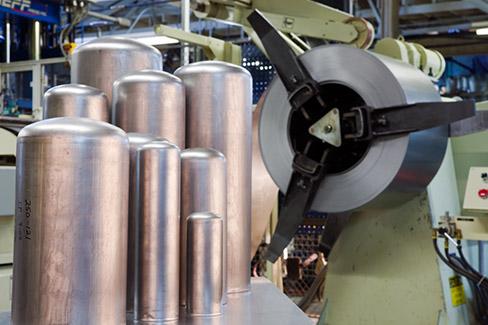
It was while helping a customer convert its fire extinguisher design from a two-piece to a one-piece design that Larson Tool & Stamping decided it had to upgrade its hydraulic presses.
Third Gen. The third generation of hydraulic presses were optimized for a smaller 5-in.-dia. by 17-in.-tall shell to maximize speed and productivity. “We found that we could do the smaller one a lot faster and cheaper on the new line,” Niquette said.
“There again, we took the press design a little further, with fewer mechanical stops on it and more reliance on the servo technology and linear transducers on the PLC.” The linear transducers allowed the operators to control the hydraulic pressures for the length and the speed of the stroke, and they could get more control over the material flow. “It made it a much faster and more reliable process, and that resulted in more accuracy of the shell’s wall thickness.”
That is important because although each batch of material comes within the tolerance range, there is always some variation. “So with the more sophisticated servo controls, we can adjust speed and stroke specifically for that batch of material,” Niquette said.
Fourth Gen. The next-generation hydraulic transfer press line was installed for one of the smaller fire extinguisher shells that Larson produces. “The volumes for those were getting a lot higher. Our customer said that they could sell a lot more of this small one if we could redesign it as a one-piece, which would make it cheaper,” explained Niquette.
The company hadn’t automated the press line for that size vessel at all. “It was still a hand-fed, press-to-press mechanical line. We ran the numbers and saw the payback of investing in a new hydraulic press line that could draw that smaller shell,” he said.
The fourth generation used a little more servo technology, with more use of linear transducers and servo valves that facilitate varying the flow of the hydraulics, which govern the speed of the press. “So the operator can throttle down the speed with the servo valves, put the power where it is needed, and back off where it isn’t. He can dial in the hold-down pressures as well.”
That enhances product quality because the process is more tolerant of material quality variation, Niquette said.
The new system came with its own challenges in terms of how to manage a small-diameter, 1-ft.-high shell. On the upside, the press line was able to be much more compact because of the small size of the part.
The biggest change from the previous press generation was simply the physical size of the press line. Floor space was restricted, so the company wanted it more compact to fit into a small footprint. “We designed the press line with fewer and shared guide posts within the whole press line, complete with a cleaning line. Instead of one long linear line, it is shaped in a big U,” Niquette said.
As a result of the compact footprint, the same operator who loads the coil and feeds it into the press packs the shells right off the press, and then in a stretch wrapper for shipping. They can observe and control the press line remotely from the inspection station.
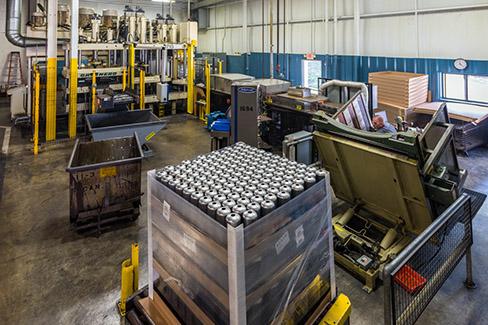
The second-generation press system was a double-acting blank and draw press equipped with a second ram and another set of hydraulic cylinders so that the first one comes down to hold that material and the second one does the drawing.
Fifth Gen. The last-generation hydraulic press line Larson installed exhibited the smallest number of upgrades, Niquette relayed. “It was designed to replace the first, original line from the ‘80s for large shells, which was finally getting long in the tooth and showing its limitations. But we took advantage of all the technology improvements and worked them into the press line.” The incremental upgrades increased productivity, reliability, and shell quality.
Because of the plant space constrictions, the line was installed as a U-shaped cell that could be run by one operator.
Severe Deep Drawing Challenges
Drawing pressure vessels three or more times as deep as their diameters comes with a unique set of challenges, which is why it is so important to have reliable control over the hold-down pressure, tonnage, material flow, force, energy, and length and the speed of the stroke. “The right material is really critical to our ability to be able to draw to the diameter and depth that we do today,” said Sales and Marketing Manager Neil Fonger, who also has served as both production manager and tooling manager.
Wall Thickness. First, because the canisters are pressure vessels vulnerable to explosion, they must meet UL service pressure standards for minimum wall thickness and performance, as well as the customer’s requirements. “The extinguisher’s wall thicknesses is gated by the UL requirement for service pressure. You see that on the extinguisher’s dial pressure gauge in a green window. And from that service pressure, there are certain calculations that you do for the minimal wall requirements. So that’s where we start,” Fonger said.
Larson Tool & Stamping must proof-test the shells multiple times at several working pressures and test to failure. The canister must fail in the sidewall above a certain minimum pressure—and the failure has to be uniform. “It can’t just fail anywhere; It has to be in the sidewall and as a tensile strength failure,” Fonger said.
But maintaining wall integrity is no easy feat, considering the extreme drawing that must occur and the physics of forming that canister shape.
The stamper makes a range of shells in materials from 0.034 to 0.090 in. thick. “As you draw, you do a couple of things to the raw material. As it flows over the dome throughout the first third of the shell, it gets stretched. That drawing action tends to thin the material out. But that material has to go somewhere, so it goes up to the open end; that’s the thickest point.” So the company’s challenge is in managing the wall thickness between the starting gauge and the minimum wall at the thinnest point.
Ductility. Fonger said that a material’s formability is more important than wall thickness—and it’s why sophisticated servo controls are needed. “It’s really more about the physical, chemical composition of the material. Some material work hardens faster than others. Some materials stretch more than others. And to a degree, in deep draw, stretching is our enemy because stretching means thinning. You want that material to hold together.”
Larson works closely with its vendors in the specification of 1008 or 1010 cold-rolled steel to make it as formable as possible for the draw process. “Drawability will allow us to draw as deeply as we do. But from time to time we encounter material that will work harden excessively, and the sidewall will develop a crack that can split over time. So if the material properties are not where they should be, we can encounter that type of defect,” Fonger said.

The two stages of a draw are cupping and drawing, according to Larson Tool & Stamping’s website. When the punch first contacts the blank, the nose of the punch initially embosses the material into the die. Some stretching occurs at this point and produces what is known as a “shock line.” This is a pronounced area of thinning around the radius at the bottom and just up into the straight wall of the shell. Depending on the shape of the bottom, the material may still be near original thickness across the bottom face (flat bottom) or thinned out by a stretching action (spherical bottom). As the blank is pulled into the die, the material at the circumference gathers and the wall progressively thickens. As the blank is pulled into near shell diameter, the material thickens to as much as 10% over the original thickness. Clearance must be provided for this thickening to occur so that the material will not get bound up between punch and die. In addition, the punch must be tapered so that the finished shell can be stripped off. Therefore, a drawn shell will taper from bottom to top. It is possible to minimize this through subsequent sizing operations, but not eliminate it entirely.
Material Purity. It’s of critical importance that the raw material does not contain imperfections that will result in cracking in the sidewall. “Imperfections and thinning material will create a weak point,” Fonger said. The company works with its steel mill to obtain steel with virtually no imperfections. The mill uses an internal recipe for the steel it makes for Larson, dubbed “Larson quality.”
“Imperfections occur regularly in steelmaking, like scale and laminations—we’re talking microscopic. In less severe forming applications, they would never be a problem. But because deep drawing is an extreme forming operation, any hidden imperfections in the material are going to bloom,” Fonger said.
Surface Finish. Another concern is with the material’s surface finish. Scoring can occur when galling gunks up the die surfaces, causing score lines on the inner or outer sidewall, which are not acceptable.
Hydraulic Press Technology Lessons
Fonger said that each hydraulic press technology upgrade has informed the company’s manufacturing. “You can only push material so fast and so far in metal forming. The speed at which you can form that material is governed by the tensile strength and the material’s ductility.
“But each generation of hydraulic press technology improvements has allowed us to experiment a lot more with pressures and speeds. We’ve learned a lot more about the steels that we need to draw—how to formulate the material better and how to dial in the controls that allow for material variation.”
He added, “We have to push the limits to be competitive while also having a little more finesse with the material at times to get the end result we need.”
Making Life-saving Fire Extinguisher Canisters
Making a major component for portable fire protection that saves lives and property doesn’t really faze the company, Fonger said.
"We don’t really dwell on it,” he said, but added, “One of our employees is a firefighter. He has mentioned more than once that he has responded to a call, and somebody had grabbed one of these fire extinguishers that we helped produce to douse a fire—and how important it was in preventing or limiting a disaster.”
About the Author
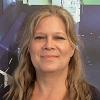
Kate Bachman
815-381-1302
Kate Bachman is a contributing editor for The FABRICATOR editor. Bachman has more than 20 years of experience as a writer and editor in the manufacturing and other industries.
subscribe now
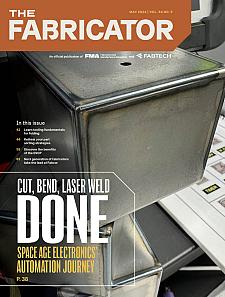
The Fabricator is North America's leading magazine for the metal forming and fabricating industry. The magazine delivers the news, technical articles, and case histories that enable fabricators to do their jobs more efficiently. The Fabricator has served the industry since 1970.
start your free subscription- Stay connected from anywhere
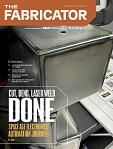
Easily access valuable industry resources now with full access to the digital edition of The Fabricator.
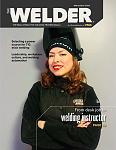
Easily access valuable industry resources now with full access to the digital edition of The Welder.
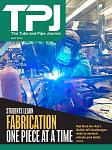
Easily access valuable industry resources now with full access to the digital edition of The Tube and Pipe Journal.
- Podcasting
- Podcast:
- The Fabricator Podcast
- Published:
- 04/30/2024
- Running Time:
- 53:00
Seth Feldman of Iowa-based Wertzbaugher Services joins The Fabricator Podcast to offer his take as a Gen Zer...
- Industry Events
16th Annual Safety Conference
- April 30 - May 1, 2024
- Elgin,
Pipe and Tube Conference
- May 21 - 22, 2024
- Omaha, NE
World-Class Roll Forming Workshop
- June 5 - 6, 2024
- Louisville, KY
Advanced Laser Application Workshop
- June 25 - 27, 2024
- Novi, MI