Senior Editor
- FMA
- The Fabricator
- FABTECH
- Canadian Metalworking
Categories
- Additive Manufacturing
- Aluminum Welding
- Arc Welding
- Assembly and Joining
- Automation and Robotics
- Bending and Forming
- Consumables
- Cutting and Weld Prep
- Electric Vehicles
- En Español
- Finishing
- Hydroforming
- Laser Cutting
- Laser Welding
- Machining
- Manufacturing Software
- Materials Handling
- Metals/Materials
- Oxyfuel Cutting
- Plasma Cutting
- Power Tools
- Punching and Other Holemaking
- Roll Forming
- Safety
- Sawing
- Shearing
- Shop Management
- Testing and Measuring
- Tube and Pipe Fabrication
- Tube and Pipe Production
- Waterjet Cutting
Industry Directory
Webcasts
Podcasts
FAB 40
Advertise
Subscribe
Account Login
Search
Infrastructure fabrication focus: Pole forming at scale
How automation has transformed a metal fabrication niche
- By Tim Heston
- January 5, 2024
- Article
- Bending and Forming
Drive down a well-lit road at night on a freeway. Look up during a Friday night football game at the local high school. That’s the rarely noticed light and utility pole doing its job. Rising infrastructure spending has shined a light on these poles and any number of other large fabrications. They appear utterly ordinary, but look at them closely, and their forming method isn’t so obvious.
The operations producing them are anything but ordinary. They incorporate extraordinarily large press brakes, sometimes singles but usually of the tandem or tridem variety. And many are extraordinarily automated, with little manual intervention.
“These systems entail the least amount of hands-on time with the material as possible,” said Matthew Crosby, regional sales manager at Pacific Press Technologies. “In some cases, material will come off a truck and go right to the press brake. It’s formed, and pushers eject a completed form to be welded.”
These specialty applications incorporate several critical elements: streamlined material movement, advanced process control, and unique tooling and gauging to ensure forming reliability. For specialty fabricators, scrapping these massive plates just isn’t an option.
Blank to Bend to Weld
To develop the optimal setup, application engineers usually start by asking questions about the material. As Danny Semick, sales manager at Revolution Machine Tools, explained, “Material really is the biggest factor. We need to know the material type, thickness, and part length. Are we talking 60 or 100 ft., or are we talking shorter, like 20 or 30 ft.?” (“Short” is a relative term here.)
Material shape also enters the equation. Tapered poles will have trapezoid blanks, while nontapered poles will be square.
The very next question, Semick said, involves the flow of the product, whether starting from a blank slate (like a new plant being constructed) or an existing facility. Systems vary widely depending on the space available.
Imagine a large plate entering a pole factory. It first goes into a limited, highly controlled raw stock inventory. From there (or sometimes directly from a truck bed in the receiving department), it’s placed onto a large-bed, high-power fiber laser cutter, with the safety enclosure riding on the gantry. The laser, which has beveling capability, cuts from the massive plate two large trapezoids, which accounts for the tapered shape of most light poles.
“A few years ago, one operation in Utah installed a 60-ft. laser with a 45-degree beveling head on it,” Semick recalled, “all to cut massive trapezoids with the weld prep. For the most part, no postprocessing [deburring] was required.”
Because of their trapezoid shape, the parts might be nested opposite of each other on the laser or plasma table to increase material yield—a cost savings that, considering the sheer amount of material involved, justifies the increased material handling.
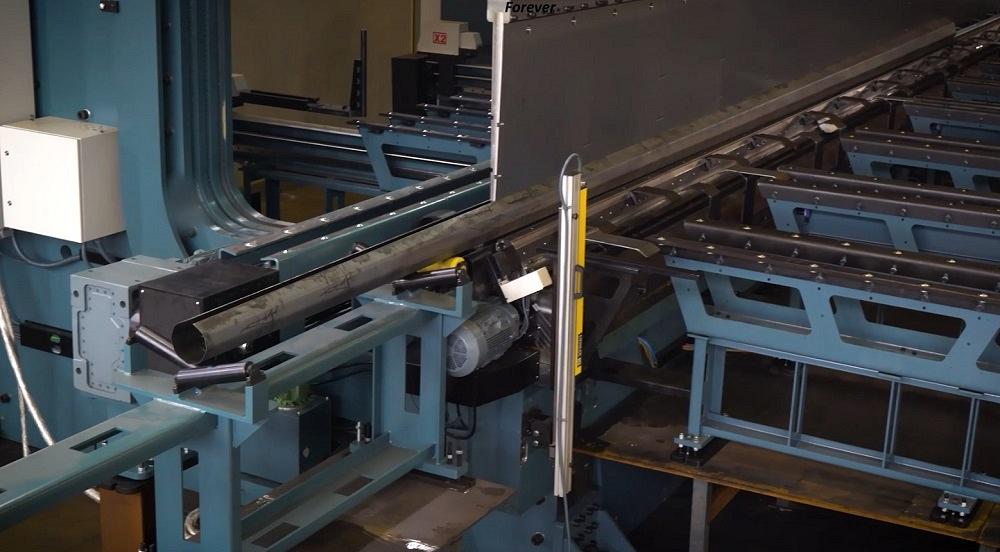
A formed pole is pushed off the edge of a large tandem press brake. Note the tall punch and the deep-throat C-frame design. Durma North America
Because of just how unwieldy these plates are, some operations have a dedicated plate rotator that positions these long cut blanks in the right orientation. Yuksel Taskin, president of Durma North America, described it this way: “Picture a specialized crane that turns the piece 180 degrees to the left or right. The automation system rotates the material in the right way. And sometimes specialized systems can carefully flip the material, if needed. This gives shops nesting flexibility on their plasma or laser.”
Plates are moved onto a conveyor. Some operations might have a buffer inventory of cut blanks, while others move blanks directly to a staging platform in front of a massive tandem press brake. Frontgauge pushers carefully manipulate the plate toward the press brake bed and against the backgauge.
A measuring device pinches the material to verify its thickness. Once everything is aligned, the punch descends, and the piece is carefully bumped to completion until both edges of the blank “hug” the body of the punch. Once the workpiece is checked and verified for quality, automated pushers remove the pole from the end of the bed onto a separate conveyor that carries the piece directly to a welding station. There, a machine clamps the workpiece, pressing the two edges together, then welds the longitudinal seam. Once welded, conveyors move the massive pole to final fabrication, assembly, and shipping.
Today, that entire operation might be managed by a handful of people, each sitting on a pedestal safely away from the automation. Finely tuned, the system produces each pole at a precise rate, timed perfectly to feed the final operations downstream.
“Today, you can potentially run such a plant, minus the finish welding and prep at the very end of the process, with just four people,” Semick said. “You’d have an operator on the plasma or laser, a brake operator, a seam welder operator, and from there you have the finished product. I’ve been in facilities where [after the blanks are cut], poles are formed and fabricated every 20 minutes.”
Controlling the Bend
The brake setup itself is extremely specialized. As Taskin explained, “These applications can call for motorized tool changes [like adjustable dies], front-loading arms, and special gauging systems, as well as special material handling.”
Tandem brakes, the most commonly used in the pole industry, give a shop flexibility. The operation can use the system either in the tandem setup, for one large job, or in two single-brake setups to run smaller jobs simultaneously. A large single brake is less flexible, but of course it also has a large open space behind the tooling, with no throat from the C-frame to worry about. That said, throats on today’s tandem and tridem machines can be extraordinarily large.
The dies can be truly massive as well. “Some operations request press brakes to handle material 4 in. thick or even thicker,” Taskin said.
The die often has an adjustable opening. Thicker material with fewer steps (bumps) will likely require a larger die opening to handle the increased tonnage, while thinner material with more steps will call for a narrower opening. Modern controllers and software help calculate the optimal number of bumps a pole might require. And as Taskin described, some setups have laser gauges, in front of and behind the die, that can check the workpiece radius throughout the cycle.
It’s a complex, highly nuanced balancing act. It doesn’t take too many degrees of bend to send forming tonnage through the roof, especially in a thick workpiece 60 ft. long or even more. Most pole bending applications deal with extraordinarily long bend lengths. At the same time, a workpiece with more steps (bumps) has narrower pitches—that is, the space between the bend lines. Those narrow pitches demand a narrower die opening, which increases forming tonnage.
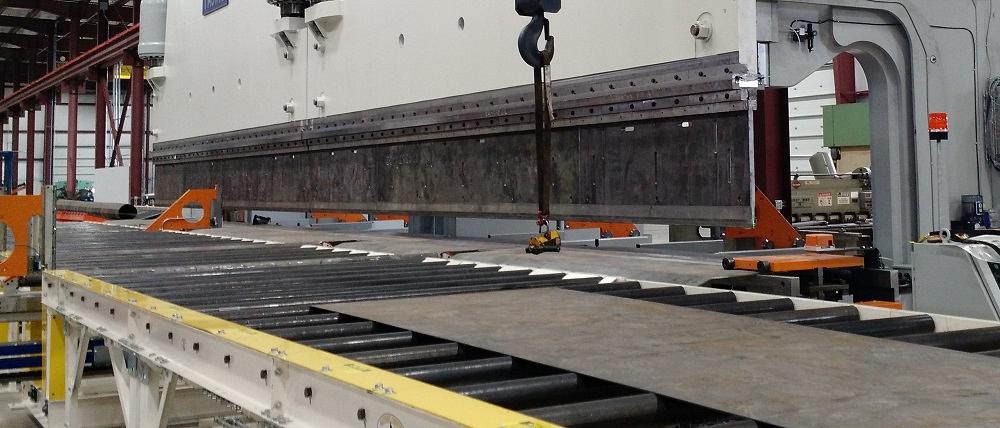
A blank is conveyed toward positioners, which double as front- and backgauges. These manipulate the blank throughout the pole-bending cycle. Pacific Press Technologies
Adding to the complexity is the fact that many poles call for tapered bends, requiring back- and frontgauges to keep the material in the correct orientation before the punch contacts the material surface. Then there’s material thickness and hardness variation, which can throw off nearly every other bending variable.
“Getting the right tooling is absolutely critical here,” Semick said.
The bump cycle varies, depending on the application requirements. Poles with two weld seams consist of two semicircular shells, each of which have a bend sequence that requires support throughout.
What about the one-piece poles with just one weld seam? “When you’re running one piece, you need to be very particular when and where your bends take place,” Crosby said, adding that today, press brake software manipulates workpieces through carefully crafted bump-bending cycles.
Some bump from the edge to the center, rotate the workpiece, then bump from the edge to the center again. This option can make sense when, say, the tandem or tridem brake’s throat isn’t sufficient to handle the entire depth of the blank. Others avoid rotating the piece by bumping in an alternating sequence—first bumping the far edge one or more times, then the near edge, then the far end, until reaching the middle, at which point the pole is fully formed and “hugging” the punch body.
After this, pushers slide the pole off the side, where hydraulic arms push the pole closed for the final seam weld. As Semick explained, single-sided welds usually can be automated. But in thick material requiring double-sided access, some manual manipulation and tacking might be required before sending the workpiece on for seam welding.
“Processes really depend on what a specific jurisdiction allows,” Semick said, adding that like other infrastructure projects, exact fabrication processes vary depending on what state and locality the pole will ultimately be.
Regardless, to make this all happen requires a press brake with sufficient open height and space for tall tooling, including extenders or adapters that give clearance during the final stages of the bend cycle. As Crosby explained, “Adapters attach to the ram. [Pole bending, being a bumping process,] doesn’t require much stroke, and, of course, you don’t want the pole edges to close up and hit the ram. You need something skinny for those final bumps in the bend cycle. You need [that portion of the tool] as thin as you can get it while still having sufficient strength for the forming process.”
Punches might be 2 or 3 ft. tall, but with adaptable tip radii. Instead of swapping out these massive punches, operators simply swap out the punch tip.
Pole bending also requires brakes with an advanced crowning system that can deal with the deflection of such a long bend in thick material. “Crowning is automated,” Taskin said. “Software calculates the appropriate crowning for the job specifications at hand. There’s no need for manual adjustment.”
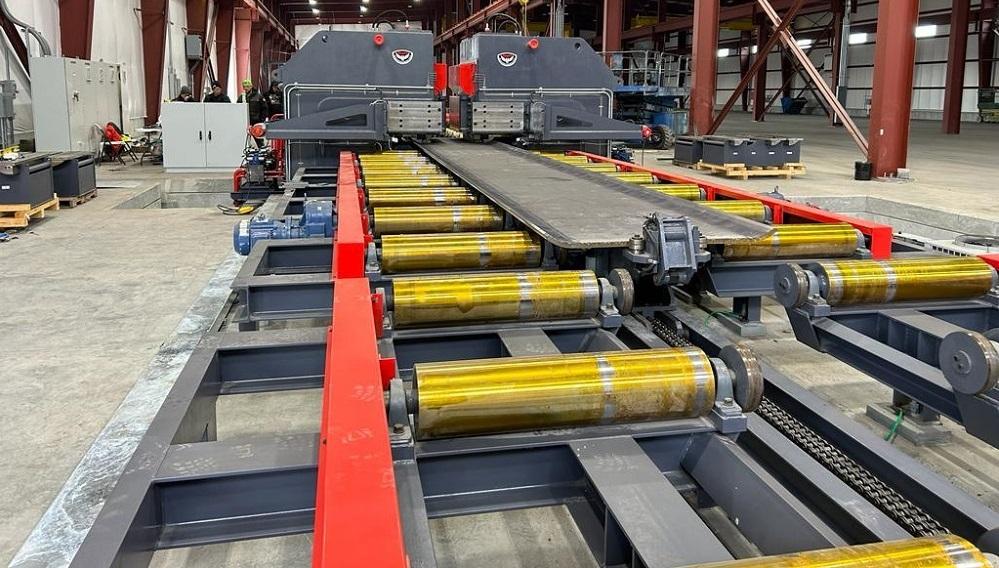
A long plate emerges from a prebending machine that forms a radius on both edges of the workpiece. Revolution Machine Tools
He added that on occasion, operations integrate a parts etching station at the press brake. “This is so they can mark specific codes or other information on the pole itself. Etching with the laser is an option, but some don’t want to tie up the cutting system with parts marking.”
Leading the Way with Automation
Infrastructure projects in general come with some constraints, including local and regional codes as well as domestic sourcing requirements. Semick described some pole bending applications—heavy-duty, nontapered sections for highway signs—that utilize a separate prebending machine before being sent to the brake. Prebending the initial radius on each edge leaves no unbent flat section that would otherwise need to be cut and scrapped. And again, the entire process can be automated, with conveyors carrying plate from prebending to the press brake pole press, then downstream to welding.
Taskin summed it up this way: “Each year, automation in metal fabrication is getting more and more important, especially with heavy-duty material. You have laser systems; plasma systems; plate rotating systems; 60-ft.-long, 4,000-ton press brakes—all run by one or a handful of people. It’s incredible just how automated these giant machines are becoming.”
About the Author
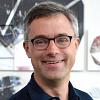
Tim Heston
2135 Point Blvd
Elgin, IL 60123
815-381-1314
Tim Heston, The Fabricator's senior editor, has covered the metal fabrication industry since 1998, starting his career at the American Welding Society's Welding Journal. Since then he has covered the full range of metal fabrication processes, from stamping, bending, and cutting to grinding and polishing. He joined The Fabricator's staff in October 2007.
subscribe now
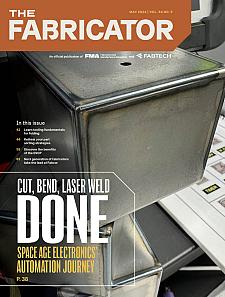
The Fabricator is North America's leading magazine for the metal forming and fabricating industry. The magazine delivers the news, technical articles, and case histories that enable fabricators to do their jobs more efficiently. The Fabricator has served the industry since 1970.
start your free subscription- Stay connected from anywhere
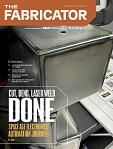
Easily access valuable industry resources now with full access to the digital edition of The Fabricator.
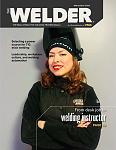
Easily access valuable industry resources now with full access to the digital edition of The Welder.
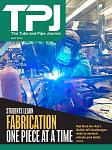
Easily access valuable industry resources now with full access to the digital edition of The Tube and Pipe Journal.
- Podcasting
- Podcast:
- The Fabricator Podcast
- Published:
- 04/16/2024
- Running Time:
- 63:29
In this episode of The Fabricator Podcast, Caleb Chamberlain, co-founder and CEO of OSH Cut, discusses his company’s...
- Industry Events
16th Annual Safety Conference
- April 30 - May 1, 2024
- Elgin,
Pipe and Tube Conference
- May 21 - 22, 2024
- Omaha, NE
World-Class Roll Forming Workshop
- June 5 - 6, 2024
- Louisville, KY
Advanced Laser Application Workshop
- June 25 - 27, 2024
- Novi, MI