- FMA
- The Fabricator
- FABTECH
- Canadian Metalworking
Categories
- Additive Manufacturing
- Aluminum Welding
- Arc Welding
- Assembly and Joining
- Automation and Robotics
- Bending and Forming
- Consumables
- Cutting and Weld Prep
- Electric Vehicles
- En Español
- Finishing
- Hydroforming
- Laser Cutting
- Laser Welding
- Machining
- Manufacturing Software
- Materials Handling
- Metals/Materials
- Oxyfuel Cutting
- Plasma Cutting
- Power Tools
- Punching and Other Holemaking
- Roll Forming
- Safety
- Sawing
- Shearing
- Shop Management
- Testing and Measuring
- Tube and Pipe Fabrication
- Tube and Pipe Production
- Waterjet Cutting
Industry Directory
Webcasts
Podcasts
FAB 40
Advertise
Subscribe
Account Login
Search
New feeder improves stamper’s forming efficiency
Service center in proximity keeps the line ‘on-line’
- October 3, 2018
- Article
- Bending and Forming
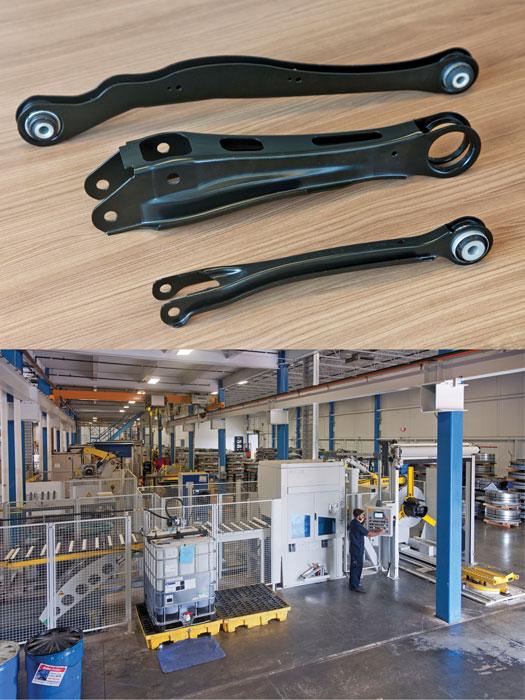
Erdrich USA draws from the German-based company’s 50 years of experience in metal forming technology and consistent growth. The company stamps large, thick-gauge steel components for wheel axles (shown) and housings for electronic devices—about 30,000 per day in total.
Erdrich Metal Forming Technology, headquartered in Germany, was founded 50 years ago producing stamping tools. It then grew to mass-produce stamped and bent parts. Over the years the company also has developed considerable expertise in deep drawing and flow forming of thick sheets and fineblanking. It uses a stamping technology that combines fineblanking and forming in a single press.
The manufacturer has grown from a small craftsman’s shop to a global player with facilities in China, Germany, the Czech Republic, and the U.S. In 2013 the company began production in Dublin, Ga., as Erdrich USA Inc. It stamps components for the automotive industry, from large chassis parts to housings for electronic devices (see lead image).
“If you look at cars on the streets, most of them are made with some of our parts,” said Erdrich USA COO Alexander Kehrer (see Figure 1). The stamper’s portfolio ranges from very slim aluminum covers for electronic boxes to robust, thick-gauge steel components for wheel axles.
The plant’s daily output is roughly 30,000 metal parts, most of which go to clients in the U.S. and Mexico, but also overseas.
Feeding the Press
Auto industry insiders like Erdrich know that its components must be engineered precisely to deliver safe and accurately finished products. Weighing up to 10 tons each, the coils require precise handling to ensure efficient processes. To ensure consistent quality, the company relies on levelers to flatten its advanced high-strength steel (AHSS) before stamping it.
In addition, the company operates in a highly competitive environment. To boost efficiency, Erdrich decided to revamp its coil feeding lines. Sheet thicknesses range from 0.06 to 0.31 inch. (1.5 to 8 millimeters).
Kehrer said that he learned from experience that coil feeding lines can’t be integrated into the existing production without substantial support. Thus, he and his team needed a flexible supplier in proximity to the plant that could provide support on short notice.
In addition, mounting cost pressures forced him to look for ways to reduce overall production expenses.
“We had been operating with coil lines from another [overseas] supplier,” explained Kehrer. The problem was that when the busy manufacturer experienced increased customer demand, its operations were vulnerable when the inevitable coil feed problems occurred. Support from his overseas supplier came with a time zone difference and, therefore, time lag, language barrier, and additional travel costs, he said.
“I need support that goes above and beyond online support,” Kehrer said. “Machines like a coil feeding line need constant support and maintenance. When I have an issue with my equipment—and I’m not neccessarily talking about a warranty issue, just a normal operational issue that happens every now and then with machines—I need a professional maintenance technician on-site,” he said.
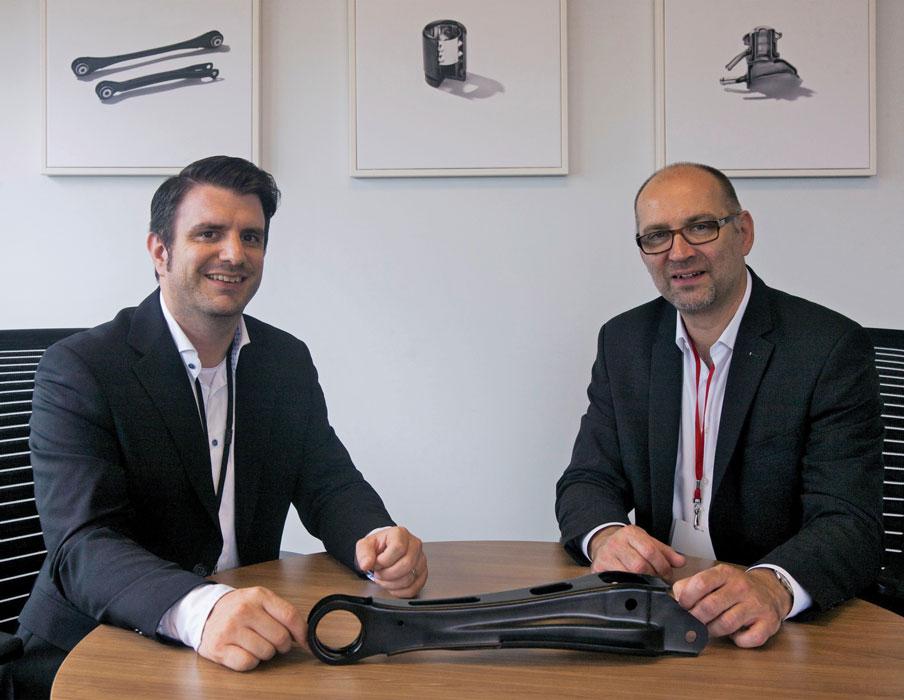
Figure 1
Erdrich USA COO Alexander Kehrer (left) and ARKU Vice President of Sales Franck Hirschmann present a chassis part manufactured at Erdrich.
Coil Line Installation
In early 2017 Erdrich USA purchased an ARKU coil feeding line that includes a CoilMaster® 7050/17 precision leveler EcoPlan® and a zig-zag servo feeder (see Figure 2).
“The most important factors were that the coil equipment [manufacturer] has a service office nearby in the U.S. and we really have a good connection to our service partner, and that their equipment is user-friendly,” Kehrer said.
“That [and] state-of-the-art engineering were the driving points for us to go with ARKU. I just give them a call and they are here the next day with a technician because their service center is here in the U.S.”
Because the ARKU has a service office stateside, it was able to offer good pricing because it could offer the service through its U.S. office, Kehrer said.
Zig-zag. Kehrer identified reducing stamping waste as key to enhancing Erdrich’s production efficiency. This required a special zig-zag feeder, which stamps the metal parts in a zig-zag pattern, keeping material waste to a minimum.
Implementation. The coil feeder and leveler implementation went smoothly and were completed in May 2017. Kehrer said the installation took only four weeks. “That is quite remarkable, considering the complexity,” he said. As a result, Erdrich was able to resume operations earlier than planned, saving valuable production time.
Energy Savings. In addition, the line features ARKU’s EcoPlan energy-efficient drive, which delivers up to 30 percent more performance with the same electrical power requirements.
Reduced Wear. The line’s material transport system prevents rapid wear of the leveling rollers, while also protecting the strip material.
Control Panel. The machine is equipped with process visualizations on the control panel to simplify control. In terms of software, the menu structure is similar to that used on personal computers, which makes for intuitive use, especially beneficial during coil changes. In addition, the user-friendliness reduces the training requirements for new employees, Kehrer said. S
Erdrich USA Inc., www.erdrich-usa.com
Photos courtesy of ARKU, www.arku.com.
Related Companies
subscribe now
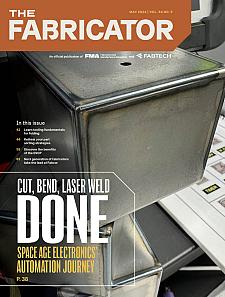
The Fabricator is North America's leading magazine for the metal forming and fabricating industry. The magazine delivers the news, technical articles, and case histories that enable fabricators to do their jobs more efficiently. The Fabricator has served the industry since 1970.
start your free subscription- Stay connected from anywhere
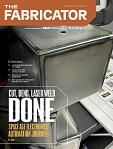
Easily access valuable industry resources now with full access to the digital edition of The Fabricator.
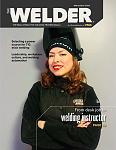
Easily access valuable industry resources now with full access to the digital edition of The Welder.
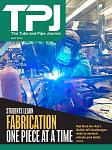
Easily access valuable industry resources now with full access to the digital edition of The Tube and Pipe Journal.
- Podcasting
- Podcast:
- The Fabricator Podcast
- Published:
- 04/16/2024
- Running Time:
- 63:29
In this episode of The Fabricator Podcast, Caleb Chamberlain, co-founder and CEO of OSH Cut, discusses his company’s...
- Trending Articles
Tips for creating sheet metal tubes with perforations
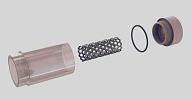
JM Steel triples capacity for solar energy projects at Pennsylvania facility
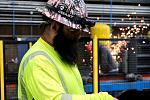
Are two heads better than one in fiber laser cutting?
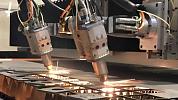
Supporting the metal fabricating industry through FMA
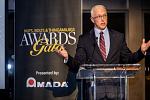
Omco Solar opens second Alabama manufacturing facility
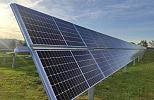
- Industry Events
16th Annual Safety Conference
- April 30 - May 1, 2024
- Elgin,
Pipe and Tube Conference
- May 21 - 22, 2024
- Omaha, NE
World-Class Roll Forming Workshop
- June 5 - 6, 2024
- Louisville, KY
Advanced Laser Application Workshop
- June 25 - 27, 2024
- Novi, MI