- FMA
- The Fabricator
- FABTECH
- Canadian Metalworking
Categories
- Additive Manufacturing
- Aluminum Welding
- Arc Welding
- Assembly and Joining
- Automation and Robotics
- Bending and Forming
- Consumables
- Cutting and Weld Prep
- Electric Vehicles
- En Español
- Finishing
- Hydroforming
- Laser Cutting
- Laser Welding
- Machining
- Manufacturing Software
- Materials Handling
- Metals/Materials
- Oxyfuel Cutting
- Plasma Cutting
- Power Tools
- Punching and Other Holemaking
- Roll Forming
- Safety
- Sawing
- Shearing
- Shop Management
- Testing and Measuring
- Tube and Pipe Fabrication
- Tube and Pipe Production
- Waterjet Cutting
Industry Directory
Webcasts
Podcasts
FAB 40
Advertise
Subscribe
Account Login
Search
Press brake bending basics: Breaking the time barrier
Getting estimates right requires good information and, not least, good operators and engineers
- By Steve Benson
- January 9, 2017
- Article
- Bending and Forming
Question: I’m the estimating manager for a contract manufacturer of build-to-print metal fabrications in North Carolina. One of our selling points is our forming capabilities, because we have a number of press brakes ranging from 50 to 2,000 tons.
We have an established ERP system that we use to build time estimates and route jobs through the shop. Most of the time estimates use variables from the specific part geometry and are calculated from formulas and tables for the equipment.
We also have a group of manufacturing engineers who are available to confirm our current press brake tooling and verify if we have adequate tonnage to form any given part. Unfortunately, our methods for developing time estimates for forming are not based on any formula. Our estimators simply enter an estimated amount of time to form parts based on their experience and their “gut feeling.”
Personally, I would like to develop a more scientific means of developing these time estimates. Intuitively, I feel like there are a number of variables that would be used in the calculation:
- Material type/grade
- Material thickness
- Bend length
- Bend angle
- Number of bends
- Load/unload time
- Backgauging time
Although I think I’ve identified the correct parameters, I have no idea where to turn to develop time calculation models and formulas. Do you have any suggestions as to where I should start?
—David Dodson, Metal Works Mfg. Co., Shelby, N.C.
Answer: Correctly calculating production times for formed parts is one of the hardest to pin down, precisely because of the number of variables you cited. Let’s look at each of these variables and where they fit into your enterprise resource planning program. We’ll also look at a couple variables yet to be considered. Let’s review each item on your list to see how each factors into estimating the cost of forming.
Material Type/Grade
Other than during prototyping or the first part run, material variables should not affect setup or run times over the long term, as any tooling and process issues will have already been worked through.
Material Thickness
While the type of material should not make a difference for setup or run-times, variations in thickness can create issues. Eliminating this variable obviously will help make estimating much more accurate and, as an added benefit, shorten your machine setup times. Nonetheless, this is something that begins in both the engineering and purchasing departments.
Purchasing must try to acquire the materials from a single source. As you are aware, finding quality metal is difficult, and it’s even harder when your metals come from multiple sources. By using a single source, your setup and run-times will be more consistent over time.
Ideally, a single source will be able to offer you materials of consistent thickness and grain direction. If these two variables alone are inconsistent, your setups and run-times will be all over the map and hard to predict.
Bend Length
If your equipment is in good working order and uses quality tooling, the length of bend should make little to no difference. Issues related to backgauge position and crowning should have been worked out during prototyping.
However, if your tooling or machine is in poor condition, then bend length can become a variable that makes it almost impossible to predict what the setup and run-times will be. There is only one solution for correcting this problem, and it will pay for itself in labor savings. I am not saying that you need a state-of-the-art machine and tooling, only that both should be in excellent condition, regardless of how technologically advanced they are.
Bend Angle
Individual bend angle adjustments are affected by the same issues as the material thickness and length of bend, and they have the same solutions: consistent material from a single source as well as machines and tooling in excellent working order.
Number of Bends
Assuming you have topnotch tooling and equipment, bidding this should be pretty straightforward: a set number of minutes per bend for setup and a set number of seconds for the run-time. Of course, each shop and each application is a little different. You need to work through issues during the initial setup, and then document the first good setup you have. At this point, setup times are now known.
When estimating your operation times, you need to consider various factors. Do operators return the current tooling, find the next set, and install it on their own, or does someone stage the tooling for them? Do they have to move the finished pieces and find their own material for the next run?
As a rule of thumb, for the initial setup on a new job, try using a safe time estimate of 10 minutes for the first flange, including the tooling installation, followed by an additional 5 minutes for each bend. This is just a starting point, however, and you may need to make some time alterations depending on the complexity of the piece.
Load/Unload Time
If the load/unload operation is automated, your software can provide you with that data. If the project requires a lot of manual manipulation, you can perform a quick time study.
If the job calls for simple handling by the operator, the time usually is negligible. Again, this depends on operations within your shop. Time estimates might include such elements as moving pallets to the next work area and finding the next pallet of material. But these too are easy to estimate.
Backgauging Time
Of course, there will be a big difference between manual and CNC backgauge setup times. But overall, backgauge time is negligible from bend to bend. When you include the backgauge time in the individual bending time calculations, it usually is no more than a few seconds.
The Catch 22 of the Overlooked Two
There were two items you did not include in your list that directly affect time estimating: the skill level of your operators and the real-world knowledge in the engineering department.
Whether you simply send a CAD print layout to the shop floor or program a forming operation completely offline, you will have serious challenges estimating run-times if your engineers do not fully understand the differences between air forming and bottom bending, and where each should be applied.
Engineers must go to the shop floor and, without judgment, discuss the way forming is being accomplished. Are the folks on the shop floor bottom bending steel and air forming aluminum? It doesn’t matter what they are doing (though you may need to address that issue in a separate conversation); but for the time being, parts need to be designed to the reality of the shop floor.
Case in point: How is the inside radius of the bend being produced? Bottom bending and coining (coining being a method that’s no longer recommended) force the punch nose radius into the part; air forming floats the radius as a percentage of the die opening. This means that a part designed to be formed by one method cannot be formed using the other, at least if you want the flat layout to work out correctly.
Even if you are a bottom-bending shop, bends other than 90 degrees by default are an air form. On that note, the engineering department must find out what tools are available so that they can correctly predict the inside radius and compute a valid bend deduction.
Engineering not only must make that forming information available, but also make that tool an absolute. For example, if a part was designed to be formed over a 0.551-inch (14-mm) die opening to achieve the correct inside radius, it must be formed over a 0.551-in. die.
There was a time, when bottom bending was prevalent, that a project could be sent to the shop floor and the operator could pick the tooling. As long as the punch nose radius was forced into the material, the part would be correct. When air forming bends, you can’t allow the operator to choose just any tool. Doing so introduces multiple variations in the inside bend radius. This will cause variations in the final part size when being produced from the same flat blank. And as setup and run-times become more varied, making a good time estimate becomes a difficult proposition.
This brings us to the Catch 22: the operator skill level. This alone is one of the biggest drivers behind making setup and run-time estimations difficult. It is also the biggest reason that production times become inconsistent over time.
The Catch 22 is this: When you have engineering taking their cues from the information provided by the operators programming to those parameters, and then informing the operators to download this program, use specific tooling, set up sheets, and run the parts, you in effect dumb-down the job of the press brake operator—often to the point where those with technical aptitude for maintaining and operating a press brake with any finesse just walk out the door. And who could blame them? They leave in search of a more interesting and challenging career. Obviously, the skill of your operators affects the accuracy of your estimates.
Unfortunately, I can offer no solution to the Catch 22 of operator skill, but this too needs to be taken into account alongside the other elements discussed in this column.
Nonetheless, there is much you can do to improve the accuracy of your time estimates, even if that means changing some of your day-to-day operations. However, any time spent making these changes and adjustments will in the long run make your ERP or manual time-estimate accuracy better and your estimates more precise.
Steve Benson is a member and former chair of the Precision Sheet Metal Technology Council of the Fabricators & Manufacturers Association International®. He is the president of ASMA LLC, steve@theartofpressbrake.com. Benson also conducts FMA’s Precision Press Brake Certificate Program, which is held at locations across the country. For more information, visit www.fmanet.org/training, or call 888-394-4362. For more information on bending, check out Benson’s book, theArtofPressBrake: the Digital Handbook for Precision Sheet Metal Fabrication, ©2014, available at www.theartofpressbrake.com. Steve Benson’s latest book on press brake bending, published by FMA, will be available soon.
About the Author
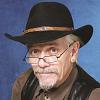
Steve Benson
2952 Doaks Ferry Road N.W.
Salem, OR 97301-4468
503-399-7514
Related Companies
subscribe now
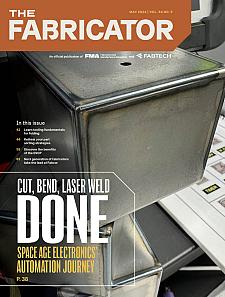
The Fabricator is North America's leading magazine for the metal forming and fabricating industry. The magazine delivers the news, technical articles, and case histories that enable fabricators to do their jobs more efficiently. The Fabricator has served the industry since 1970.
start your free subscription- Stay connected from anywhere
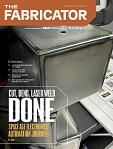
Easily access valuable industry resources now with full access to the digital edition of The Fabricator.
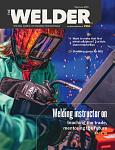
Easily access valuable industry resources now with full access to the digital edition of The Welder.
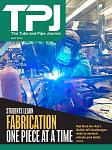
Easily access valuable industry resources now with full access to the digital edition of The Tube and Pipe Journal.
- Podcasting
- Podcast:
- The Fabricator Podcast
- Published:
- 05/14/2024
- Running Time:
- 62:12
Cameron Adams of Laser Precision, a contract metal fabricator in the Chicago area, joins the podcast to talk...
- Trending Articles
White House considers China tariff increases on materials
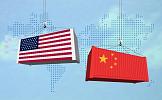
A visit to Automate 2024 reveals the future might be now
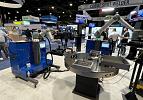
Majestic Steel Arkansas fully operational
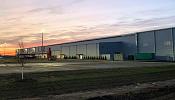
Rivian to expand Illinois facility to manufacture midsized SUV
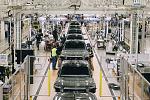
Why employee-owned companies make sense in manufacturing
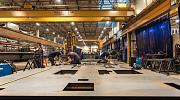
- Industry Events
Laser Welding Certificate Course
- May 7 - August 6, 2024
- Farmington Hills, IL
World-Class Roll Forming Workshop
- June 5 - 6, 2024
- Louisville, KY
Advanced Laser Application Workshop
- June 25 - 27, 2024
- Novi, MI
Precision Press Brake Certificate Course
- July 31 - August 1, 2024
- Elgin,