Director of Sales and Operations
- FMA
- The Fabricator
- FABTECH
- Canadian Metalworking
Categories
- Additive Manufacturing
- Aluminum Welding
- Arc Welding
- Assembly and Joining
- Automation and Robotics
- Bending and Forming
- Consumables
- Cutting and Weld Prep
- Electric Vehicles
- En Español
- Finishing
- Hydroforming
- Laser Cutting
- Laser Welding
- Machining
- Manufacturing Software
- Materials Handling
- Metals/Materials
- Oxyfuel Cutting
- Plasma Cutting
- Power Tools
- Punching and Other Holemaking
- Roll Forming
- Safety
- Sawing
- Shearing
- Shop Management
- Testing and Measuring
- Tube and Pipe Fabrication
- Tube and Pipe Production
- Waterjet Cutting
Industry Directory
Webcasts
Podcasts
FAB 40
Advertise
Subscribe
Account Login
Search
Protect stamping dies with ion/plasma nitriding
Dies for advanced high-strength steels need advanced hardening
- By Drew Hutchison, Edward Rolinski, Gary Sharp, and Mikel Woods
- November 23, 2017
- Article
- Bending and Forming
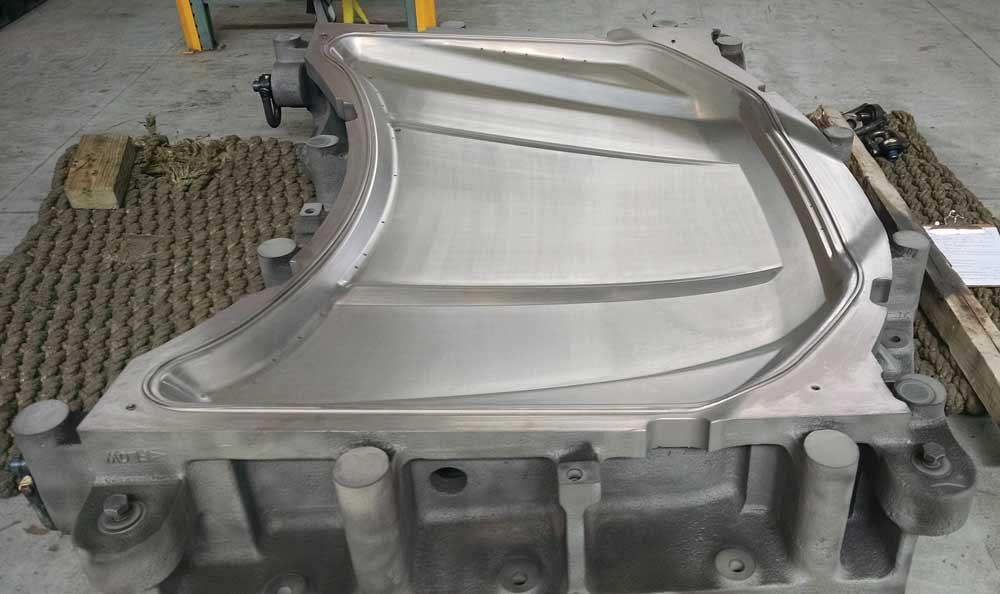
The use of ion/plasma nitriding of stamping dies is growing as the use of AHSS work materials increases.
It’s no secret that the demand for lighter yet safer vehicles has increased the demand for stronger steels in automotive bodies. Steels are significantly stronger than those that were used in older vehicle designs. New generations of advanced high-strength steels (AHSS) used in the auto industry create great challenges for stamping tools used in those applications. Some components, such as floor panels, are made of press-hardened steels, which can have tensile strength as high as 1,500 to 1,800 megapascals (MPa). The stress required to induce sufficient plastic deformation in those steels is as much as 400 MPa.
The hardness of such materials typically is insufficient for resisting high-contact Hertzian stresses inherent in the forming operations. These tools can be induction- or flame-hardened, but treatments with chemical vapor deposition (CVD) or physical vapor deposition (PVD) techniques are not feasible for them because of their large size.
Tool-Hardening History
Dies for stamping and forming long have been made with various hardenable steels, whether mill-formed, forged, or cast. Today, to reduce die cost and weights, large stamping dies and tools typically are made of cast irons or cast steels. Typically these materials are not hard enough to resist high-contact Hertzian stresses inherent in the forming operations.
Depending on the die size and shape, hardening involves heating at high temperatures and then quenching (very fast cooling.) Next, the steels undergo tempering to prevent cracking, thereby increasing toughness, ductility, and die life.
Dozens of steel variations exhibit good hardening properties, especially for small dies. Flame hardening also has been used on complex shapes and large dies, as it focuses the hardening on the surface of the large die. As with any steel-hardening process, careful attention must be paid to obtaining the correct properties to extend die life. Usually, special coatings are not available for large dies.
Chromium plating has been used successfully to protect stamping dies for many years.
It offers a very smooth surface with a low coefficient of friction. However, chromium plating’s limitations seem to be more pronounced as AHSS become harder. Those on the higher end of the spectrum are harder than the substrate below the surface of the chromium layer. This layer’s adhesion is dependent largely on the substrate material, so premature wear and galling occur sooner than with steel grades in the lower hardness ranges. This galling results in lower production runs and requires that the dies be recoated more frequently. Therefore, chromium plating can be costly and time-consuming when it is used to keep a die surface in optimal condition for stamping AHSS.
If slug damage occurs on a chromium-plated die surface, it needs to be either heat popped or weld-repaired. In both cases, it is likely that the bare substrate will be exposed. Because chromium is harder than the underlying die material (see Figure 1), the bare area can exhibit a faster rate of wear than the chromium surrounding it. This also can change the flow characteristics of the die surface; the drag on untreated areas will increase its friction value.
With ever-increasingly harder work materials, a die’s surface requires more protection than just a layer of 10 to 20 micrometers, as plating provides. Plating is also an electrolytic process. That means that the chromium deposit tends to be heavier on the male, or protruding, areas and thinner, possibly even nonexistent, on the female, or recessed, areas. This variation may cause dimensional differences, however slight, and could potentially cause problems during die setup.
In addition, chromium plating can be a health hazard. The Environmental Protection Agency (EPA) issued national emission standards for hazardous air pollutants that limit the discharge of chromium-compound air emissions from existing and new hard chromium electroplating, decorative chromium electroplating, and chromium anodizing tanks at major and area sources. Chromium compounds are among the 189 hazardous air pollutants (HAP) listed for regulation under Section 112 of the Act. Hard and decorative chromium electroplating and chromium anodizing tanks have been identified by EPA as significant emitters of chromium compounds to the atmosphere. (www.epa.gov/stationary-sources-air-pollution/chromium-electroplating-national-emission-standards-hazardous-air#additional-resources)
Enter Ion/Plasma Nitriding
In recent years a technique called ion/plasma nitriding has been successful in surface hardening of those tools and dies.1 This is especially true if the cast materials are alloyed with chromium, molybdenum, and other elements, which form very stable and hard nitrides. Nitrided layers formed in those alloys are very hard and their depth exceeds 0.010 inch (0.25 mm).
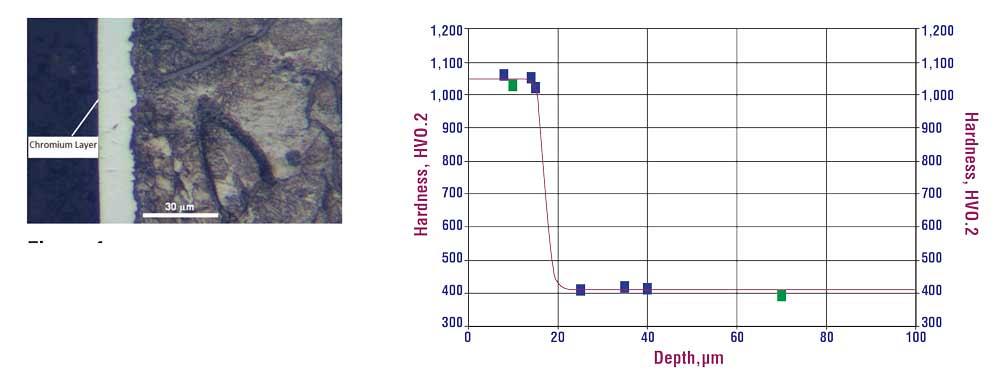
Figure 1
At left is a photomicrograph of chromium-
plated G25HP cast iron. The graph on the right shows the hardness distribution in the chromium-plated G25HP cast iron.
The treatment is performed in a large vacuum vessel equipped with resistance heaters and the plasma generator. Parts are covered with glow discharge plasma, which generates ions and active nitrogen species, causing a nitriding effect. The process can be seen inside the vacuum chamber (see Figure 2). The nitrided layer is built of compound and diffusion layers (see Figure 3).
The ion/plasma nitriding process has been widely used to harden components of large draw dies such as punches and binders. Typically, they are made of gray or ductile cast irons such as G2500, G3500, and D5506, as well as cast steels, including S0050A and D2. Line and progressive dies, as well as various inserts, are made of Uddeholm CALDIE® M2, S7, and other high-quality tool steels.
Nitriding is not a coating, so it does not chip or peel. It can provide the substrate depth hardness required to withstand the greater impact that occurs in forming AHSS. This results in less slug damage.
Plasma nitriding does not create dimensional changes because the process is evenly applied on both the protruding and receding areas (see Figure 4).
The results of studies conducted have indicated that a chromium-plated surface on cast iron or cast steel can last for as many as 600,000 hits. Those numbers are decreasing, though, as AHSS increases in use. In the same stamping environment, results show a nitrided surface lasts more than 850,000 hits. One particular study showed 1.2 million hits from a nitrided die used to form a floor pan die cavity.
A very sharp gradient of hardness in chromium coatings may be a reason for the cracking and exfoliation of the chromium layer in high-stress contact areas such as radii. On the contrary, the smooth transition of hardness in the surface of the ion/plasma nitrided dies extends the life of metal forming tools subjected to very high Hertzian stresses. It should also be noted that the stresses in nitrided surfaces are compressive.
Small tools or inserts withstand the contact stresses inherent in forming steel components and last the longest when they are made of the strongest tool steels, nitrided and PVD- or CVD-coated with the hard and wear-resistant layers such as chromium nitride (CrN) and titanium aluminum nitride (TiAlN).
It’s optimal to treat monolithic, large die components with ion/plasma nitriding. Nitriding offers the ability to have a more ductile core, reducing cracking and making forming and shaping of the steel easier, because the initial hardening does not need to be as high. Yet it has a very high surface hardness after final forming. This extends die life.
Large, expensive dies that were nitrided previously are easily repairable with conventional welding techniques to allow die reuse.
Note:
1. D. J. Meuleman and T. E. Dwyer, “Die Materials and Treatment with Electrogalvanized Steels,” SAE Technical Paper Series, 880369, 1988, pp. 51-60.
About the Authors
Edward Rolinski
Senior Scientist
subscribe now
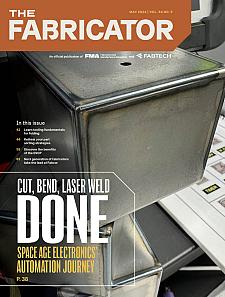
The Fabricator is North America's leading magazine for the metal forming and fabricating industry. The magazine delivers the news, technical articles, and case histories that enable fabricators to do their jobs more efficiently. The Fabricator has served the industry since 1970.
start your free subscription- Stay connected from anywhere
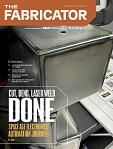
Easily access valuable industry resources now with full access to the digital edition of The Fabricator.
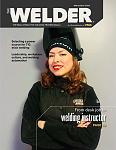
Easily access valuable industry resources now with full access to the digital edition of The Welder.
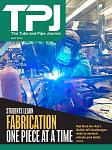
Easily access valuable industry resources now with full access to the digital edition of The Tube and Pipe Journal.
- Podcasting
- Podcast:
- The Fabricator Podcast
- Published:
- 04/16/2024
- Running Time:
- 63:29
In this episode of The Fabricator Podcast, Caleb Chamberlain, co-founder and CEO of OSH Cut, discusses his company’s...
- Trending Articles
Tips for creating sheet metal tubes with perforations
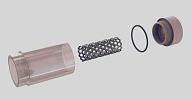
Supporting the metal fabricating industry through FMA
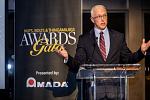
JM Steel triples capacity for solar energy projects at Pennsylvania facility
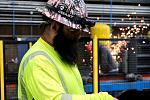
Are two heads better than one in fiber laser cutting?
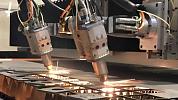
Fabricating favorite childhood memories
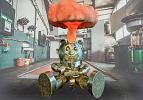
- Industry Events
16th Annual Safety Conference
- April 30 - May 1, 2024
- Elgin,
Pipe and Tube Conference
- May 21 - 22, 2024
- Omaha, NE
World-Class Roll Forming Workshop
- June 5 - 6, 2024
- Louisville, KY
Advanced Laser Application Workshop
- June 25 - 27, 2024
- Novi, MI