- FMA
- The Fabricator
- FABTECH
- Canadian Metalworking
Categories
- Additive Manufacturing
- Aluminum Welding
- Arc Welding
- Assembly and Joining
- Automation and Robotics
- Bending and Forming
- Consumables
- Cutting and Weld Prep
- Electric Vehicles
- En Español
- Finishing
- Hydroforming
- Laser Cutting
- Laser Welding
- Machining
- Manufacturing Software
- Materials Handling
- Metals/Materials
- Oxyfuel Cutting
- Plasma Cutting
- Power Tools
- Punching and Other Holemaking
- Roll Forming
- Safety
- Sawing
- Shearing
- Shop Management
- Testing and Measuring
- Tube and Pipe Fabrication
- Tube and Pipe Production
- Waterjet Cutting
Industry Directory
Webcasts
Podcasts
FAB 40
Advertise
Subscribe
Account Login
Search
R&D Update: Clinching for assembly: A process simulation case study
- October 2, 2017
- Article
- Bending and Forming
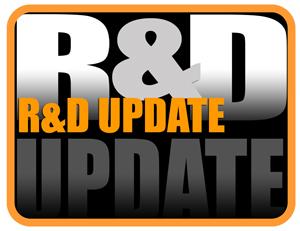
Figure 1
A schematic of sheet-to-sheet clinching illustrates metal flow during the forming process. Source: TOX Pressotechnik GmbH.
Dissimilar or pre-painted materials cannot be welded together, such as steel to aluminum, steel to magnesium, and aluminum to magnesium. Therefore, alternative joining techniques like clinching are required for assembly.
Clinching, or press joining, is an alternative process that someday may compete with spot welding to fasten difficult-to-weld materials. An example of a clinching process is shown in Figure 1 ).
The process forms a leakproof mechanical interlock with higher fatigue strength than spot-welded joints. Clinching equipment can be automated and has low cycle times and extended tool life. It also can be monitored in real time for quality control and does not produce a heat-affected zone (HAZ).
The main disadvantage of clinching is that a joint’s static strength is only one-half to three-quarters of that produced by a spot weld of the same size.
Clinching R&D
Clinching mechanics have not been well-studied because, in the past, aluminum and magnesium sheet was not used extensively, although some attempts have been made to study the process through trial-and-error experimentation. Even though experiments may lead to increased clinched joint strength, the experiments do not provide a fundamental understanding of actual process mechanics.
Using experimentation to study the interaction among several process variables, such as punch geometry, die geometry, sheet thickness, material properties, and friction, would be expensive and time-consuming with results that may be difficult to interpret.
However, finite element analysis (FEA) is an inexpensive way to study the influence of many process variables and provide a time history of metal flow during the forming process. FEA allows for the investigation of different forming scenarios and visualization of metal flow in the clinching process, which may lead to the development of a new forming process with minimal time and expense.
For some clinching applications, it may be necessary to develop new tool geometries, establish the best tool motion, and estimate forming forces and tool stresses.
FEA can be used to explore the basic mechanic that govern metal flow during the clinching process. The sensitivity of the clinched joint to parameters such as punch geometry, die geometry, and clinching temperature can be studied using FEA. A joint’s strength and clinching tool stresses also can be estimated with FEA.
Current FEA clinching studies have focused on clinching joints in which two sheet metals of similar or dissimilar materials are deformed to form the assembly. In other scenarios, however, leakproof joints require hard fasteners to be attached to sheet metal. Therefore, only the sheet metal can be deformed to make a joint. Depending on the size of the fastener, the process window for clinching can be very narrow, but FEA can aid process development.
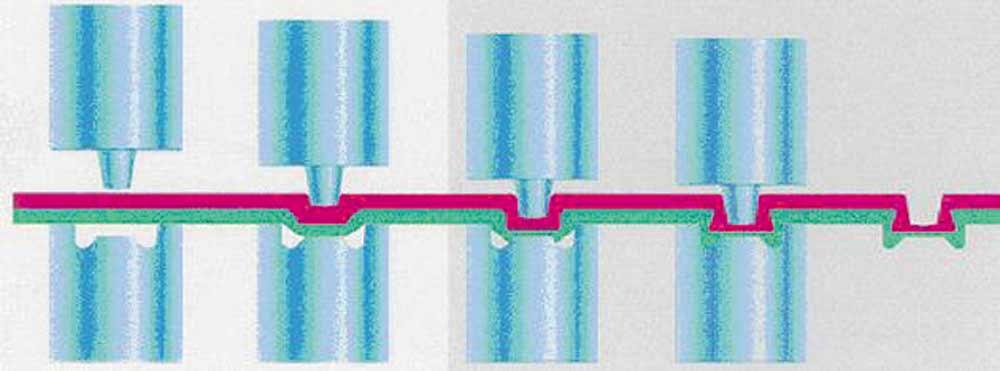
Figure 2
FEA for sheet-to-fastener clinching shows metal flow and effective strain distribution in a preform geometry (top) and the final clinched assembly (bottom).
Figure 2 shows results from sheet-to-fastener clinching simulations. FEA was used to develop the forming sequence, check tool stresses, and estimate the axial load required to remove the fastener from the assembly. Metal flow in sheet-to-fastener clinching experiments matched well with FEA results.
FEA of sheet-to-sheet and sheet-to-fastener clinching can help engineers by providing design guidelines for recommended tool geometries and clinching temperatures for sheet materials. It also can help to estimate static joint strength for different joint size and materials and required forming loads and tool stresses.
subscribe now
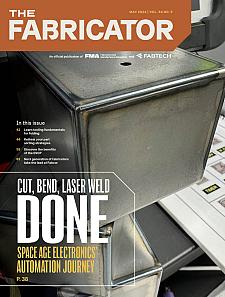
The Fabricator is North America's leading magazine for the metal forming and fabricating industry. The magazine delivers the news, technical articles, and case histories that enable fabricators to do their jobs more efficiently. The Fabricator has served the industry since 1970.
start your free subscription- Stay connected from anywhere
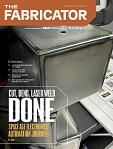
Easily access valuable industry resources now with full access to the digital edition of The Fabricator.
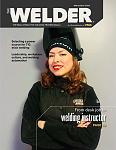
Easily access valuable industry resources now with full access to the digital edition of The Welder.
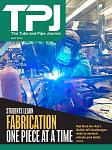
Easily access valuable industry resources now with full access to the digital edition of The Tube and Pipe Journal.
- Podcasting
- Podcast:
- The Fabricator Podcast
- Published:
- 04/16/2024
- Running Time:
- 63:29
In this episode of The Fabricator Podcast, Caleb Chamberlain, co-founder and CEO of OSH Cut, discusses his company’s...
- Industry Events
16th Annual Safety Conference
- April 30 - May 1, 2024
- Elgin,
Pipe and Tube Conference
- May 21 - 22, 2024
- Omaha, NE
World-Class Roll Forming Workshop
- June 5 - 6, 2024
- Louisville, KY
Advanced Laser Application Workshop
- June 25 - 27, 2024
- Novi, MI