Graduate Research Associate
- FMA
- The Fabricator
- FABTECH
- Canadian Metalworking
Categories
- Additive Manufacturing
- Aluminum Welding
- Arc Welding
- Assembly and Joining
- Automation and Robotics
- Bending and Forming
- Consumables
- Cutting and Weld Prep
- Electric Vehicles
- En Español
- Finishing
- Hydroforming
- Laser Cutting
- Laser Welding
- Machining
- Manufacturing Software
- Materials Handling
- Metals/Materials
- Oxyfuel Cutting
- Plasma Cutting
- Power Tools
- Punching and Other Holemaking
- Roll Forming
- Safety
- Sawing
- Shearing
- Shop Management
- Testing and Measuring
- Tube and Pipe Fabrication
- Tube and Pipe Production
- Waterjet Cutting
Industry Directory
Webcasts
Podcasts
FAB 40
Advertise
Subscribe
Account Login
Search
R&D Update: Edge fracture in hole extrusion and flanging, Part I
The effect of process variables
- By Advaith Narayanan, David Diaz-Infante, Dr., and Taylan Altan, Ph.D.
- July 30, 2018
- Article
- Bending and Forming
Editor’s Note: This is Part I of a two-part series that discusses edge fracture in hole extrusion. Part II, which will appear in the September/October 2018 issue, will discuss how to reduce edge fracture in hole extrusion or collar forming.
Hole extrusion, or collar forming, is widely used in stamping (see Figure 1). In this process, the blanked hole with a small diameter is extruded to a collar with a larger diameter. The characteristics of the blanked edge, the ratio between these two diameters, and the radius of the die affect the height of the collar that can be extruded. During extrusion, the metal thins from stretching, which causes the flange thickness to vary. The thinnest part of the extrusion is at the top of the flange. When a higher flange is desired, the thickness in the flange is reduced and determined by the punch/die clearance during collar extrusion. However, in extrusion, the required flanging or extrusion force also is increased.
Hole extruded features, or formed collars, often are used to provide mechanical attachments or threads necessary for assembly. Edge fracture in hole extrusion is a major problem when forming and flanging advanced high-strength steels (AHSS) that exhibit considerable strain hardening and low ductility (see Figure 2).
Common Process Variables
Research indicates that many variables affect both the quality of the blanked edge and the extrusion height that can be achieved without fracture.
The quality of the blanked edge is affected by:
- Material properties (strain hardening behavior, microstructure, presence of inclusions).
- Material thickness.
- Punch/die clearance and its uniformity around the periphery of the blanked part.
- Tool wear.
The height of the collar that can be extruded depends on:
- The quality of the blanked edge.
- Tool geometry used in extrusion, including die diameter and die corner radius.
- Punch geometry.
Often the objective is to estimate the diameter of the initial, smaller blanked hole, provided that the material type and thickness, extruded collar diameter, die corner radius, and desired extruded collar height are known for the given blank.
For relatively low-carbon steels, such as AISI 1008 and AISI 1010, the blanked hole diameter can be estimated using the following formula:
d = D - (2H - 0.86Rd - 1.43T)
Where:
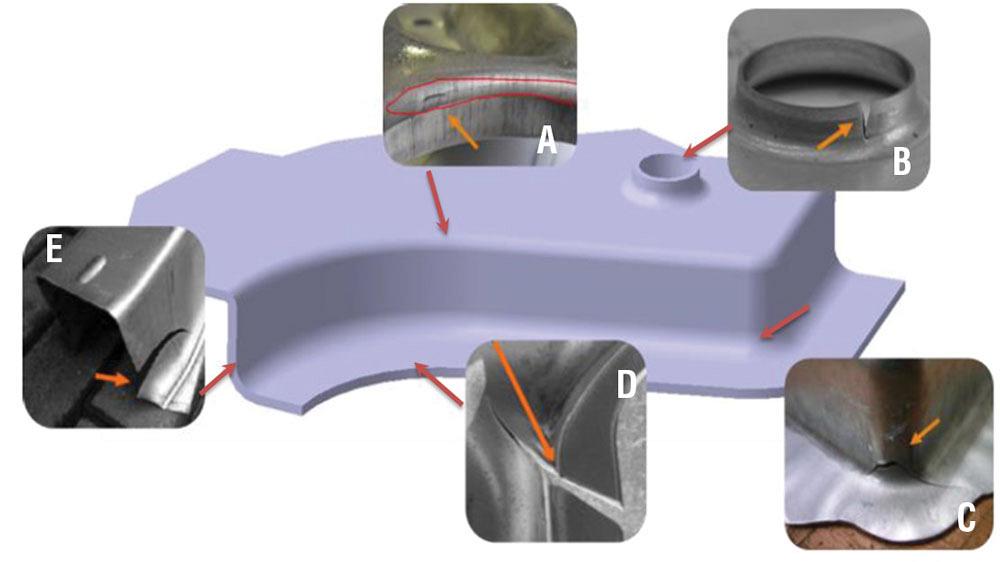
Figure 1
Edge cracking can manifest as a surface crack on the radius (A), edge cracking after hole flanging or collar forming (B), shearing crack at the deep-drawn edge (C), edge cracking at the flange (D), and edge cracking at the open head (E).
- d = Initial hole diameter
- D = Extruded collar diameter
- T = Material thickness
- Rd = Die corner radius
- H = Desired extruded collar height
However, for AHSS, such as DP600 and DP780, this formula does not give reliable results, so a new method for estimating the diameter (d) must be developed.
Effect of Punch/Die Clearance in Blanking
The quality of the blanked or sheared edge affects edge cracking when tensile stresses and strains are imposed on the edge during hole extrusion. The blanked edge is divided into five zones (see Figure 3):
- The rollover zone, where the edge of the sheet is bent by elastic and plastic deformation. The geometry of the rollover zone is determined by the punch/die clearance.
- The shear or burnish zone, a smooth and shiny area obtained by shearing.
- The main fracture zone, where fracture causes the material to separate.
- The burr zone that results from fracture.
- The depth of crack penetration that often is equal to punch/die clearance.
The load-stroke curve of blanking is shown in Figure 4. When the punch contacts the sheet, the blanking force starts to increase suddenly, while the tool and the press are elastically deformed and stretched. When the fracture zone is reached, the blanking force (with elastic and plastic components) sinks abruptly. The rapid increase of the punch force at the start of blanking and the sudden drop in the force when the sheet fractures may cause vibrations and excessive loading of the press and tooling, often called reverse loading, at the end of the process. These excessive vibrations can damage the press and tooling in repetitive operations, especially in blanking AHSS or 8- to 10-millimeter-thick blanks.
Researchers at The Ohio State University’s Center for Precision Forming recently investigated the effect of blanking speed on edge quality, as well as the effect of multiple-step blanking using several punch motions during one blanking stroke. They used a 300-ton AIDA servo press and a blanking tool provided by KTH to blank TRIP780 sheets (see Figure 5).
One of the most interesting results of this study was that the punch/die clearance of the blanking tool (see Figure 6) did not seem to be uniform around the circumference of the tool. The rolling direction in the blanked samples was well indicated. To determine the quality of the blanked edge and to estimate the punch/die clearance at various locations of the blanked hole, the researchers obtained micrographs of the edges and compared them with finite element simulations (see Figure 7) for positions 1 and 3. The hole flanging tests indicated that more fractures occurred near position 1. This observation can be explained by the difference in the punch/die clearance between positions 1 and 3.
References
V. Boljanovic,
Sheet metal forming processes and die design (South Norwalk, Conn.: Industrial Press Inc., 2004).P. Stemler, A. Samant, D. Hofmann, and T. Altan, “Impact of Servo Press Motion on Hole Flanging of High Strength Steels (No. 2017-01-0311),” SAE Technical Paper, 2017.
T. Beier, G. Gula, S. Woestmann, and L. Keßler, “Eine Bewertung des Umformpotenzials von Schnittkanten zur Auslegung von Formgebungsprozessen mit höherfesten Stahlwerkstoffen,” in EFB-Kolloquium Blechverarbeitung, Bad Boll, Germany: Europäische Forschungsgesellschaft für Blechverarbeitung eV, 2015.
About the Authors
Advaith Narayanan
Center for Precision Forming
The Ohio State University 1971 Neil Ave., Room 339 Baker Systems Engineering Building
Columbus, OH 43210
(614) 292-5063
David Diaz-Infante, Dr.
Servo Press Scientist
250 W 5th St.
Minster, OH 45865
o 419 628 2331, d 419 501 1890, m 419 733 7971
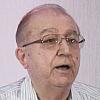
Taylan Altan, Ph.D.
Professor Emeritus and Director - Center for Precision Forming
Related Companies
subscribe now
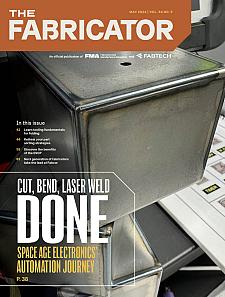
The Fabricator is North America's leading magazine for the metal forming and fabricating industry. The magazine delivers the news, technical articles, and case histories that enable fabricators to do their jobs more efficiently. The Fabricator has served the industry since 1970.
start your free subscription- Stay connected from anywhere
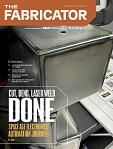
Easily access valuable industry resources now with full access to the digital edition of The Fabricator.
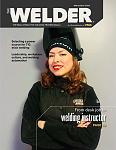
Easily access valuable industry resources now with full access to the digital edition of The Welder.
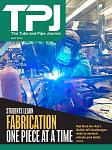
Easily access valuable industry resources now with full access to the digital edition of The Tube and Pipe Journal.
- Podcasting
- Podcast:
- The Fabricator Podcast
- Published:
- 04/16/2024
- Running Time:
- 63:29
In this episode of The Fabricator Podcast, Caleb Chamberlain, co-founder and CEO of OSH Cut, discusses his company’s...
- Trending Articles
Tips for creating sheet metal tubes with perforations
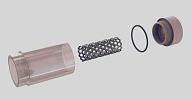
Supporting the metal fabricating industry through FMA
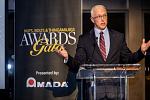
JM Steel triples capacity for solar energy projects at Pennsylvania facility
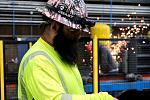
Fabricating favorite childhood memories
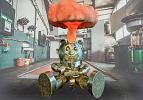
Omco Solar opens second Alabama manufacturing facility
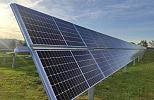
- Industry Events
16th Annual Safety Conference
- April 30 - May 1, 2024
- Elgin,
Pipe and Tube Conference
- May 21 - 22, 2024
- Omaha, NE
World-Class Roll Forming Workshop
- June 5 - 6, 2024
- Louisville, KY
Advanced Laser Application Workshop
- June 25 - 27, 2024
- Novi, MI