Professor Emeritus and Director - Center for Precision Forming
- FMA
- The Fabricator
- FABTECH
- Canadian Metalworking
Categories
- Additive Manufacturing
- Aluminum Welding
- Arc Welding
- Assembly and Joining
- Automation and Robotics
- Bending and Forming
- Consumables
- Cutting and Weld Prep
- Electric Vehicles
- En Español
- Finishing
- Hydroforming
- Laser Cutting
- Laser Welding
- Machining
- Manufacturing Software
- Materials Handling
- Metals/Materials
- Oxyfuel Cutting
- Plasma Cutting
- Power Tools
- Punching and Other Holemaking
- Roll Forming
- Safety
- Sawing
- Shearing
- Shop Management
- Testing and Measuring
- Tube and Pipe Fabrication
- Tube and Pipe Production
- Waterjet Cutting
Industry Directory
Webcasts
Podcasts
FAB 40
Advertise
Subscribe
Account Login
Search
R&D Update: Evaluating lubricants using the stamping lubricant tester (SLT)
- By Taylan Altan, Ph.D.
- August 15, 2017
- Article
- Bending and Forming
Friction between a sheet blank and a press’s dies plays an important role in stamping parts. Fracture and wrinkling are influenced by frictional behavior, and many stampers use lubricants to reduce friction.
To produce quality parts, stamping lubricants most perform at high pressures; high temperatures; and when the material slides over a die, punch, or blank holder surface. The stamping lubricant tester (SLT) shown in Figure 1 studies lubricant performance under combined blank holder and draw bread forces.
Lubricant Research Parameters
The SLT involves coating a sheet with a test lubricant, clamping the sheet in the draw bead dies at the desired blank holder force, and pulling the sheet at the test velocity. This pulling velocity and blank holder force can be changed to emulate deep-drawing conditions. Different sheet materials and lubricants can be readily tested because the test is easy to run.
The SLT at lubricant manufacturer Lubrizol Metalworking Additives has die-heating capability, so lubricants used in multistage mass production and warm forming operations can be tested. Heat generated during mass production affects lubricant properties.
SLT Output
Frictional forces and pulling forces vary for lubricants. During the test, a sheet is pulled through the dies and the pulling force profile is obtained from a data acquisition system, as shown in Figure 2 . The pulling force profile characterizes lubricant performance used in the test.
Testing Lubricants
Lubricant performance can be quantified by a coefficient of friction (μ), which is the ratio of friction force and the normal force applied on the friction surface. The coefficient of friction depends not only on the lubricant, but also on the test conditions (sheet material, temperature, pulling velocity, and blank holder force).
Figure 3 illustrates that the pulling force is a combination of frictional force and bending/ unbending under the draw bead. In the SLT, the ratio of the pulling force to the normal force (blank holder force) does not represent the coefficient of the friction, μ. Therefore, an SLT can compare a set of lubricants for a given condition.
To make better use of the SLT, researchers at the ERC/NSM conducted a study to evaluate lubricant performance under various conditions. Various values of the μ were input into a finite element analysis (FEA) model until the calculated pulling force profile matched the experimental results. Simulation results also were compared with analytical results obtained from Stoughton’s mathematical model.
Figure 4 shows the results for stainless steel (SS316). Using a coefficient of friction of 0.18. The left bar graph shows FEA predictions are within 5 percent of experimental results. The right graph indicates that an iterative FEA approach can help estimate the coefficient of friction. Using this technique, lubricant manufactures can assess the performance of a lubricant for various blank holder forces, velocities, and sheet material conditions. Using FEA simulations, they can formulate effective lubricants and additives for stamping applications.
About the Author
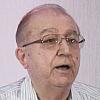
Taylan Altan, Ph.D.
subscribe now
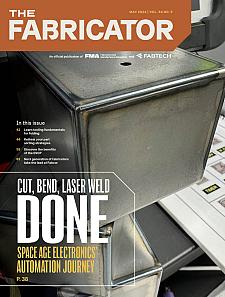
The Fabricator is North America's leading magazine for the metal forming and fabricating industry. The magazine delivers the news, technical articles, and case histories that enable fabricators to do their jobs more efficiently. The Fabricator has served the industry since 1970.
start your free subscription- Stay connected from anywhere
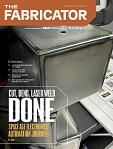
Easily access valuable industry resources now with full access to the digital edition of The Fabricator.
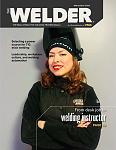
Easily access valuable industry resources now with full access to the digital edition of The Welder.
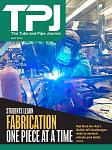
Easily access valuable industry resources now with full access to the digital edition of The Tube and Pipe Journal.
- Podcasting
- Podcast:
- The Fabricator Podcast
- Published:
- 04/30/2024
- Running Time:
- 53:00
Seth Feldman of Iowa-based Wertzbaugher Services joins The Fabricator Podcast to offer his take as a Gen Zer...
- Industry Events
16th Annual Safety Conference
- April 30 - May 1, 2024
- Elgin,
Pipe and Tube Conference
- May 21 - 22, 2024
- Omaha, NE
World-Class Roll Forming Workshop
- June 5 - 6, 2024
- Louisville, KY
Advanced Laser Application Workshop
- June 25 - 27, 2024
- Novi, MI