- FMA
- The Fabricator
- FABTECH
- Canadian Metalworking
Categories
- Additive Manufacturing
- Aluminum Welding
- Arc Welding
- Assembly and Joining
- Automation and Robotics
- Bending and Forming
- Consumables
- Cutting and Weld Prep
- Electric Vehicles
- En Español
- Finishing
- Hydroforming
- Laser Cutting
- Laser Welding
- Machining
- Manufacturing Software
- Materials Handling
- Metals/Materials
- Oxyfuel Cutting
- Plasma Cutting
- Power Tools
- Punching and Other Holemaking
- Roll Forming
- Safety
- Sawing
- Shearing
- Shop Management
- Testing and Measuring
- Tube and Pipe Fabrication
- Tube and Pipe Production
- Waterjet Cutting
Industry Directory
Webcasts
Podcasts
FAB 40
Advertise
Subscribe
Account Login
Search
R&D Update: Examining edge cracking in hole flanging of AHSS
- October 2, 2017
- Article
- Bending and Forming
Factors such as edge condition before flanging, punch shape, shearing operation, and the microstructure (volume fractions of the different phases) affect the ability of the hole flange to stretch. The forming limit curve (FLC) traditionally used to evaluate formability is not sufficient to predict potential edge cracking because FLC represents the limit of stretching but not bending.
Therefore, the edge stretchability is studied using a hole expansion test that can emulate the stress/strain conditions formed during hole flanging. In the hole expansion test, a pierced hole is expanded to fracture using a conical, hemispherical, or flat-bottom punch to evaluate its edge stretchability. A blank holder clamps the sheet to restrict the material movement in the flange (see Figure 2 ). The edge of the hole is under stretching and bending conditions. Therefore, the circumferential strain/stress along the edge leads to cracking. It is most probable, however, that a complex stress/strain history, and the edge quality of the pierced hole, can determine when edge cracking occurs.
Researchers investigated the edge stretching limits of various steel grades with different sheet thicknesses using hole flanging experiments with both a conical punch and a flat-bottom punch to punch the material. The researchers observed that mild steel and high-strength steel (HSS) had hole expansion ratios beyond 100 percent while the AHSS [transformation-induced plasticity (TRIP), dual phase (DP), recovery annealed steel (RA), and martensitic steels] have expansion ratios of about 50 percent (see Figure 3 ). Also, TRIP steels have the same hole expansion ratio as DP steels, although TRIP steels generally have better formability than DP steels, as measured by total elongation in the tensile test.
Effects of Edge Quality, Microstructure
Various shearing operations that are used to form the pre hole, as well as the tool’s condition, directly influence sheared edge quality. Tests showed that, as expected, the hole expansion ratio of AHSS decreased as the punch wore out during production.
Other studies showed that hole flange stretchability of a wire-cut hole was better than a drilled or punched hole, indicating that the edge quality of the hole has a significant influence upon hole flange stretchability. Also, the level of martensite in the material and the homogeneity of its microstructure had considerable influence on hole flange stretchability. For example, CP 800 has more homogenous microstructure compared to DP 800. Therefore, although CP 800 has lower formability in terms of tensile properties, hole expansion ratios are lower for DP 800.
Prediction of Edge Cracking in Hole Flanging
It is desirable to predict and eliminate the edge cracking in hole flanging. Some studies use FEA together with thickness distribution and damage values as a fracture criterion.
In our preliminary study, the FEA commercial code DEFORM-2D was used to establish a relationship between the stress/strain states in hole flanging, material properties, and the edge quality of the prehole. We compared the FEA predictions for mild steel and HSS with experimental data from other research (see Figure 4 ). The initial blank had an outer diameter of 80 millimeters and a pre hole diameter of 10 mm. The die and punch diameters were 42.5 mm and 40 mm, respectively. A conical punch with an angle of 60 degrees was used.
Preliminary FEA simulation results showed agreement with experimental data. Similar results were obtained when comparing the FE predictions with hole flanging using a spherical punch.
subscribe now
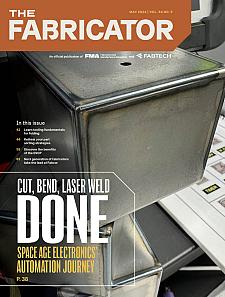
The Fabricator is North America's leading magazine for the metal forming and fabricating industry. The magazine delivers the news, technical articles, and case histories that enable fabricators to do their jobs more efficiently. The Fabricator has served the industry since 1970.
start your free subscription- Stay connected from anywhere
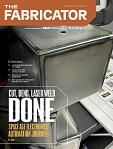
Easily access valuable industry resources now with full access to the digital edition of The Fabricator.
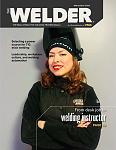
Easily access valuable industry resources now with full access to the digital edition of The Welder.
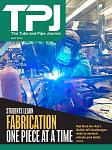
Easily access valuable industry resources now with full access to the digital edition of The Tube and Pipe Journal.
- Podcasting
- Podcast:
- The Fabricator Podcast
- Published:
- 04/16/2024
- Running Time:
- 63:29
In this episode of The Fabricator Podcast, Caleb Chamberlain, co-founder and CEO of OSH Cut, discusses his company’s...
- Trending Articles
Tips for creating sheet metal tubes with perforations
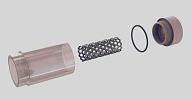
Are two heads better than one in fiber laser cutting?
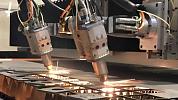
Supporting the metal fabricating industry through FMA
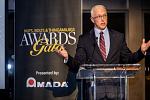
JM Steel triples capacity for solar energy projects at Pennsylvania facility
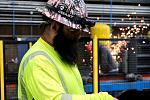
Omco Solar opens second Alabama manufacturing facility
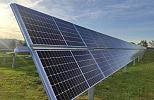
- Industry Events
16th Annual Safety Conference
- April 30 - May 1, 2024
- Elgin,
Pipe and Tube Conference
- May 21 - 22, 2024
- Omaha, NE
World-Class Roll Forming Workshop
- June 5 - 6, 2024
- Louisville, KY
Advanced Laser Application Workshop
- June 25 - 27, 2024
- Novi, MI