Servo Press Scientist
- FMA
- The Fabricator
- FABTECH
- Canadian Metalworking
Categories
- Additive Manufacturing
- Aluminum Welding
- Arc Welding
- Assembly and Joining
- Automation and Robotics
- Bending and Forming
- Consumables
- Cutting and Weld Prep
- Electric Vehicles
- En Español
- Finishing
- Hydroforming
- Laser Cutting
- Laser Welding
- Machining
- Manufacturing Software
- Materials Handling
- Metals/Materials
- Oxyfuel Cutting
- Plasma Cutting
- Power Tools
- Punching and Other Holemaking
- Roll Forming
- Safety
- Sawing
- Shearing
- Shop Management
- Testing and Measuring
- Tube and Pipe Fabrication
- Tube and Pipe Production
- Waterjet Cutting
Industry Directory
Webcasts
Podcasts
FAB 40
Advertise
Subscribe
Account Login
Search
R&D Update: Industry 4.0 and the use of sensors in sheet metal forming
- By David Diaz-Infante, Dr. and Taylan Altan, Ph.D.
- December 6, 2018
- Article
- Bending and Forming
Industry 4.0 is an initiative that aims to drive digital manufacturing forward by increasing digitization and interconnection of products, value chains, and business models. In simpler words, this initiative suggests to improve a given process by recording and using all the information available from the very beginning of the process to its end.
Data mining (see Figure 1) now is possible thanks to the various systems that can measure and control different aspects of a given process. Data mining can be applied to sheet metal forming, with the main objective being to form a defect-free part of desired dimensions, without wrinkles or fractures. This objective can be achieved by measuring and/or controlling material properties, material flow, lubrication conditions, forming forces, surface roughness, and tool dynamics. Figure 2 shows examples of sensors used to measure some of these parameters.
Material Flow Measurement
Measuring the amount of material flowing into the die cavity is useful to control the forming process. On one hand, insufficient material flow may lead to excessive thinning and eventually to fracture. On the other hand, excessive material flow can cause wrinkles.
AUDI AG plants in Neckarsulm and Ingolstadt use laser sensors to measure the material flow. This information is sent to an algorithm that electronically adjusts, per stroke, the height of the spacers, which are two wedges located between the lower die and the blank holder/binder to control material flow into the die cavity.
Measurement of Forces
Force sensors, also referred to as tonnage monitors, can record either the peak load values or the load as a function of slide displacement or time. These sensors typically are placed in the press frame, the connecting rods, the slide, or directly in the tool.
Force measurement can be used to prevent press overloading or off-center loading, to monitor tool wear, and to detect changes in lubrication or material fracture (see Figure 3a). Load cells and piezoelectric sensors are the most commonly used force-measuring devices.
Detection of Tool Breakage and Part Flaws
In addition to force sensors, ultrasonic or acoustic emission sensors also can be employed to detect some changes in the process (see Figure 3b). When a crack is generated in the workpiece or tool, waves are propagated from this crack and can be recorded by ultrasonic and acoustic emission sensors. Special care is required to locate and interpret results from this type of sensor, since noise signals can interfere with the measurements.
Displacement Sensors
Typically used for tracking the die position to prevent crashes, displacement sensors also can be used to detect wrinkle initiation on the flange of the blank during a stamping or deep drawing process. Displacement sensors can indicate when wrinkling occurs in the flange (see Figure 3c).
This technique can be important in an automated process in which the blank holder force can be adjusted locally. Linear variable differential transformers, proximity sensors, ultrasonic sensors, and photoelectric sensors are used for these tasks.
Online Material Property Evaluation
The material’s mechanical properties have a significant effect on processing conditions and part quality. The material’s formability can be determined by the yield strength, ultimate tensile strength, uniform elongation, elongation and fracture, and hardness, and all these properties can vary from batch to batch or even within the same batch.
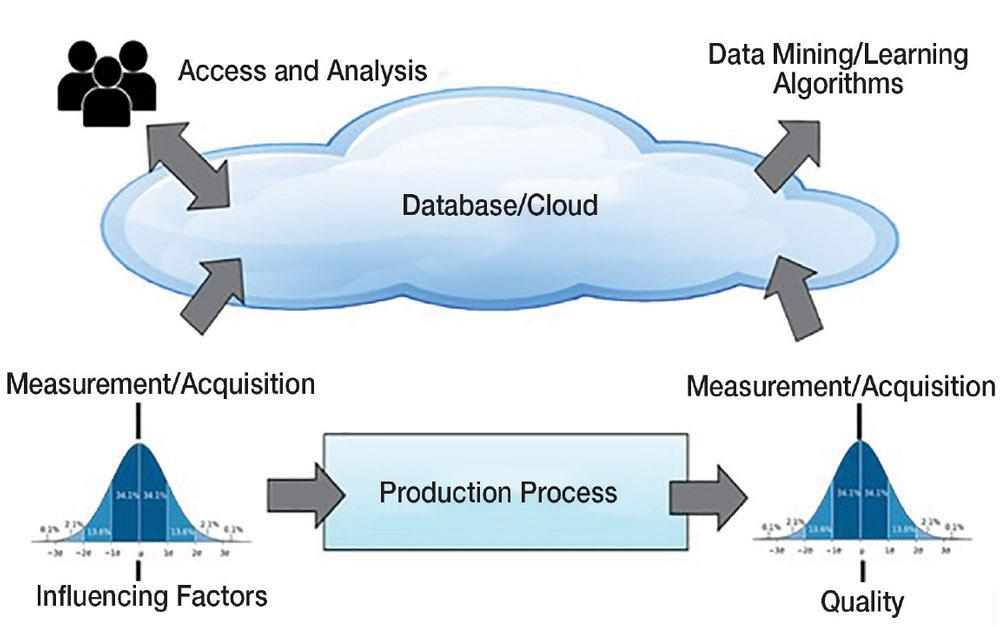
Figure 1
These are the basic principles of using the data mining method in the press shop (Meinhardt et al, 2018).
Therefore, in large-volume production, it is good practice to measure each coil’s properties before use. This can be accomplished by conducting tensile tests or using an eddy current sensor. When the material’s mechanical properties are identified, adjustments can be made to press speed, blank holder force, and lubrication to improve forming results.
Lubrication Control
The amount and type of lubricant required can vary depending on its main purpose: cooling the blank and tools, reducing tool wear, or improving material flow. The amount can also depend on the surface roughness of the material under consideration.
Techniques such as spectroscopy can be used to measure lubricant thickness in real time during production. BMW has installed a system that records the amount of lubricant along the width of the incoming coil. An additional system, placed along the sensor measuring lubricant thickness, adds a tailored amount of lubricant to a target spot where a lack of lubricant is detected.
Application of Industry 4.0 at the BMW Group
BMW has applied data mining successfully at its press shop in Regensburg, Germany, improving production of the 3 Series Sedan side frame made of 0.7-millimeter-thick DC03.
All the information required is tracked from the beginning to the end of the process. Sensors continuously record lubricant film thickness, mechanical properties, sheet thickness, and sheet topography. The side frames are marked with 10-digit alphanumeric code. Cameras using optical character recognition read the code. In series production, up to 18 sample records per minute can be generated per press line.
Data mining showed some trends, such as larger concentrations of lubricant either at the beginning or at the end of the strip. Also, variations in thickness were most common toward the end of the coil, even when the material thickness was within specifications (0.7 +/- 0.035 mm). Using all the collected data and decision trees, BMW can track flaws on parts back to the root of the problem to improve its manufacturing process.
References
J. M. Allwood et al, “Closed-loop control of product properties in metal forming,” CIRP Annals, Vol. 65, No. 2 (2016), pp. 573-596.
J. Meinhardt, R. Hummelsberger, K. Grossenbacher, and S. Purr, “Strategic orientation of the BMW Group’s Press Shops,” in proceedings from New Developments in Sheet Metal Forming, IFU-Technical University of Stuttgart, May 15-16, 2018, pp. 187-194.
About the Authors
David Diaz-Infante, Dr.
250 W 5th St.
Minster, OH 45865
o 419 628 2331, d 419 501 1890, m 419 733 7971
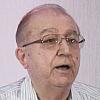
Taylan Altan, Ph.D.
Professor Emeritus and Director - Center for Precision Forming
Related Companies
subscribe now
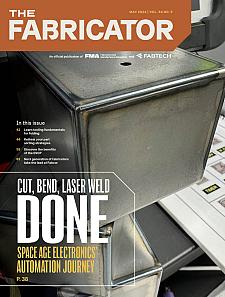
The Fabricator is North America's leading magazine for the metal forming and fabricating industry. The magazine delivers the news, technical articles, and case histories that enable fabricators to do their jobs more efficiently. The Fabricator has served the industry since 1970.
start your free subscription- Stay connected from anywhere
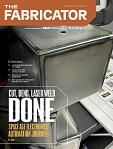
Easily access valuable industry resources now with full access to the digital edition of The Fabricator.
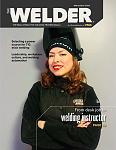
Easily access valuable industry resources now with full access to the digital edition of The Welder.
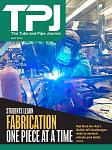
Easily access valuable industry resources now with full access to the digital edition of The Tube and Pipe Journal.
- Podcasting
- Podcast:
- The Fabricator Podcast
- Published:
- 04/16/2024
- Running Time:
- 63:29
In this episode of The Fabricator Podcast, Caleb Chamberlain, co-founder and CEO of OSH Cut, discusses his company’s...
- Trending Articles
Tips for creating sheet metal tubes with perforations
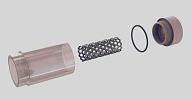
Supporting the metal fabricating industry through FMA
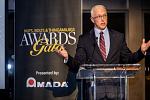
JM Steel triples capacity for solar energy projects at Pennsylvania facility
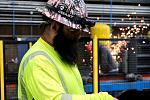
Fabricating favorite childhood memories
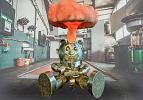
Omco Solar opens second Alabama manufacturing facility
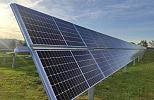
- Industry Events
16th Annual Safety Conference
- April 30 - May 1, 2024
- Elgin,
Pipe and Tube Conference
- May 21 - 22, 2024
- Omaha, NE
World-Class Roll Forming Workshop
- June 5 - 6, 2024
- Louisville, KY
Advanced Laser Application Workshop
- June 25 - 27, 2024
- Novi, MI