Graduate Research Associate - Center for Precision Forming
- FMA
- The Fabricator
- FABTECH
- Canadian Metalworking
Categories
- Additive Manufacturing
- Aluminum Welding
- Arc Welding
- Assembly and Joining
- Automation and Robotics
- Bending and Forming
- Consumables
- Cutting and Weld Prep
- Electric Vehicles
- En Español
- Finishing
- Hydroforming
- Laser Cutting
- Laser Welding
- Machining
- Manufacturing Software
- Materials Handling
- Metals/Materials
- Oxyfuel Cutting
- Plasma Cutting
- Power Tools
- Punching and Other Holemaking
- Roll Forming
- Safety
- Sawing
- Shearing
- Shop Management
- Testing and Measuring
- Tube and Pipe Fabrication
- Tube and Pipe Production
- Waterjet Cutting
Industry Directory
Webcasts
Podcasts
FAB 40
Advertise
Subscribe
Account Login
Search
R&D Update: Reducing springback using poststretching with stake beads
- By Ali Fallahiarezoodar, Tanmay Gupta, and Taylan Altan, Ph.D.
- June 4, 2018
- Article
- Bending and Forming
Reducing springback, especially when forming advanced high-strength steels (AHSS), is a major challenge in sheet metal forming. The article “Reducing springback in hat-shape bending with variable BHF using a servo-hydraulic cushion,” published in the March/April 2018 issue of STAMPING Journal®, discussed the use of a servo-hydraulic cushion and variable blank holder force (BHF) for poststretching and reducing springback.
Figure 1 illustrates a simple hat-shape bending operation. In this application, the draw-in of the sheet material is controlled by the BHF, and the sheet material goes through both bending and unbending deformation. As a result of elastic recovery of the strains, the material has a natural tendency to unbend itself in the side wall and in the bending corners of the hat-shaped part. This causes the side wall to curl, affecting the dimensional accuracy and final shape of the formed part.
Springback is the result of nonuniform distribution of stresses in sheet thickness. Thus, additional stretch/tension force on the part can reduce this nonuniform stress distribution and, consequently, the springback. Poststretching is a common way to reduce springback in drawn parts. In this method, additional BHF is applied toward the end of deformation, which causes additional stretch on the side wall and reduces the nonuniform stress distributions.
Figure 2 illustrates how poststretching can drastically modify the stress distributions in the wall from tensile-compression to tensile only. As a result, appropriate poststretching can reduce the springback in the part.
Poststretching can be achieved using a variable BHF, but many North American stampers do not use servo-hydraulic cushions to generate variable BHF. Another way to reduce springback with poststretching is with stake beads. Figure 3 shows the tool setup at the start of deformation (a), followed by the upper die moving down and forming the material up to the stroke where the beads start touching the blank (b). The blank then is formed into the beads area, and stretch force is applied on the side wall during the last few millimeters of the upper die stroke (c). Different designs can be considered for the stake bead (d).
For this method to be used, usually the die is designed so that:
- The stake bead will not break or wear out easily.
- The stretching of the material in the bead itself does not cause any local fracture or cracks.
- It provides adequate stretch at the side wall to reduce springback.
As the blank is formed, when the beads start touching the sheet material, higher BHF is required to prevent an opening between the die and the blank holder. As a result, the total load on the die and press ram increases dramatically. The load versus displacement curve shown in Figure 4 shows the reaction force applied on the blank holder during the deformation. The reaction force is calculated using simulation with a constant gap between the die and the blank holder. In reality, however, when nitrogen cylinders or an air cushion is used, the BHF cannot be controlled or increased toward the end stroke like it can be done with a servo-hydraulic cushion. Therefore, a high BHF should be applied at the beginning of the deformation stroke. This is one of the limitations of using stake beads for poststretching.
For the increase of force in forming with stake beads to be minimized, the die design requires a stake bead radius and height that eliminate the possibility of fracture in the formed part wall and the bead region. In addition, the maximum force on the die (Fmax in Figure 4) should be as small as possible. Different bead designs were investigated by researchers at The Ohio State University’s Center for Precision Forming (CPF), and the results showed that the maximum force on the die decreases by about 30 percent when an edge bead is used as compared to a circular bead. Also, the side wall curl is smaller with an edge bead.
In cooperation with Hyson Metalforming Solutions, CPF conducted a study of forming a hat-shaped part from 1.2-mm Al5182-O using a servo-hydraulic cushion. The results showed that using a variable BHF can significantly reduce springback and side wall curl. Figure 5 shows the profile of the experimental result compared to numerical simulations. Simulations showed side wall curl can be reduced by using either variable BHF and a servo-hydraulic cushion or constant BHF and stake beads.
CPF researchers currently are working to develop a method for optimizing stake bead design.
About the Authors
Ali Fallahiarezoodar
Tanmay Gupta
Graduate Research Associate - Center for Precision Forming
1971 Neil Ave. Baker Systems Engineering, Room 339
Columbus, OH 43210
(614)-292-5063
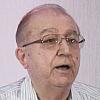
Taylan Altan, Ph.D.
Professor Emeritus and Director - Center for Precision Forming
Related Companies
subscribe now
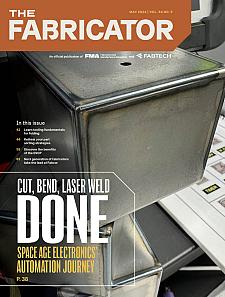
The Fabricator is North America's leading magazine for the metal forming and fabricating industry. The magazine delivers the news, technical articles, and case histories that enable fabricators to do their jobs more efficiently. The Fabricator has served the industry since 1970.
start your free subscription- Stay connected from anywhere
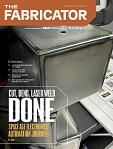
Easily access valuable industry resources now with full access to the digital edition of The Fabricator.
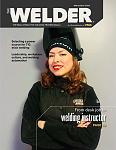
Easily access valuable industry resources now with full access to the digital edition of The Welder.
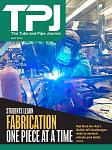
Easily access valuable industry resources now with full access to the digital edition of The Tube and Pipe Journal.
- Podcasting
- Podcast:
- The Fabricator Podcast
- Published:
- 04/16/2024
- Running Time:
- 63:29
In this episode of The Fabricator Podcast, Caleb Chamberlain, co-founder and CEO of OSH Cut, discusses his company’s...
- Trending Articles
Tips for creating sheet metal tubes with perforations
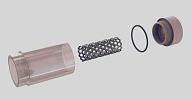
Supporting the metal fabricating industry through FMA
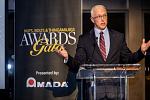
JM Steel triples capacity for solar energy projects at Pennsylvania facility
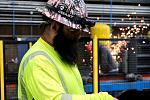
Fabricating favorite childhood memories
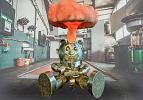
Omco Solar opens second Alabama manufacturing facility
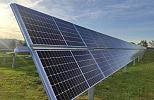
- Industry Events
16th Annual Safety Conference
- April 30 - May 1, 2024
- Elgin,
Pipe and Tube Conference
- May 21 - 22, 2024
- Omaha, NE
World-Class Roll Forming Workshop
- June 5 - 6, 2024
- Louisville, KY
Advanced Laser Application Workshop
- June 25 - 27, 2024
- Novi, MI