- FMA
- The Fabricator
- FABTECH
- Canadian Metalworking
Categories
- Additive Manufacturing
- Aluminum Welding
- Arc Welding
- Assembly and Joining
- Automation and Robotics
- Bending and Forming
- Consumables
- Cutting and Weld Prep
- Electric Vehicles
- En Español
- Finishing
- Hydroforming
- Laser Cutting
- Laser Welding
- Machining
- Manufacturing Software
- Materials Handling
- Metals/Materials
- Oxyfuel Cutting
- Plasma Cutting
- Power Tools
- Punching and Other Holemaking
- Roll Forming
- Safety
- Sawing
- Shearing
- Shop Management
- Testing and Measuring
- Tube and Pipe Fabrication
- Tube and Pipe Production
- Waterjet Cutting
Industry Directory
Webcasts
Podcasts
FAB 40
Advertise
Subscribe
Account Login
Search
R&D Update: Warm-forming and magnesium , Part I
Part I: Forming a round cup
- September 6, 2017
- Article
- Bending and Forming
Warm-forming Aluminum, Magnesium Alloys
The automotive industry’s mandate to use more lightweight metals in structural and body part is constantly increasing. As a result, researchers in North America and around the world are conducting extensive studies to increase aluminum’s (Al) and magnesiums (Mg) formability at elevated temperatures.
To obtain material properties and determine incoming sheet quality for Mg AZ31-O alloys, ERC-NSM has conducted elevated-temperature hydraulic bulge tests, which demonstrate significant formability increases and property variations. The study’s objective is to develop a warm-forming process for Mg and Al alloy sheets with an emphasis on material, tooling, lubrication, and process design. Warm-forming is influenced by incoming sheet quality and mechanical properties, tool geometry (punch and die corner radii), die and blank holder temperature, punch temperature, dwell time, blank holder force, forming velocity, and lubrication.
Round Cup Forming
ERC/NSM and AIDA Engineering Ltd., Japan, designed and manufactured a tool for round cup forming at elevated temperatures. This design was selected because because deformation in round cup deep drawing is quite severe compared with most stamping operations. Deep drawing round cups also provides fundamental information for forming more complex parts.
The tool is capable of heating the die and blank holder up to 300 degrees C. The sheet heated inside the tool is equipped with a punch cooling system and three interchangeable die rings (3 mm, 4 mm, and 6 mm). These die rings have minimum contact with the die insert to keep them relatively cool. The tool set is tested in a 110-ton, single-action servomotor press. The servo press provides infinite velocity programming, including blank approach, dwell, and forming velocity (see Figure 1 ).
Figure 2 illustrates the process sequence used during the experiments. Initially the blank is placed on the bottom die and blank holder. After the dwelling period, the top ram moves farther down against the stationary punch and the sheet is formed.
In preliminary experiments, alloys AL 5754-O, Al 5052-H32, and Mg AZ31-O were used and LDR values of 2.9, 2.9, and 3.2 were obtained, respectively (see Figure 3 ). For the LDR to be accurate, the cup must be fully drawn. As shown in Figure 3, all cups from Al 5754-O and Al 5052-H32 are fully drawn. For Mg AZ31-O, LDR 2.6 is fully drawn, but LDR 3.2 has some flange. To be accurate, ERC/NSM uses the cup height to punch diameter radio (HDR) to represent formability. For determining the HDR for cups with ears, cup height is hmin , as shown in Figure 4 . Specific ratios are provided in Figure 3.
Preliminary experiments found that high formability is possible with appropriate punch and die and blank holder temperatures. For Mg AZ31-O, no formability improvement was observed was observed up to 175 degrees C. It’s well-known that lubrication and heat transfer play significant roles in any process in which temperature is involved.
Warm-forming of lightweight alloys is in the development stages. Future experiments will include more detailed finite element-based deformation analysis and process-related parameters such as interface heat transfer coefficient of aluminum, magnesium, and titanium alloys.
We will try to obtain the same deformation levels with higher forming speeds and lower cycle times. Our efforts are ongoing to obtain the finite element model of this process which could optimize the process sequence further. The hope is that this project will establish process and tool design guidelines and process operation windows for future industrial applications.
subscribe now
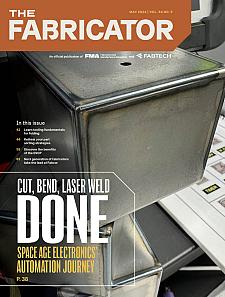
The Fabricator is North America's leading magazine for the metal forming and fabricating industry. The magazine delivers the news, technical articles, and case histories that enable fabricators to do their jobs more efficiently. The Fabricator has served the industry since 1970.
start your free subscription- Stay connected from anywhere
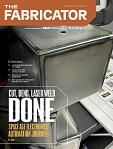
Easily access valuable industry resources now with full access to the digital edition of The Fabricator.
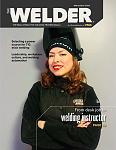
Easily access valuable industry resources now with full access to the digital edition of The Welder.
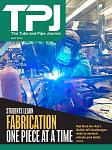
Easily access valuable industry resources now with full access to the digital edition of The Tube and Pipe Journal.
- Podcasting
- Podcast:
- The Fabricator Podcast
- Published:
- 04/16/2024
- Running Time:
- 63:29
In this episode of The Fabricator Podcast, Caleb Chamberlain, co-founder and CEO of OSH Cut, discusses his company’s...
- Trending Articles
Tips for creating sheet metal tubes with perforations
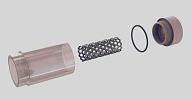
Are two heads better than one in fiber laser cutting?
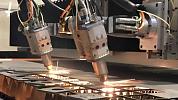
Supporting the metal fabricating industry through FMA
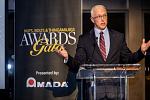
JM Steel triples capacity for solar energy projects at Pennsylvania facility
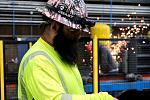
Omco Solar opens second Alabama manufacturing facility
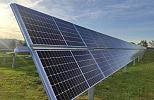
- Industry Events
16th Annual Safety Conference
- April 30 - May 1, 2024
- Elgin,
Pipe and Tube Conference
- May 21 - 22, 2024
- Omaha, NE
World-Class Roll Forming Workshop
- June 5 - 6, 2024
- Louisville, KY
Advanced Laser Application Workshop
- June 25 - 27, 2024
- Novi, MI