Contributing Writer
- FMA
- The Fabricator
- FABTECH
- Canadian Metalworking
Categories
- Additive Manufacturing
- Aluminum Welding
- Arc Welding
- Assembly and Joining
- Automation and Robotics
- Bending and Forming
- Consumables
- Cutting and Weld Prep
- Electric Vehicles
- En Español
- Finishing
- Hydroforming
- Laser Cutting
- Laser Welding
- Machining
- Manufacturing Software
- Materials Handling
- Metals/Materials
- Oxyfuel Cutting
- Plasma Cutting
- Power Tools
- Punching and Other Holemaking
- Roll Forming
- Safety
- Sawing
- Shearing
- Shop Management
- Testing and Measuring
- Tube and Pipe Fabrication
- Tube and Pipe Production
- Waterjet Cutting
Industry Directory
Webcasts
Podcasts
FAB 40
Advertise
Subscribe
Account Login
Search
Die Science: Reducing lead-times and tooling cost, Part II
- By Art Hedrick
- June 23, 2017
- Article
- Bending and Forming
One of the common problems I hear from tooling buyers is that the quotes they receive often are significantly different. It’s not unusual for one die shop to quote a job at $50,000 and another shop to quote $75,000 on the same tool. What are the differences between those two dies? Will the lower-cost die perform as well as the more expensive one?
First of all, understand that a significant difference in quotes is most likely process-related. In other words, the die supply shop that quoted it more than likely created the process that they felt could produce the part within the part specifications. Perhaps the lower-cost shop felt that certain hole locations could be developed in the flat blank, while the more expensive shop elected to use cam slides to put the holes in after the forming was completed, which adds more stations to the die and increases tooling costs. Perhaps the more expensive tool shop was planning to use cheaper conventional tool steel.
Other factors that affect tooling cost are the shop’s geographic location, current work load, niche, efficiency, experience, and how well the shop is paid by its costumers.
Determining the Best Value
To determine which tool is the better choice, first try to separate tooling cost from value. In other words, of what value is poorly processed, lower-cost tool that doesn’t perform as intended? The truth is that the die may be more of a liability than an asset.
They key to purchasing a quality, well-performing tool is to do so with a good understanding of what is necessary for the tool to perform adequately. The best resource for this information can come form many of the people who deal day in and day out with die and part problems.
Many stamping companies produce a variety of similar parts. Through years of experience, they understand just what needs to go into the tool for it to work. Unfortunately, these processes are rarely conveyed to their quoting departments. As a result, the die shop comes up with its own process, and the quote submitted reflect the process being used.
Ensuring Correct Part Processing
It’s important to remember that most die shops are not given enough time or money during the quoting process to prove that their process will work. To prove out the process, forming simulation might be necessary.
Die shops often pay $50, 000 to $70,000 a year for a single stimulation license. They can’t afford nor are they typically compensated for any work performed during the quoting stages of the tooling.
Before sending the part out for quotes, you might consider processing, stimulating, and developing the stages necessary to produce it. Some large companies use this method. It requires the company have on staff individuals with a great deal of metal forming, die processing, and building experience. Complex parts that are to be drawn and stretched most likely will require an investment in some type of incremental forming simulations software, as well the necessary software training.
Most product designers and metal stamping companies use single-step software for part feasibility studies, but that does not guarantee that a part can be made; it simply shows areas of a part that are major concerns. Incremental forming simulation, on the other hand, replicates the die forming process.
When using these methods, don’t automatically dismiss any different ideas that die shop might have, but keep in mind that your process has been established as a result of success, not speculation.
Processing Your Own Parts
It’s a big investment for a shop to process its own parts, but for those that have embraced it, the investment pays off. Consider the benefits:- Quotes are apples to apples because every die shop is quoting to the same process.If product changes are required for formability, they can be addressed and solved before the process goes out for quoting.
- If product changes are required for formality, they can be addressed and solved before the process goes out for quoting.
- No time is wasted waiting for part tolerance data at the die building shop.
- Because both product design an process design are often in the same building or department, the communication gap is reduced between them.
- The die will be less expensive because the part processing has already been performed.An effective process is assured. The key to success boils down to knowledge and communication. Although die shops are a great resource for part processing methods, the stamper also has a great deal to offer the die builder. If your stamping shop can’t justify buying incremental forming simulation software, consider outsourcing the simulation to a company that specializes in forming simulation.
Until next time… Best of luck!
About the Author
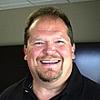
Art Hedrick
10855 Simpson Drive West Private
Greenville, MI 48838
616-894-6855
Related Companies
subscribe now
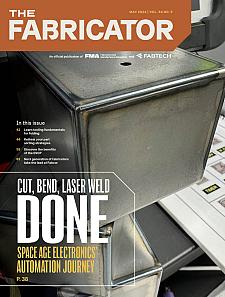
The Fabricator is North America's leading magazine for the metal forming and fabricating industry. The magazine delivers the news, technical articles, and case histories that enable fabricators to do their jobs more efficiently. The Fabricator has served the industry since 1970.
start your free subscription- Stay connected from anywhere
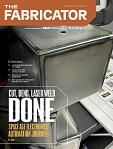
Easily access valuable industry resources now with full access to the digital edition of The Fabricator.
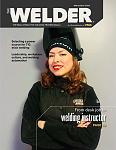
Easily access valuable industry resources now with full access to the digital edition of The Welder.
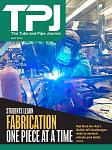
Easily access valuable industry resources now with full access to the digital edition of The Tube and Pipe Journal.
- Podcasting
- Podcast:
- The Fabricator Podcast
- Published:
- 04/16/2024
- Running Time:
- 63:29
In this episode of The Fabricator Podcast, Caleb Chamberlain, co-founder and CEO of OSH Cut, discusses his company’s...
- Trending Articles
Tips for creating sheet metal tubes with perforations
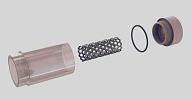
Supporting the metal fabricating industry through FMA
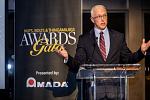
JM Steel triples capacity for solar energy projects at Pennsylvania facility
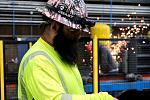
Fabricating favorite childhood memories
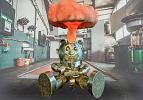
Omco Solar opens second Alabama manufacturing facility
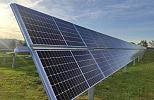
- Industry Events
16th Annual Safety Conference
- April 30 - May 1, 2024
- Elgin,
Pipe and Tube Conference
- May 21 - 22, 2024
- Omaha, NE
World-Class Roll Forming Workshop
- June 5 - 6, 2024
- Louisville, KY
Advanced Laser Application Workshop
- June 25 - 27, 2024
- Novi, MI