Contributing editor
- FMA
- The Fabricator
- FABTECH
- Canadian Metalworking
Categories
- Additive Manufacturing
- Aluminum Welding
- Arc Welding
- Assembly and Joining
- Automation and Robotics
- Bending and Forming
- Consumables
- Cutting and Weld Prep
- Electric Vehicles
- En Español
- Finishing
- Hydroforming
- Laser Cutting
- Laser Welding
- Machining
- Manufacturing Software
- Materials Handling
- Metals/Materials
- Oxyfuel Cutting
- Plasma Cutting
- Power Tools
- Punching and Other Holemaking
- Roll Forming
- Safety
- Sawing
- Shearing
- Shop Management
- Testing and Measuring
- Tube and Pipe Fabrication
- Tube and Pipe Production
- Waterjet Cutting
Industry Directory
Webcasts
Podcasts
FAB 40
Advertise
Subscribe
Account Login
Search
Servo press puts reverse tonnage in reverse
Stamping manufacturer takes two-tiered approach to form "wicked" stainless automotive part
- By Kate Bachman
- April 27, 2021
- Article
- Bending and Forming
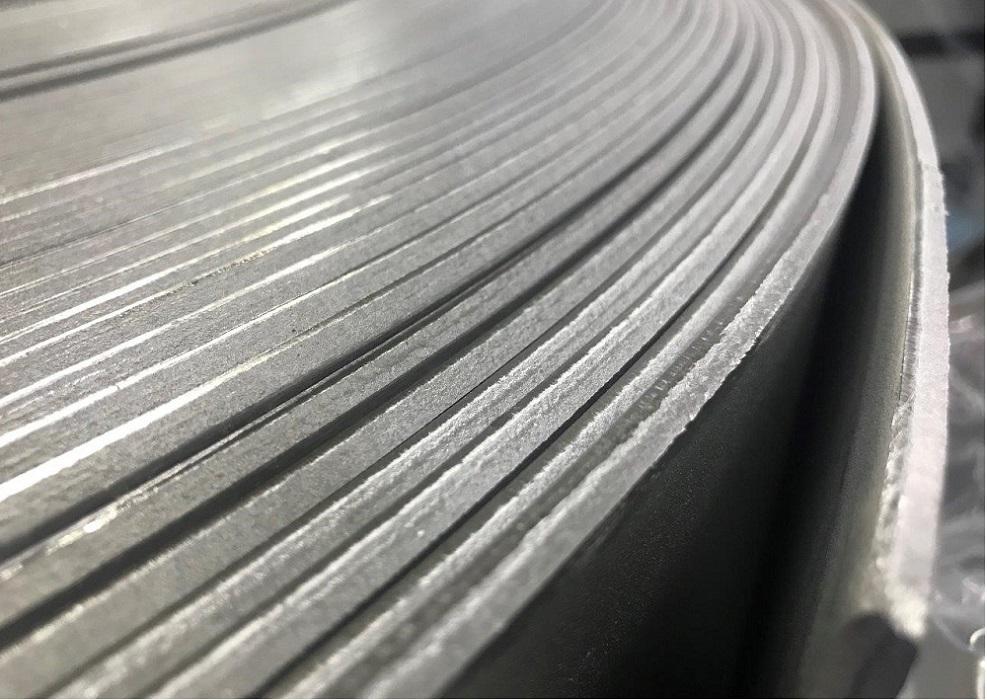
Clips & Clamps Industries stamps a part from a 5-mm stainless steel material. The material was exerting 100 tons of reverse tonnage on the company’s 300-ton mechanical press, which put severe stress on the press’s clutch and burned it out. After a run, pieces would land on the crown of the press and down on the floor, and toolholders installed on the press did not stay in. Items that were tapped and screwed in would completely back out. Images: Clips & Clamps Industries
When forming a stainless steel part on a 300-ton mechanical press, stamping manufacturer Clips & Clamps pushed the press to the apex of its capacity and worse—it encountered extreme reverse tonnage. The press, tooling, and entire system took a beating that even a robust hydraulic dampening system couldn’t completely quell.
The part is made of what company President Jeff Aznavorian calls “wicked” material—1/8-in.-thick, 78 Rockwell stainless steel. “It’s hard. It can be very brittle. We are buying probably the thickest version of this material in coil form in the country. It’s the only material we buy mill-direct because of the volume and its unique nature.” The thickness and hardness of the metal are necessary to achieve the part’s structural strength and integrity in a high-heat, high-stress assembly environment.
“When we designed the die for this product, we knew that it was going to push the top of our tonnage range,” said Aznavorian. The entire profile had to be completely blanked through in one stroke. “Because of what we needed on the edges of the material, we knew that this would take everything that our 300-ton mechanical press had. Sure enough, when we blanked the first pieces, the forward tonnage on it was at the top of the 290s.”
Even more problematic than pushing the press to the very height of its capacity was the reverse tonnage. It went to more than 100 tons on the 300-ton press. That’s a lot of kickback. “There’s a rule of thumb that you never want your reverse tonnage to be more than 10%.”
Aznavorian said that the company could not slow the press to less than 45 SPM to reduce breakthrough at bottom dead center because that speed was needed to get through the material. Otherwise the press could completely stall out.
“It was so loud, some of our operators wore muffs on top of earplugs when we were running that job in the mechanical press. The press was about as far away from my office as you can get—about three football fields away. Not only could I hear the job running from my office, I could also feel it. If I had a glass of water on my desk, you could see ripples in the water. It was like the scene from ‘Jurassic Park’ where a glass of water rippled when a T-rex got close.”
The reverse tonnage put severe stress on the mechanical press’s clutch because the stopping motion was so abrupt. “We completely burned out the clutch. I think we were down for four weeks. It was a $60,000 complete clutch rebuild.”
Aznavorian said he knew they had to do something to tame the beast.
“After a run, we’d find pieces up on the crown of the press, down on the floor ... Toolholders installed on the press did not stay in. Things that were tapped and screwed in would completely back out. It was a mess.”
Hydraulic Dampening System Subdues
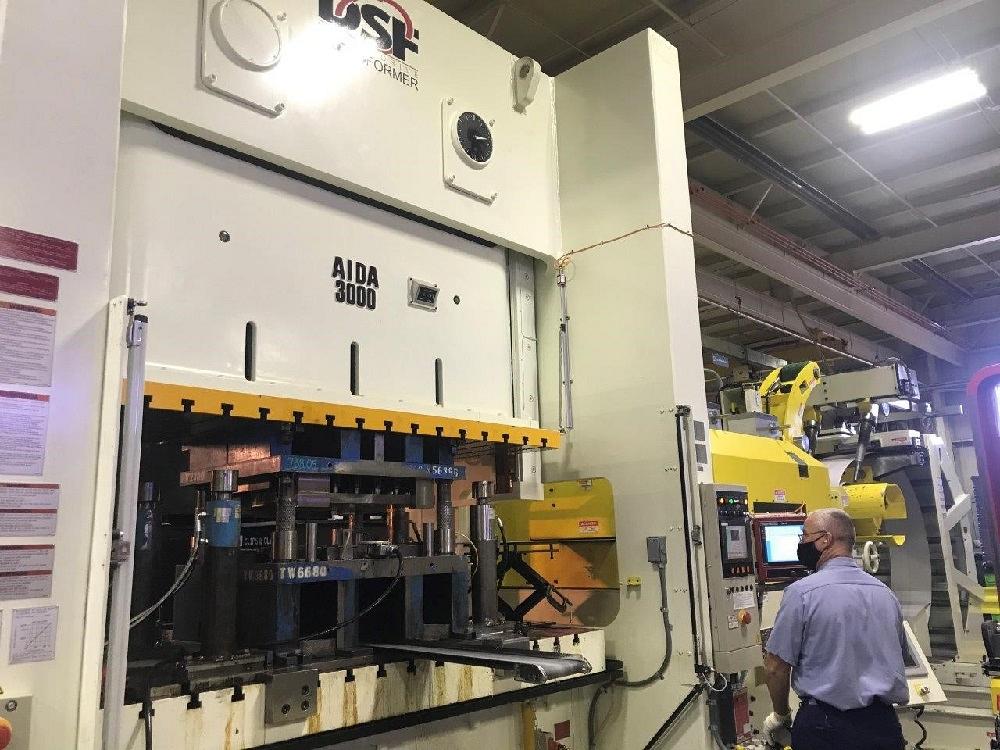
The stamper bought an AIDA DSF-N2-3000 330-ton, floor-standing servo press. The reverse tonnage dropped to 18 tons immediately. Tool life was extended as well.
The first step the company took was to install a robust, solidly built, four-post hydraulic dampening system. “It’s got a huge hydraulic reservoir that sits off to the side, and tubes run throughout. It looks like a mad scientist hookup because there are so many tubes coming off the die set.” The dampening system lowered the reverse tonnage into the 60- to 70-ton range, he said, which helped. “So we reduced it by about a third, maybe more. But even at that rate, it was still shaking everything like a bull in a china shop.
Trying to maintain supply while the press was limping was difficult, he said. Although the press could run, its stop time was so delayed, operating it was becoming unsafe. So the company built up a bank of parts while the press was on its last legs and still capable of running in a safe manner before taking it down for the clutch rebuild.
The tooling group worked with a local supplier to design and build several hydraulic dampening systems for the die sets. The program was in two parts—an A part and a B part. In addition, there were backup dies for both of them because of the size of the program. While one die set was being maintained, the other was running.
“This was not going to be the kind of job where we would get 500,000 hits out of a die and then go in and do regular maintenance,” Aznavorian said. “We’re getting about 75,000 hits out of them.”
Press Evaluation Points to Servo
The reverse tonnage stress on the press was the tipping point that drove the company to buy a new press that it had already resigned to buy. The company needed a new press to balance its existing capacity utilization in the 200-plus tonnage range because it was running out of capacity.
“Clips & Clamps has a long history of getting the best of the best when we invest in a new piece of equipment or new technology. And the press department was an area in which we hadn’t made a major investment in decades.”
Unfortunately, the cramped facility placed limitations on press size, Aznavorian said. “I was dead set on a 400-ton press with a 120-in. bed. We realized that even though we might be able to wedge that in here, we wouldn’t be able to handle or store the coils needed to run on that size press. The dies that would go into a 120-in. bed … we wouldn’t be able to pick them up.” In addition, the 400-ton would have required a pit. The infrastructure that would have been required for a larger press directed the company to a slightly smaller 330-ton press.
After determining the press size that could fit in the facility and vetting various presses and makes, Clips & Clamps bought an AIDA DSF-N2-3000 330-ton servo press. The press is a floor-standing model with a 96-in. bed size. The ram is offset, so it is smaller than the bed. It was delivered in the spring of 2020.
“We felt that this press system would help us achieve what we wanted to accomplish—being able to access the capabilities of servo technology in a press size that we could handle in this facility, plus expanding overall capacity,” Aznavorian said. Because it is a floor-standing model, the company did not have to install a pit.
The stamper installed a Coe Press Equipment SpaceMaster Series 4 line for the feed line. “That helps with the overall space and footprint,” Aznavorian said.
Servo Press Reverses Reverse Tonnage
The servo press successfully reversed the reverse load and the problems that accompanied it.
“Much to our delight, when we first went in there with this job on the new servo press, the reverse tonnage dropped to 18 tons immediately.” That amount of reverse shock generally is considered acceptable tolerances. “Our forward tonnage went down as well, at about 220.
“We definitely attribute that to the power the press has throughout the stroke. Plus, because the stroke is infinitely adjustable, we were able to slow that snap-through down quite a bit compared to what we had to do on the mechanical,” he said.
“The fact that servo maintains its tonnage through the stroke at snap-through is just incredible,” he added.
He said that the operation runs very smoothly and is much quieter now too. “It doesn’t shake the press to death. It doesn’t shake the whole plant. It still snaps, and there’s still quite a pop, but it’s not deafening.
"I can’t hear it in my office anymore, which is a good and a bad thing,” he said with a laugh. “Sometimes you kind of like to know, ‘Hey, it’s running!’”
Aznavorian said press speed has increased, too, because it is set to accelerate on the upstroke. “We are above 60 SPM on the servo. We are probably actually running 160 degrees total on the stroke in pendulum mode at 180 degrees.
Hydraulic Dampening Retained
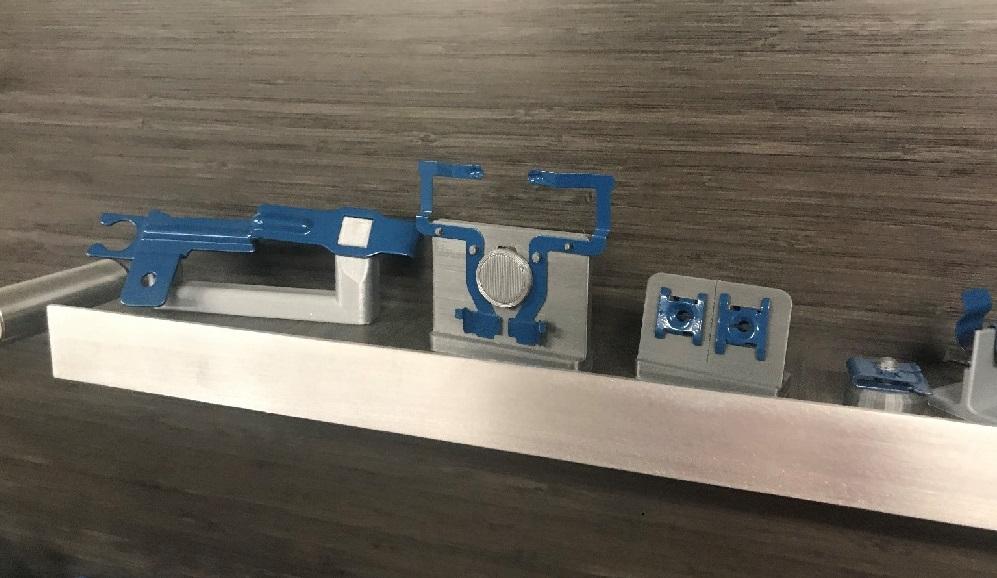
Often, the parts are made to be stress-tensioned because most parts’ functions are to hold or attach another part.
Even though the servo press mitigated most of the reverse tonnage, Aznavorian thought it best to retain and continue using the hydraulic dampening system.
“As much as we would have liked to abandon it, we knew that because of the thicknesses of the material we were blanking through, we needed that extra security blanket on there,” he said.
“So we’re below 220 now, and we’re extremely happy.”
No More Double Dies
Aznavorian said the company no longer needs a double set of dies. It had been running sister parts, two different parts, and two dies for each. “We can service between the sister parts now, so we don’t need the extra tools.”
He said the company keeps the extra tools as a backup, as risk mitigation, but they aren’t as critical as they were.
Die life seems to have improved. “We don’t have a lot of data because it’s only been in operation for a few months.” Right after the press was installed, the company shut down because of the pandemic. “I do know that we’re not snapping punches like we used to. We’re getting more overall strokes between sharpenings. We know it’s going in the right direction.”
Part Appearance Improved
Part appearance and functionality have improved also. “Even though we were shipping 100% quality parts off the mechanical press, and within tolerance, the visual was not always perfect on the nonappearance part,” Aznavorian said.
For example, the stresses on the breakthrough would warp some of the punched holes, and they would look slightly oblong.
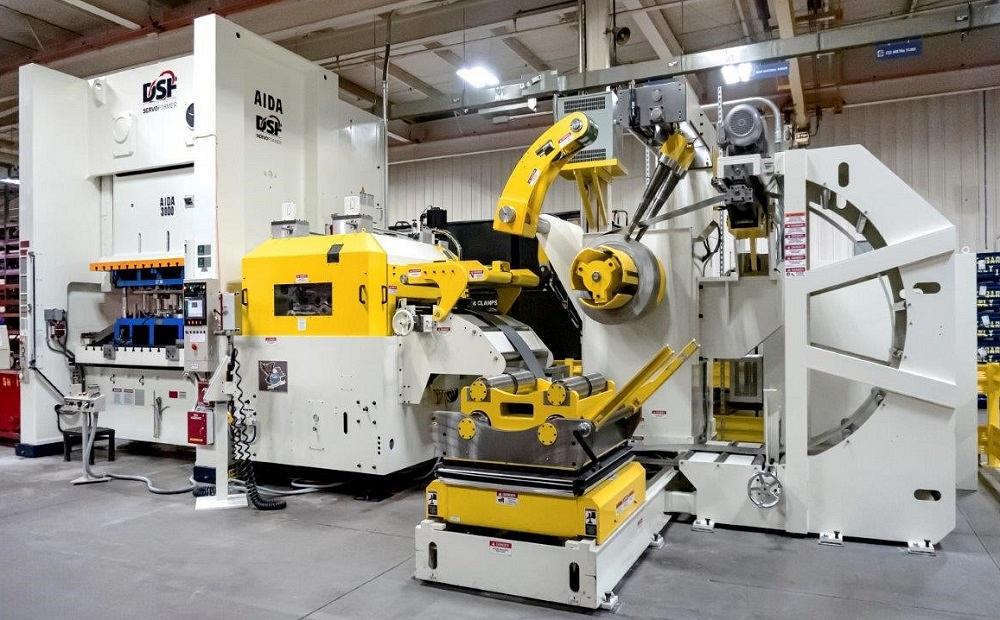
The stamper installed a Coe Press Equipment SpaceMaster Series 4 feed line, which fits into the limited footprint available.
“But now we’ve gotten the total profile tolerance much closer to nominal. The edges are a lot cleaner. We’re not getting the break we used to have. Overall, the holes are rounder than they used to be.
“It’s not an appearance part, and those things don’t make it function any better, but it looks better.”
Equipped for Future Projects
Aznavorian said that using the servo press has been a learning experience. Because the press can slow at bottom dead center, the company can hold flatness, profile tolerances, and draw specs better. Equipped with the servo press, he feels confident that the company can tackle jobs needing machining-quality tolerances on profiles and flatness.
“One of the things we’ve been seeing more of lately is customers trying to take parts that are labor-intensive machinings and turn them into less labor-intensive stampings. If we can stamp those out at 50 to 70 SPM, that’s a lot faster and economical than machining them.” Machined parts tend to have really tight tolerances in terms of things like profile and flatness. “Now we know that if we have a part similar to this, we can quote it.
“We’re not a deep-draw company by any means, but we’re excited that we’ll be able to do a lot more with draws in our parts than we could before because of what we can do with the speed and maintaining the tonnage all the way through,” he added.
Aznavorian’s entrepreneurial spirit has its origins in Clips & Clamps’ founder’s innovative spirit. Estelle C. Dul was an entrepreneur who, after working in manufacturing since the age of 17, founded several companies. “This wasn’t my grandmother’s first manufacturing company, but it was the one that ended up sticking,” Aznavorian said.
About the Author
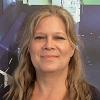
Kate Bachman
815-381-1302
Kate Bachman is a contributing editor for The FABRICATOR editor. Bachman has more than 20 years of experience as a writer and editor in the manufacturing and other industries.
Related Companies
subscribe now
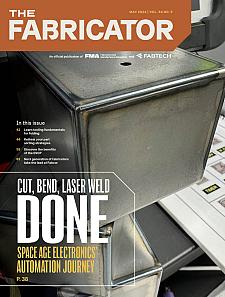
The Fabricator is North America's leading magazine for the metal forming and fabricating industry. The magazine delivers the news, technical articles, and case histories that enable fabricators to do their jobs more efficiently. The Fabricator has served the industry since 1970.
start your free subscription- Stay connected from anywhere
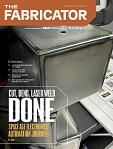
Easily access valuable industry resources now with full access to the digital edition of The Fabricator.
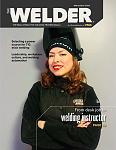
Easily access valuable industry resources now with full access to the digital edition of The Welder.
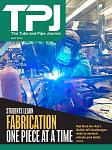
Easily access valuable industry resources now with full access to the digital edition of The Tube and Pipe Journal.
- Podcasting
- Podcast:
- The Fabricator Podcast
- Published:
- 04/16/2024
- Running Time:
- 63:29
In this episode of The Fabricator Podcast, Caleb Chamberlain, co-founder and CEO of OSH Cut, discusses his company’s...
- Trending Articles
Tips for creating sheet metal tubes with perforations
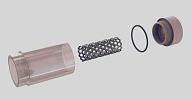
Supporting the metal fabricating industry through FMA
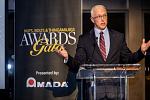
JM Steel triples capacity for solar energy projects at Pennsylvania facility
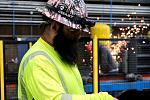
Fabricating favorite childhood memories
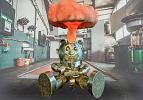
Omco Solar opens second Alabama manufacturing facility
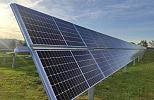
- Industry Events
16th Annual Safety Conference
- April 30 - May 1, 2024
- Elgin,
Pipe and Tube Conference
- May 21 - 22, 2024
- Omaha, NE
World-Class Roll Forming Workshop
- June 5 - 6, 2024
- Louisville, KY
Advanced Laser Application Workshop
- June 25 - 27, 2024
- Novi, MI