- FMA
- The Fabricator
- FABTECH
- Canadian Metalworking
Categories
- Additive Manufacturing
- Aluminum Welding
- Arc Welding
- Assembly and Joining
- Automation and Robotics
- Bending and Forming
- Consumables
- Cutting and Weld Prep
- Electric Vehicles
- En Español
- Finishing
- Hydroforming
- Laser Cutting
- Laser Welding
- Machining
- Manufacturing Software
- Materials Handling
- Metals/Materials
- Oxyfuel Cutting
- Plasma Cutting
- Power Tools
- Punching and Other Holemaking
- Roll Forming
- Safety
- Sawing
- Shearing
- Shop Management
- Testing and Measuring
- Tube and Pipe Fabrication
- Tube and Pipe Production
- Waterjet Cutting
Industry Directory
Webcasts
Podcasts
FAB 40
Advertise
Subscribe
Account Login
Search
Stamper uses servo press to final-form spline
Step/vibration mode lets metal flow, form without distortion
- May 22, 2019
- Article
- Bending and Forming
A stamping manufacturer to the automotive industry used its Komatsu servo press for a unique application—final forming a machined shaft into a high-end splined component on the press instead of machining it.
The manufacturer used the servo press’s step/vibration mode to perform the intricate forming. Starting only 3 inches off the bottom of the stroke, the ram goes up and down multiple times in one stroke, applying full, consistent energy. The downward motions form the shape, and the upward motions allow the metal to reflow.
Because the ram does not push down on the metal in one aggressive stroke, the metal is allowed to flow in a path of least resistance—even upward on the upstroke. As a result, the splined shaft final-formed on a servo press is actually slightly taller than the original machined blank.
This final forming could not be performed on a standard mechanical press without “mushrooming” the part.
Using the servo press, the supplier was able to achieve the same tolerances as machining. The press is equipped with a linear scale that holds accuracy level in microns.
A splined shaft is engineered to last longer than a shaft with a simple key that is inserted into a similarly sized, machined keyway. A spline has multiple contact connections rather than just one as does a key. By using its servo press, the manufacturer was able to supply a superior part to its customer without secondary operations.
Using the press expedited throughput because stamping the final details of the shaft into a spline in the servo press was faster than machining them.
Komatsu America Industries LLC,
Komatsupress.com
Related Companies
subscribe now
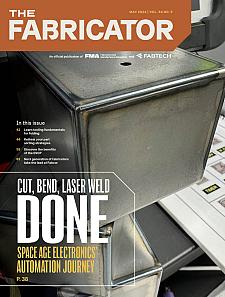
The Fabricator is North America's leading magazine for the metal forming and fabricating industry. The magazine delivers the news, technical articles, and case histories that enable fabricators to do their jobs more efficiently. The Fabricator has served the industry since 1970.
start your free subscription- Stay connected from anywhere
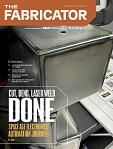
Easily access valuable industry resources now with full access to the digital edition of The Fabricator.
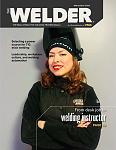
Easily access valuable industry resources now with full access to the digital edition of The Welder.
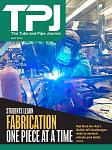
Easily access valuable industry resources now with full access to the digital edition of The Tube and Pipe Journal.
- Podcasting
- Podcast:
- The Fabricator Podcast
- Published:
- 04/16/2024
- Running Time:
- 63:29
In this episode of The Fabricator Podcast, Caleb Chamberlain, co-founder and CEO of OSH Cut, discusses his company’s...
- Trending Articles
Tips for creating sheet metal tubes with perforations
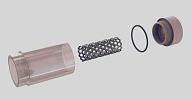
Are two heads better than one in fiber laser cutting?
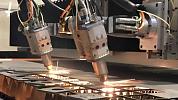
Supporting the metal fabricating industry through FMA
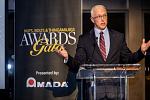
JM Steel triples capacity for solar energy projects at Pennsylvania facility
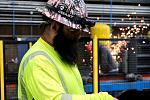
Omco Solar opens second Alabama manufacturing facility
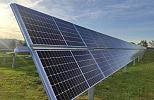
- Industry Events
16th Annual Safety Conference
- April 30 - May 1, 2024
- Elgin,
Pipe and Tube Conference
- May 21 - 22, 2024
- Omaha, NE
World-Class Roll Forming Workshop
- June 5 - 6, 2024
- Louisville, KY
Advanced Laser Application Workshop
- June 25 - 27, 2024
- Novi, MI