Contributing editor
- FMA
- The Fabricator
- FABTECH
- Canadian Metalworking
Categories
- Additive Manufacturing
- Aluminum Welding
- Arc Welding
- Assembly and Joining
- Automation and Robotics
- Bending and Forming
- Consumables
- Cutting and Weld Prep
- Electric Vehicles
- En Español
- Finishing
- Hydroforming
- Laser Cutting
- Laser Welding
- Machining
- Manufacturing Software
- Materials Handling
- Metals/Materials
- Oxyfuel Cutting
- Plasma Cutting
- Power Tools
- Punching and Other Holemaking
- Roll Forming
- Safety
- Sawing
- Shearing
- Shop Management
- Testing and Measuring
- Tube and Pipe Fabrication
- Tube and Pipe Production
- Waterjet Cutting
Industry Directory
Webcasts
Podcasts
FAB 40
Advertise
Subscribe
Account Login
Search
The STAMPING Journal story
100 percent devoted to stamping for 30 solid years
- By Kate Bachman
- December 27, 2018
- Article
- Bending and Forming
As of this November/December issue, STAMPING Journal® will have been in publication for 30 years. Why and how was it launched? For that answer, I consulted STAMPING Journal’s first editor, Kathy Velasco.
“We had started running inserts in The FABRICATOR® that were specific to certain technologies, because there were heavy demographics in stamping, as well as welding and tube and pipe. Stamping was our first insert,” Velasco recalled.
The stamping insert was starting to gain traction, she said. The U.S. Post Office limited the number of pages that could qualify the piece as an insert. “We were really pushing that page count. After it grew to over 28 pages, we decided to take a leap and produce a stand-alone magazine.
“Once we decided to do it, man, we did it fast. Within six months we had a magazine,” she said. “It was exciting. It was also stressful because the time frame was pretty tight and we were publishing The FABRICATOR on top of that. Once we committed to it, we couldn’t screw it up. So we worked a lot of extra hours,” she said.
Velasco recalled going to the first photo shoot for the cover image at a stamping plant in Chicago. “We spent a lot of time trying to get a really beautiful four-color photo of a stamping press with special spotlights and gels to get pinks and purples.” She said that the cover shots were always a big challenge in the early days. Once photography technology changed, it became a lot easier to get good photos.
Costly Mistake
Post office requirements created some growing pains for Velasco and for FMA, she recalled. “When I was researching the post office requirements for a full magazine, I didn’t do a good job of reading all the fine print. Back then there were seven versions of the language to put under the indicia to tell the post office how to send back undelivered issues.” Velasco said she had inadvertently chosen the wrong language, because rather than just getting a notice to pick up the undelivered issues from the post office, all of the publications were returned to FMA—at a cost of $3 per issue. “So I cost the company something like $10,000. John [Nandzik, the FMA president at that time] was quite charitable to me about it. That was a really big mistake that cost a lot of money—and one I never made again.”
Renamed
Originally the publication was called Stamping Quarterly, publishing four times a year. When it grew in frequency to six times a year, Velasco said there was some discussion about renaming the publication to avoid confusion. “We were talking about calling it SQ like GQ did when it increased from a quarterly, but we settled on STAMPING Journal.
Printing Technology Then
The printing technology in the early years required a great deal of time and manual composition. On the early issues, Velasco and the production staff had to take the photos to a processing shop for color separations into four different negatives. Before laser scanning technology came out, the processor had to do it using photographic means. “It was very extensive.”
Transporting the composed publication to a printer was an ordeal. Early on it had to be shipped to RR Donnelley printers in St. Louis. “Everything was a hard copy, so we had to box everything up and take it to a shipping company, which drove it to O’Hare Airport and put it on a plane to St. Louis. At a later point, we were able to take it to the Rockford [Ill.] airport and put it on a freight plane. I remember jumping in my car and driving just as fast as I could to make it in time,” Velasco said. Later, the printing was transferred to Quebecor Inc.’s Minneapolis plant. Subsequent companies have printed the magazine since.
Coverage
What did STAMPING Journal cover in its first issue? Press technology. Tool and die. Materials. Lubricants. Material handling. As the expression goes, the more things change, the more they stay the same. The industry still is encountering problems and challenges, and STAMPING Journal is still seeking answers to those problems from industry experts and successful stamping manufacturers willing to share their solutions. Our coverage over the years has included new technologies such as servo presses, cushions, and feeders; softwares; controls, material handling; materials; and methods to form them.
Enter Columnists
As it became clear that certain topics required regular coverage, SJ retained industry experts to pen columns. They included Tim Stephens, Art Hedrick, Dr. Taylan Altan, Bernard Swiecki, Dennis Cattell, and Tom Vacca. We are truly fortunate that Hedrick, Altan, and Vacca are still with us today.
Art Hedrick. Art Hedrick began writing his column in 1989—nearly two decades ago. He started by writing a couple of articles. They were so popular, he was asked to pen a regular column. Topics originate from his real-world experiences as a tool and die consultant.
Hedrick’s in-the-field expertise provides valuable problem-solving content. His columns appear on the walls of stamping and tool and die plants the world over, because they are so true to life. “When I go into stamping facilities, more often than you can imagine I see my articles on bulletin boards. One of the real popular ones is ‘How to destroy a press in 10 easy steps.’ Somebody will say ‘Man, were you at our company? Because that’s exactly what we do here.’”
And the “problems well” never seems to run dry.
In STAMPING Journal’s surveys and feedback from readers, one theme resounds more frequently than any other. “Art writes about complex problems in a way that I can really understand them,” readers say in one form or another. That communication approach is no accident.
“Of all the things that I value and believe are the most important, communication is by far the most critical,” Hedrick relayed. “I believe with all of my heart that the ability to communicate effectively is the most critical asset anybody can have; not just the ability to clarify what you’re trying to say, but the ability to make other people feel important. … to make them feel like they’re part of the process, part of the solution, not the problem; to inspire them; to make them smile, to make them laugh.”
As experienced and knowledgeable as Hedrick is, he demonstrates in his writing that he has never forgotten what it’s like to be a newbie apprentice and he isn’t afraid to simplify his sentence construction or define a term. “I find myself reverting back to the day when I was a brand-new apprentice and try to treat other apprentices and people in the industry with respect. Everybody else might think you should know what a dowel rod is, but there was a day when I didn’t know what a dowel rod was, so I’m going to teach you what it is. And I’m going to do so respectfully,” Hedrick said.
R-e-s-p-e-c-t. That is the impetus for why Hedrick named his column Die Science. “My big hairy audacious goal my whole career has been to try to change the perception of the tool and die industry from a ‘factory job’ to a ‘professional career path’—and if I had my druthers, ‘a science.’ That’s why I coined the phrase ‘dieologist.’ Good tool- and diemaking and maintenance are about making good, data-based decisions based on physics,” Hedrick said.
Hedrick said he enjoys writing his column for STAMPING Journal. “I wanted to be recognized as a toolmaker, not because I’m not humble, not because I think I’m better than anyone else, but because I want to elevate the perception of a toolmaker. Every time I tell anybody about my job and they ask what factory I work in, I get really frustrated. And I thought, hey, if I can tell people I write for the magazine, they might realize that there’s more to this tool and die business than they think.”
Dr. Taylan Altan. Distinguished, well-respected Dr. Altan has been sharing the results of his and his students’ research at the Center for Precision Forming (CPF) in our pages since 1998 in R&D Update, forming the scientific cornerstone of our journal.
The first article was entitled “Process simulation for can manufacturing by deep drawing and ironing” and discussed how finite element modeling could be helpful in process simulation.
“The main purpose of CPF’s contributions to STAMPING Journal is to inform the practicing stamping engineer, in relatively simple terms, about the latest advances and possible improvements in stamping technology. As much as possible, the CPF team has tried to explain the results of ongoing stamping and sheet forming research in an easily understandable format,” Altan said.
Because weight reduction and the use of aluminum in the automotive industry were of primary importance starting in the late 1990s, R&D Update columns covered the forming of aluminum and magnesium alloys, Altan relayed.
Over the years the R&D effort in the stamping industry was driven by the continued need for weight savings. Thus, the technology evolved into cold forming of advanced high-strength steels (AHSS) with tensile strength above 600 megapascals (MPa) to 1,200 MPa. Parallel to this effort, hot stamping of boron steels that could be processed (heated and die quenched) to reach tensile strengths of 1,600 MPa was also developed. These processes are now state of the art, as are cold and warm forming of aluminum alloys that exhibit increased use for weight savings, Altan said.
The R&D Update columns focused on technologies and tests that enable and support advanced stamping operations. These included the determination of material properties using uniaxial tensile tests and biaxial bulge tests; evaluation of lubricants; use of new presses and tooling (mechanical and hydraulic servo presses, single and multiple servo hydraulic cushions, blank holder force control); hot stamping of boron steels and hot and warm forming of aluminum alloys; blanking, trimming, and prediction of edge fracture in flanging in forming high-strength steels (HSS); and advanced methods for cost-effective prediction and reduction of springback in forming HSS.
“While R&D in these areas may lead to rather complex test procedures and computer simulations, we strive to summarize the results in a form that is relatively easy to understand and apply,” Altan said.
Tom Vacca. I recall when Ask the Expert columnist Tom Vacca joined STAMPING Journal. Vacca is an enthusiastic tool- and diemaker turned engineer turned working toolroom manager with a huge passion for toolmaking and stamping. At first, he and industry veteran Dennis Cattell fielded the questions together, and then Vacca took over the entire column when Cattell retired. Ask the Expert has become one of the most popular components of our publication.
Vacca also has had his columns posted in shops around the country, particularly “The 10 laws of die design,” which we have published twice. Who can argue with the No. 1 rule, “Have no other goal except perfection” and “If nothing changes, nothing will change”?
Over the Years
As the stamping industry goes, so goes STAMPING Journal. It has burst with content in the robust years, and thinned but survived the lean years. I remember a couple of editions in 2008 and 2009 when we had only three ads. Considering that advertising revenue is the lifeblood of most publications, providing the means to publish, those were scary times indeed.
Cost-effective Distribution. One of the ways we managed both to be cost-effective with postage (postage again!) and to resolve the need to meet some stampers’ demands for coverage of metal fabrication was by co-mailing STAMPING Journal with The FABRICATOR. After all, The FABRICATOR is already the best source of metal fabrication coverage out there. We have been able to provide that broader coverage without reinventing the wheel.
Seeking Stamping Solutions. Another way we worked to stay afloat has been by actively seeking out survival approaches with our coverage for our stamping, engineering, and toolmaking readers—picking up a few awards and accolades along the way. ASBPE-award-winning articles “Winning work from the New Domestics”; “How 2016 Car of the Year Honda Civic maneuvered around AHSS obstructions”; “Silicon Valley stamper sizes up, down electronics”; and “Presses help form new future, fortune for tool- and diemaker” were all intended to help readers find new pathways to success.
Alliances in FABTECH®. As a publication of the Fabricators & Manufacturers Association (FMA), STAMPING Journal has always covered FABTECH and the technologies showcased there. In 2008, when Metalform merged with FABTECH, our tradeshow coverage became that much more complete.
The Staff. As for STAMPING Journal’s staff who have built the publication and brand together, after the initial issues, Kathy Velasco reverted to heading up The FABRICATOR and passed the role over to other editors. Since, editors Theresa Houck, Eddy McNeil, Kathleen McLaughin, and Dan Davis have filled that seat.
I served as STAMPING Journal editor twice—from 2008 to 2012, leaving to launch another magazine for a few years, then returning in 2014. You can take the girl out of stamping, but you can’t take the stamping out of the girl.
Contributing Editor Amy Nickel, aka, Amy Boeselager, has fortified STAMPING Journal for many years by editing and proofing press releases, columns, and articles. Senior Copy Editor Teresa Chartos has improved its content and rescued it from grammatical, spelling, and other errors too often to count. Suffice it to say that headlines like “Missippi’s literacy program shows improvement”; “Band member on drugs [instead of on drums]”; or “Think of a headline 56-pt. bold headline” will never happen in our pages as long as she has a red pencil and an opportunity to review them. Graphic artist Margaret Clark has been making STAMPING Journal look good—and readable—for nearly 20 years now. Sherry Young preceded her in shaping SJ’s appearance, and Deb Strout before her. Former Executive Editor Theresa Houck and current Editor-in-Chief Dan Davis have influenced SJ with their thorough supervision over the publication as well.
Today’s Publishing Technologies
It’s no secret that publishing technologies have undergone a revolution. STAMPING Journal is now published in both digital and print media. Its articles are posted on the very highly rated fabricator.com website. We post on social media. We include video captures of interviews. My research has been expedited and benefited by being able to access more information, faster on the internet. Gone are the days of scanning photos and rushing hard copies of the magazine layout to the printer; electronic files are sent via cyberspace instead.
Memorable Moments
For me, as one of the editors shepherding STAMPING Journal, one coverage standout included the nine-part mega-article that culminated as a result of my researching the stamping industry when I first took over the editorship: “Press selection—sorting it out” was my own baptism by fire.
My favorite articles, though, are those that I wrote about stamping manufacturers I’ve had the honor of interviewing. I’ve been humbled as they relayed their most pivotal moments, growth, strength, successes, and nonsuccesses. I’ve even made a few friends and fans.
The very best aspect of editing this magazine is receiving correspondence, feedback, and questions from readers. No compliment means more to me than for a reader to say, “Thanks. I really learned something valuable here that helped me.”
Future
As for the future of STAMPING Journal, we’ll continue to follow new technologies and seek resolutions to stamping, materials, and die challenges—and to be 100 percent devoted to stamping.
About the Author
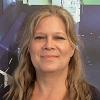
Kate Bachman
815-381-1302
Kate Bachman is a contributing editor for The FABRICATOR editor. Bachman has more than 20 years of experience as a writer and editor in the manufacturing and other industries.
subscribe now
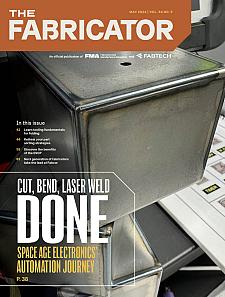
The Fabricator is North America's leading magazine for the metal forming and fabricating industry. The magazine delivers the news, technical articles, and case histories that enable fabricators to do their jobs more efficiently. The Fabricator has served the industry since 1970.
start your free subscription- Stay connected from anywhere
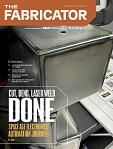
Easily access valuable industry resources now with full access to the digital edition of The Fabricator.
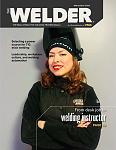
Easily access valuable industry resources now with full access to the digital edition of The Welder.
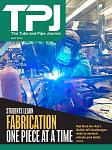
Easily access valuable industry resources now with full access to the digital edition of The Tube and Pipe Journal.
- Podcasting
- Podcast:
- The Fabricator Podcast
- Published:
- 04/30/2024
- Running Time:
- 53:00
Seth Feldman of Iowa-based Wertzbaugher Services joins The Fabricator Podcast to offer his take as a Gen Zer...
- Industry Events
16th Annual Safety Conference
- April 30 - May 1, 2024
- Elgin,
Pipe and Tube Conference
- May 21 - 22, 2024
- Omaha, NE
World-Class Roll Forming Workshop
- June 5 - 6, 2024
- Louisville, KY
Advanced Laser Application Workshop
- June 25 - 27, 2024
- Novi, MI