Senior Editor
- FMA
- The Fabricator
- FABTECH
- Canadian Metalworking
Categories
- Additive Manufacturing
- Aluminum Welding
- Arc Welding
- Assembly and Joining
- Automation and Robotics
- Bending and Forming
- Consumables
- Cutting and Weld Prep
- Electric Vehicles
- En Español
- Finishing
- Hydroforming
- Laser Cutting
- Laser Welding
- Machining
- Manufacturing Software
- Materials Handling
- Metals/Materials
- Oxyfuel Cutting
- Plasma Cutting
- Power Tools
- Punching and Other Holemaking
- Roll Forming
- Safety
- Sawing
- Shearing
- Shop Management
- Testing and Measuring
- Tube and Pipe Fabrication
- Tube and Pipe Production
- Waterjet Cutting
Industry Directory
Webcasts
Podcasts
FAB 40
Advertise
Subscribe
Account Login
Search
Avoiding ERP headaches for the custom metal fabricator
How Fulcrum tailors software for job shops to improve integration, interoperability, and planning
- By Tim Heston
- November 20, 2023
- Article
- Manufacturing Software
For years, Sunny Han worked as a consultant helping small and medium-sized manufacturers implement ERP platforms or tie disparate platforms together. It wasn’t easy. Plenty of custom metal fabricators have their own ERP horror stories, and Han experienced more than a few of them.
So, in 2015, he quit his job and, with a team of like-minded engineers, started a consulting firm called Atlas Solutions, which built custom software for a variety of companies, including manufacturers. This often involved building and integrating features like scheduling and time-tracking tools that a manufacturer’s legacy software often lacked.
That experience led him toward developing a new system in 2019. Called Fulcrum, the platform has evolved over the past few years into something that, according to Han, is designed to eliminate some well-known headaches in the manufacturing software arena.
Fixed-Fee Implementation
The first headache comes with getting the system set up in the first place. Implementation often takes time simply because of what Han called the different “archeological layers” of data in a typical manufacturer.
“In the 1980s, engineers were just building whatever they could to make the software work. There was no thought in making things work together.”
Fulcrum charges a fixed, one-time fee for implementation. What makes this possible from a business perspective, Han said, are the tools that company engineers have developed to automate certain tedious, time-consuming aspects of the process, including data uploading and cleanup.
“Using our data uploader, one of our customers did it all themselves,” Han said. “They uploaded the data; we told them where it needed to be cleaned up; they cleaned it up and re-uploaded it. That happened within a week.”
Han emphasized that implementation time still depends on the complexity of the business and the quality of the data. In general, Han said, implementation isn’t instantaneous, but the company does tout a streamlined process that takes weeks instead of months.
Two Sides, One Coin
Fulcrum’s platform really can’t be described as having distinct building blocks—purchasing, scheduling, job tracking—stitched together to form a complete system. Instead, Han described the platform as a bonsai tree. Customization happens by trimming the tree to the shape a manufacturer’s needs—but at its core, it’s still a bonsai tree, one entity.
The reason for this, he said, has to do with how different elements within the platform work together. The relationship between scheduling and purchasing is a prime example. As Han explained, “Purchasing and scheduling are two sides of the same coin. You purchase based on what you schedule, and you’ve got to schedule based on what’s in inventory. That process is often done by a team of three or more people. With us, it’s assessed by one mathematical engine.”
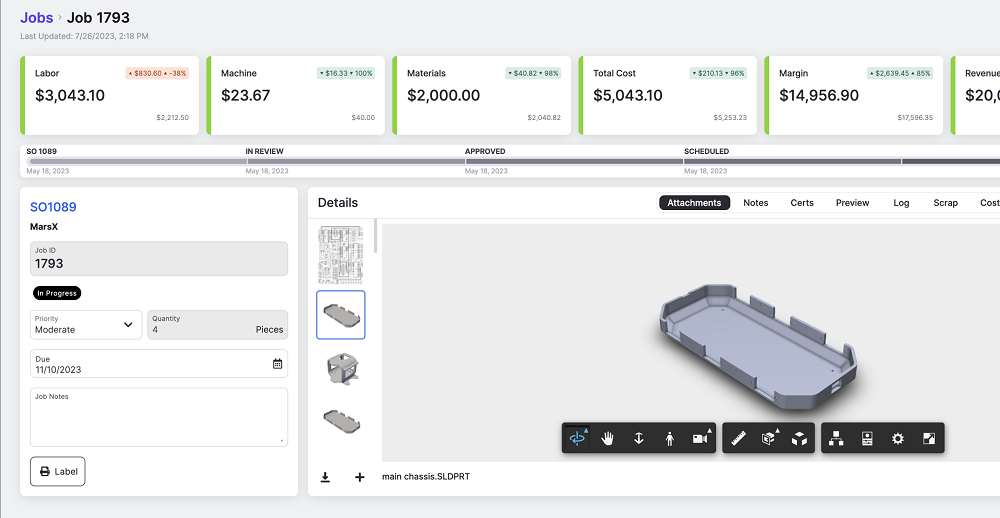
Fulcrum was developed in 2019, and has evolved over the past few years into a platform designed to eliminate some well-known headaches in the manufacturing software arena. Fulcrum
Consider the goals of purchasing. “You need to make sure you have as little material as possible on hand to support as much production flexibility and throughput as possible,” Han said. “I want to buy as few things as I can to do as many different scheduling combinations that I possibly can.”
To make purchasing truly effective and efficient requires an intimate tie-in with scheduling. A change in the production schedule means a change in purchasing and vice versa. Purchasing lead times for specific vendors are used to anticipate when material will be available for a job to start. The scheduler, understanding when material will be available, schedules the job to start after the material’s expected arrival date in receiving.
The schedule also adjusts based on real-time data coming from the shop floor. Using an app, operators clock into an operation and track setup, labor, and machine time. Meanwhile, progress data flows back to the scheduler. (Outside of the scheduler, the platform uses this information to calculate job costing data.) Drawing from all this, the automatic scheduler works in concert with other modules of the software.
“The system is designed to make the most efficient schedule possible with the goal of getting the most work out the door on time while reducing WIP,” Han said, adding that the system balances variables like priority levels, due dates, capacity constraints, and material availability. The scheduler, relying on the computing power of the cloud, uses statistical models and mathematical weighting.
Han described one instance where, due to space limitations, a job shop needed to reduce work in process (WIP) significantly—a common challenge for job shops with a wide mix of jobs and numerous potential job routings. It was still possible to optimize a production schedule to reduce WIP while still getting as much work out the door on time as possible. “The scheduler does this by first understanding the shop’s capacity constraints, including shifts and machine capacity, and then creates the optimal schedule that will fit within those constraints automatically.”
EDITORIAL INSIGHT: THE STATE OF SOFTWARE
Software in precision metal fabrication seems to be at a transition point. For years, the industry has invested in an alphabet soup of options. Materials resource planning (MRP) evolved into enterprise resource planning (ERP). Then came manufacturing execution systems (MESs) and customer relationship management (CRM).
You have nesting CAM nesting software, production control software that connects machines on the floor with business systems in the office. Then came the Industrial Internet of Things (IIoT) and its associated platforms that track equipment performance and throughput. You’ve got quoting platforms and scheduling software.
The choices seem endless, which for fabricators can be a good thing—unless they end up building a Tower of Babel, a collection of disparate software that can’t communicate. Operators enter data once, then people in the office end up exporting that data into a CSV file and manually pasting together a production report.
That’s what some at Metalworks Inc. ended up doing, and a few young engineers aimed to change that, launching a custom software company called Cortex Data Services.
Sunny Han of Fulcrum emphasized that interoperability between different platforms is part of his software company’s core strategy. “We want to be the connective tissue,” he said.
Wayne Byrne of the low-code platform Tangle said he wants his technology to be the “glue” that can help disparate software platforms work in a cohesive way.
Some platforms (including Fulcrum) are avoiding the use of “ERP” and other legacy initialisms altogether. The lines are blurring, and people are realizing that what software can do is more important than what it’s called. The easier software becomes to implement and integrate, the better off the metal fabrication industry will be.
A Connected Ecosystem
Another problem in manufacturing software overall is the ability for different software platforms to work together. “We want to be the connective tissue,” Han said. “There are other platforms that have expertise in accounting and other processes. We integrate with those systems instead of creating our own and splitting our focus from what is most important.”
The idea is that the better software platforms can interact, the better all those software platforms can help manufacturers. As Han put it, “Our vision is to create a connected manufacturing ecosystem.”
About the Author
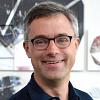
Tim Heston
2135 Point Blvd
Elgin, IL 60123
815-381-1314
Tim Heston, The Fabricator's senior editor, has covered the metal fabrication industry since 1998, starting his career at the American Welding Society's Welding Journal. Since then he has covered the full range of metal fabrication processes, from stamping, bending, and cutting to grinding and polishing. He joined The Fabricator's staff in October 2007.
subscribe now
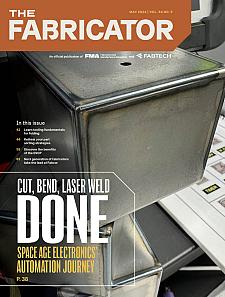
The Fabricator is North America's leading magazine for the metal forming and fabricating industry. The magazine delivers the news, technical articles, and case histories that enable fabricators to do their jobs more efficiently. The Fabricator has served the industry since 1970.
start your free subscription- Stay connected from anywhere
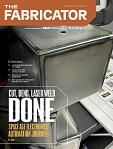
Easily access valuable industry resources now with full access to the digital edition of The Fabricator.
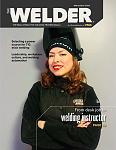
Easily access valuable industry resources now with full access to the digital edition of The Welder.
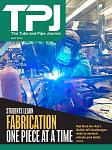
Easily access valuable industry resources now with full access to the digital edition of The Tube and Pipe Journal.
- Podcasting
- Podcast:
- The Fabricator Podcast
- Published:
- 04/16/2024
- Running Time:
- 63:29
In this episode of The Fabricator Podcast, Caleb Chamberlain, co-founder and CEO of OSH Cut, discusses his company’s...
- Trending Articles
Tips for creating sheet metal tubes with perforations
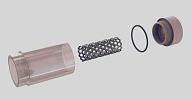
JM Steel triples capacity for solar energy projects at Pennsylvania facility
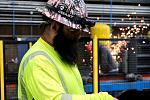
Are two heads better than one in fiber laser cutting?
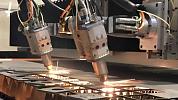
Supporting the metal fabricating industry through FMA
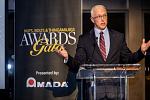
Omco Solar opens second Alabama manufacturing facility
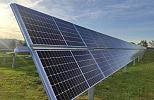
- Industry Events
16th Annual Safety Conference
- April 30 - May 1, 2024
- Elgin,
Pipe and Tube Conference
- May 21 - 22, 2024
- Omaha, NE
World-Class Roll Forming Workshop
- June 5 - 6, 2024
- Louisville, KY
Advanced Laser Application Workshop
- June 25 - 27, 2024
- Novi, MI