Vice President and Head of Product Management for Application Group
- FMA
- The Fabricator
- FABTECH
- Canadian Metalworking
Categories
- Additive Manufacturing
- Aluminum Welding
- Arc Welding
- Assembly and Joining
- Automation and Robotics
- Bending and Forming
- Consumables
- Cutting and Weld Prep
- Electric Vehicles
- En Español
- Finishing
- Hydroforming
- Laser Cutting
- Laser Welding
- Machining
- Manufacturing Software
- Materials Handling
- Metals/Materials
- Oxyfuel Cutting
- Plasma Cutting
- Power Tools
- Punching and Other Holemaking
- Roll Forming
- Safety
- Sawing
- Shearing
- Shop Management
- Testing and Measuring
- Tube and Pipe Fabrication
- Tube and Pipe Production
- Waterjet Cutting
Industry Directory
Webcasts
Podcasts
FAB 40
Advertise
Subscribe
Account Login
Search
How stamping manufacturers can navigate labor shortages and achieve quality goals
ERP software, workforce training, and automation are among the best practices for the metalworking industry
- By Anthony Murphy
- April 19, 2022
- Article
- Manufacturing Software
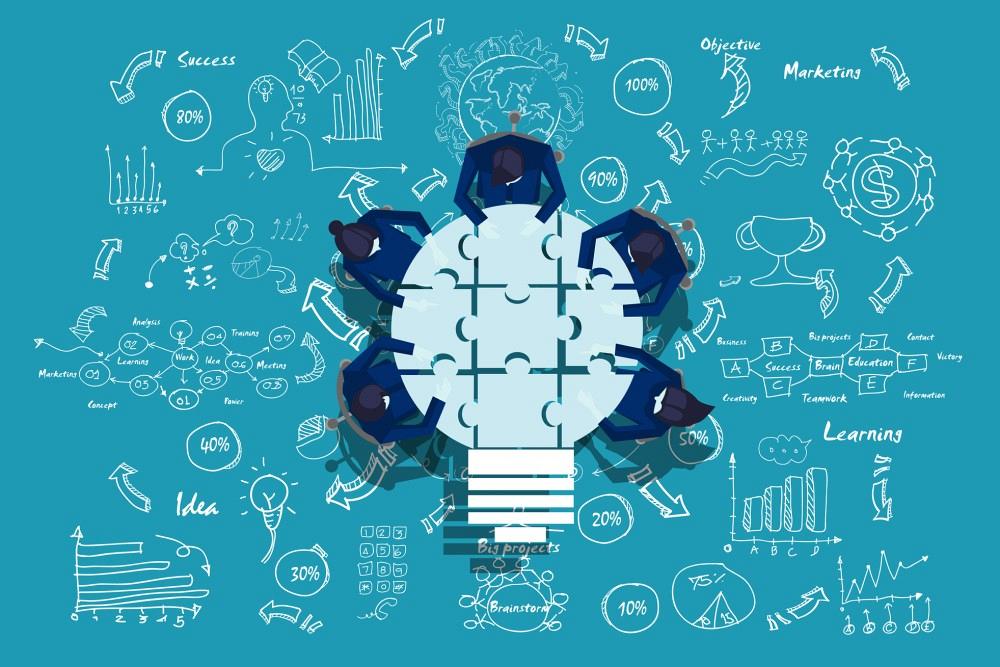
Quality is essential for any business to succeed. Here’s how top stamping manufacturers are navigating workforce issues while continuing to uphold quality standards using some industry-wide best practices. Getty Images
Quality is essential for any business to succeed. A manufacturing organization not prioritizing quality will encounter competitive and business challenges. Poor quality will cause customer complaints and a negative hit to brand reputation, margin loss, and business continuity risk. Though quality improvement strategies have been around for years, COVID-19 has accelerated change and exacerbated challenges.
What’s getting in the way of sustaining quality in stamping manufacturing? Hint: ongoing labor shortages. Follwoing are some current manufacturing workforce issues and how top stamping manufacturers are navigating them while continuing to uphold quality standards.
The State of Workforce Resources Today
As COVID continues impacting manufacturing, it becomes clear that the impact the pandemic has had on manufacturers will be long-lasting. The pandemic has accelerated major trends that stamping manufacturers have been grappling with for years: supply chain chaos, shifting demands for goods and services, constantly evolving regulatory requirements, and the skilled labor shortage. The latter has been grabbing hundreds of headlines in the news over the past several months.
It’s not news to U.S. manufacturers, though, that they have been hit hard by the lack of skilled labor and are currently facing a shortage of qualified workers. While the pandemic put the labor shortage into sharper focus, this problem predates COVID by years, with the “great retirement” of baby boomers driving an exodus of workers from the industry.
Unfortunately, American manufacturing companies have faced—and will continue to face—labor shortages for the foreseeable future.
With the potential for long-term disruption, what can manufacturers do to avoid the negative effect workforce issues could have on quality management?
Stabilizing Resources and Labor
Many factors are accelerating today’s labor shortage. For one, manufacturing jobs aren’t typically considered top career options for younger generations, and the aging workforce in these industries is retiring fast, shrinking the overall talent pool and widening the skills gap. According to a report from Deloitte and The Manufacturing Institute, if nothing is done about the manufacturing skills gap, it could cost the U.S. economy as much as $1 trillion. This is a serious problem that needs to be addressed, because to deliver consistent quality across any organization, there needs to be a measure of stability.
The transient and fluid nature of today’s workforce makes that increasingly difficult. For context, a transient and fluid workforce means that the days of a 20-plus-year tenured employee are largely behind us, and the team member producing the product today—or responding to the customer—may not be the same one tomorrow.
The industry is at a tipping point and must act now. Fortunately, many manufacturers are getting smart with their approaches. Given that the resource pool is smaller and more dynamic, leading manufacturers are instituting measures, processes, automation, and tools to drive consistency, even with the decline of the skilled workforce and the generational shift in workforce norms, behaviors, and expectations.
Let’s look at what the most successful manufacturers are doing to achieve success, and what lessons the stamping industry can learn from them.
How Top Manufacturers Are Leading the Way
While labor shortages are a pervasive problem, manufacturers have found and implemented new strategies to circumvent many of these issues. Here are some of those best practices:
1. Operationalize Training, Education. The first is operationalizing training and education.
Metal forming manufacturers should focus on onboarding, instituting, and measuring key performance indicators around speed-to-employee-productivity, training effectiveness, and employee retention. The objectives for standard and consistent training programs are simple. Consistent training and onboarding will help reduce the ‘time to productivity’ KPI, while increasing quality. Manufacturing leaders must provide new team members the same experience and training to support their effectiveness, regardless of background or skill set.
One way to ensure consistency among staff is by leveraging cloud ERP software services. Having information centralized on the cloud helps streamline processes across an entire organization. In a pandemic environment, stamping manufacturers are using the cloud to keep their businesses moving forward even when their teams are dispersed across multiple locations.
For example, Aero, Farmington, Conn., found that although many commercial aircraft makers stopped buying parts when most flights were grounded at the onset of COVID, the company ended up doing more business with military clients. When about 25% of staff began working from home in the first months of the lockdown, the staff could easily keep up with business by logging on from any web-enabled device.
Second, stampers must provide a better employee “day one” experience. Employees who receive adequate training, understand the company mission, and have a clear idea how their efforts support that mission are more connected and more likely to stay. Good training and initiation measures not only drive up productivity, they support retention. Who wouldn’t want to work for a company that invests in them and makes them feel connected to the good work they are doing? According to studies, effective onboarding and training can improve retention by 82% by helping new hires integrate into their roles and learn about manufacturing career paths.
2. Invest in Automation. A second strategy is investing in more automation, especially in processes. Stamping manufacturers have always looked to streamline processes and eliminate waste through automation, but leading manufacturers are adapting to the changes that COVID and other trends are presenting by leveraging automation in several key areas.
It may seem obvious, but stampers can alleviate labor shortages by automating routine tasks that don't necessarily need to be performed by people. When labor was readily available, manufacturers could assign people to a problem or routine task. Today, successful manufacturers are inspecting every facet of their operations—from data input and collection, to reporting and analytics—to drive speed, efficiency, and consistency and keep their teams focused on high-value, high-impact work.
Another example is G&W Products, Fairfield, Ohio, which performs metal fabrication, metal stamping, welding, and powder coating. Employees were spending too much time tracking down the right data and not enough time thinking strategically about how to use it.
After engaging ERP software, the business connected hundreds of devices in the cloud and gained access to the right data at will. As a result, G&W was able to save eight labor hours per week on report preparation, while also improving inventory accuracy from as low as 40% in some areas to 96%. All of this increased profitability.
3. Incorporate ERP Software.
Manufacturers can automate report generation for increased process visibility. While it was once someone’s job to collect and disseminate data, instructions, and charts, manufacturers are now relying on automated tools and systems. That not only supports consistency and frequency, but adoption by the broader group. With the ubiquity of an automatically generated dashboard, every employee can immediately see the progress and impact of their work and be connected to the broader mission.Finally, to be successful, manufacturers should review their operations and look to automate activities where they can no longer get skilled labor—whether it’s self-service tools, machine automation, process automation, or data automation. Leading stampers understand that labor shifts are here to stay and are adapting through automation so they can focus their high-value team members on high-impact work.
Hatch Stamping, Chelsea, Mich., was finding it difficult to achieve efficiency, accuracy, and continued growth with its manual processes and an antiquated ERP infrastructure. After automating its report generation, the stamper can now streamline data gathering and data management. This eliminated many inefficiencies. For example, the company previously had two to three full-time staff working only on report generation. Now, any user can create reports within minutes. This allows management to prevent unnecessary costs, redirect resources to other higher-value tasks, and proactively address production quality issues.
It All Comes Back to Quality
By automating many of the tasks that ensure real-time monitoring of quality measurements and control of processes, manufacturers can prevent quality problems from occurring. This will also enable the rapid deployment and correction of quality problems when they occur rather than after the fact.
For stamping manufacturers that are facing a long-standing labor dilemma exacerbated by a global pandemic, addressing the current workforce issues may feel like an uphill battle. Fortunately, many manufacturers successfully leading the charge have blazed a path for others to follow. The more you can get equipment and systems to perform and the more systems talk to each other, the less of an impact labor shortages will be felt across your organization.
About the Author
Anthony Murphy
900 Tower Drive, Ste. 1500
Troy, MI 48098
Related Companies
subscribe now
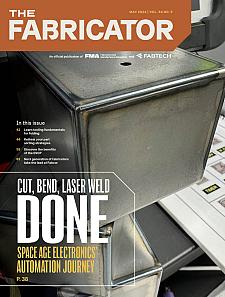
The Fabricator is North America's leading magazine for the metal forming and fabricating industry. The magazine delivers the news, technical articles, and case histories that enable fabricators to do their jobs more efficiently. The Fabricator has served the industry since 1970.
start your free subscription- Stay connected from anywhere
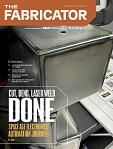
Easily access valuable industry resources now with full access to the digital edition of The Fabricator.
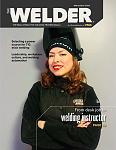
Easily access valuable industry resources now with full access to the digital edition of The Welder.
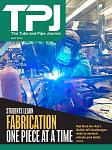
Easily access valuable industry resources now with full access to the digital edition of The Tube and Pipe Journal.
- Podcasting
- Podcast:
- The Fabricator Podcast
- Published:
- 04/16/2024
- Running Time:
- 63:29
In this episode of The Fabricator Podcast, Caleb Chamberlain, co-founder and CEO of OSH Cut, discusses his company’s...
- Trending Articles
Tips for creating sheet metal tubes with perforations
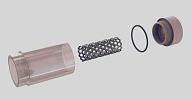
JM Steel triples capacity for solar energy projects at Pennsylvania facility
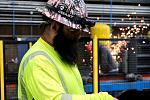
Are two heads better than one in fiber laser cutting?
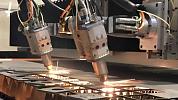
Supporting the metal fabricating industry through FMA
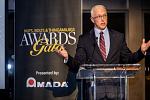
Omco Solar opens second Alabama manufacturing facility
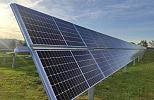
- Industry Events
16th Annual Safety Conference
- April 30 - May 1, 2024
- Elgin,
Pipe and Tube Conference
- May 21 - 22, 2024
- Omaha, NE
World-Class Roll Forming Workshop
- June 5 - 6, 2024
- Louisville, KY
Advanced Laser Application Workshop
- June 25 - 27, 2024
- Novi, MI